變速器齒輪電子束焊和激光焊對比
A.緒論
汽車變速器齒輪在變速或行駛中易受到衝擊,離合器上齒輪和變速器齒輪間的焊接處的強度要高。同時,不會產生焊接變形導致的噪音。 變速器齒輪要求高強度、高精度焊接。
電子束焊滿足高強度、高精度的條件,被廣泛應用。電子束焊的焊縫形貌是扁平狀,相比於激光焊接有橫嚮應力少和母材表面熱傳導少的特徵。從很薄的薄膜至幾百毫米的焊接都可進行。電子束容易被大氣中的導電粒子分散,所以必須在5×10-2torr以上高真空狀態進行焊接,但電子束焊為抽真空,需要大量的時間,制約生產效率提高,也因真空狀態不同導致焊接的質量不同的缺點。
隨之可代替的激光焊接方法克服電子束的缺點,受到矚目。也被海外的汽車製造商驗證並使用。
表1】電子束焊接與激光束焊接的特徵
為提高變速器零配件的焊接效率,電子束焊接與激光焊接做了對比,驗證變速器零配件焊接領域裡激光焊接工藝方法的合理性。
B.試驗方法
工件:手動變速器變速器齒輪
激光焊接
1) 4KW ND:YAG f=200, Spot Size=0.6mm
2) 2.5KW CO2f=200, Spot Size=0.3mm
電子束焊接
40KV 低電壓型加速電壓
對相同焊接深度條件下的焊縫寬度,焊縫高度,變形量等比較分析
【圖1】手動變速器變速器齒輪和離合器齒輪
圖1的試驗中使用的Manual Transmission的變速器齒輪由離合器齒輪和變速器齒輪組成。
2種材料在焊接之前經過了清洗、烘乾及壓裝工序,使用的材質是ASCM17H1(參照表2)。
C.結果及考察
焊接端面、變形疲勞強度、熱變形方面對電子束焊接和激光焊接進行結果分析。
1. 焊接端面分析
把熱變形試驗樣件焊接方法做的分析列表看【表3】
焊接深度因各焊接方法的熱傳導而不同,Nd:YAG激光的焊縫寬度最大。
CO2激光焊和電子光束Spot大小是0.3mm,Nd:YAG激光0.6mm時,焊縫寬度因光束Spot大小而變化。
【表3】焊接方式不同的情況下焊接端面及試驗條件
【圖2】是受熱影響監測範圍從焊縫表面至0.2mm深度測量的結果,所以得出受熱影響範圍大小不會因焊接方法而不同。
焊接深度(mm)【圖2】焊接深度導致受熱影響範圍對比
2. 變形疲勞強度
【圖3】是監測變形疲勞強度的樣件,為了測量焊接部位的破壞強度,以10mm間距焊接了3處,焊接深度為3.0mm。樣件疲勞強度試驗條件按發動機最大輸出扭矩3倍以上的動態扭矩100萬Cycle,結果與電子束焊接相同。
【圖3】變形疲勞強度試驗樣件
3. 熱變形試驗
如【圖4】,為掌握變速器齒輪的熱傳導特性,利用熱成像攝影機監測了激光焊接前後0.5s~10s之間的變化。焊接時產生的熱量傳到離合器齒輪Taper處內側後,逐漸向離合器齒輪和變速器齒輪的齒牙散去。
單位:秒/S【圖4】激光焊接後溫度分布
熱變形監測部位是Taper角度、Taper高度、變速器齒輪內徑、齒牙,如【圖5】,按焊接方法焊接了15個樣件,各抽選10個進行測量
A:Taper角度 B:變速齒輪內徑 C:Taper高度 D:齒牙
【圖5】變速器齒輪的熱變形測量部位
考慮到最後加工公差是CO2激光焊的熱變形特性表現最好,Nd:YAG相比電子束焊,散布高、50%左右超出了加工公差範圍。雖然電子束焊有加工余度,但相比CO2激光焊,散布大。
■:電子束焊 ●:CO2激光 ▲:Nd:YAG激光焊 Taper角度(分)
【圖6】變速器齒輪的Taper角度變化導致的熱變形分布
D.結論
電子束焊接、CO2激光焊、Nd:YAG激光焊接特性試驗對比結果
1) 焊接深度
電子束焊以最少的熱量達到最深的深度,Nd:YAG激光在芯部焊接上比CO2焊接不利,受熱影響部位與焊接方法無關。
2) 疲勞強度
與焊接方法無關,可得到類似的強度
3) 熱變形
按焊接方法測量結果CO2激光焊結果與電子束焊結果類似,Nd:YAG激光焊結果與CO2激光焊相比,存在能量吸收率高的特性,導致熱變形大。
通過電子束焊和CO2及Nd:YAG激光焊接的特性對比結果,對於變速器的齒輪焊接,使用激光焊接更為有利。
--end--

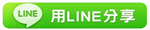
TAG:齒輪傳動 |