Carbon CLIP技術應用案例:大黃蜂賽車隊3D列印重新設計製造進氣歧管重量減少50%
幾年前,美國Carbon公司推出了具有專利的CLIP技術高速3D印表機,並與阿迪達斯合作開發了一系列尖端3D列印運動鞋,以及其他開創性項目。Carbon技術的另一個令人印象深刻的應用案例是由加州大學薩克拉門托分校的學生工程團隊HornetRacing進行的,這個團隊使用3D列印技術來革新它正在為重大比賽而建造的賽車。
汽車工程師協會(SAE)每年都在不同的大學團隊之間進行比賽,它有嚴格的準則,旨在鼓勵創造力,挑戰學生提出解決設計和工程問題的創新方法。在2017年,SAE要求所有發動機的蓄能器節氣門必須拆除,並用所有四個氣缸的單一節氣門代替。此外,準則規定,一個20毫米直徑的限流器必須放在單節氣門後面。HornetRacing發動機的性能限制減少了其潛在的空氣流動,嚴重限制了其輸出功率。
大黃蜂賽車使用的車輛有一台本田CBR600RR系列四缸發動機,通常配備有四個獨立的節氣門(每個氣缸一個),每個節氣門直徑各為44毫米,並且放置得非常靠近氣缸蓋。競爭指南要求對進氣系統進行重大改組,氣流問題也影響了前幾年的車輛性能。氣流不暢通常會導致加速時間延遲或不可預測,這使駕駛員的工作在試圖控制車輛時變得更加困難。
該團隊決定利用Carbon的3D列印技術來改善發動機的設計。最重要的是發動機進氣歧管的形狀必須改變,以改善和優化通過發動機的空氣流動。具體來說,團隊的主要目標是創建促進最小邊界層形成的組件,以實現更平滑的氣流。他們還希望將燃油噴射器埠集成到進氣流道(將充氣室與氣缸蓋連接起來的管子)的底部,以實現最小的流動湍流。整體的重量減輕和簡化的裝配過程,會留下較少的誤差,也被認為是可以提高性能的因素。
插播小廣告
Carbon的CLIP3D列印技術的使用意味著團隊可以使用全新的設計幾何圖形。經歷大量不同的幾何迭代以找到完美的形狀之前會花費太多時間,但是整個過程通過基於直接實現3D數字模型的製造過程來顯著簡化。而且,使用傳統的製造工藝,包括大量的工具,碳纖維模具和焊接,成品設計的組裝和生產成本已經高得驚人。
使用Carbon專有的RPU70材料列印,大黃蜂賽車的進氣歧管的新設計是球形,只有7英寸的長度。這取代了以前的兩英尺長的擴散器,以及超過半加侖容量的大增壓器。整體設計靈感來源於超音速噴氣發動機震動錐體,能夠根據其形狀調節進氣量。該團隊通過在燈泡結構內設計釘狀流動分流,將擴散器和通風系統的功能集於一體。
3D列印還意味著不涉及焊接,並且新的進氣部件的重量顯著減小。進氣歧管位於車身相對較高處,這意味著其重量對汽車的側傾中心和其他車輛動力學有重大影響。3D列印組件的重量比2016年「大黃蜂」賽車所使用的重量減少了50%,並且有助於改善車輛操控性和改善整體駕駛體驗。
在Carbon3D列印系統和材料的幫助下,「大黃蜂賽車」在SAE比賽中的表現比以前更好。HR2017賽車全球排名第16位,共有來自世界各地80多所大學的車隊。
180頁3D列印行業應用白皮書(2017)

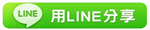
TAG:3D列印世界 |