化學清洗技術在300萬噸/年渣油加氫脫硫裝置上的應用!
本期內容由湖南天一奧星泵業有限公司冠名
摘要:本文主要對300 萬噸/年渣油加氫脫硫裝置2014 年停工檢修使用化學清洗技術的情況進行介紹。選用某公司水基油垢清洗劑,對原料、分餾部分依次進行水置換、水循環、升溫、加藥劑循環、清水沖洗等處理,有效地清除了系統中的油垢、無機鹽垢、銹垢及焦泥等污垢,死角清洗到位,管線清洗乾淨,消除了清洗系統內部的可燃氣體、H2S、CO,為檢修施工提供了安全的作業環境,加快了檢修進度,達到了預期目的,同時該技術還具備環保、節能、高效的特點。
關鍵詞:渣油加氫 化學清洗 停工檢修
1、概述
300 萬噸/年渣油加氫脫硫裝置至2014 年4 月已運行到第四周期末期,設備內積存了大量的油污、硫化亞鐵和硫化氫等有害物。這些物質會使冷換設備傳熱效果變差,尤其是大型裝置管線較粗,系統流程複雜,採用傳統的停工吹掃模式時蒸汽的用量很大,且難以將裝置徹底的吹掃乾淨,達到預計的目標。加之裝置員工的精簡,裝置停工時現場操作人員的缺乏尤為突出。為了在裝置停工時節約蒸汽耗量,平衡全廠蒸汽用量,確保停工質量,最終採用某公司的水基全清洗技術。
該技術推出的水基油垢清洗劑清洗技術,清洗後的清洗液退回至污油儲罐分離切水,剩餘污油進行回煉,不產生浪費,從根本上解決了油垢的清除問題;同時避免了大幅度的憋壓吹掃,降低了裝置操作人員的勞動強度,縮短了停工檢修時間,同時減少了停工時蒸塔等操作大量有毒有害氣體就地排放帶來的安全隱患及對環境的污染,實現裝置的高效、環保、安全停工。
2、清洗劑機理及性質
本次化學清洗是通過有機溶劑溶解、絡合、轉化及其他作用使油垢從設備表面脫離的技術。利用現有流程和臨時管線,將需清洗設備連接,建立循環流程,並在100±5℃循環20 小時,達到清洗目的。
3、清洗方案及執行
主要停工步驟包括:(1)以<14℃/15 分鐘降低反應器入口溫度,按降溫要求和降壓要求將CAT 降至約350℃,系統壓力降至8.0MPa,反應器進料量降至149t/h.列;(2)引VGO置換渣油並保持VGO 進料6 個小時,建立兩系列運載油長循環;(3)按照運載油目標運動粘度50℃時15cSt 計算柴油量引入柴油;(4)粘度調整合適,改閉路循環後注入成膜劑;(5)循環成膜12 小時以上,爐出口溫度140℃以下,進料量149t/h,催化劑成膜結束,停止反應進料,反應部分退油至分餾部分;(6)高壓系統,循環氫循環冷卻催化劑至50℃以下,停循環氫壓縮機後,高壓系統氮氣置換至合格;(7)反應系統停進料後,在循環氫壓縮機循環帶油的過程中,原料部分引柴油置換進料和分餾部分,濾後罐改至分餾塔底泵入口,打通原料和分餾部分流程,拆熱低分和汽提塔充氮盲板,用氮氣控制好熱低分、汽提塔頂壓力,將蠟油和柴油退至分餾塔:(8)上游裝置、罐區將原料線均掃至二系列濾前原料罐,啟動原料油增壓泵將原料系統中的油全部趕至濾後原料罐,壓至分餾塔;分離部分的油按照從前至後的順序全部趕至汽提塔,進入分餾塔;啟動分餾塔底泵將污油全部外送;(9)低壓部分進行化學清洗;(10)硫化亞鐵鈍化。
本次停檢確定使用化學清洗技術首先是受全廠停檢、吹掃蒸汽難以平衡的影響,故化學清洗替代傳統蒸汽吹掃,確定實施化學清洗的部分主要包括兩系列原料系統至濾後原料緩衝罐、低壓分離系統至硫化氫汽提塔、硫化氫汽提塔頂迴流系統、硫化氫汽提塔底至分餾塔、分餾塔底系統、分餾塔頂迴流系統、分餾塔柴油側線抽出和中段迴流系統等。
化學清洗主要過程包括,二系列濾前原料緩衝罐用作一、三蒸餾、罐區掃原料線使用,液位高後開啟二系列原料油增壓泵,通過泵出口污油線直接送至污油系統。一系列濾前原料緩衝罐用作水沖洗及化學清洗使用,通過臨時線引入除氧水,開啟原料油增壓泵備泵將除氧水送入兩系列沖洗原料系統。原料系統沖洗乾淨後,在兩系列濾後原料緩衝罐處將污水壓至分餾塔底泵入口即分餾塔,啟動分餾塔底泵將污水外送。汽提塔頂迴流罐、分餾塔頂迴流罐分別引入除鹽水,沖洗汽提塔頂迴流及石腦油外送系統和分餾塔頂迴流及石腦油外送系統。裝水至分餾塔,19 層塔盤積水後啟動中段迴流泵沖洗中段迴流系統並經開工空冷外送,柴油塔積攢液位後啟動柴油外送泵沖洗柴油系統。啟動分餾塔底泵沖洗加氫常渣流程至空冷外送。熱低壓分離器使用反應部分余壓掃至汽提塔,冷低分流程換熱器全部低點將油排至地下污油罐。
