金剛石印壓微孔成形裝置開發與試驗研究
隨著越來越多的產品向精密化、微型化發展,微小孔的需求越來越大,要求微小孔的直徑越來越小。對微小孔加工質量要求的提高給微小孔加工帶來了巨大的挑戰,大深徑比微孔的加工仍是製造業的難題,因此研究微孔加工技術具有重要的現實意義。
在國內外學者的不斷努力下,微孔加工技術得到了長足發展。日本Kinki大學利用鑽削技術在單晶硅上可穩定鑽削出φ10μm的微孔,能實現的最小孔為φ6.7μm;日本東京大學利用微細電火花加工,用φ2.5μm的微細電極加工出直徑為φ5μm的微細孔;德國馬克斯-普朗克協會的學者專家們利用微細電解加工技術加工出直徑φ5μm以下的微孔;新加坡南洋理工大學的學者們利用飛秒激光加工技術在含有金和鉻兩種金屬薄膜的掩模母版上加工出直徑600nm的微孔;沖孔加工技術在一些精密製造業(如儀錶、儀器等)方面應用較為廣泛,沖微小孔能加工直徑為25μm的小孔。
超快激光等先進加工技術能夠實現微孔、超微孔的加工,但存在價格昂貴、成本高、不適合大批次生產等缺點。本文針對超聲波測漏儀標定樣件(金屬薄片上存在微孔)等易耗件,利用金剛石圓錐壓頭及其刀尖鈍圓的微尺度作用,實現基底效應下金屬薄片壓透成孔的方法,設計開發出大載入力量程的金剛石印壓微孔裝置,旨在實現單側微孔的衝壓成形。該成形裝置具有結構簡單、多感測器原位監測、成本較低等優點,為形成自主產權的金剛石印壓單側微孔成形技術提供參考。
1 金剛石印壓微孔成形裝置開發
(1) 印壓成孔裝置的功能分析
在金剛石印壓微孔裝置中,通過直線電機控制具有一定刃磨質量的金剛石圓錐壓頭對放置在玻璃基底上的金屬薄片進行印壓成形。當錐形壓頭鈍圓部分壓出薄片材料時,金屬薄片底部形成微孔,壓頭鈍圓部分所壓出的薄片量直接影響微孔大小。利用玻璃基底的硬基底效應實現金屬材料在底部的側向塑流,從而成孔,且透明玻璃基底方便採用視頻顯微感測器對薄片底部進行原位檢測。為保證微孔的成形質量,印壓過程中金剛石圓錐壓頭軸線和壓入位移必須與金屬薄片平面保持相對垂直,這要求金剛石印壓微孔裝置可以精確控制金剛石壓頭壓入金屬薄片的位移量和下壓速率,並且金剛石壓頭的角度可任意調整;能夠承載玻璃基底的工作台水平移動,以完成不同位置處的印壓成形。應使用原位多感測器系統進行實時監控,並對金屬薄片底部的成孔時刻進行精確判斷,以實現特定孔徑的微孔成形加工。
根據金剛石印壓微孔裝置的技術要求,對所需的運動空間設計參數進行初步估算。壓頭需滿足Z軸方向位移的自由度。由於壓頭在印壓過程中可能出現傾斜現象,所以壓頭還有繞X軸和Y軸的自由度。對測試件的空間運動範圍進行分析,試件的中心點要有X軸、Y軸方向的相對運動。
(2)印壓成孔裝置的結構設計
根據以上功能分析對金剛石印壓微孔裝置進行結構設計,如圖1所示。裝置採用龍門式框架結構,直線電機固定在橫樑上。直線電機通過導軌實現壓頭的Z向移動,金剛石壓頭固定調節裝置,並與刀架固定連接,通過滑台調節X、Y方向的角度,使壓頭保持豎直。微視頻顯微鏡裝夾在工作台一側,通過光學反射鏡視野觀察光學偏折,既可對金屬薄片(本試驗採用10mm×10mm×0.5mm的銅片)底部材料流動情況進行實時監測,又能簡化結構設計。力感測器通過螺釘固定在機床底座與工作台中間,聲發射感測器通過粘膠固定在銅片附近玻璃基底的上表面。為精密控制壓頭的下壓位移量,下壓直線電機選擇5nm解析度的MicroE光柵尺作為閉環反饋系統。
