典型燃煤電廠節能降耗措施綜述(1)
電力行業節能環保公眾服務平台——權威、專業、創新的電力節能環保公眾號
典型燃煤電廠節能降耗措施綜述(1)
一、概述
華能鶴崗電廠地處黑龍江省鶴崗市新華鎮,一期工程安裝兩台30萬千瓦亞臨界濕冷機組,於1999年投產,汽輪機為哈爾濱汽輪機廠生產,型號為N315-16.7/537/537型;鍋爐為哈爾濱鍋爐廠製造,型號為HG-1021/18.2-YM8型亞臨界參數自然循環鍋爐,配備鋼球磨煤機中間儲倉式乏氣送粉系統。二期工程安裝一台60萬千瓦超臨界機組,於2007年投產,汽輪機為哈爾濱汽輪機廠生產,型號為CLN600-24.2/566/566型超臨界、一次中間再熱、三缸四排汽、單軸、雙背壓凝汽式機組;鍋爐為哈爾濱鍋爐廠製造,型號為HG-1900/25.4-YM4型超臨界參數變壓直流爐,配備中速磨煤機直吹式制粉系統。
二、節能改造案例介紹
(一)降低廠用電率節能案例
1、#3爐磨煤機電機增頻改造
由於入爐煤熱值嚴重偏離設計工況,制粉系統在額定出力下運行,#3機組出力最大帶至450MW,無法帶滿負荷運行,經鍋爐廠核算,按目前燃用煤種,鍋爐BMCR工況下燃煤量為320t/h(原設計為241.7t/h)。需增加磨煤機出力,以滿足現煤種帶負荷需要。經過計算磨煤機轉速由24.3rpm增加至30rpm可以達到所需要求。為此電廠利用一期機組淘汰的變頻器進行再利用,採用超頻的辦法對A、B、C三台磨煤機電機進行增頻改造,通過提高磨煤機出力,不僅使機組出力達到90%以上,磨煤機耗電率亦相應下降,而且機組整體耗電率隨出力係數提高而降低。
2、循環水泵降速改造及優化運行
鶴崗電廠冬季環境溫度較低,結合地區特點,在2007年11月對循環水泵進行優化運行,當環境溫度低於15℃時,循環水泵由兩台泵運行改為單台泵運行,經試驗同一負荷下凝汽器背壓維持不變,但廠用電率由優化前的1.1%降至0.7%,供電煤耗降低1.3g/kWh。
經過一段時間運行及同類型機組對標,發現循環水泵運行性能還是不夠理想,冬季不同月份循環水量不能根據運行工況進行及時調整,廠用電率仍偏高。經可研論證,採取循環水泵雙速改造措施,即利用原有繞組結構,在不更換定子繞組和不降低原有絕緣等級的情況下,通過改變電機內部繞組接線方式,形成雙速,達到改變循環水泵轉速的目的。改造後結合運行優化管理,不同季節(循環水入口溫度)、不同負荷實現單台低速循環水泵、單台高速、兩台低速、一高一低、兩台高速五種運行方式,同時優化運行時間由冬季延伸到春秋季節,在優化時間段,循環水泵耗電率降低0.5%左右,全年循環水泵耗電率平均降低0.2%以上。
目前在實際運行中,由於冬季環境溫度最低達-30℃,循泵優化運行後,上塔循環水量降低,水塔結冰較為嚴重,每天要啟動另一台循泵對水塔進行化冰兩小時左右,泵啟動頻繁。另外,本地區晝夜溫差較大,每天要根據溫度變化進行泵高、低速切換運行,對泵和系統衝擊較大,電廠正進行考察、分析,將根據對比分析結果考慮進行變頻改造,一方面可以減少由於結冰對填料的損壞,影響水塔冷卻效果,另外也可避免泵啟動頻繁對泵體及凝汽器管束的衝擊。
3、一期風煙系統節能措施
