揭秘GE陶瓷基複合材料價值鏈——宏圖與現狀(下)
GE航空在陶瓷基複合材料(CMC)上已經花費超過15億美元,目標是將製造成熟度提升到可以大批生產的狀態。在過去10年間,GE使用的CMC原材料的數量已經增長20倍。到2020年,GE航空預計將在美國建立首個CMC的垂直集成供應鏈,擁有約750名僱員,每年生產20噸的CMC預浸料和10噸的SiC纖維。
在長達20年的耕耘之後,原創於GE全球研究中心(GRC)的CMC技術已經孵化到了GE的位於紐約州尼什卡納CMC精益實驗室和位於俄亥俄州伊文戴爾的快速工廠實驗室,並且在GE位於德克薩斯州紐瓦克的CMC低速初始生產(LRIP)中心開始了量產。GE航空複合材料和陶瓷製造總經理邁克爾·考夫曼表示:「我們與GRC通過在阿什維爾的生產而有緊密聯繫,這意味著產品的成品率可以通過供應鏈整體跟蹤。」在垂直集成的供應鏈中,生產問題可以充分利用GE的CMC資源的整體處理,最大限度提升速度和效率。
阿什維爾CMC工廠生產的兩種LEAP發動機零件
GE公司預見了先進位造的未來,在3D列印和數字線索/數字孿生/大數據技術上投入巨資,GE還為探索先進CMC的潛力奠定了一個堅實基礎,以期讓未來噴氣發動機滿足提升性能、減重和減排以及降低運營成本的需求。這種遠見不僅促使供應鏈結構按GE設想的那樣發展,也形成了基於團隊的工廠運行模式。
二、從現狀到宏圖——探秘GE航空阿什維爾CMC工廠
GE新建於北卡羅來納州阿什維爾的CMC零件生產廠投資1.25億美元,坐落於CMC快速工廠實驗室和正在阿拉巴馬州亨茨維爾建設中的CMC纖維和預浸料廠的中間。這家新廠房挨著GE航空一家有著70年歷史的轉子零件廠。我們可以通過GE航空CMC生產經理賴安·胡斯一起參觀這家新工廠。
1.即將自動化的鋪放和追求高效的熱加工
工廠擁有13000平米的開放式生產區域,儘管絕大部分空間還是空的,但胡斯表示正開始填充,每年都增加新的東西。「我們目前只有一條生產線,但是後續會複製更多條,每條都會為要將製造的零件類型進行修改。」他解釋道,CMC技術仍然是相同的,但是零件設計不同。「首條生產線分別是製造LEAP 1A/C和LEAP 1B的盒式葉冠和開口葉冠。未來,我們將建造燃燒室內襯、葉片、噴嘴和其它零件。」
SiC/SiC複合材料工藝鏈
他表示原材料從工廠的南端進來,最終將運至多條生產線,構成一個U型生產流。葉冠生產線在工廠北端,SiC纖維增強SiC基複合材料的製造有4個基本步驟:預浸帶切削和鋪放,多個熱加工步驟,零件後加工以及無損檢測(NDI)。
生產線從左邊開始,是一個玻璃環繞的、進行污染控制的潔凈間。胡斯表示:「進入潔凈間的原材料是單向帶,Gerber公司的自動切割機為每個零件的鋪疊而切出每層的外形。」目前,來料是從紐瓦克運來,亨茨維爾的首次交付預計在2018年5月。預浸帶不是卷狀,而是平板狀,以板狀送進鋪層料切割機。這些鋪層料之後在一個金屬模具上鋪放,形成複合材料鋪層。
胡斯表示:「當前,鋪放是手工的。」潔凈間對面是第二個用玻璃圍住的鋪放單元,配有Virtek視景國際公司的激光投影系統,輔助鋪層料定向和定位。兩個單元都有計算機終端,零件圖顯示在屏幕上,技術人員坐在裡面,把切割好的鋪層料放置在模具上。不過,胡斯表示正在開發自動鋪放工藝。「這個單元的自動化正在獨立於該工廠開發,現在正在進行工藝審查。2017年第四季度工藝就會就緒,以補充手工操作並且隨著生產速度上升,一步一步地擴大生產規模。」
環境控制下的切割和鋪層
下一個是熱加工區域,佔用了至少三分之一的生產線。熱加工是三個不同的步驟完成,第一步是在熱壓罐中,去除揮發性有機化合物(VOC),並且塑造零件外形。在鋪疊之後,零件密封在一個可重複使用的Torr技術公司真空袋下。「物理學規定了我們每個熱步驟中的加工時間,所以我們沒有能力在這裡縮短時間。但是,我們可以影響裝運時間,所以我們希望所有鍋爐盡量連續地使用。這是為什麼我們使用可重複使用的真空袋。」
通過一次性加工12個一組的零件,效率也得到提升。熱電偶指定了在真空袋內靠前和靠後的點,抽真空計劃安排包括1個可重複使用的通氣口材料、4個熱電偶口和2個真空口。ASC工藝系統公司的熱壓罐在比典型聚合物基複合材料加工更高的溫度下運行。
在熱加工中的第二步,「燃燒的」鍋爐將有機材料裂解,以形成CMC微結構中的碳橋。溫度比典型熱壓罐加工高得多,並且使用了惰性氣體。第三步和最後一步在熔滲(MI)鍋爐中進行,在超過1316攝氏度的運行溫度下烘烤零件,這就像家用的帶夾蓋的金屬高壓鍋,儘管比它大得多。在MI過程中,熔化的硅通過毛細作用穿過零件與碳發生反應,形成碳化硅(SiC),最終產品就是在SiC基體中有SiC纖維。
