系統思考 指標拉動 深入推進位造業務新模式轉型
原標題:系統思考 指標拉動 深入推進位造業務新模式轉型
航空工業南京機電製造業務指標體系自2016年底開始逐步建立,2017年各分廠圍繞指標體系,從SQCDPT幾個維度採集基線、分析差距、尋找機遇、持續改善。通過大半年的運行,核心指標已逐步融入各單位的日常工作中,製造系統已然形成了指標拉動、持續改善的良好氛圍。
挑戰與機遇
進入「十三五」以來,國家已明確提出「實施軍民融合發展,形成全要素、多領域、高效益的軍民融合的發展格局」。隨著軍民融合的不斷深入,南京機電人敏銳地察覺到形勢的變化,在做實系統部、打造精益製造體系上率先邁出了堅實的一步。研究部從過去僅僅關注產品的功能實現,逐步向關注市場、研發、服務等全生命周期的轉變,並且向關注設計的可靠性、工藝的可達性以及成本節約性轉變。這樣的轉變,也為製造系統向精益化轉型提供了有利條件。
為適應新的形勢,製造系統的轉型已成為必然。作為未來的「成本中心」,製造系統要緊緊圍繞「提升產能、降低成本」這一核心目標,以「兩個轉變」為著力點,不斷推進新形勢下的製造業務轉型。第一,要由原來只關注交付進度和節點,向同步關注品質與成本轉變;第二,要由過去只關注內部工藝能力的提升,向同時關注外部供應鏈的協同發展轉變。通過「兩個轉變」,充分發揮集成供應鏈的優勢,實現「多快好省」地為各系統部提供零件,更好地為系統部的快速發展提供有效支撐。
承接戰略 模式轉型
「十二五」期間,南京機電圍繞生產運行持續變革,生產運行的精益化、系統化進程更加穩健、更加立體。同時,為適應航空製造業轉型升級,提高滿足客戶需求的應對能力,製造業務聚焦自身發展戰略,通過對標國外企業先進位造模式,推進基於集成供應鏈的製造業務轉型,不斷提升企業的核心競爭能力。
國家供給側改革,提出「降產能、降庫存、降成本、補短板」,提高企業的運行效率的要求,南京機電製造業務如何能夠對標國際標杆,滿足國企改革要求,「提質增效」,實現企業「健體」?這就需要製造系統通過精益化,不斷提高自身運營效率。「降產能」——就是生產能力不能片面追求規模無限增加,在現有內部資源相對保持不變的前提下,充分利用各類製造資源,通過集成供應鏈來解決通用能力的不足;「補短板」——就是不斷在核心專業領域,做精、做細技術,通過工藝攻關以及與設計部門的溝通交流,把核心工藝水平不斷提高,將工藝技術能力存在的短板補充,謀求長遠發展。
基於這樣的考慮,製造系統作為南京機電價值鏈的重要環節,除了在技術方面不斷加強,運營管理體系的搭建、製造業務的整合升級也迫在眉睫。南京機電要保持核心競爭力,就要在管理上不斷去探索、完善,圍繞「開源」「節流」雙管齊下。製造系統轉型為專業系統部的快速發展提供有效支撐,為職能機關的有效履職提供支持,助推南京機電的戰略實現。在南京機電的科研生產經營活動中,各專業系統部負責「開源」,製造系統負責「節流」,也就是要「多快好省」產出零件,滿足客戶的訂單需求,逐步構建「集團抓總、系統牽頭、體系保障」的運營模式。而製造系統要實現「節流」,就要「輕」投入,重協作,有效控制人員職數和設備投入;同時要保證產出,要深度挖掘設備有效產能,利用「大數據」,提升生產效率,要特別重視生產現場精益生產的深入推進,保證良好的生產環境,向世界一流製造企業看齊。
南京機電只有以核心價值鏈為主線,從製造業務出發,整合內外部製造資源,逐步建立統一計劃,統一調配製造資源,高效、敏捷處理問題的運行機制,打造基於集成供應鏈的精益製造平台,才能為南京機電又好又快發展持續提供動力。
2014年,隨著集團AOS0300生產製造模塊的導入、應用以及AOS工廠實體運行過程中的不斷探索,南京機電製造業務經過現場實踐、系統設計、頂層規劃,探索基於集成供應鏈下的航空零部件製造工廠轉型實踐,進行生產製造模式的精益轉型,搭建「多單元+四中心」的生產製造業務模式,將內部製造分廠打造成供應鏈上的零部件製造中心,為研發部門提供產品和零件。
組織創新 關注QCD
為進一步適應航空製造業轉型升級、技術進步和外部競爭的需要,南京機電積極探索製造管理模式向「生產服務型」的轉變,成立「大製造部」,通過製造系統的優化整合,打造「統一計劃、集成資源、質優敏動」的精益製造平台,多快好省地實現從訂單、計劃、製造、庫存、配送、質量、成本、保障等多維度的無縫銜接。
