基於數字化製造的某肋緣條高效加工技術研究
海軍駐瀋陽地區航空軍事代表室王偉
中航工業瀋陽飛機工業集團有限公司張 殊 王金海 孫國雁
《金屬加工(冷加工)》2017年第4期
某項目肋部緣條類零件屬於某傳動機構,緣條連接著兩側接頭與中間腹板,它們經焊接處理後共同組成了盒體機構。此機構連接著牆和大壁板,為主要的承力結構件。緣條上的理論形面直接與蒙皮貼合,緣條外形面的加工精度直接影響理論氣動外形的精度;緣條耳片則是整個盒體機構的主要承力單元,緣條耳片孔鎖緊後,通過剪切應力的受力方式承受著幾乎所有傳遞來的載荷。
所以,緣條類零件的加工質量關乎整架飛機的飛行安全性。而該類緣條在每架份飛機上有16~20個,數量大、生產周期長,如何在保證加工質量的前提下實現高效率的生產,成為該系列機型急需攻關的重點項目。
一、零件結構與加工工藝性分析
該緣條零件是某項目肋組件的重要受力構件之一,具有安全傳遞載荷和實現各部位連接之功用。其零件形狀較為複雜,帶有理論外形面,耳片間距小,耳片孔同軸度要求高。緣條類零件結構為大尺寸多型面結構,毛料狀態為B類狀態模鍛件,其典型結構如圖1所示。
1、零件毛料分析
料為B類狀態鈦合金模鍛件,單邊均勻餘量4mm,材料為高強度鈦合金,退火狀態。毛料外廓尺寸為900mm×300mm×65mm,毛料質量為23.2kg。
2、鈦合金材料特性分析
在航空領域廣泛應用的鈦合金可分為3種:α鈦合金、β鈦合金和α+β鈦合金。α+β鈦合金由α和β雙相組成,這類合金組織穩定,有較好的高溫變形性能、韌性和塑性,可以通過淬火、時效處理等使其組織結構得以強化。
鈦合金有如下特點:①高強度(σb=62~148kg/mm2),低密度(ρ=4.5×103kg/m3)。②熱強度高,溫度在400℃左右時,強度是鋁合金的9~11倍。 ③工藝性差。鈦合金材料硬度大,導熱係數低,加工時容易產生很大的熱量,使其工藝性大大降低。④耐腐蝕性好。
3、零件結構特點
零件外廓尺寸為800mm×261mm×108mm,按三維數模製造。零件一側為翼面理論外形面,開有下陷槽腔。另一面為開敞槽腔結構,筋條高度由5.6~19.0mm漸變。耳片直徑為24mm,耳片間距為32mm,耳片厚度及耳片槽口尺寸為關鍵尺寸,公差範圍為0.2mm。腹板厚度為3.8mm,底角為R4mm,最小轉角為R4mm。
4、加工難點分析
①產量要求高,加工效率難以滿足當前產量要求。
②理論形面各處曲率難以保證。
③後續零件需進行焊接,焊接狀態不可控,破壞機加形位尺寸。
④耳片孔邊距以及耳片孔同軸度難以保證。
二、加工方案分析及技術關鍵點突破
結合以上加工難點,若想實現緣條類零件的數字化高效加工,則必須突破以下關鍵點:鈦合金高速銑削技術、轉角處理技術、工藝裝備輔助定位、預留機加餘量以及進刀宏指令控制方法。
鈦合金緣條類零件數字化高效加工技術旨在通過合理高效的數控加工編程方法,融合鈦合金高效加工思想,選擇合理的加工參數和高效刀具,設計出一套工藝方法合理、機床利用率高且產品質量穩定的高效加工方案,並進行實際的生產來驗證。在此基礎上構建了鈦合金緣條類零件加工流程,該方案由以下4個方面組成。
1、鈦合金高效銑削技術
利用先進的編程技術,綜合考慮機床利用率、刀具磨損情況等因素,力爭實現最高效的鈦合金銑削方案。衡量銑削是否高效的重要指標就是金屬去除率,即單位時間內去除金屬的體積,用Q表示,可按下式計算
Q=ae·ap·vf(1)
式中,Q為金屬去除率(mm3/min);ae為徑向切削深度(mm);ap為軸向切削深度(mm);vf為進給速度(mm/min)。
切削加工中,金屬去除率與切削用量三要素ae、ap和vf均保持線性關係,其中任一參數增大一倍,都可使金屬去除率提高一倍。然而由於刀具壽命的制約,當任一參數增大時,其他二參數必須減小。為達到高效銑削的目的,選擇切削用量時需遵循一定的原則:①粗加工時,選用較小的進給速度以及較大的軸向切削深度和徑向切削深度。②精加工時,選用較大的進給速度、較大的軸向切削深度和較小的徑向切削深度(一般為0.5~2.0mm)。③加工外形時採用徑向分層,即取較大的軸向切削深度,銑內形時採用軸向分層。
通過大量零件的切削加工及刀具加工試驗,獲得了較理想的切削用量,數據如表1、表2和表3所示。
表1φ40mm和φ50mm立銑刀的切削參數
表2φ19R3立銑刀的切削參數
表3φ30R15立銑刀的行切切削參數
2、轉角處理技術
