分葯器數控加工刀具應用技術
作者:孫長勝
單位:航天三院31所
來源:《金屬加工(冷加工)》2017年第5期
在「中國製造2025」大環境的帶動下,數控加工、智能製造技術將會風起雲湧,高速發展,帶我們進入一個高度智能化、自動化的世界,而數控刀具應用技術作為一門基礎技術,也將迎來高度的發展。目前刀具廠家日益繁多,我們已不再盲目追求進口的刀具品牌,在大量的試驗和實際應用案例中,國產刀具已給了我們足夠的驚喜和震撼人心的加工效果。
1.工件特點
分葯器(見圖1)由上端蓋和基座兩部分組成,由φ8mm圓柱銷聯接,通過端蓋靈活的開合,可以實現將不同大小的藥片均勻地一分為二,同時具備將藥片碾成粉末的效果,解決了日常生活中因藥片過大、不便分割和碾碎成粉末的難題。
圖1
2.加工難點
(1)曲面的加工。常用加工自由曲面的刀具主要有平底立銑刀、球頭銑刀、錐柄立銑刀、小刀桿球頭銑刀及環底銑刀等,如圖2所示。
圖 2
為了分析方便,根據刀具的特點,可以簡單地把加工自由曲面的刀具類型分為兩類: 平底立銑刀和球頭立銑刀(環底銑刀介於二者之間)。
球頭立銑刀在曲面的數控加工中應用最普遍,它的底部為球形,切削過程中,切削刃和工件的接觸面的法線始終通過刀具的中心,使得刀具的行距計算與避免干涉的計算簡單化,因此,球頭刀的編程和使用比較方便,並且球頭刀對加工對象的適應能力很強。但球頭刀加工也存在不足之處,由於球頭刀切削刃上各點的切削情況不一,越接近球頭刀的底部切削條件越差,如容屑空間小、底部切削效率低及切削速度不恆定等。正是這些缺險導致了球頭刀具易磨損、加工效率與表面質量難以進步,另外,球頭刀加工時的走刀行距一般比相同直徑的平底立銑刀加工時的行距小,相比之下加工效率較低。
圖3
平底立銑刀是平面銑削的主要刀具。在多軸加工中,可以通過控制刀軸的傾角來對曲面進行加工,獲得較大的有效半徑。在滿足相同殘留高度要求的條件下,可以採用較大的行距加工,從而減少走刀次數,進步加工效率。此外,它的切削條件好,能夠保證切削速度的穩定性和容屑空間。它的缺點是數學模型複雜、刀具軌跡及干涉運算複雜。
綜上所述,平底立銑刀較球頭立銑刀在曲面五軸加工中具有非常大優勢,在曲面加工及編程時,應首先考慮使用球頭立銑刀。本次加工採用φ10mm球頭銑刀加工,行距0.2mm,轉速6 000r/min,進給f=1 500mm/min。
(2)分葯器上端蓋深槽的數控加工及刀具應用技術。分層銑削工件輪廓深槽時(見圖4),要用最短的時間切除工件大部分餘量。但當工件X、Y向或Z向有較大餘量,受工藝系統剛度和強度限制,刀具不可能一次走刀就切削完成該向餘量,應根據工藝系統剛度和強度的實際情況分成多次切削。如當工件表面有硬皮第一刀銑削時,應吃刀量宜大些以避開硬層。輪廓是否分層切削還取決於工件的表面質量要求。當工件上要求的表面粗糙度值Ra=6.3~3.2μm時,可分粗、精銑兩次加工,粗銑留有0.5~1mm的餘量給精加工。當工件上要求的表面粗糙度值Ra=1.6~0.8μm時,可分粗、半精、精銑三次加工,精加工餘量0.5mm,半精加工餘量1.5~2mm。
圖4
本次選用φ10mm整體合金硬質銑刀,由於z向餘量較大,採用分層加工,z向分2mm一層,輪廓方向精加工餘量0.2mm,底面精加工餘量0.2mm,轉速4 500r/min,進給f=800mm/min。
(3)分葯器底座的M30X1.5螺紋孔銑削加工及刀具應用技術。當螺紋孔的直徑較大時,採用螺紋銑刀加工,獲得較好的加工質量和較高的加工效率。螺紋銑刀有單齒刀和螺紋梳刀兩種,梳刀相對與單齒有著更高的加工效率。螺紋梳刀又有刀片式和整體式的區別。本次加工採用整體式螺紋梳刀(見圖5),這種刀具專門用於內螺紋的加工,最小加工直徑10mm,也就是說只要螺距不變,這種螺紋銑刀可以加工更大直徑的螺紋孔。而且不用考慮退刀槽的影響。
圖 5
M30X1.5螺紋銑削,西門子828D手工編程銑削螺紋示例:
G01 X0 Y0 Z1.5 F2000
G01 Y =15-R1 F1000
G03 X0 Y0 Z-9 I=0 J=R1-15 TURN=6
G01 Y0
G01 Z100….