鶴崗電廠一期兩台機組風煙系統分別配備兩台動葉可調式軸流送風機和兩台雙吸離心式引風機,送風機型號為ASN-2640/1600,電機額定功率為1600kW,引風機型號為Y4-2×73No29F,電機額定功率為2240kW,風機在實際運行時,一直存在送風機動葉和引風機調節擋板開度小,運行電流大,節流損失較大。電廠決定對離心式引風機進行變頻改造,結合循環水泵單套優化運行經驗對軸流式送風機進行運行優化。其中,引風機改造後節電量幅度在30%左右,效果非常明顯;送風機經調試實現單套風機運行,在75%負荷率下,送風機動葉開度由9%提高到40%,兩台送風機運行電流由(72.6+74)A變為單台的91.9A,電流下降較為明顯。但經連續半月以上跟蹤發現,日統計送風機耗電率降低不明顯,主要是送風機設計性能與管網匹配性較差,單套運行時電機電流雖然下降,但功率因數變化較大,實際運行功率降低不大,且鍋爐兩側排煙溫度偏差增加較大。後經西安熱工院專家診斷,確定機組負荷率在80%以上時,送風機運行效率低於50%,而機組負荷率在70%左右,運行效率僅為35%,診斷結論是該型送風機與本廠送風系統極不匹配,必須全面徹底改造或更換成其它型號的風機才能適應本廠送風系統。經可研論證,電廠對一期四台送風機進行降速改造,轉速由990rpm降到595rpm,改造後,不同負荷段風機效率均在70%以上,月統計送風機耗電率由0.23%降到0.1%以下,實際節電效果好於預期,一年半就收回了成本。
4、引風機、增壓風機優化運行及改造
鶴崗電廠於2009年對三台機組進行脫硫系統安裝改造,2010年2月份分別投入運行,脫硫系統運行耗電率平均在0.9%左右,通過採取對吸收系統運行優化(在不同負荷、不同入口SO2濃度時,確定最佳的漿液循環泵組合方式、最佳的PH設定值、氧化風機的投運台數、吸收塔液位和石灰石粒徑)、除霧器運行維護及檢修治理、公用系統(製漿、脫水等)運行優化,三台機組脫硫耗電率平均降到0.75%,但在節能監督管理中,分析發現在引風機、增壓風機聯合優化運行時,增壓風機出力降到最低,引風機還有一定調整空間,經研究討論,並報請環保部門,在70%-80%負荷率區間,對#1機組進行停運增壓風機試驗,用引風機代替增壓風機取得成功,後續又對增壓風機加裝旁路改造以及增壓風機轉子抽出工作,一期實現100%額定工況時,引風機取代增壓風機運行,脫硫耗電率月均低於0.35%,二期實現75%負荷率下,引風機取代增壓風機運行,脫硫耗電率月均在0.6%左右。
5、凝結水泵變頻改造
三台機組原凝結水泵運行方式為定速運行,流量的調節是靠調門進行節流調節,調節門開度在20-40%區間運行,這種調節方式節流損失很大,同時由於節流調節,泵出口壓頭大,軸承及密封部件經常損壞,增加了檢修維護成本。改造後,一期凝結水系統耗電率由0.32%降到0.15%,二期由0.38%降到0.16%。
6、一期電除塵節能措施
2009年末一期兩台機組電除塵進行三電場改四電場後,電廠結合市場推廣技術,對一期電除塵一電場高頻電源改造及節能智能控制系統優化改造,改造後電除塵耗電率由改造前的0.23%降到0.11%,降幅達到52%。 小結:幾年來通過落實上述節電措施,並通過合同能源管理方式對#3機組引風機電機進行變頻改造,水源地升壓泵變頻改造等措施,三台機組耗電率均降低在1個百分點以上。具體見附圖(圖表中不含脫硫耗電率)
(二)一期中儲式乏氣送粉鋼球磨製粉系統節能措施
