殲15成功著艦五年了!它背後有哪些你不知道的黑科技?
原標題:殲15成功著艦五年了!它背後有哪些你不知道的黑科技?
來源:軍武硬漢
部分素材來自央視網、解放軍畫報、央廣軍事,航空工業整理
全文共3462字,閱讀需要6分鐘
2012年11月23日,殲15艦載機在航母遼寧艦上成功降落。作為中國航空工業發展中一款具有里程碑式意義的飛機,當殲15艦載機在航母遼寧艦上成功降落時,引來世界普遍關注的目光。
殲15艦載機,是航空工業沈飛研製的我國首款艦載機。長22.28米、翼展15米、高5.92米;有12個武器外掛點,可掛載空空導彈、反艦導彈、火箭彈、航空炸彈等多種武器;配裝2台大推力發動機,最大起飛重量32.5噸,最大飛行速度2.4馬赫,實用升限20000米,航程3500公里。
2012年11月23日,殲15艦載機在我國第一艘航空母艦遼寧艦上首批完美著艦,成功實現雙劍合璧,中國航空工業由此實現從陸地到海洋的跨越。在國外看來,至少要花上一兩年時間,才可能攻克的艦載機起降問題,卻讓中國航空工業的英雄團隊,僅在遼寧艦服役兩個月就做到了。
全數字化操作系統
孫聰,56歲,先後擔任殲15等多種型號戰鬥機的總設計師。說起殲15飛機研製過程中的自主創新,孫聰仍然覺得這是一個很大的挑戰和課題。
孫聰:實際上我們是朦朦朧朧地懂艦載機,但是並不完全懂艦載機,在這樣一個前提下,對整個設計生產、設計製造這兩大領域來說,都是具有挑戰性的。
艦載機與陸地上戰鬥機最大的不同,就是艦載機在航母狹小的跑道上起飛、降落,而一般航母甲板上的飛機跑道長度只有100多米,大約只相當於陸地跑道的十分之一。如何讓飛機在這麼短的距離里平穩起飛,一直是困擾他們的一道難題。
十幾年前,接到設計生產航母艦載飛機的任務時,孫聰和他的同事們就清楚地知道艦載機研製是一場必須打贏的硬仗。而這場沒有硝煙的戰鬥剛一打響,就面臨設計手段、設計方法的重大改變。他們決定要在殲15上嘗試全新的數字化設計方法。
既然是全數字化操作系統的高科技產品,無論什麼樣的條件下都必須保持網路暢通,成了艦載機首先必須攻克的技術難題。因此,研製中,設計師們圍繞航母周圍的複雜電磁環境,開始各種設計和試驗。
孫聰:電磁環境是非常惡劣的,跟陸上飛機相比,不是一倍兩倍的關係,是很多倍。那就要考慮三方設計,我們在整個的試驗鑒定過程中,是嚴格按照鑒定程序,有全機的、體系內的,做電磁防護的設計,進行試驗驗證,最後才拿得出去的。
取保艦載機通信暢通僅僅是設計的第一步,在航母上比起飛還要難的實際是降落,攔阻鉤、攔阻索系統直接決定艦載機著艦的成功與失敗。然而,攔阻系統是中國飛機製造的一大空白,更是航空工業沈飛公司面臨的一道全新課題。
設計方案反反覆復,大大小小的試驗做了上萬次,中國自主研製的國產攔阻鉤、攔住索系統終於成功研製,但設計師們還沒有來得及品嘗成功的喜悅,新的難題又迎面而來。
大型金屬3D列印技術
早在上個世紀五六十年代,飛機機體結構的骨架構型已經固定下來。在傳統結構形式上,通過優化設計,已經把飛機的潛力挖到極限了。在傳統結構形式下,飛機機體重量已經減到最輕,如何能夠繼續減輕飛機體重,同時又提高它的性能、品質,這是沈飛公司遇到的又一個門檻。設計師們明白要想邁過這個門檻,就得尋找一個新技術,對飛機機體平台進行突破性改造。
吳斌,一個從業18年的資深設計師坦言:我們是做航空的,軍機結構的。接觸3D列印,我們走過比較坎坷的路。
在北京一座普通的居民樓里,林宗棠老人正在家裡搭建著心中的3D列印王國。
林宗棠:全國哪裡有3D,我就到哪裡去。我估計全國我跑了可能有五六十家企業和研究所。我拜了十幾個老師,拜他們為師,我不懂這3D,向他們學習。
航空人年齡不分長幼,只看誰能走在技術尖端。耄耋之年的林宗棠,2年前將3D列印列為自己的新課程。雖然中國的3D列印技術,已經幫殲15、「鶻鷹」等飛機研發大大提速,但航空強國的高歌猛進,還是讓林宗棠有些不安。
老人關心的是金屬3D列印,在航空領域,這是個前沿課題。就在5年前,一台擁有全球最高製造水平的金屬3D印表機,已經安裝在這座廠房裡。
這台外表並不光鮮的設備能夠製造出全球尺寸最大的鈦合金結構零件。而能否製造大型金屬結構件,是衡量一個國家3D列印技術先進程度的重要標準。
電子束沉積快速成型技術
十年前,鞏水利他們開始攻堅電子束沉積快速成型技術。它是用高密度的電子束作為熱源,在真空室內熔化送進來的絲材,再按照預定加工路徑,逐層堆積成型。
