燒結煙氣污染物治理技術研究及應用現狀
燒結煙氣污染物治理技術現狀
Tips:隨著我國經濟發展對鋼鐵需求量的日益增加,鋼鐵工業已經成為國民經濟的重要支柱產業。據中鋼協統計,2014年我國粗鋼產量達8.2億t,同比增長0.9%,佔全球粗鋼產量的49.3%。隨著產量的不斷攀升,鋼鐵企業的大氣污染問題日益嚴重。鋼鐵行業排放的大氣污染物主要包括顆粒物、SO2、NOx、重金屬元素和二惡英等。據環保部統計分析,2014年鋼鐵行業的顆粒物、SO2和NOx排放量分別為101.5萬t,180.7萬t,6.6萬t,分別約佔工業源總排放量的10.4%、4%和7%。
燒結作為鋼鐵生產過程中污染最嚴重的工藝環節之一,其煙氣中的顆粒物、SO2、NOx和二惡英排放量分別約佔鋼鐵生產總排放量的20%、60%、50%和90%,燒結煙氣的治理已成為鋼鐵企業環保達標的重中之重。
燒結煙氣污染物治理技術
燒結過程的特點是煙氣量大,污染物種類多,且含量波動大,煙氣溫度低。目前燒結機頭煙氣污染物的治理措施主要分為3個方向:源頭減排、過程式控制制和末端治理。下面小編為您逐個進行分析:
源頭減排
源頭減排是通過對燒結原料成分的控制,來減少燒結後煙氣中污染物的含量。燒結煙氣中的SO2、NOx主要來自於燒結原料中的S、N;粉塵顆粒主要以鐵及其化合物顆粒為主,還有硅、鈣等鐵礦伴生成分以及不完全燃燒物質等;重金屬如鉛、砷、鎘、鉻、汞等,也主要來自於燒結礦。可以看出,燒結煙氣中的污染物基本均來自於燒結原料。同時,一些燒結工藝主要參數,如混合料的含水量、燃料配比、料層厚度、生石灰配比等,對煙氣中SO2、NOx排放也有重要影響。因此,源頭減排主要是在保證燒結礦性能不受影響的前提下,改變燒結原料的成分配比或添加不同的成分,調整優化燒結工藝參數,從源頭上減少煙氣中多種污染物的排放濃度,降低末端處理設備的凈化壓力。
過程式控制制
過程式控制制是在燒結生產過程中進行污染物減排,主要方法是採用煙氣循環技術。利用燒結過程的特點,使部分廢氣中的有害成分進入燒結層中被熱分解或轉化,消除部分二惡英和NOx,抑制NOx的生成;粉塵和SO2也會被燒結層捕獲,從而減少粉塵、SO2的排放量;煙氣中的CO可作為燃料使用,降低固體燃耗。因此該類技術在去除循環煙氣中的多種污染物,顯著減少煙氣和污染物的排放總量的同時,能夠回收循環煙氣中的餘熱,節省能量消耗。目前煙氣循環技術主要包括能量優化燒結技術(EOS)、環境型優化燒結(EPOSINT)、低排放能量優化燒結工藝(LEEP)、區域性廢氣循環技術,但由於設備改造複雜,國內成功實施的案例較少。
末端治理
末端治理則是採用專門的凈化設備來脫除燒結機頭煙氣中的各種污染物,如電除塵器、脫硫塔、布袋除塵器等,多為單一的污染物脫除設備。將各單元協同配套使用,是燒結煙氣處理最實用的手段。目前,各設備均有較好的工程效績,但在越來越嚴格的排放標準背景下,必須通過設備的改造調整,或者更換更高脫除效率的凈化設備來滿足排放要求。同時,凈化設備產生的廢棄物難以利用,不當處置也會造成後續的環境問題,引起二次污染。
01
顆粒物