鶴崗電廠一期2*300MW機組配備8套制粉系統,採用中間儲倉式布置,熱風乾燥、乏氣送粉方式,磨煤機型號為DTM-350/600,電動機額定功率1000kW,排粉機型號為M6-31NO200,葉輪直徑為2000mm、風量119880m3/h、風壓13940Pa、轉速1490rpm、額定功率800kw。從節能監督角度分析,制粉系統運行好壞不僅影響制粉系統電耗,同時對鍋爐燃燒效率影響較大,為此,電廠成立制粉系統優化攻關小組,通過對鋼球裝載量、煤粉細度、磨出入口溫度、排粉機出口風壓等調整控制、低谷時段合理組織配煤,降低制粉系統運行台數,制粉系統再循環風門調整等不斷摸索試驗制定對應節能措施。
1、運行優化方面
(1)控制磨煤機電流在92-95A之間,低於92A以下時,立即補加鋼球,保證磨煤機出力。
(2)控制磨煤機出口溫度在72-75℃,入口溫度不低於200℃,保證磨煤機乾燥出力。
(3)採取制粉系統優化調整,精細調整給煤量,控制好磨煤機出入口差壓,始終保持磨煤機在最大出力。
(4)每天化驗一次各磨煤機的煤粉細度,始終保持R90在20-25%之間,發現超出範圍立即調整分離器擋板,並及時進行跟蹤化驗。
(5)值長根據調度曲線合理指揮控制配煤,並充分利用螺旋輸粉機進行倒粉,確保在75%負荷率以下停止#1排粉機運行。
(6)嚴格控制排粉機出口風壓在3000-3300Pa之間,並且及時關閉停用給粉機對應的一次風門(根據試驗每個備用給粉機對應一次風門未關閉,造成排煙溫度升高3-4℃),降低排粉機耗電率。
(7)運行中如因為下層部分給粉機停用影響#1制粉系統通風出力不足時,應通過調整再循環風門進行控制,嚴禁開啟備用給粉機一次風門,人為使鍋爐漏風,影響鍋爐燃燒效率。
(8)盡量減少磨煤機啟停次數,當粉位出現不均衡時,用螺旋輸粉機進行倒粉。
(9)當發生磨煤機斷煤情況時,及時停止磨煤機運行,防止長時間空轉磨煤機。
(10)啟動磨煤機時及時啟動給煤機運行,並且將給煤量加至最大合理值。
(11)停磨煤機將煤粉抽凈後,及時停止磨煤機運行,並將系統風導至近路風運行,降低排粉機出力。
2、檢修治理方面
(1)每月定期對波浪瓦進行檢查和更換,重點保證對磨入口的檢查和更換,以保證護甲波形。
(2)嚴格按照制粉系統漏風檢查規定,對磨煤機本體、鎖氣器、人孔門、防爆門、系統風門以及螺旋輸粉機進行檢查和維護。
(3)每次停機執行粗粉分離器折向擋板檢查消缺規定,保證擋板內外開度一致,並調整開度在40-60%之間,以降低系統通風阻力和提高分離效率,減少回粉中合格煤粉含量,提高制粉出力。
(4)每次停機對排粉機葉輪、風箱及管道等部件進行防磨治理,必要時對排粉機進行找動平衡試驗。
(5)當磨煤機電流低於90A,經補加鋼球後,制粉出力提高不明顯,或補加鋼球周期明顯縮短時,必須對磨煤機進行鋼球篩選。
3、節能技改方面
(1)2010年針對#1爐#3磨應用新型小球技術,應用後對應磨煤機單耗降低,耗電量降低13%,但由於磨煤機出力降低,未進行推廣,目前該公司新型小球技術進一步提升,並配套研製台階型襯板,制粉出力提高約23%左右,鶴崗電廠立即組織調查研究,目前進行項目申報審批中。
(2)針對排粉機風門開度平均在40%左右,運行電流在65-70A之間,產生節流損失較大,考慮到排粉機台數多(8台)進行變頻或降速改造投資大,根據離心式風機相似性定律,對8台排粉機葉輪進行切削,葉片直徑由原來的2000mm切割掉150mm為1850mm,每個葉片切割掉75mm,根據葉輪和機殼間隙,對機殼內壁進行相應處理,改造後電流降低8-10A,耗電率降低0.15%。