1.直線導軌 2.角度調節台 3.聲發射感測器 4.玻璃基底5.工作台 6.力感測器 7.金剛石壓頭 8.工件 9.微視頻顯微鏡 10.底座
圖1 金剛石印壓微孔裝置結構
印壓裝置選擇500倍的迷你微視頻顯微鏡,可採用具有較高反射率的三角反射鏡對金屬薄片底部成形孔情況進行原位檢測和記錄,見圖2。此方案節省豎直空間,方便操作。選擇Kistler公司三向測力儀9256C2記錄載入—成孔—卸載過程中金屬薄片所受的壓力及變化規律。該感測器具有靈敏度高、量程範圍大以及測量精度高的特點,可以滿足本試驗的需求。
材料或構件在受力過程中產生變形或裂紋時,以彈性波形式釋放出應變能的現象稱為聲發射。在試驗過程中,被加工材料斷裂形成聲發射源,聲發射源發出的彈性波經介質傳到信號採集器上轉化為電信號,經過信號放大器和軟體分析處理後顯示並記錄在計算機上。試驗選用北京聲華興業科技有限公司製造的SAEU2S-1016-02型聲發射感測器,通過採集金屬薄片斷裂過程中產生的聲發射信號來判斷出孔時刻。
圖2 微視頻顯微鏡裝載方式
(3)金剛石印壓微孔裝置結構
在設計印壓裝置和選擇各元器件後,結合典型支撐零件的加工製造,通過裝配和調試得到的金剛石印壓微孔成形裝置如圖3所示。
1.直線導軌 2.角度調節台 3.聲發射感測器 4.玻璃基底 5.工作台 6.測力儀 7.金剛石壓頭 8.工件 9.微視頻顯微鏡 10.底座
圖3 金剛石印壓微孔成形裝置
2 印壓微孔試驗與分析
(1)參數選擇與感測器設置及調試
為了驗證所開發的金剛石印壓微孔裝置可行性,採用圓錐角為80°的金剛石錐形壓頭對10mm×10mm×0.5mm的純銅銅片進行印壓試驗,經顯微鏡檢測,所得的壓頭鈍圓半徑為5.41μm。
連接完成Kistler 9256C2力感測器硬體設備後,首先測試採集軟體和電荷放大器之間的連接是否正常,然後進行軟體參數設置:選擇8-channel並點擊Auto detect 5080,檢測與電荷放大器的通訊情況;設置電荷放大器標籤、感測器靈敏度、工程單位、測量範圍、濾波器、時間常數等基本參數後,點擊Send Parameters,將設置參數寫入電荷放大器;參數設置完成後對力感測器進行漂移補償,同時對聲發射採集參數進行設置。由於金剛石印壓微孔試驗不需要對聲發射源進行定位,因此該聲發射感測器採用單通道模式。採樣頻率設為10000kHz,採樣點數240,濾波器頻率20kHz-100kHz範圍內。
參數設置完成後對聲發射感測器進行斷鉛試驗,以保證印壓微孔時聲發射信號採集系統可靠工作。試驗時,壓頭壓入速率先快後慢,在接近銅片底部時,放緩壓入速率。在確定測力儀和聲發射感測器的信號採集系統正常的情況下,通過編程式控制制金剛石壓頭開始壓入銅片,同時進行信號採集和分析。
(2) 試驗結果分析