脫硫設施對入口煙氣的粉塵濃度有較嚴格的要求,所以煙氣一次除塵至關重要。國內大部分燒結廠採用三電場、四電場的ESP,基本滿足脫硫入口煙氣粉塵含量40~80 mg/m3的要求。煙氣二次除塵技術則根據脫硫工藝的不同去選擇,干法、半干法脫硫採用布袋除塵,濕法脫硫採用除霧器或濕法電除塵器對煙粉塵進行控制。
雖然電除塵器和布袋除塵器可以達到較好的除塵效果,但難度在於去除煙氣中細顆粒物,研究發現燒結機頭電除塵器前後的煙氣中,PM2.5和PM10占煙粉塵總量的比重變化明顯,PM10由51.23%變為93.13%,PM2.5由 43.73%變為85%,說明經除塵後的煙粉塵主要為PM10,以及粒徑更小的PM2.5,因此對煙氣中細顆粒物的去除,是今後研究的主要方向。
02
二氧化硫
目前燒結煙氣脫硫技術以濕法和半干法技術為主,技術比較成熟,設備國產化程度高。據中國鋼鐵工業協會燒結機脫硫統計,截止至2012年,國內脫硫設備共287套,其中濕法209套,佔總數的72.82%,以石灰(石)-石膏法為主;半干法76套,佔總數的26.48%,主要為循環流化床法和旋轉噴霧法;干法2套,佔總數的0.7%,為活性炭/焦法。
濕法脫硫技術的優點是:吸收劑利用率較高,脫硫效率在95%以上,對煙氣適用範圍寬,副產物脫硫石膏成分相對穩定,二次污染小。其缺點是:工藝廢水中Cl_濃度高,對設備有一定腐蝕;石灰漿液噴嘴易發生堵塞情況;除霧器易結垢堵塞,影響尾氣處理,形成石膏雨,對周邊環境造成污染。
半干法脫硫技術應用較多的有旋轉噴霧半干法、循環流化床法、MEROS等。半干法脫硫技術脫硫效率一般為85%~95%,且具有同時脫除強酸、重金屬和二惡英的潛力,系統不存在腐蝕問題,適合處理煙氣溫度較高、SO2濃度較低的煙氣,基本無廢水排放,尾氣較輕,但副產物是以CaSO3為主的灰渣,易分解應用價值有限。
干法,即活性炭/焦法,主要應用於太鋼和寶鋼湛江鋼鐵。優點是吸附的SO2氣體可加工成硫酸,具有較高價值,且無二次污染。同時可實現脫硝、脫二惡英、吸附粉塵及重金屬等效果。但入塔煙氣SO2濃度不能超過2400 mg/m3,以避免因吸附熱過高而發生爆炸。解析後產生的酸為混合酸,要求設備防腐性能高,而且投資及運行費用高。
03
氮氧化物
NOx脫除工藝主要分為2種,第一種是在脫硫工藝後設置單獨的脫硝設備,一般為中溫SCR工藝或低溫SCR工藝。中溫SCR工藝是通過換熱和燃燒器將煙溫加熱到300℃以上,將氨或尿素等噴入煙氣中與NOx反應,生成N2後再進行排放,脫硝效率可達80%,但在進入脫硝設施前,燒結煙氣溫度僅有80~180℃,加熱耗能巨大,且SCR技術本身投資大,因此經濟適用性較差。目前,應用SCR技術的燒結廠有日本Kawasaki鋼鐵公司Chiba廠,Kokan公司的Keihin廠,台灣中鋼3、4號燒結機。
低溫SCR工藝的溫度窗口在120~300℃,無需加熱煙氣,可節約大量能源,一般布置在除塵和脫硫設備之後,以減輕鹼金屬元素和SO2對催化劑的影響,但在低溫下,SO2與H2O、NH3易形成黏稠的銨鹽,附著在催化劑表面,使催化劑中毒失活,因此,需對入口煙氣的粉塵和SO2濃度進行嚴格控制。目前,低溫SCR催化劑分為釩鈦體系和非釩系(錳基係為主)兩種,國內燒結機應用工程案例較少。
