淺談塑料機械工業4.0的現狀和金緯公司關於智能製造的投入進展
關於工業4.0,《中國塑機》有幸採訪到上海金緯公司副總工程師、2017年中國好塑才科技英才獎得主許勇先生,下面與大家分享許工對工業4.0的見解。
1、金緯是如何看待工業4.0?
許:我認為「工業4.0」,是工業電氣化、自動化、數字化、智能化的結合體,缺一不可。我國早在十二五計劃就提出工業化和信息化的兩化融合,並在十三五計劃中重點強調了智能製造,與德國提出的工業4.0概念基本趨於一致。
所以我認為智能製造的核心是利用現代物聯網、大數據、雲計算為手段,基於海量數據的建模分析,形成智能決策與動態優化,同時整合分布於全球的設計、生產、供應鏈、銷售等各種資源協同製造和創新,不僅滿足全球用戶的標準化需求,也能通過靈活的生產製造設計,滿足全球用戶個性化定製需求。同時智能工廠對產品的全生命周期進行跟蹤維護,深度挖掘數據,推動產品的快速再創新與再發展。
我以塑料機械公司的智能製造為例,給大家簡單描述一下:
訂單生成後,根據MES系統的分工規劃,將訂單協議下傳到相關的技術部,技術部設計好圖紙,通過建模模擬調試,確認無誤後,生成BOM表和數控加工程序,BOM表中採購件與外協件自動傳到採購部。
自製件圖紙生成加工程序直接下傳到數控機床伺服器計算中心,由伺服器根據機床的在線情況和OEE數據分析,來分配給加工機床的流水線,機床與機床之間的搬運和工件的碼垛都由機器人來完成。
需要電鍍、熱處理的零件通過AGV小車運到外協加工出口區域,完工的零件放在裝配出口區域等待AGV小車運到由生產廠長指定的裝配區域。
採購部的伺服器與外協廠家、供應商廠家是互聯互通的,因為每年與這些供應商都簽訂了供貨協議。BOM表中的零部件自動分配到各個廠家的數據伺服器中,按照MES系統中的計劃時間,通過各種智能物流輸送到工廠的裝配區域,公司倉庫做到零庫存。只需在售後服務部有備品備件的倉庫,且這個倉庫的數據共享給全球用戶的。
通過一系列裝配工序,完美的機器來到了地球上,最後到整機帶載調試,這時機器進入了公司的PLM(全生命周期管理)系統,系統將對機器進行終生在線維護,並且將設備的運行和維護數據保存到歷史資料庫,供設計部深度分析這些數據,從而不斷改進創新,提升產品的品質。
員工的工時將通過車間每個工序的終端機上確認後,員工每天、每月、每年的工時都可以在車間的電子看板系統查詢,生產廠長可以通過總訂單生產負荷的查詢,可以及時發現哪道工序比較堵塞,哪些工序比較寬鬆,並對各個工序進行動態調配。
公司的EMS(能源管理系統)系統將每天消耗的水、電、氣與上面提到電子看板系統中工人的工時數據和採購數據實時上傳到ERP系統供財務部使用。
公司的銷售部的技術配置伺服器存儲了許多模塊化的配置方案,銷售員只要將配置組合一下,並與ERP互通,就可計算出設備的製造成本和對外的銷售價格。銷售員可用各種電子終端通過公司雲平台就可獲取這些數據,同時也能查看到在產訂單的進度情況和開展多方視頻會議,也可把用戶的需求通過電子終端上傳到公司的設計開發部,然後將可行性方案及時反饋給用戶。
公司的非一線生產員工,比如售後服務工程師、銷售員等等,實行任務式管理---即只要完成公司在規定的時間內指派的任務和銷售目標。他們手機中只需安裝工作APP,在工作時間打開就可以了,公司通過GIS管理系統就知道他們在全球的每一個地方。不需要朝九傾巢而出,晚五傾巢而歸。現在高峰期無法解決的擁堵問題,到那時或許就解決了。
公司的一線工人的上班通過人臉識別或者帶有RFID感測的工卡識別,並將數據連接到ERP中。屆時,時間成本將成為產品的重要成本,交貨時間將納入企業的徵信系統,銀行成為第三方的服務平台來保障買賣雙方的金融風險。
最終所有的智能工廠都融入到物聯網中。
設備上諸如電機、驅動器等關鍵零部件成為設備物聯網中的一個元素,每台設備又成為企業物聯網中的一個元素,每個企業成為行業物聯網中的一個元素,每個行業成為國家物聯網中的一個元素,每個國家將來成為全球物聯網中的一個元素。各個元素之間又可互聯互通,整個物聯網路呈現一個扁平化的架構模式。
2、國內與國外同行在擠出機方面有哪些不足?金緯是如何應對的?
