超細長鈦合金梁的數控加工工藝
圖1為超細長鈦合金梁類零件。其毛料為模鍛件,材料牌號TA15M,毛料外廓尺寸3500mm×210mm×180mm,毛料重量220.5kg。零件外廓尺寸3450mm×160mm×151mm,最寬處為151mm,最窄處僅為34mm。零件外形為複雜雙曲面,雙面槽腔,緣條與腹板厚度最小處僅為2mm。尺寸精度及表面質量要求較高。
圖1 零件模型
1 確定工藝方案
零件毛料為TA15M自由鍛件,鍛件殘餘應力導致了機加過程中零件的變形。零件超長且窄,長寬比範圍22.8-101.5。零件結構面多為變角度曲面,所有緣條都為斜面,裝夾定位不可靠。緣條和腹板厚度薄,最小處2mm,公差±0.2mm。緣條較高,角度大,最高處96mm。零件的裝配關係複雜,在該梁每一個位置都有零件與之裝配。表面質量要求高,所有轉角及底角粗糙度1.6μm。該零件結構屬於工藝性極差的結構類型。在加工中要解決的問題包括:機加過程中變形的控制、裝夾定位方式的選擇和縮短加工周期。
(1)零件定位方式
超細長鈦合金梁在加工過程中,定位方式的選擇至關重要。該梁長又細,且為兩面槽結構,因此採用緣條定位。由於該零件採用斜緣條直接定位會大幅降低定位面的精度,對零件加工質量影響很大,所以在緣條上設置工藝凸台來進行定位,既可以保證定位基準精度,又可以避免在加工過程中頻繁的倒壓板工作。工藝凸台的距離應適當,如果太近會增加加工過程中的跳刀頻率,加大工藝凸台的去除難度;工藝凸台太遠會使定位不穩定,增加零件在機加過程中的變形幾率,降低定位準確度。根據該梁的結構特點,採用階梯工藝凸台,再在梁身上鑽兩工藝孔聯合定位,孔徑分別為25H9、12H9,定位穩定可靠。工藝凸台外形如圖2所示。
圖2 工藝凸台外形
(2)機床設備及工裝的選擇
超細長鈦合金梁加工採用緣條高工藝凸台及梁身基準孔定位方式。頭部採用輔助可調支撐,用於頭部變形量的校正以及加工中變形量的去除;壓板選用Z字形壓板,可以有效降低刀具長度,避免機床與工裝的干涉,並且提高加工效率,保證零件加工後的表面粗糙度;工裝增加校驗塊的使用,用於加工中程序的驗證,以及避免工人由於用錯刀具造成的零件超差及廢品,提高了產品加工的一次就成功概率。正反面加工各需一套工裝。
超細長鈦合金梁緣條兩側的導孔接近300個,如採用傳統方法,常規加工難度非常大,費時費力,產品質量也不易保證。使用數控機床鑽導孔,既省時省力,又能保證產品質量。採用數控鑽導孔需工裝要求較高。緣條兩側各一套。
(3)確定加工流程
加工流程的合理安排是零件生產研製的重要環節,加工流程的合理與否是導致零件加工變形的重要原因。加工流程的順序直接決定零件的去量方式、去量大小和去量先後順序,這些都會影響零件材料的應力釋放,以及零件的變形大小、變形方式。合理的加工流程可以大幅降低零件的變形幾率。加工流程不僅要考慮零件的變形因素,還要保證零件尺寸精度。
根據超細長鈦合金梁的零件特點,制定零件的加工流程:模鍛件來料—銑基準面—鏜基準孔—粗銑航後面(留7mm餘量)—粗銑航前面(留7mm餘量)—粗銑航前面(留3mm餘量)—粗銑航後面(留3mm餘量)—粗銑槽一側(留3mm餘量)—粗銑槽另一側(留3mm餘量)—測量外形及槽口—半精銑外形(留1mm餘量)—半精銑航前面(留1mm餘量)—半精銑航後面(留1mm餘量)—測量外形及交點孔—精銑槽口—精銑外形—測量外形及槽口—精銑航前內形—精銑航後內形—測量孔位等—數控鑽緣條導孔—銑工藝凸台—鉗工鑽筋條導孔—半檢—清洗—熒光檢驗—吹砂—標識—成檢—交付。通過多次不斷的翻面加工以及去量的逐漸遞減,有效消除零件變形,保證產品質量。
(4)刀具的選擇及參數的確定
數控加工機床採用冷卻液冷卻,結合零件的鈦合金材料,應以淺切刀具和整體合金直柄立銑刀為主,國產鑲齒合金刀具為輔。由於鈦合金屬於難加工材料,對刀具的質量和性能要求都很高。
依據現有參數庫及零件的實際加工情況來確定刀具加工參數。在切削中主要的切削參數有:主軸轉速n、切削深度ap、切削寬度ae、每齒進給量fz、刀具齒數Z和進給速度vf,其中vf=nZfz。
鈦合金加工刀具的齒數一般是多齒刀具,在加工該零件選用的刀具絕大多數都是4齒刀具。影響刀具加工效率的主要參數是主軸轉數(n)和刀具每齒進給量(fz)。表1為參與加工的主要刀具的規格及加工參數。
表1 加工刀具選擇及切削參數數值
2 數控程序的編製
根據零件的變形控制、來料狀態、零件結構特點、機床特性、刀具特點等,編製數控加工程序。在編製程序時需有效避免一些常見的問題:避免刀具路徑冗餘,減少不必要的跳刀;盡量採取順銑的走刀方式,保證零件尺寸精度;針對不同的餘量,採取徑向以及軸向的分層加工,保證刀具切削餘量均勻,降低機床及刀具的損耗;避免刀具垂直與零件接觸;在轉角要降低加工速度,普通轉角降速值是正常切削的60%,特殊轉角(例如工藝凸台內側筋條轉角)降速要達到20%。保證無人工干預的正常切削;精加工前清轉角,保證精銑的銑切量均勻;正確計算R退縮值。
程序的走刀方式也可以影響零件的變形,比如淺切、順銑等都可以大幅降低零件的變形量。淺切加工不僅可以大幅提高金屬去除率,更重要的是可以降低切削力、減少加工應力,有利於減小零件加工中的變形,同時還可以降低機床負荷、保護數控機床。淺切使用的專用的加工刀具,該類型刀具加工效率較高,以D20R4刀具為例,進給速度可達1432mm/min,相比普通的刀具粗銑進給速度60mm/min,效率可以高出幾倍甚至十幾倍。淺切加工特別適合超細長鈦合金梁的粗加工。
選用「roughing」命令編製淺切程序,在半精加工和精加工過程中採用徑向分層的方式,每層進量0.5,在保證零件精度的前提下,可以大幅降低切削應力,減小零件的變形量。
小結
制定一套合理的工藝方案適用於超細長鈦合金梁類零件,通過應力釋放、優化切削方式與合理刀具參數等方法有效控制了零件變形,採用工藝凸台定位的方式也起到了很好的定位效果。該方案已通過加工驗證,在實際加工中取得了非常好的效果,最終生產出了合格的零件,加工過程穩定,產品質量合格。
原載《工具技術》 作者:孫麗敏

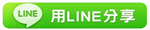
TAG:工具技術 |