如圖4所示,透過微視頻顯微鏡底部的透明玻璃基底記錄載入—成孔過程中銅片底部材料的塑性流動情況。
(a)壓頭剛接觸銅片時(b)壓頭壓入銅片初期
(C)壓頭壓入銅片後期(d)壓頭成孔時刻
圖4 微視頻顯微鏡觀察的圖像
由圖4可知,金剛石壓頭開始壓入銅片時,銅片底部沒有發生變化;隨著壓頭的不斷壓入,金屬片底部材料開始發生塑性流動,壓頭作用的中心區域材料逐漸向四周拓展;受玻璃基底部分支撐約束作用,材料向下的運動被抑制,從而產生側向流動,出現「塑流環」現象;塑流環逐漸增大,其增長速度先快後慢,最後趨於穩定,成孔時刻便發生在「塑流環」穩定狀態中的某個時刻;當壓頭刀尖的鈍圓部分壓出銅片底部瞬間,在顯微鏡自帶的LED照明燈的白光照射下,成孔區域發生反射,呈現出特別高的亮度,微視頻顯微鏡可以很清晰地捕捉到白色亮點的出現,從而判定成孔時刻。
金剛石壓孔過程中力感測器信號採集結果如圖5所示。由於試驗為豎直下壓,銅片材料受X、Y水平方向力很小,這裡僅對Z向力進行分析。
由圖5可知,壓頭在測力儀開始測試後的35s左右壓入銅片;繼續壓入,單位時間內力的增量先是平緩增加,接著增量逐漸變大;在出孔瞬間銅片所受壓力會出現一個小跳躍,峰值壓力615N左右;為防止銅片回彈導致微孔消失,成孔瞬間立即停止下壓運動但不退刀,在下壓運動停止的這段時間壓力有所減小,但總體上幾乎保持不變;待出孔穩定後,壓頭按給定的速度進行退刀運動,此階段壓力逐漸減小,直至壓頭與銅片分開,測力儀顯示數值歸零。
圖6為金剛石壓孔過程中聲發射感測器信號採集結果。
圖5 力感測器採集圖像
(a)聲發射波動幅度
(b)聲發射能量幅值
圖6 聲發射數據採集數據
由圖6可知,壓頭與銅片剛剛接觸時,由於碰撞產生了聲發射信號;隨著壓頭的不斷壓入,銅片發生變形和塑性流動,聲發射信號的波動幅度與能量值一直在一定範圍內波動;在銅片被壓頭壓透瞬間會產生巨大的能量值,聲發射波動幅度也會相應增大,因此也可將能量幅值和波動幅值作為控制點,以判斷成孔時刻。
試驗結束後對所得的銅片微孔進行檢測分析(見圖7)。圖7a為微視頻顯微鏡微孔成形時刻的形態圖,圖7b為SEM檢測的微孔形態和尺寸大小。檢測結果表明:金剛石印壓微孔成形裝置能夠在金屬薄片上實現微孔的成形加工,經過多次試驗檢測,受被壓金屬材料的影響,銅片底部微孔孔徑可穩定在絲米級,極限尺寸可達微米級。
(a)底部成孔形態(b)SEM的成孔特徵檢測
圖7 微孔檢測圖像
小結
為實現金屬薄片上單側微孔的成形加工,對金剛石印壓微孔成形裝置進行了開發,包括裝置整體結構設計及各元件選擇,並通過印壓試驗驗證了所開發裝置的可行性。
通過配套的多感測器原位監控系統(即力感測器)記錄印壓過程中銅片所受壓力的變化規律,採用微視頻顯微鏡呈現銅片底部材料「塑流環」的變化規律。將聲發射採集數據中能量幅值、波動幅值作為控制點,結合微視頻顯微鏡中出現的白亮點,能精確判斷成孔的時刻,從而實現金屬薄片底部微米級微孔的印壓成形加工。
原載《工具技術》 作者:石廣豐
書訊

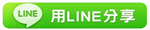
TAG:工具技術 |