水頂油過程中,主要注意確保裝置進水水質中氯離子含量不高於25μg/g,各個塔、容器要保持低液位操作,防止大量油水在塔內返混延長置換時間和效果,所有換熱器、控制閥、機泵的付線全都要稍開過水,備用泵的預熱線也要打開過水,防止留下死角。當加氫常渣出裝置處觀察大量見水後,開始採樣分析;採樣點為各個循環流程的末端低點排凝,分析方法用100mL 量筒採集100mL 油水混合液,滴入破乳劑靜置分層,以所採集的樣品含油量不超過5%為合格。
水沖洗結束後,建立下圖中各循環,通過分餾塔進料加熱爐加熱,在一系列濾前原料緩衝罐底加入清洗藥劑,汽提塔頂迴流罐、分餾塔頂迴流罐補除鹽水,形成化學清洗系統。開工空冷長循環:濾前原料緩衝罐至濾後原料緩衝罐至分餾塔底泵至開工空冷至濾前原料緩衝罐。長循環:濾前原料緩衝罐至濾後原料緩衝罐至分餾塔底泵至加氫常渣空冷至濾前原料緩衝罐。短循環:分餾塔底泵至產品渣油蒸汽發生器至冷低壓分離器至分餾塔。
分餾塔底泵出口送至分餾塔頂迴流罐,建立塔內液相迴流,形成中段迴流循環。柴油汽提塔內保存液位,最後以外送藥劑的形式清掃存油。分餾塔底泵出口送至汽提塔頂迴流罐,建立汽提塔液相迴流清洗塔盤。
用分餾爐逐步升溫,當系統循環溫度高於60℃時(即各循環流程出裝置處的溫度),開始加入清洗溶劑,控制分餾爐出口溫度到(100±5)℃,並維持穩定。加入水基油垢清洗劑,同時在分餾塔頂迴流罐、汽提塔頂迴流罐處增加備用加劑點。循環至8 小時後,分析循環液內的油含量,如果超過5%,進新水重新置換系統至油含量低於5%(按照水頂油步驟進行),然後繼續清洗循環,每兩小時採樣分析一次,直至循環液內的油含量不再變化,即作為循環的終點,監控數據如圖3。
化學清洗污水全部通過分餾塔底泵外送後,再次從濾前原料緩衝罐、汽提塔頂迴流罐、分餾塔頂迴流罐引水,進行水沖洗,將化學清洗乳化污水全部沖洗乾淨。循環結束後,用不低於70℃的清水沖洗整個系統流程,將系統內的乳化液快速排出系統,送至儲罐,待各個系統排出裝置處的COD 低於500ppm 時將各塔、罐液位送空,管線內存水排入含油污水系統。
4、總結與分析
4.1 本次停工化學清洗仍需改進的方面
(1)化學清洗水在塔、罐送空後即停泵,管線及換熱器內仍存有一定量的水,需及時排放,防止靜置時間過長,乳化液中油、水重新分層,達不到好的清洗效果。本次停工排水過程中發現原料及加氫常渣流程等重油管線導淋堵塞較多,疏通費時費力,故排水效率較低。應該在建立水循環過程中即確定各排水低點並進行試排及疏通。
(2)化學清洗過程中裝置內各油泵打水,易超電流。為防止泵超電流關小流控閥控制流量,則泵出口至控制閥前流程上的換熱器超過正常操作壓力,且流量較小影響清洗效果。
4.2 化學清洗的技術優勢
(1)清洗效果良好。經化學清洗後,各容器、換熱器、管道內基本不存油,可以達到甚至超過蒸汽吹掃的效果,為檢修過程的安全、綠色提供了有效保證,圖4 為清洗後的換熱器。
(2)節能效果顯著。300 萬噸/年渣油加氫裝置為重油裝置,按已有經驗停工吹掃需低壓蒸汽50t/h 左右。在全廠大停檢的背景下,蒸汽平衡困難,如採用蒸汽吹掃方式,不但能耗較大,而且各裝置使用蒸汽時相互制約,必定影響停工進度。
(3)節省大量人力。化學清洗過程與裝置正常運行類似,主要是利用裝置內各塔、罐壓力等級和泵進行循環清洗,而不需要像蒸汽吹掃時反覆憋壓,大大減輕員工勞動強度。
綜上,化學清洗技術在重油裝置停工處理過程中的應用具有很好的前景,不但安全、環保的達到檢修條件,還具有節能降耗、節省人力的優點;同時對新技術的應用也應結合現場實際,制定詳細方案,充分考慮運行介質對流量、壓力的影響。
參考文獻:
[1]白俊.化學清洗技術在停工中的應用[J].廣東化工,2012,39(9):8~9
[2]叢海濤.化工設備化學清洗技術[J].石油化工腐蝕與防護,2001,18(4):60~64
[3]賀曉慧.水基金屬油污清洗劑的研製[J].精細化工,1998,(6):13~16

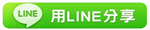
※石化緣推薦:走進地煉群雄之首——東明石化三十年歷程!
※安全科普:車輪這兒摸不得,否則非死即傷!
※國內最大的催化裂化裝置一次開車成功!
※石化緣推薦:中海油煉油化工科學研究院四大研究所、一中心一基地!
※石化緣推薦:盛虹石化裝置流程圖!
TAG:石化緣科技諮詢 |