第2種是在脫硫工藝中聯合脫除NOx。在活性炭/活性焦法中,由於活性炭/焦炭的催化作用,NOx與注入其中的液態氨發生反應,分解成氮和水分,NOx脫除效率可達50%。
中冶節能環保有限責任公司開發的低溫煙氣循環流化床同時脫硫脫硝除塵技術,在傳統的循環流化床半干法脫硫工藝基礎上,利用低溫選擇性催化氧化原理,通過使用催化劑以及合理控制工藝步驟和運行參數,先將NO催化氧化為NO2後,再與SO2一起被吸收劑Ca(OH)2或CaO吸收,實現同時脫硫脫硝的目標,同採用傳統半干法煙氣脫硫技術相比,其脫硫效果明顯提高,在實現高效脫硫的同時,也可以脫除煙氣中的NO,脫硝效率超過80%,使得在常規的煙氣二氧化硫濃度和氮氧化物濃度範圍內,硫氧化物和氮氧化物排放滿足國家環保要求,大大節省了設備投資,降低了煙氣污染物排放的控制成本。
04
二惡英
目前燒結煙氣中二惡英控制主要方法為活性炭法,活性炭對二惡英有強吸附作用,被吸附的二惡英,在脫吸塔中無氧、400℃的條件下,分解為CO2、H2O、HCl。太鋼的活性炭工藝可以達到PCDD/Fs濃度0.15 ng-TEQ/m3的煙氣排放能力。
其他工藝是在布袋除塵器前加噴碳裝置,活性炭在煙道里吸附二惡英,並在布袋除塵器被攔截脫除,吸附了二惡英的活性炭可添加到燒結料中,該工藝國內報道較少,脫除效果有待研究。
作者結語
燒結機頭煙氣的煙粉塵控制在現有的工藝條件下可以滿足新排放標準,並有一定提升空間。SO2的控制工藝較成熟,從目前的運行狀況來看,以石灰(石)-石膏法為代表的濕法具有更高的脫硫效率,脫硫副產物也可以進行綜合利用,具有一定的經濟效益。對於NOx的脫除工藝,低溫SCR和低溫選擇性催化氧化是未來主要的發展方向。低溫SCR工藝的研究難點在於催化劑要滿足更低的溫度要求,適應更複雜煙氣工況條件下的煙氣特性,但由於該工藝將有價值的氨氣作為反應原料,並轉化為無用的氮氣排出,導致運行費用昂貴。低溫選擇性催化氧化工藝投資成本低,運行費用少,並生成有經濟效益的副產品,具有能夠同時脫硫脫氮,減少凈化流程,將是最具價值的煙氣NOx凈化技術。二惡英的脫除尚無成熟工藝,源頭抑制技術有待進一步研究。
隨著越來越嚴格的排放標準的實施,選擇技術可行、經濟合理、符合清潔生產和節能減排要求的燒結煙氣多污染協同控制技術是未來的發展方向。為實現對多種污染物的排放控制,可以採用具有多污染物脫除效果的單項技術等。如活性炭/焦法、低溫煙氣循環流化床同時脫硫脫硝除塵技術,一體化設備能夠有效降低環境污染的治理成本;還可採用多項技術組合,如濕法脫硫+低溫SCR,但需要注意各工藝間的協同和優化,建造費用及佔地情況。
視頻資料:中冶環保循環流化床脫硫脫硝技術攻克低溫脫硝難題
1.【乾貨】DCS控制系統:低溫煙氣脫硫脫硝技術的指揮中樞
2.南屯電力低溫煙氣脫硫脫硝一體化裝置 圓滿通過168小時滿負荷運行性能考核
3.了解更多中冶節能環保

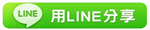
TAG:環境工程 |