許:我們與國外發達國家的擠出設備,比如德國巴頓菲兒、克勞斯瑪菲、奧地利辛辛那提、義大利Bausano等等相比,國外設備比較耐用一些,第一主要是他們的基礎材料工業比較發達。
第二,他們的控制系統比較複雜一點,除了符合嚴格的CE與UL標準以外,採用的HMI(人機界面)與控制軟體基本都有SCADA的功能,比如倍加萊的阿波羅監控軟體,西門子wincc監控等。SCADA(Supervisory Control And DataAcquisition)系統,即數據採集與監視控制系統,它具有實時資料庫、關係資料庫。具備有SCADA後,上層的MES、ERP系統才能與它對接訪問數據。
我們國內設備比如金緯公司、仕城公司、恆瑞公司等國內所有的機械設備廠,大部分電氣控制系統基於成本考慮,都沒有配置SCADA監控軟體。但也不是說不能夠採集控制數據,現在市場上為了解決這個問題,許多電氣公司推出了各種各樣的串口網關來採集數據,但我認為只是為了解決目前存量設備的數據採集,串口協議速度較慢,不符合未來工業4.0的大數據採集介面標準,也只是權宜之計。
目前,不管是國內設備廠家,還是國外設備廠家都沒有做到設備的數據開放,這對推進數字化工廠的進程是比較困難的。後面會談到我們機械加工廠實施數字化工廠所遇到的瓶頸。
怎麼說呢?就是你的設備介面不是標準的,你的每個數據變數的含義不告訴用戶,用戶怎麼能夠將你的設備融合到他的智能工廠里去呢?所以,我希望大家今後一定要引導和提升客戶的需求:(1)在設備的電氣控制系統上要麼配上SCADA系統,要麼選擇帶有乙太網口的PLC和HMI,加上帶有TCP/IP或OPC介面的智能網關;(2)生產線的控制要實現全集成自動化,不能是由多個設備廠家拼湊起來的離散控制,在資料檔案中一定要說明程序控制其中每個變數的地址與含義。
只有具備以上兩個基本條件,設備的運行信息才有可能夠方便用戶快速而實時的上傳到MES系統當中,做到自動化與信息化的融合。
我深耕塑機製造行業16年,很清楚生產製造效率有很大的提升空間,我們製造的每個工序都是靠人去統籌安排的,我們的高管只看到不是很精準的ERP數據,看不到準確的生產流程數據,每個工序基本靠人去喊,如果人再把七情六慾、喜怒哀樂等各種關係和情緒帶到工作中去,可想而知,生產的效率,產品的質量怎麼能精準控制,所以未來智能製造一定會成為現代企業的迫切需求。
智能工廠既要成為新一代智能化生產技術的使用者和受益者,同時也成為先進工業生產技術的創造者和供應者。這是什麼意思呢?就以我們金緯公司來講,公司是生產塑料擠出機械的,公司本身的生產製造要向智能化方向發展。另外我們生產的各種設備要能夠融入到全球用戶的智能工廠體系中去。
這兩項工作我們是如何推進的呢?第一項,2017年我們在蘇州公司試點了MES(可製造執行系統)系統。剛才前面講了,設備數據不開放,沒有辦法做到兩化融合。我們蘇州金緯公司自成立以來陸陸續續採購了數百台的數控機床,來自可能數十個廠家,這些機床有的沒有標準的採集介面,有的只是串列介面,需要上游軟體公司開發通訊協議,有的通訊協議完全不開放。
所有的機床廠家沒有提供變數表(因為多年前用戶沒有要求,廠家也未意識到)。這樣,數百台機床的數據連接到MES系統變得非常困難。我想這是個瓶頸,這是所有機械製造企業的共同難題,也將大大阻礙機械製造企業實現智能製造數字化工廠的前進步伐。
我們現在只好暫且將機加工作為產品的一個工序來對待,然後將生產計劃排表,計劃裝配工序工時,實時生產狀態的查詢與統計,電子看板系統,手機APP的查詢終端,並與公司的ERP(企業資源管理)進行數據對接。
第二項工作其實早在2015年,公司就建立了設備PLM(全生命周期管理)的物聯網雲平台。通過對設備的運行實時檢測,進行遠程維護、故障預測與排查、設備檔案管理、視頻查看,引入了設備與調試人員的GPS技術,也可以將數據上傳到用戶的智能製造系統中去。
這些年,我們的用戶在設備的數據和運行的安全上有很大的顧慮,為了打消顧慮,我們不僅在軟體上走VPN安全通道,經過工業防火牆,同時在智能盒子上還設計了一個安全門電路,只有用戶打開門,金緯物聯網雲平台才能讀取數據。
從2018年起,公司為了響應國家2025智能製造的戰略目標,在新設備上計劃淘汰所有不帶大數據介面的程序控制器,全部換成帶有TCP/IP介面的程序控制器,人機界面(圖f)。根據用戶的需求,加裝萬能通訊協議盒子(圖g)。
未來幾年,除了上面開發的生產監控、生產管理、設備管理、訂單管理、人員管理、看板系統等模塊外,我們還要開發能源管理、成本管理、效率管理等模塊,並且與公司的ERP系統對接,然後再與合作企業倉庫數據,物流信息的數據進行對接。(來源:上海金緯公司副總工程師、2017年中國好塑才----科技英才獎得主 許勇先生)

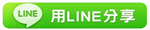
TAG:機械 |