做實製造部是為了更好地滿足南京機電、各分部的需求,敏捷高效地實現客戶價值。將「大製造部」作為一個模擬公司來運行,將之前只重點關注生產交付(D),逐步轉變為持續系統提升生產製造SQCDP全維度指標。在這些指標中,追求QCD(Quality質量、Cost成本、Delivery交付)的不斷改善,是實現製造部卓越運行的關鍵。
Q質量——質量是企業的立足之本。以客戶為中心,客戶需求的是品質,因此在做實製造部後,要把質量提升作為首要工作,要強化流程,將「質量」要求固化到各個日常運行的業務流程中去,圍繞統一的質量目標,採用大數據分析、PDCA、分層診斷等工具,致力於生產出可充分滿足客戶需求的產品。
C成本——在過去的製造業務模式中,常常忽略了成本這一要素,導致目前存在很多問題:在制品數量龐大、工裝刀具大批申請、冷卻液更換隨意,等等,給企業造成了大量浪費。製造系統目前已經開始採集相關指標數據,在後續的推進過程中,成本指標將更加具體、有針對性,通過管理的精細化,不斷降低製造業務運行成本。
D交付——圍繞著交付這一指標,「十二五」以來製造系統做了很多工作,但還有大量的工作需要去策劃、實施。製造體系的搭建、製造部的做實、質量的提升、流程的固化等都是對最終交付指標起推進作用的手段。計劃體系的梳理優化、現場問題的快速反應、生產保障體系的建立、製造信息化的深入應用等,都是需要考慮的關鍵問題。製造業務只要通過系統性的「制訂措施」,不斷追求整體運行效率,交付指標一定會邁入一個更新的高度。
建立體系 運用工具
QCD是製造業務提升的一個很好的切入點,但對於整個製造體系,如何更好地發現問題,不斷提升各項運營指標?為拉動整體績效指標的提升,實現卓越運營,滿足客戶期望,南京機電梳理建立更全面、邏輯層次更清晰的製造業務三級指標體系:
1.從供應鏈的角度,基於戰略選擇,確定分廠層面指標。分廠層面指標強調分廠在安全、質量、交付、成本和人員(SQCDP)方面的綜合表現,區別於以往分廠只關注產品交付和質量指標要求,指標較之以前更細、更量化和動態,並全部在分廠可視化管理板上體現。
2.按業務向下分解分廠指標,設立主管(SQCDP)功能指標。按照業務職能向下分解分廠層面指標,設立各業務主管指標。業務主管對各自承擔的業務指標負有統計數據、分析、改善的職責。
3.指標落地,設立班組/精益單元指標。班組/單元層級指標重在落地,對業務主管、分廠指標進行承接和支撐。
設立的三級指標體系,指標之間相互分解和承接,確保客戶和分廠關注能全面落實在各個實體的日常管理中。各級指標體系,對生產現場狀態進行可視化的測量、監控,進而建立的一套反饋、預警、響應系統,及時發現問題並響應,驅動持續改進。
通過這樣的流程,生產現場過程監控從之前的「事後把關」為主,慢慢轉變為「事前預防」和「事中控制」為主。同時通過SQCDP看板,結合分層例會制度、管理者標準作業等工具,對現場生產績效的關鍵指標及其影響要素進行動態反應、動態控制、過程記錄及管理改進。
凸顯問題 把握機遇
在AOS指標運行體系的基礎上,2016年底南京機電製造業務就著手開始準備、收集、分析102廠房各個分廠在SQCDP等各維度的指標基線,收集、整理出各類指標共569個,各層級人員關心的問題共1203個。通過2017年半年多的運行、總結、迭代,目前已形成相對固定的製造業務核心運行指標共32項。這32項指標的監控,目的是挖掘出真實數據以服務於製造,把各分廠在質量、成本、交付等方面存在的問題充分暴露出來,通過對這些問題的監控,各單位能在第一時間利用PDCA等多種管理工具去發現問題、解決問題。在解決問題的過程中,要提出解決方案、追根溯源並實施改善措施;把生產成本控制意識、質量控制意識傳遞給員工,使每位員工都感受到切實的壓力,讓員工共同參與進降本增效的實際行動中。
這種指標的牽引,更重要的是要求南京機電各個層面都要形成精益生產意識,實行精益管理,把製造業務指標常態化,成本做小,與過去傳統經營方式逐步分離,真正做實「製造系統」。所有員工都有責任與義務轉變思想,本著「持家人」的心態,立足「製造系統」,各個單位都要有基於自身側重的行動項,從計劃、管理、運行等全方位進行改善,把改善思想落實到崗位,形成合力以達到降本增效、開源創效的目標。
「精益無處不在,改善時時皆有」,伴隨著管理模式優化的指標提升,必將塑造出南京機電企業良好的品牌形象,提高企業的核心競爭力,為南京機電戰略目標的實現打下堅實的基礎。

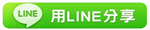
※美空軍「雷鳥」飛行表演隊高空加油,精彩飛行表演的保障
※日本研發可水洗超薄太陽能電池
※首台國產電力驅動盾構機下線
TAG:看航空 |