刀具路徑的優化對高速切削起到什麼作用
(文章底部可以評論,歡迎對文章進行點評和知識補充)
精彩推薦
每天學點機械知識
(來源易搜刀具網)
以高切削速度、高進給速度和高加工精度為主要特徵的高速切削技術,在航空航天、模具製造及精密微細加工等領域得到了廣泛應用。高速切削不僅提高了對機床、夾具、刀具和刀柄的要求,同時也要求改進刀具路徑策略,合理的高速切削刀具路徑,能將切削過程中的切削負荷突變降至最低,高速切削機床只有有了合理的高速刀具軌跡才能真正獲得最大效益。
確定刀具路徑應滿足的基本要求
為了消除切削過程中切削負荷的突變,刀具路徑應滿足以下基本要求:
1. 切削過程中切削力恆定。
2. 盡量減少空行程。
3. 盡量減少進給速度的損失。
1
通用的刀具路徑
為了滿足上述基本要求,刀具路徑應是:
1)進刀時採用螺旋或圓弧進刀,使刀具逐漸切入零件,以保證切削力不發生突變,延長刀具壽命。
2)切削速度的連續和無突變,使切削連續平穩。
3)順銑切削使切削過程穩定,不易過切,刀具磨損小,表面質量好。
4)採用小的軸向切深以保證小的切削力、少的切削熱和排屑的順暢。
(1-1) 無切削方向突變,即刀具軌跡是無尖角的,普通加工軌跡的尖角處用圓弧或其他曲線來取代( 圖1),從而保證切削方向的變化是逐漸的而不是突變的,減小了衝擊,也能避免過切,在尖角處切削負荷不會突然加大( 圖2),引起衝擊。
(1-2) 採用等高線軌跡,加工餘量均勻的走刀路線可取得好的效果。(圖3a)為採用等高線法的刀具軌跡,刀具沿X 或Y 軸方向平動, 完成金屬的切除,這樣可保證高速加工中切削餘量均勻,更多數控編程知識關注微信公眾號(數控編程教學),對加工穩定,有利於刀具壽命的延長。(圖3b)為傳統方法的刀具軌跡,刀具沿斜線方向時,X、Y 方向的插補運動使加工餘量不均勻,降低了刀具的耐用度。
2
粗加工刀具路徑
(2-1) Z 向等高線層切法:即將零件分成若干層,一層一層逐層往下切,在每層中將零件的所有區域加工完再進入下一層,在每一層均採用螺旋或圓弧進刀,同時採用無尖角刀具軌跡( 圖4)。這樣有利於排屑,避免切削力發生突變。對薄壁件來說,更應採用這種刀具軌跡,因為這種刀具軌跡在切削過程中還能使薄壁保持較好的剛性。
(2-2) 插銑刀具路徑:較深腔體的粗加工可採用插銑的方法來加工,深腔加工, 需要很長的刀具,這時刀具的剛性很差,按常規的切削路線切削刀具易變形,而且也易產生振動,影響加工質量和效率,採用插銑的軌跡可解決這一問題。
(2-3) 擺線刀具路徑:採用擺線刀具軌跡(圖6)使刀具在切削時距某條曲線( 一般是零件的輪廓線及其平移線) 保持一個恆定的半徑,更多數控編程知識關注微信公眾號(數控編程教學),從而可使進給速度在加工過程中保持不變,徑向吃刀量取刀具直徑的5% 左右,因此刀具的冷卻條件良好,刀具的壽命較長,這對高速加工是非常有利的。
3
精加工刀具路徑
(3-1) 先在陡峭面用Z 向等高線層切法加工,然後在非陡峭面採用表面輪廓軌跡法加工( 見圖7);
(3-2) 先用表面輪廓軌跡法加工所有面,再在垂直方向上加工陡峭面( 見圖8)。
薄壁件的精加工採用Z 向等高線層切法,在加工過程中每一層都要盡量做到螺旋或圓弧進刀,採用無尖角刀具軌跡。
4
其他的刀具路徑
(4-1) 加工單一型腔的薄壁件,應盡量採用(圖9)所示的走刀路線,它比單純的等高線逐層切法對保持薄壁的剛性更好,保證加工餘量均勻,零件變形小。
(4-2) 對薄底零件應採用(圖10)所示的走刀軌跡。即從離支撐最遠的點開始切削,分層切削直到深度到位 ;每次深度銑到底後再向支撐處移動一個徑向切深,重複上一步的過程,直至切削完成。這樣在切削時能較好地保持零件剛性,避免振動。
刀具路徑
刀具路徑的優化對高速切削是非常必要的,對不同形狀的零件及不同的加工過程應採用不同的刀具軌跡,但是螺旋或圓弧進刀、切削速度的連續和無尖角刀具軌跡是在各種刀具路線中都應盡量採用的,以保證切削過程的平穩、快速。
點擊展開全文

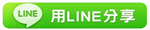
※大學實慣用數控機床加工「子彈」感覺自己很牛叉
※看完這個,對於切削液的降溫方法,無師自通!
TAG:機械微學 |