學術乾貨│尋根究底——等離子刻蝕技術
1. 序頑石默默,醴香幽幽,霧靄沉沉,便為尋常景。尋常之外,亦有因緣際會才能得見的勝景。「劍影奔星落」是流星如雨,「列缺霹靂」是閃電轟鳴。其相不同,其質一也。
閃電,通常是積雨雲產生電荷,底層為陰電,頂層為陽電,並且還在地面產生陽電荷,如影隨形地跟著雲移動。正電荷和負電荷之間彼此相吸,但空氣卻不是良好的傳導體。因此正電荷奔向樹木、山丘、高大建築物的頂端甚至人體之上,企圖和帶有負電的雲層相遇;負電荷枝狀的觸角則向下伸展,越向下伸越接近地面。最後正負電荷終於克服空氣的阻障而連接上。巨大的電流沿著一條傳導氣道從地面直向雲涌去,產生出一道明亮奪目的閃光。
圖1 閃電
流星是進入地球的大氣層內發出可見的光亮,並且被看見的流星體或小行星。對一個大於大氣層內自由路徑(由十公分至數米)的物體而言,它的發光是來自於進入大氣層的撞擊壓力產生的熱。因為絕大多數的流星都只是沙子到穀粒大小的流星體造成的,所以多數可以看見的光都來自於流星體被蒸發的原子和大氣層內的成分碰撞時,由電子所釋放的能量
圖2 流星
它們能夠發光,具有更高的能量和大量做隨機運動的自由帶電粒子。它們被稱為等離子體。因而我們所熟知的物態中加入了一名新成員——等離子體。
圖3 物質四態
2. 等離子體許多做隨機運動的帶電粒子集合在一起形成等離子體,換句話說,等離子體是由氣體電離後產生的正負帶電離子以及分子, 原子和原子團所組成。就平均效應而言,等離子體在宏觀上呈電中性。值得注意的是,氣體從常態到等離子體的轉變, 也是從絕緣體到導體的轉變。
圖4 氣態-等離子體
等離子體具有以下特點:電中性、受電場驅動、發光、含有大量具有高度活性的離子和自由基。
我們通常把電離度小於0.1%的氣體稱為弱電離氣體(低溫等離子體),電離度大於0.1%的氣體則是強電離氣體(高溫等離子體)。高溫等離子體常用在受控核聚變中,而低溫等離子體則被用於切割、焊接和噴塗以及製造各種新型的電光源與顯示器。
圖5 強弱電離氣體
這裡我們著重介紹半導體製造工藝中的刻蝕技術,所以一起來認識弱電離等離子體吧!
這裡有一個簡單的放電裝置原理圖。這個裝置中有一個電壓源,在兩個極板之間的電壓驅動下,低氣壓氣體產生放電現象,電流會從一個極板流向另一個極板。此時,氣體被「擊穿」而產生等離子體,但是這種等離子體的密度遠遠小於氣體分子的密度,因此被稱為弱電離等離子體。
圖6 弱電離等離子體
3. 刻蝕與等離子體刻蝕刻蝕,是半導體製造工藝、微電子IC製造工藝以及微納製造工藝中的一個重要的步驟。廣義來講,刻蝕成為了通過溶液、反應離子或其它機械方式來剝離、去除材料的一種統稱,是微加工製造的一種普適叫法。而因為等離子體放電可以產生具有化學活性的物質,所以被廣泛用於改變材料的表面特性。當「刻蝕」遇上"等離子體",竟開啟了「等離子體刻蝕」新的篇章!