發動機CMC熱端零件的熱加工
「我們這條生產線有12台鍋爐。未來幾個月內,我們將複製這條生產線,增加另外12台。」他指出僅針對LEAP發動機葉冠,這些年的生產量從2015-2016年增長900%,從2016年到2017年增長400%。「我們還在為GE9X製作零件。」胡斯指向一個生產區域的顯示板,跟蹤了精益製造的指標。「每個團隊都在努力實施持續改進,每個團隊都有一個輔導者,管理安全、質量、交付、成本和現金等方面。」
2.接近單件流的精密加工和無損檢測
胡斯拾起LEAP 1A/C發動機的一個盒式葉冠,葉冠外表面是輕量化、銀色的,內表面是白色的,就像金屬但又不是。他還展示了一個LEAP 1B的開口葉冠,帶有一點曲度。第一級HPT葉冠形成了高壓渦輪葉片外圍的環形結構。LEAP 1B的葉冠在頂端沒有閉合的盒,而是開口的4個彎曲凸起,即凸緣,每個帶一個通孔,用來與發動機連接。
「在MI之後,就得到一個完全彎曲的CMC零件。」下一步是機械加工:「我們在生產線的每台機床上,使用一個帶真空卡盤的3R介面,以便儘可能地接近單件流。」這個3R介面涉及一個工件夾具系統,在加工線中可夾取多種不同的零件,實現快速安裝和最大的生產率。「我們進行簡單、不複雜的加工,每次完整一個特徵。我們用超強力膠水粘住工件到介面,以便機器人拾起它,一站站運送通過自動化加工線,每站不需要額外的安裝工作。最後,你就得到了一個完全加工好和標記好的零件。」
精密加工能力最大化
據胡斯稱,在這些類型的零件上進行常規磨削要花費一小時。「所以我們使用激光微噴單元,在一個水柱中射出激光。」水冷卻零件並且帶走碎屑,它還幫助維持孔直徑的高精度水平。「微噴可以在兩分鐘內鑽出這些孔。」該技術是聯合開發的:使用Synva公司創新的激光切割系統,牧野銑床公司的高精度加工技術,以及GE的優良孔鑽削軟體。葉冠底部表面沿著氣流通道,上面有來自3R介面的膠粘點,會使用金剛石磨料加工平滑。不過胡斯指出這是一項正在進行中的降本項目的主題,「我們很快就不會這樣做了。」
CMC零件生產線的最後一步是NDI,使用GE的計算機X射線斷層掃描(CT)機。每個零件都要檢測,掃描時間是15分鐘,完成時間是30分鐘,包括數據評價。
微噴工藝避免後處理瓶頸
3.當前的大數據,未來的大藍圖
阿什維爾的步伐是快速的,但是並不混亂。GE考慮了所有必需的方面,不只是為已經訂購的發動機交付零件,還有確保設施在接下來70年保持在生產的最前線。一個面向長期運行的例證就是銀管網路,從工廠中的每台機床直到屋頂都有鋪設。「這些室內乙太網電纜,都連接到我們的資料庫系統。因此鋪放次數、潔凈間內的相對濕度、鍋爐時間、加工指標和CT掃描,在每個零件的數字線索中都記錄下來,並用於分析以幫助我們優化工藝,提速降本。」
考夫曼表示GE的大數據能力是其當前戰略的基石。「大數據對我們的CMC供應鏈是關鍵,因為整個供應鏈是對工藝過程高度敏感的,有上千種輸入變數,而且還會持續波動。最開始在纖維精紡中的元素不僅是會影響纖維塗層和預浸料製作,還會全程影響直到組件中的固結如何發生。」大數據通過供應鏈的採集與集成還指導產品和工藝過程的模擬模型。「我們讓數據找到自身的相互關係,坦白地說,經常能發現我們在自建的模型中沒有預測到的東西。」
為什麼對設計和供應鏈的建立如此重視?「因為我們在過去十年投入了巨大資金,CMC技術是我們產品與眾不同的地方。我們希望保護這筆投資和我們的知識產權。我們熟悉我們的競爭對手在做什麼,我們是唯一使用這種方法去滲透一個增強體的,我們相信將達到更好的緻密性效果。」他指出另一個驅動因素是確保GE的合作夥伴願意將CMC工業化。「工業界對CMC的重視程度時高時低,但是我們堅信在減重、性能和效率方面能夠得到太多,對我們來說,決定是明確的。」而現在,正是前進的時候。
(航空工業發展研究中心劉亞威)
個人分享或轉載請註明來源和作者,刊物和機構如需轉載,請聯繫授權事宜:
聯繫人:王元元
關注本公眾號有以下三種方式:
3、長按下方二維碼,點擊「識別圖中二維碼」。

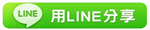
※藍色閃電划出——GE航空「藍弧」工藝助力航空發動機製造
※高價值航空零件的展翅高飛依賴基礎性研究
※NASA研究項目加速實現飛機電推進兆瓦級組件技術
TAG:民機戰略觀察 |