(R1為螺紋梳刀的半徑)
3.工序設計
分葯器由底座和端蓋兩部分組成,材料分別是45鋼和2AL12鋁,加工時分成兩道工序,共九個工步。主要從刀具使用情況和工件配合要求兩方面考慮,先安排加工底座,再加工端蓋,底座的加工共分為四次裝夾,端蓋的加工分為五次裝夾。
在配合精度較高的部分採用雷尼紹在線測量系統,其測量精度在0.005mm以內,保證了配合部分的精度。曲面採用粗精加工分開的工序安排,既保證了較高的生產效率,也得到了較高的表面質量。
4.刀具選用
在選用過程中,安排了進口品牌的刀具和國產刀具的參數對比,主力刀具還是國產刀具。某國產品牌的φ10mm整體硬質合金刀具在n=5000r/min、f=1500mm/min、ap=8mm、ep=5mm的切削參數下,連續切削時間超越某著名進口品牌,而且刀具價格懸殊。國產刀具製造技術和刀具材料技術的提升,為我們降低生產成本帶來更多的選擇。
加工過程共需要13把刀具,如附表所示。其中,最小的刀具直徑只有1.8mm。
5.加工過程
(1)底座的加工共需要4次裝夾,具體步驟如下:
工步1(見圖6):①採用φ10mm整體硬質合金銑刀加工外形上的2個R20mm圓弧。②採用φ16mm端面銑刀加工M30螺紋孔底孔。③採用φ10mm整體硬質合金螺紋梳刀加工2個M30螺紋。④採用φ6mm整體硬質合金銑刀加工φ6mm孔和90°夾角圓弧槽。⑤採用φ1.8mm整體硬質合金銑刀加工寬2mm、深6mm通槽。⑥採用φ10mm整體硬質合金球頭銑刀加工30°斜面。⑦採用φ10mm NC點鑽加工各倒角。
圖6
工步2(見圖7):①採用φ16mm端面銑刀加工2個15mm寬度。②採用φ10mmNC點鑽加工各倒角。
工步3(見圖8):①採用φ7.8mm鑽頭打通兩個底孔。②採用φ10mmNC點鑽加工各倒角。③採用φ8mm鉸刀,一次絞通兩個孔。
圖7
圖8
工步4(見圖9):①採用φ16mm端面銑刀去除粗加工餘量。②採用φ6mm整體硬質合金螺紋梳銑刀,加工兩個2mm後立板外輪廓。③採用φ10mm整體硬質合金銑刀加工2個φ10mm孔和φ10mm孔。④採用φ10mm整體硬質合金球頭銑刀加工立板斜面。⑤採用φ10mm NC點鑽加工各倒角。
圖9
(2)上端蓋的加工共需要5次裝夾,具體步驟如下。
工步1(見圖10):採用φ16mm整體硬質合金銑刀加工外輪廓。
圖10
工步2(見圖11):①採用φ25端面銑刀去除上表面餘量,並粗加工φ15mm圓柱凸台。②採用φ10mm整體硬質合金銑刀精加工φ15mm圓柱凸台,並加工60mm×70mm方槽,加工兩連接孔處R7mm圓弧面。③採用φ10mm整體硬質合金球頭銑刀加工刃口斜面。④採用φ10mm NC點鑽加工各倒角。
圖11
工步3(見圖12):①採用φ25mm端面銑刀去除兩連接孔。②採用φ10mm整體硬質合金銑刀精加工中間部位的餘量。
工步4(見圖13):①採用φ7.8mm鑽頭鑽通兩個底孔。②採用φ8mm鉸刀,一次絞通兩個孔,保證兩處寬15mm的尺寸。
圖12
圖13
工步5(見圖14):①採用φ10mm整體硬質合金球頭銑刀加工圓弧面。②採用φ4mm刻字刀刻字。
圖14
6.結語
以「中國製造2025」為契機,以國家的戰略需求和國民經濟的市場需求為導向,以提高我國製造裝備業綜合競爭能力和產業化水平為目標,重點解決數控刀具的材料應用,提高生產效率及加工質量,贏得市場。最後衷心希望我國數控技術和刀具材料等技術的發展不斷完善,不斷提高,更加有效合理地適應實際生產的需求,更高效地提高生產率。

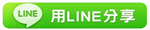
TAG:機工刀具世界 |