圖7 等離子體刻蝕
劃重點——理想的刻蝕工藝必須具有以下特點:
各向異性刻蝕,即只有垂直刻蝕,沒有橫向鑽蝕。這樣才能保證精確地在被刻蝕的薄膜上複製出與抗蝕劑上完全一致的幾何圖形;
良好的刻蝕選擇性,即對作為掩模的抗蝕劑和處於其下的另一層薄膜或材料的刻蝕速率都比被刻蝕薄膜的刻蝕速率小得多,以保證刻蝕過程中抗蝕劑掩蔽的有效性,不致發生因為過刻蝕而損壞薄膜下面的其他材料;
加工批量大,控制容易,成本低,對環境污染少,適用於工業生產。╮(╯╰)╭
刻蝕工藝分為兩類,濕法刻蝕和干法刻蝕。
濕法刻蝕是傳統的刻蝕方法。把矽片浸泡在一定的化學試劑或試劑溶液中,使沒有被抗蝕劑掩蔽的那一部分薄膜表面與試劑發生化學反應而被除去。
例如,用一種含有氫氟酸的溶液刻蝕二氧化硅薄膜,用磷酸刻蝕鋁薄膜。
優點:操作簡便、對設備要求低、易於實現大批量生產,並且刻蝕的選擇性也好。
缺點:化學反應的各向異性較差,橫向鑽蝕使所得的刻蝕剖面呈圓弧形。這使精確控制圖形變得困難。抗蝕劑在溶液中,特別在較高溫度的溶液中易受破壞而使掩蔽失效,因而對於那些只能在這種條件下刻蝕的薄膜必須採用更為複雜的掩蔽方案。
圖8 濕法刻蝕所得的薄膜剖面
對於採用微米級和亞微米量級線寬的超大規模集成電路,刻蝕方法必須具有較高的各向異性特性,才能保證圖形的精度,但濕法刻蝕不能滿足這一要求。
干法刻蝕是上世紀70年代末研究出一系列所謂干法刻蝕工藝,包括有離子銑刻蝕、等離子刻蝕和反應離子刻蝕三種主要方法。
離子銑刻蝕:低氣壓下惰性氣體輝光放電所產生的離子加速後入射到薄膜表面,裸露的薄膜被濺射而除去。由於刻蝕是純物理作用,各向異性程度很高,可以得到解析度優於1微米的線條。這種方法已在磁泡存儲器、表面波器件和集成光學器件等製造中得到應用。但是,這種方法的刻蝕選擇性極差,須採用專門的刻蝕終點監測技術,而且刻蝕速率也較低。
等離子刻蝕:利用氣壓為10~1000帕的特定氣體(或混合氣體)的輝光放電,產生能與薄膜發生離子化學反應的分子或分子基團,生成的反應產物是揮發性的。它在低氣壓的真空室中被抽走,從而實現刻蝕。通過選擇和控制放電氣體的成分,可以得到較好的刻蝕選擇性和較高的刻蝕速率,但刻蝕精度不高,一般僅用於大於4~5微米線條的工藝中。
反應離子刻蝕:這種刻蝕過程同時兼有物理和化學兩種作用。輝光放電在零點幾到幾十帕的低真空下進行。矽片處於陰極電位,放電時的電位大部分降落在陰極附近。大量帶電粒子受垂直於矽片表面的電場加速,垂直入射到矽片表面上,以較大的動量進行物理刻蝕,同時它們還與薄膜表面發生強烈的化學反應,產生化學刻蝕作用。選擇合適的氣體組分,不僅可以獲得理想的刻蝕選擇性和速度,還可以使活性基團的壽命短,這就有效地抑制了因這些基團在薄膜表面附近的擴散所能造成的側向反應,大大提高了刻蝕的各向異性特性。反應離子刻蝕是超大規模集成電路工藝中很有發展前景的一種刻蝕方法。
By the way, 現代化的干法刻蝕設備包括複雜的機械、電氣和真空裝置,同時配有自動化的刻蝕終點檢測和控制裝置。
這裡我們著重介紹干法刻蝕中的等離子體刻蝕,因為它是目前能夠各向異性地將一些材料從物體表面去除並且在工業上可行的技術。
它的基本原理是:
等離子體產生激活態的粒子以及離子。激活態粒子(自由基)在干法刻蝕中主要用於提高化學反應速率,而離子用於各向異性腐蝕。
在固定能量輸入的氣體中, 電離和複合處於平衡狀態,在正負離子複合或電子從高能態向低能態躍遷的過程中發射光子。這些光子可用於終點控制的檢測。
半導體工藝等離子體一般都是部分電離,常規0.01%~10%的原子/分子電離。