美國是最早擁有這項製造技術的國家,但研發成功後便實施技術封鎖,直到今天是否已經投入大規模應用,依然秘而不宣。
鞏水利:我們現在在研的設備,都是在世界上體積最大、成型能力最大、最優的一些設備。在這個基礎上,又研發我們的產品,突破了材料和關鍵的工藝。
曾經,他們的願望是讓中國成為第二個掌握這項技術的國家。現在,他們已經成功了,而且依然沒有停下腳步。
像這樣大的一個構件,如果用傳統的模具製造,工期至少半年以上,而用這台設備列印只需要20天。
不僅是航空領域,工業製造研發,從設計到驗證,如果有了這樣的速度,就可以加速迭代。正因為如此,3D金屬列印,一直是大國之間暗自較勁並發力的領域。
3D列印技術是一個國家從製造大國向製造強國轉變的重要技術路徑和手段,它衡量著一個國家製造技術的水平。
鞏水利和他的技術團隊,仍然在和時間賽跑。
抗疲勞製造技術
為了擁有智能製造的未來,78歲的老院士趙振業正帶著團隊完成一個從300小時到4000小時的跨越。
他們正在努力提高飛機發動機主軸承的使用壽命。軸承上任何一個小的損傷,都可能帶來致命的災難。歷史上的諸多空難,都是因為關鍵構件使用到一定年限後,發生疲勞失效引起的。
趙振業他們提出一種新的「抗疲勞製造」理念。抗疲勞製造技術,這個團隊已經研發了整整20年,現在已經能將一些關鍵構件的使用壽命提高十幾倍甚至幾十倍。
減重是飛機對機體結構要求最直接最重要的一個指標。3D金屬列印的成功開發成為殲15艦載機減輕機體重量的重大突破口,有的機型上,已經達到減重26.8%,在「一克重量一克金」的飛機製造領域,有著非同尋常的意義。
另外,3D列印的最大優勢,是能設計創造出一些全新的結構構型和多材料組合複合材料。也就是不同材料根據需求,可自由組合搭配、合理使用,在提高質量、強度的同時,還能減輕重量,減少隱患。
3D列印,創新性地突破傳統製造、加工的一些難點,最大限度地減輕了飛機的重量,大大提高了飛機的載荷功能,也加快了研發團隊的攻關進程。
智能螺栓
在攻克3D高科技列印難關後,航空工業瀋陽所還研發出一項具有世界先進水平的高科技產品——智能螺栓。一個螺栓怎麼能稱得上智能呢?秘密就在於其中增加的感測器功能,能主動感知載荷多少。
飛機機體的拼接部位需要很多螺栓連接,尤其是機體、機翼等部位的連接螺栓非常重要,一旦螺栓不能承受實際載荷,或者到了金屬疲勞期,螺栓會出現問題甚至折斷,危及整個飛機的安全。智能螺栓就是為解決這個問題研究發明的,能起到維護飛機安全、減輕機體重量的作用。
如何計算螺栓的載荷承受力是此前存在的技術難點,計算不準確,螺栓連接部位重量偏大,給飛機帶來額外的重量損失。實現準確計算後,因為螺栓的連接部位非常之多,節省的重量非常可觀。
傳統測量螺栓承受力的方法,通常有兩種:一是靠手工扳手,間接測量螺栓擰緊的扭力,不能測量螺栓能承受多少重量的剪切力,數據不精準。
另一種是在螺栓外部安裝超聲感測器測量。但受環境、條件等因素的限制,傳統測量螺栓內部受力的方法很難獲得精準數據,工程人員無法準確判斷螺栓的安全性。那麼,怎麼突破、創新呢?
王健志和技術人員在螺栓內部,安裝一個感測器,就是在螺栓中間打一個小孔,然後把很細小的光纖、光柵感測器給放進去,這樣的話就變成了一個具有感測器功能的智能螺栓。
雖然有了一個好的創意,但要實現這個創意,必須攻克一大難題,那就是對螺帽和螺桿內部打孔鑽洞的精加工。
比如說在鑽孔的時候,很容易深度不夠,再加上飛機上的一些螺栓都是高強度的材料,所以加工非常困難,後來採取了一些新型的加工技術,慢慢把這個技術問題解決了。
現在,智能螺栓已經得到廣泛的運用,不僅包括殲15、「鶻鷹」等各類軍工產品,也運用到民用產品上,比如大橋橋樑、交通軌道、高壓電塔、建築房屋等結構部件的連接螺栓。
智能螺栓的應用市場非常廣闊,據前期調研,在國內的電力、船舶、建築等行業的市場需求量達到25億,而且五年內增長率能達到25%,跟智能螺栓相關的結構健康監測,光纖感測技術應用,這方面市場佔有率能夠達到50%以上。
從一張白紙的設計、一個零件的生產,到攻破重重難關,中國航空工業實現了艦載機的零突破。

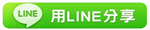
※為什麼中國用220伏電,美國用110伏電?
※俄羅斯人用戰鬥機引擎組裝的吹雪神器:沒想到中國的更厲害!
※如何辨別殲系列國產戰機,看完你就全明白了
※世界上最快的火箭橇,時速10430公里,是音速8.5倍!
※波音737飛機駕駛艙面板全解讀,震撼來襲!
TAG:航空製造網 |