在銑削槽腔結構或帶有筋條側壁結構時,由於粗加工使用的刀具直徑較大,而精加工時根據轉角半徑選用較小直徑的刀具,這樣就勢必會造成轉角處切削量大的情況,使精加工餘量不均勻,造成折刀、崩刃現象,嚴重影響產品質量。
目前解決此問題的方案主要有:
①轉角減速處理。
②插銑後輪廓切削。
③軸向分層輪廓切削。
應用轉角減速方法時應注意:
①使用轉角減速需要考慮粗加工刀具的直徑以及精加工刀具直徑的大小及底R,這些涉及到在轉接R處需要採用哪種方式進行精加工,或進行幾次加工去處餘量。如果前一把刀具的直徑較大,後一把刀具的直徑較小,可能需要多次加工才能去除轉角處餘量;或者轉角的角度較小,也需要進行多次加工。
②轉角減速時需計算減速前後的距離,準確的計算既可以節省不必要的加工時間、提高加工效率,又可以避免因減速距離過短而帶來的刀具磨損所導致的加工質量不好。轉角減速距離計算示意圖如圖2所示,公式總結如下
(2)
式中,L為轉角減速距離(mm);α為轉角兩側側壁之間的角度(°);r為精加工使用的刀具半徑(mm);R為粗加工使用的刀具半徑(mm);m為粗加工預留餘量(mm)。
某緣條類零件的轉角採用插銑方式,該方法不同於前兩種轉角處理的方式,它是通過機床沿著刀具的軸向切入零件毛坯,類似於鑽削的一種加工方法,插銑轉角刀路如圖3所示。
常規的側刃銑加工方法,刀桿部分受力主要是徑向力,隨著刀具長度的增加,刀桿部分受到的彎曲力矩越來越大,對刀桿材料的要求也越來越高,即使採用硬質合金材料、超長的刀桿,也易使螺旋銑刀發生振顫。由於插銑加工時徑向切削力較低,由傳統加工方法的徑向切削,變為刀具的軸向切削,刀桿承受軸向載荷的能力要遠強於徑向。由於插銑切削麵積小於側刃銑,加工過程中的切削力也明顯地減小,所以轉角採用插銑方式一般不會出現刀具折斷或掉刀現象。
3、定位方式及狀態協調
由於緣條類零件正反兩面為雙曲面形狀,其中一面是理論外形面,所以零件本身並無合適的定位基準以及加工基準。現應用工藝凸台輔助定位技術,在零件兩側預留出工藝凸台,以「一面兩孔」的定位方式(將定位銷孔預留在兩側凸台上),實現緣條類零件翼面一側的加工定位。
而對於非翼面一側的加工,則申請了專用工裝作為輔助定位裝置,這樣加工非翼面一側時可以保證側翼面與工裝的貼合程度好,工藝系統剛度高,有利於提高切削參數和保證加工質量。定位方式如圖4所示。
由於緣條類零件在機加工序完成後,需要進行熱處理和焊接工序,故變形量和變形狀態比較難以控制,所以就涉及到與其他專業協調狀態的問題。比如,緣條與接頭對合處的焊條厚度預留0.3mm餘量,保證後續焊接對合精度。
耳片外圓翼面一側預留0.75mm餘量,非翼面一側預留0.5mm餘量,這樣可以保證變形後耳片孔邊距仍然符合要求。而預留餘量的去除方式,現採用數控加工,替代了鉗工打磨,單件緣條即可縮短加工時間3~5h,加工效率顯著提升。
4、進刀宏指令控制
緣條類零件耳片外圓全部採用行切方式加工,B類狀態鍛件單邊餘量為4mm,考慮焊接變形因素,為焊接專業留有0.50~0.75mm加工預留量,實際切削量大致為3.25~3.50mm。行切時徑向排刀較密,故行切的切削量很小,可以實現高轉速、高進給來提高加工效率。
但是進刀時的第一層切削深度很大,可達3.5mm,嚴重影響和制約了整個行切過程的進給速度,使整體行切的加工速度大打折扣。為解決此問題,使用了進刀宏指令控制第一層的進給速度,而其餘部分按正常行切速度來加工,即可有效避免此問題,刀路如圖5所示。圖中黃色刀路(行切第一層)設置為進刀宏,進給速度為80mm/min,綠色刀路為正常行切軌跡,進給速度為350mm/min。
三、結語
本文給出了緣條類零件高效數字化加工的工藝方法,運用鈦合金高速銑削技術、轉角處理技術、工藝裝備輔助定位、預留機加餘量控制變形以及進刀宏指令控制等方法,解決了該類零件加工效率低、制約公司某機型生產進度的問題。該工藝方法已在公司多個緣條類零件製造中得到應用驗證,運行穩定、高效,加工質量高,取得了顯著效果。同時為以後緣條類零件的加工提供了寶貴經驗。
免責聲明:本文系網路轉載,版權歸原作者所有。但因轉載眾多,無法確認真正原始作者,故僅標明轉載來源。本文所用視頻、圖片、文字如涉及作品版權問題,請第一時間告知,我們將根據您提供的證明材料確認版權並按國家標準支付稿酬或立即刪除內容!本文內容為原作者觀點,並不代表本公眾號贊同其觀點和對其真實性負責。
近期鼓勵投稿內容:工業機器人相關、維修與改造相關
《金屬加工》出品(其他投稿地址均為虛假信息)
熱門圖書排行

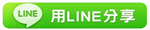
TAG:機工機床世界 |