在工業中常採用高頻輝光放電反應來產生等離子體。因而等離子體刻蝕是採用高頻輝光放電反應,使反應氣體激活成活性粒子,如原子或遊離基,這些活性粒子擴散到需刻蝕的部位,在那裡與被刻蝕材料進行反應,形成揮發性生成物而被去除。它的優勢擁有快速的刻蝕速率的同時能夠獲得良好的物理形貌 。
4. 刻蝕工藝過程一般情況下,有四種基本的低氣壓等離子體工藝過程可以用於物體表面去除材料,即濺射、純化學刻蝕、離子能量驅動刻蝕和離子-阻擋層複合作用刻蝕(離子能量防護法)。
圖9 四種基本的等離子體刻蝕工藝過程
濺射是由於能量離子的撞擊而引起表面物質的原子急速蒸發和向外噴射的純物理過程。
在濺射刻蝕過程中,襯底在真空反應室內被置於負電位的固定器上。導入的氬氣在反應室內離化成帶正電荷的高能(500eV)氬離子。氬離子在電場中加速轟擊位於陰極固定器上的襯底薄膜表面,如果轟擊離子傳遞給被撞原子的能量比原子的結合能(幾到幾十eV)大,就會使被撞原子脫離原來位置飛濺出來,形成濺射刻蝕。
優點:具有較好的各向異性。
缺點:刻蝕選擇性較差、刻蝕速率較小且會造成一定的刻蝕損傷。
舉例:在刻蝕Al-2%Cu薄膜時可以用濺射的方法去除銅。
圖10 濺射刻蝕系統示意圖
在純化學刻蝕過程中,等離子體只提供氣相的刻蝕原子或分子,它們與表面發生化學反應生成氣相產物。這個過程可以具有很高的化學選擇性。但是純化學刻蝕幾乎總是各向同性的,這是因為氣相刻蝕離子是以近似均勻的角分布到達襯底表面的。因此,除非參與反應的一方是晶體(其反應速率與結晶取向有關),我們可以認為純化學刻蝕速率是比較各向同性的。
舉例:氬等離子體使氯分子分解成氯原子,活化的Cl與表面的硅結合生成易揮發的SiCl4,從而使Si被Cl刻蝕。
在離子能量驅動刻蝕過程,是受離子能量驅動的增強型刻蝕。其中等離子體既能產生刻蝕離子,又能提供載能離子。刻蝕原子和載能離子相結合進行刻蝕的效果比單純用純化學刻蝕或者只用濺射刻蝕的效果好得多。
舉例:當用高入射通量的氟原子刻蝕硅時,一個1 kV 的氬離子可以從材料表面去除25個硅原子(和100個氟原子)。
離子-阻擋層複合作用刻蝕,需要在刻蝕中使用能形成阻擋層的粒子。等離子體能夠提供刻蝕粒子、載能離子和形成阻擋層的前驅物分子,該分子可以吸附或沉積在襯底表面並形成保護層或聚合物薄膜。
舉例:利用 CCl4/Cl2或 CHCl3/Cl2放電對鋁進行各向異性刻蝕,得到鋁的溝槽或孔。
圖11 對等離子體刻蝕要求的計算示意圖
雖然四種刻蝕過程各有特點,但對特定薄膜的刻蝕經常需要這些刻蝕過程並行或串列進行,例如前面提到的對Al-2%Cu的刻蝕。再舉個例子,如圖11所示(在厚度為d的薄膜上刻蝕一個寬度為w的溝槽對刻蝕各向異性的要求),考慮在厚的多晶硅層挖一個垂直的溝槽,要求刻蝕選擇性必須足夠高以至於在二氧化硅層上不發生刻蝕。這可能需要兩步的刻蝕過程來完成。第一步是快速的、高各向異性的離子能量驅動刻蝕。並行發生的對側壁的純化學刻蝕將決定該過程的各向異性。除去幾乎所有多晶硅後,最後一步是慢速的,高選擇性的但相對各向同性的刻蝕,用以去除剩餘的多晶硅並使得對下面氧化層的刻蝕量最小。如果第一步完成後剩餘的多晶硅足夠薄,則第二步產生的很小的底切是可以接受的。
5. 化學反應框架對於刻蝕速率、對掩膜和下層材料的刻蝕選擇性以及各向異性的要求之間存在一定的矛盾,所以等離子體刻蝕中使用的混合氣體通常較複雜。對於離子-阻擋層複合作用刻蝕更是如此,在這種刻蝕中我們必須在刻蝕粒子通量、形成阻擋層的粒子通量和襯底上的粒子通量間找到一個平衡。而且等離子體可以使原料氣體分解成其他(通常更有活性)的粒子。
原料氣體和它們的分解產物可以包括如下的化學成分:
具有飽和結構的粒子:CF4、CCl4、CF3Cl、COF2、SF6等;