(三)#1鍋爐節能增效綜合治理措施
目前機組入爐煤嚴重偏離設計工況,灰分較大,加上爐型設計和制粉、燃燒系統的設備問題及保溫、漏風問題,鍋爐仍存在制粉電耗高、滿負荷時引風機出力不足、排煙溫度高、主再熱汽溫偏低、空預器入口煙溫偏低等問題,嚴重影響機組運行經濟性。經西安熱工院診斷並提出建議,電廠確定在2012年的#1機組大修中對鍋爐進行節能增效綜合治理(具體分析及治理措施見附件一)。
目前,運行措施及檢修治理項目已全部完成,其中,將磨煤機出口溫度從70℃提高到75℃是合理可行;另外,所做的一次風調平試驗有效降低鍋爐尾部煙氣CO含量,改善了爐膛配風;技改項目在本次大修中完成。預計在蒸發量達到最大連續蒸發量(1021t/h)時,過、再熱汽溫可達到540℃,且過、再熱器減溫水量無明顯增加,鍋爐效率>92.5%(入爐煤熱值不低於16.44MJ/kg),最低穩燃負荷<50%B-MCR。
(四)冷端治理節能案例
1、真空泵工作液冷卻水改造
三台機組真空泵均為水環式真空泵,工作液溫度在15℃時,設計極限抽吸能力51 kg/h,而在夏季以及春秋季節時,其工作液冷卻水溫度均在20℃以上,最高達到33℃。此時,真空泵工作液溫度達到35-45℃,嚴重影響真空泵抽吸能力,電廠對真空泵冷卻水系統進行改造,將工業冷卻水(水溫10-15℃)接入對真空泵工作液進行冷卻,改造後,工作液溫度明顯降低,經測試春秋季節,機組真空提高約0.7kPa,夏季機組真空最高提高1.8kPa,為配合循環水泵優化運行,公司原則上規定每年真空泵工業冷卻水投入時間為4月15日-10月15日,該區間段機組真空平均提高約1.2kPa,煤耗降低約3g/kWh,同時延長了循泵優化運行時間。
2、一期300MW機組凝汽器改造
一期#1、2凝汽器為哈爾濱汽輪機廠輔機工程有限公司生產的N-15770型單背壓、單殼體、雙流程、表面式凝汽器。凝汽器採用冷卻塔循環供水冷卻方式,冷卻水系統配套兩台循環水泵,以滿足機組在不同季節和不同負荷時對冷卻水量的要求。凝汽器抽空氣系統配套兩台水環真空泵,機組正常運行時,一台運行,一台備用。凝汽器銅管由於產品本身質量及安裝中存在問題,易出現循環水泄漏、凝結水水質惡化現象,兩台凝汽器分別進行不同程度堵管,另外,機組經長周期運行管束出現不同程度腐蝕結垢,冷卻能力下降,凝汽器端差全年平均高達8℃以上,經專業技術人員全面考察、分析和論證,通過了進行凝汽器不鏽鋼管更換的改造方案,改造前後技術規範見附表:
改造前、後經西安熱工院性能考核試驗:
在相同工況條件下,改造後凝汽器壓力較改造前降低約1.838kPa,凝汽器冷卻水進口溫度30℃、冷卻水流量28162t/h下,凝汽器壓力為8.868kPa,達到並優於設計保證值(9.1kPa)。300MW負荷工況下凝結水過冷度為-0.217℃,低於設計保證值(0.5℃)。實際運行中凝汽器端差在1.5-3℃,低於集團公司規定的3.5℃優秀標準。
3、以合同能源管理方式實施一期300MW機組冷卻水塔改造
一期兩台水塔投運多年,由於設計冷卻面積小、材料老化等原因,冷卻效果很差。2011年按規定在80%負荷率以上測試水塔冷卻幅高達15℃左右,超標準值約8℃,造成汽輪機在該季節排汽壓力上升2.8kPa以上,供電煤耗上升約6.5g/kWh,嚴重影響機組經濟性。經診斷及檢查分析主要存在以下問題:
(1)淋水填料老化及破損程度嚴重,已達到其使用壽命。
(2)破碎填料常堆積在凝汽器水室以及冷卻管內,對機組的安全運行造成影響。
(3)噴嘴堵塞、損壞較多,淋水濺散的均勻性差,並且部分區域無法正常淋水。
(4)噴濺裝置脫落較多,冷卻塔內柱狀流水直接落下的區域較多。
(5)大部分除水器已損壞、失效。
(6)塔芯部件變形破損、堵塞,使冷卻塔的配風、配水極不均勻。
基於上述問題,電廠以合同能源管理方式與節能服務公司簽訂合同,在不改變槽式配水情況下,用雙斜波淋水填料、145-42除水器,反射III型噴濺裝置及I70玻璃鋼托架更換原有設備及部件,建設工期35天,目前兩台水塔已全部改造完畢,經改造後考核性試驗,#1水塔冷卻幅高為5.6℃,#2水塔冷卻幅高為5.1℃,比改造前降低接近10℃,低於標準值7℃在1℃以上。
4、二期600MW機組凝汽器抽空氣方式改造
電廠600MW機組為雙背壓凝汽式機組,抽氣裝置為串聯布置方式,即高壓凝汽器中的不凝結氣體連通到低壓凝汽器抽氣通道,與低壓凝汽器中的不凝結氣體混合後經真空泵抽出,2009年經熱工院專家診斷,低壓凝汽器汽側存在空氣聚集現象,同時由於機組真空嚴密性達到270Pa/min,說明空氣聚集是由於真空泵沒有及時抽出漏入的空氣造成。為此,電廠按照專家提出改造建議(見附圖)進行改造,改後經比較真空提高約0.37kPa。
建議真空系統連接方式
(五)一期#7低加疏水改造
一期300MW機組自投產後,就存在#7、#8低加疏水逐級自流不暢,導致低加危急疏水處於常開狀態,每小時約70噸左右65℃疏水直接進入凝汽器,致使一部分高品位熱能未合理利用,還導致凝汽器熱負荷增加,影響機組熱力循環經濟性。為解決該問題,經專業討論分析通過在#7低加正常疏水管道上增加一台管道變頻泵,布置在循環水泵坑內,將疏水導入#6低加入口凝結水管道(具體見附圖),改造後系統工作正常,由於凝結水泵已改為變頻運行,經統計改造後系統耗電率基本沒有變化,凝汽器熱負荷得到降低,經估算機組煤耗約降低0.69g/kWh,年節約標煤2000噸左右。
(六)落實300MW汽輪機組節能降耗實施導則中熱力系統改進措施,並對600MW機組進行有選擇改進
泵體放氣門低加導#8正常疏水調門疏水泵入口壓力真空表疏水泵電動門後壓力表疏水泵出口逆止門前壓力表疏水泵逆止門後放氣至凝汽器手動門疏水泵泵體放氣至凝汽器手動門疏水泵放氣至凝汽器總門循環水泵坑疏水泵出口電動門後管道注水放氣門電動閘閥,4.0疏水泵入口手動門疏水泵疏水泵出口逆止門疏水泵出口電動門低加出口至#6低加入口凝結水管道機#7低加正常疏水增加疏水泵米0.6米機循環水泵坑低加低加原設計熱力系統疏水閥門複雜、個數繁多,並普遍存在泄漏現象,不但使做功減少,還引起凝汽器熱負荷增加,真空下降,嚴重影響機組的經濟性。以#1機組為例,由於疏水閥門內漏較為嚴重,機組汽耗偏高,在270MW負荷以上時,備用凝結水泵經常聯起,不僅使機組煤耗增加,同時使機組耗電量增加,基於上述原因,並結合節能降耗實施導則,嚴格按照導則要求,分別對一期主、再熱蒸汽及旁路系統,汽輪機本體疏水,加熱器疏水及放空氣系統,軸封系統,凝水及小汽輪機蒸汽系統,給水系統疏水進行優化改進,並借鑒300MW機組導則,有選擇地對600MW機組熱力系統進行優化治理,均取得了明顯效果,尤其#1機組額定出力下,實現單台凝結水泵運行。
