電池模組作為產品帶來的一些變化
版權聲明:本文為IND4汽車人版權所有,未經網站官方許可嚴禁轉載
開篇還是談一談整個電動汽車的未來的商業模式,也同時重新思考價值鏈。這樣比較能清楚的勾勒出未來電池模組,可能成為一個標準的產品系列,成為一個基本的單元。在這樣的條件下,產業鏈如何洗牌,車企、Pack企業和電芯企業在設計和製造兩個層面
電池系統的價值鏈分工方式
在談這個問題之前,其實我們真的需要思考一下對待電池系統這類佔用資金量非常巨大的部件,如何來定義的問題。我們以前單一採購較多的,更多還是原材料。真正達到總成採購的,以自動變速箱較多,其價格技術也是以千為單位的。在電池系統裡面,以萬為單位的採購,整個博弈和供給的過程真的還沒有穩定下來。
1) 設計分工
電動汽車層面的人員組織,其實和傳統汽車方面還是有差異。隨著大的車企,面臨在多個車型平台上構建不同產品,在設計資源和人力資源上的調整勢必成了一個很重要的分歧點。由於進行中的平台項目,所適應和調整的空間需要預留,使得整個電動汽車的開發資源,勢必把原來的從上到下,從車型VTS、單個電池系統的STS,再到下面子零件進行調整。如下圖所示,整個大的車企的車海戰術的支持,勢必使得在通用性的模組層級產生了一些預先的設定。通過彈性的設計,使得企業內相對標準化和可兼容的一部分出來,成為快速開發和多平台使用的必要條件。
這裡的模塊層級的基本組件包括:
電池模組:這個是封裝電芯的形式
EE電子系統的模塊化:這裡包含整個電子管理系統構建的重新梳理,也是需要進行模塊化切分的一個考慮對象
圖1 電池系統模塊化的分割
1.1 電池模組
不同的車企對待電池模組,一個需要考慮未來國家傾向性的的電池尺寸。《GB/T 34013-2017 電動汽車用動力蓄電池產品規格尺寸》由於是行業協調不同電池廠家現有產品,一個是乘用車、商用車、專用車等不同產品融合在一起了,顯得很雜亂;一個是確實缺乏一些實際電池系統較優設計的支撐,使得這個尺寸統一化的過程變成了電池廠家協商大會。
圖2 《GB/T 34013-2017 電動汽車用動力蓄電池產品規格尺寸》
汽車企業本身,由於未來的需求,是需要開始規劃模組標準化復用的過程,當然目前最多的還是與VDA一樣標準化模組實施,這最簡單本身也是一個跟隨的過程。
這個最簡單的思考,是在尺寸上做個分割。一個是從根據整車布置的需要,推薦模塊一個面的二維尺寸,在第三維尺寸上體現串並聯數量的變化 ,表現為模塊長度或者高度的尺寸自由度,適應整車空間的限制和設計的需要
通過對電池單體的串聯、並聯或串並聯混合的方式,確保電池模塊統一尺寸,並綜合考慮了電池本體的機械特性、熱特性以及安全特性。在安裝設計不變的情況下,根據不同的續航里程和動力要求,提供不同電池容量,以滿足不同的需求。這種模塊化應用,在單體、模組端都可實現大規模自動化生產,大幅降低生產成本,這就使得整個電池企業的供應都以模組為最小單元。
如下圖所示,比較之前在10~30Kwh,通過組合能量型電芯和功率型電芯,在結構層面,很多的工作已經被壓縮了。
圖3 VDA標準化模組在之前EV/PHEV兼容上很有優勢
圖4 PHEV和EV 模組
往更高層面,如之前所說的,更大的容量的電池系統,其模塊構成是如何的?
圖5 更大的電池包
在這個過程中,下一步的集成電池模塊,則比傳統電動汽車模塊容納更大容量電池組。以往電池模塊一般由 12 個容量為 2-3kWh 電池組組成,開始往能容納 24 個單體的 6-8kWh 的電池組。這無疑將在同樣的電池空間內,提高電池容量,有效增加電動汽車續航。
2) 製造分工
這個其實也是根據不同電池系統的成本構成細分的。由於整個電池系統的大頭在電芯層面,其基本的成本結構比例如下圖所示:
圖6 電池系統成本結構
你以為就這樣結束了嗎?當然還沒有!

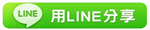
TAG:IND4汽車人 |