具有不飽和結構的粒子:CF、CF2、CF3、CCl3等;
刻蝕粒子:F、Cl、Br、O(對光刻膠)、F2、Cl2、Br2等;
氧化劑:O、O2等;
還原劑:H、H2等;
非反應氣體:N2、Ar、He等。
(接下來我們可以混搭了,有沒有一種瞬間變成魔法師的感覺 (>
這些粒子可以按如下的一些反應形式在氣相和表面上進行相互反應:
e+飽和粒子不飽和粒子+刻蝕粒子+e
刻蝕粒子+襯底揮發性產物
不飽和粒子+襯底薄膜
對於一些襯底材料(如二氧化硅),不飽和粒子本身可以成為刻蝕粒子,即
不飽和粒子+襯底揮發性產物
在低氣壓下,如下的三體反應:
刻蝕粒子+不飽和粒子(+M)飽和粒子(+M)
在氣相中是不重要的,但在表面上或高氣壓下或許是重要的。如果在原料氣體中能夠添加氧化劑(通常是氧氣或包含氧原子的氣體)或還原劑(通常是氫氣或包含氫原子的氣體),還可以發生如下反應:
氧化劑+不飽和粒子刻蝕粒子+揮發性產物
還原劑+刻蝕粒子揮發性產物
在襯底上刻蝕粒子與不飽和粒子的通量是一個重要的過程參數。
實例:
我們可以把刻蝕粒子(Cl2、Br2)添加到原料氣體中以增加刻蝕粒子與不飽和粒子間的比例;也可以加入氧化劑,通過氧化不飽和粒子產生刻蝕粒子的方法來提高這個比例。例如,
CF3+OCOF2+F
反之,如果需要,我們也可以加入與CF4相比具有較低的F/C比例的氣體(如c-C4F8、C3F8、C2F4)和氫氣以降低刻蝕粒子與不飽和粒子間的比例,從而通過在側壁上沉積更多的薄膜來提高對側壁的保護。
6. 等離子刻蝕處理材料的應用A.用鹵素原子刻蝕硅有選擇性地和各向異性地除去已經圖形化的硅或多晶硅薄膜,是等離子體刻蝕最重要的應用之一。它的基本刻蝕原理是用「硅-鹵」鍵代替「硅-硅」鍵,從而產生揮發性的硅鹵化合物。用氟原子刻蝕硅是人們在實驗中能夠表徵得最清楚的表面刻蝕過程,這裡我們也用此例來說明等離子體的刻蝕過程。
離子能量驅動的氟原子刻蝕
前面提到,當用高入射通量的氟原子刻蝕硅時,一個1 kV的氬離子可以從材料表面去除25個硅原子(和100個氟原子)。當存在離子轟擊時,SiFx層中氟原子總的表面濃度最多可以減少到一半。而且,刻蝕產物中各成分間的比例也改變了,一個顯著的特點是形成了很高比例的SiF2(g)。雖然刻蝕的各向異性比可以高達5~10,但在這種條件下對溝槽側壁仍然存在相當高的純化學刻蝕速率。因此,一般不採用氟基的各向異性的硅刻蝕。
人們提出了許多機制來解釋在氟原子刻蝕硅的過程中,由於離子轟擊使刻蝕速率增加的原因。Gary 等人(1993)提出了一個氬離子增強的氟原子刻蝕硅(和二氧化硅)的更完整的模型,由該模型得到的結果與高通量的離子和原子束的試驗結果及其他實驗數據一致。當刻蝕硅時,該模型的動力學過程包括以下一些過程。
圖12 氬離子增強的氟原子刻蝕硅模型的動力學過程
在這個模型中,離子轟擊增加刻蝕速率的主要機制包括:離子轟擊導致了化學吸附密度的增加;刻蝕產物的化學增強的物理濺射速率的增加;刻蝕產物的化學反應速率和熱解吸附速率的增加。
B.Si3N4的刻蝕氮化硅一般用作使硅局域氧化的掩膜材料、電介質及最後的鈍化層。有兩種類型的氮化硅材料:在高溫下用化學氣相沉積(CVD)產生的氮化硅和在溫度低於400 °C時用等離子體增強化學氣相沉積(PECVD)生長的氮化硅。
用PECVD生長的材料不一定具有3:4的Si/N原子數比,一般在晶格中還有很大比例的氫原子。PECVD生長的材料的刻蝕速率一般比CVD生長的氮化硅的刻蝕速率高。
圖13 被刻蝕的氮化硅
用氟原子以純化學方式刻蝕氮化硅對二氧化硅的刻蝕選擇比是5~10,但對硅的刻蝕選擇比很低。刻蝕是各向同性的,活化能約為0.17V。用低F/C比例的氟碳化合物原料氣體可以進行各向一行的離子能量驅動的氮化硅刻蝕,它對二氧化硅的刻蝕選擇比很低,但對硅和光刻膠有相當高的刻蝕選擇比。