(七)一期2×300MW汽輪機組通流部分改造,並獲得國家財政獎勵資金1172萬元
一期兩台汽輪機型號為N300-16.7/537/537型、亞臨界一次中間再熱、單軸、雙缸、雙排汽凝氣式汽輪機,是20世紀80年代初哈爾濱汽輪機廠引進美國西屋公司製造技術並改進設計製造的早期產品(老73型)。機組投產後,存在的普遍問題是各項經濟指標未能達到預期的設計性能,汽輪機出力存在不足,各監視段均不同程度存在超溫超壓現象,其中,2、3段抽汽溫度超設計值30℃左右,5、6段抽汽溫度超設計50℃以上,三缸效率低於設計值4%以上,高、中壓過橋汽封漏汽量超標嚴重。機組實際熱耗率為8442kJ/kWh,比設計值高出461kK/kWh,影響煤耗升高18.56g/KWh。
本次通流改造的主要內容為將汽輪機通流部分中高壓進汽結構(含一段抽汽)改造;高壓內缸改造;高、中壓缸的夾層冷卻蒸汽系統改造;高壓缸通流改造;中壓缸通流改造;低壓缸通流改造;低壓5、6段抽汽溫度偏高治理;1-6號調節閥順序改變;高壓外缸改造、高、中壓缸和低壓缸端部汽封更換為新型高效汽封,整個系統的工藝流程不發生變化,與改造前相同。其生產能力增加5%,即機組的額定功率由300MW增加到315MW。
本項目實際完成投資5616.5萬元,項目改造完成後,經西安熱工院熱力性能試驗,汽輪機熱耗率分別為7977.2kJ/kWh、7959.1kJ/kWh,分別比改造前降低432.8kJ/kWh、629.7kJ/kWh,每年可節省標煤58464噸,年降低燃料成本3500萬元,並獲得國家節能改造財政獎勵資金1172萬元。
(八)廠用輔助蒸汽系統優化運行及改造
鶴崗地區冬季較為寒冷,冬季採暖用汽量較大,以一期中南設計院為例,電廠採暖供汽汽源設計分別由二段、四段、五段抽汽供給。但在實際運行中,由於各種因素影響,除熱水採暖外基本為二段抽汽供給。其中,保守估計採暖期有三個月(12、1、2月)供汽量在130t/h左右,其餘三個月一般在30-50t/h,整個採暖期供汽量平均在80t/h左右。根據等效焓降法,用四段抽汽取代二抽供汽,按兩台300MW機組運行,供汽量80t/h計算,汽輪機效率提高0.84%,對應煤耗降低2.65g/kWh。另外,蒸汽採暖一般利用飽和蒸汽的汽化潛熱,理論上應採用飽和蒸汽即可,為此,通過合理控制供汽參數(維持供汽壓力不變,通過減溫水裝置控制供汽溫度160-180℃),在同樣換熱效果下,全廠供汽量約降低7t/h,對應煤耗約降低1.6g/kWh,即通過合理調整採暖供汽汽源,合理控制供汽溫度,冬季機組煤耗約降低1.6+2.65=4.25g/kWh。電廠在2012年對各採暖供汽聯箱減溫裝置進行治理或改造,主廠房採暖聯箱增加一路五抽汽源,由擴建端低輔母管接入,討論和制定四抽取代二抽汽源切換方案,並於採暖期落實實施,實現採暖汽源合理應用,採暖供汽參數得到合理控制,而且採暖回水溫度由100℃以上降到80℃左右。
點擊展開全文

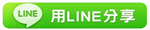
※2017中國國際電力節能環保低碳論壇開始徵文了
※文一波:給年輕創業者的七句箴言
※脫硫島煙氣餘熱回收及風機運行優化技術
※全面解析鍋爐各系統
※高含鹽廢水零排放——蒸髮結晶技術
TAG:電力節能環保服務平台 |