C.光刻膠的刻蝕光刻膠掩膜材料主要是由碳和氫組成的長鏈有機聚合物組成。可以用氧等離子體各向同性地從晶圓上刻蝕(脫除)光刻膠掩膜材料。
在所謂的光刻膠表面成像干法曝光工藝中,氧等離子體被用來各向異性地將圖形轉移到掩膜材料上。在這兩種應用中氧原子是具有活性的刻蝕粒子。
圖14 光刻膠刻蝕示意圖
氧原子對許多光刻膠的純化學刻蝕速率是較低的,但可以通過向原料氣體混合物中添加百分之幾的C2F2或CF4來增加刻蝕速率。
用氧等離子體進行離子增強的各向異性刻蝕可以實現光刻膠表面成像干法曝光工藝過程。在這種方法中光刻膠層只有頂部的一小部分體積被曝光。
下面是典型的光刻膠表面成像技術的流程。
圖15 硅化表面成像的光刻膠干法曝光工藝的典型流程圖
使1.5μm厚的光刻膠層的頂部0.2μm厚的部分曝光形成圖形。
將光刻膠暴露在含硅的氣體中使光刻膠被硅化。硅被選擇性地吸收到曝光的光刻膠中,但不被沒有曝光的光刻膠吸收。
用氧等離子體把光刻膠各向異性地刻蝕掉。
刻蝕過程的開始階段是氧原子與曝光的、含硅的光刻膠表面層反應產生SiOx的掩膜,它可以阻止接下來的對光刻膠離子輔助的氧原子刻蝕。而沒有曝光的,不包含硅的光刻膠就被各向異性地刻蝕掉。這樣,原始的表面圖像就被轉移到整個厚度的光刻膠薄膜上。
D.鋁的刻蝕鋁在集成電路中通常用作互連材料,因為它有很高的電導率,並且對硅和二氧化硅也有良好的成鍵能力和黏結性,此外還具有與CDV氧化物和氮化物的兼容性和在硅中形成歐姆和肖特基接觸點的能力。
圖16 感應耦合等離子體刻蝕鋁
因為AlF3是不揮發的,所以氟原子不能用於刻蝕鋁,通常使用的原料氣體是Cl2和Br2。這兩種氣體在沒有離子轟擊的情況下就可以強烈地刻蝕鋁,刻蝕是各向同性的。鋁的各向異性刻蝕需要使用包括阻擋層化學過程的離子增強刻蝕。當原料氣體是氯氣時,需要使用像CCl4、CHCl3、SiCl4和BCl3這樣的添加劑。
E.銅的刻蝕
在高性能的集成電路中,用銅取代鋁作為互連材料應用得越來越多,因為銅的電導率幾乎比鋁高60%,而且具有極大的抗電遷移能力,然而,因為鹵化銅的蒸氣壓很低,限制了銅刻蝕被成功地用於商業目的。
圖17 等離子體銅刻蝕
這裡我們講一種常用的銅的刻蝕工藝。通常採用金屬鑲嵌過程使銅形成圖案,來製造銅的互連導線。在該工藝的過程中,首先在襯底上沉積一層電介質材料,用等離子體刻蝕在該電介質層上形成銅互連的圖案,然後用物理或化學氣相沉積或電鍍的方法把銅沉積在整個電介質表面上,最後用化學-機械拋光(CMP)法去除電介質表面上多餘的銅。在此過程中,在形成銅互連圖形時用介質的蝕刻代替了金屬刻蝕。
7. 流行的等離子放電刻蝕技術以上是五種較為常見的等離子體刻蝕的應用,下面我們一起來認識較流行的等離子放電刻蝕技術。它們分別是:反應離子刻蝕 (RIE)、微波電子迴旋共振等離子體刻蝕(ECR)、感性耦合等離子體刻蝕(ICP)。A.反應離子刻蝕(RIE)
它的原理是利用反應氣體離子在電場中的定向運動的刻蝕。
圖18 反應離子刻蝕原理圖
頻率為13.56MHz 的射頻電壓加在兩塊平行電極上,樣片放在陰極上,陽極與反應器壁接地。陰極面積小,而陽極面積大,形成非對稱性輝光放電系統。在等離子體區域與電極之間形成等離子體鞘層,小面積電極一邊具有大的鞘層電壓,因此離子在陰極鞘層區域被加速。高能量的離子垂直轟擊樣片靶面,造成濺射,於是靶面被刻蝕。離子對刻蝕起了主要作用。反應離子刻蝕以物理濺射為主,兼有中性活化自由基參加的化學反應。因此反應離子刻蝕也稱為反應離子濺射刻蝕。它的優點是刻蝕速率快,且有各向異性,最小限寬達0.2μm,缺點是容易造成器件損傷。
圖19 RIE刻蝕圖
B.微波電子迴旋共振等離子體刻蝕(ECR)微波能量被離化氣體吸收形成等離子體。我們知道,微波在等離子體中主要有三種吸收機制:碰撞吸收、無碰撞吸收和非線性反常吸收。吸收方式主要取決工作氣體的壓力還有所產生的等離子體的性質。電子迴旋共振微波等離子體屬於無碰撞吸收。
圖20 微波電子迴旋共振等離子體刻蝕系統總體結構示意圖
微波經傳輸迴路引入到共振腔開口面附近的陶瓷窗上,同時陶瓷窗表面的永磁磁鋼產生高強磁場,在此磁場作用下,腔體內氣體分子的外層電子做圓周運動。當電子的圓周運動頻率與微波角頻率一致時,ECR條件成立。在這個條件下,電子能有效地吸收微波能量並被加速,使氣體大量電離,由於電子的碰撞,提高了電離效率,促使更多的氣體分子電離。於是在沒有放電電極的情況下,僅由等離子源便產生了高密度、低溫等離子體。由於磁場梯度,產生了等離子體中的電子分布,並形成了等離子電位梯度,在這個電位梯度作用下,形成了指向樣品的等離子流。
ECR的優點是可以產生很高的等離子體密度,又可以維持較低的離子轟擊能量,解決了高刻蝕速率和高選擇比這個原本相矛盾的問題。它的缺點是結構複雜,需要微波功率源,及微波諧振與樣品基板射頻源的匹配問題。
C. 感性耦合等離子體刻蝕( ICP)
圖21 感性耦合等離子體刻蝕系統總體結構示意圖。
ICP系統有2個獨立的13.56MHz的射頻電源RF1和RF2,一個接到反應室外的電感線圈,功率為1500W,另一個接反應室內的電極,功率為700W。
給反應室外的線圈加壓時,反應室內產生交變的電磁場,當電場達一定程度,氣體產生放電現象,進入等離子態,交變的電磁場使等離子體中電子路徑改變,增加等離子體密度。反應室內的電極電壓提供偏置電壓給等離子體提供能量,使等離子體垂直作用於基片,並與其反應生成可揮發的氣態物質,以達到刻蝕的目的。反應生成的可揮發氣體由機械泵從反應室中抽出。感應耦合等離子體刻蝕系統還包括供氣系統、抽氣系統和冷卻系統,供氣系統和冷卻系統由流量計控制其流量 ,抽氣系統由機械泵抽真空,並由真空計測其真空度。
圖22 ICP刻蝕圖片
8. 總結七十多年前,人們發明了晶體管;六十多年前,集成電路出現了;而微處理器的面世也已經有四十多年了。技術不斷地創新,相關的等離子體工藝也需要持續地革新。希望這份關於等離子體蝕刻的基礎說明能幫你初步的認識它。後附一些等離子體蝕刻的相關資料(密碼:atb9),學習快樂!
參考資料
[1] Michael A. Lieberman,Allan J. Lichtenberg. 等離子體放電原理與材料處理[M]. 蒲以康,譯. 北京:科學出版社,2007:6,440-471
[2] 劉之景,劉晨. 光刻與等離子體刻蝕技術[J]. 物理,1999,28(7):426-429
[3] 鄭志霞,馮勇建,張春權. ICP刻蝕技術研究[J]. 廈門大學學報(自然科學版),2004,43:365-368
[4] 徐新艷,王家友,楊銀堂,李躍進,吳振宇. 微波ECR等離子體刻蝕系統[J]. 真空科學與技術,2002,22(5):385-386
本文由材料人編輯部學術乾貨組Ahenn供稿,材料牛編輯整理。
技術服務

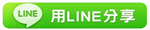
※Adv.Mater.基於V2–VI3二維納米片的定性自組裝工程以及熱電研究
※激光錘鍛造石墨烯
※JACS:高性能單原子鉬催化劑用於氮還原合成氨
※Nature:分子動力學模擬探測金屬塑性極限
※Natl.Sci.Rev.張錦展望:單壁碳納米管的手性可控制備發展路線
TAG:材料人 |