灰鑄鐵缸體頂面精加工問題解析
缸體頂面是連接缸蓋,使缸孔和缸蓋組成密閉燃燒室的重要特徵,它的加工質量直接影響著燃燒室的質量狀況,進而影響發動機的性能。缸體材料一般都是鋁合金和灰鑄鐵,鋁合金重量輕、散熱好、抗磁性和機械加工性較高,目前在汽車上的應用越來越多,但因面臨較高的成本,不少發動機廠家仍在使用灰鑄鐵缸體。
本文針對我公司灰鑄鐵缸體頂面加工過程中存在的問題進行了系統分析,並結合現場的大量試驗驗證給出了解決措施。
圖1 缸體頂面加工效果
銑削加工概述
缸體頂面的終尺寸和表面粗糙度一般要經過粗銑、半精銑和精銑等多道工序達到期望的質量。近年來,隨著機加工設備能力和刀片材料的改善提升,銑削已成為箱體類零件的主要加工方式,高轉速、快進給和大餘量的切削方式對促進加工效率的提升有著極大的幫助。同時,通過對設備能力、刀具材料、切削參數和餘量分配的組合優化,可以獲得很高的尺寸精度和表面粗糙度(見圖1)。
1. 缸體頂面加工工藝
為保證缸體頂面最終尺寸符合圖樣要求,達到較高的尺寸精度和表面粗糙度,大批量生產時一般需要經過粗銑、半精銑和精銑等共三次銑削,工藝過程及作用如圖2所示。
粗銑:去除毛坯餘量,銑削掉大部分的毛坯表面缺陷,如砂眼、氣孔等,切削餘量約2.5~3.5mm。
半精銑:終尺寸形成的重要保證,同時獲得較為平整的表面,切削餘量約0.5mm。
精銑:修光階段,獲得較為光潔的表面,表面粗糙度Rmax 10μm以內。
a)粗銑頂面
b)精銑頂面
圖2 缸體頂面加工工藝流程
2.銑削設備及刀具簡介
我公司機加工車間採用MAG四軸聯動CNC機床,該設備具有高精度、高柔性和高自動化等特點。刀具採用TCM提供的大面銑刀,具有高效率、高精度和壽命較高等特點。粗加工時,採用六點定位,銑刀分3刀銑削頂面,去除毛坯餘量,加工精度較低,且受毛坯預加工基準(六點定位面)影響定位精度。半精加工和精加工採用一面兩銷定位,且集中在同一個工位,在同一把刀具上安裝半精銑和精銑的刀片,使得具有較高的加工精度,避免重複定位誤差,並提升加工效率。由於缸體頂面較大,為能保證平面度需要一次完成整個面的銑削。因此刀盤直徑200mm的刀盤,由15片半精銑刀片和3片精銑(修光刃)刀片組合而成。半精銑刀片為CBN材料,精銑刀片為陶瓷材料。精銑刀片比半精銑刀片在軸向上高50μm,即修光餘量為50μm。
精銑頂面問題分析
1.精銑頂面輪廓度尺寸不合格
缸體頂面的面輪廓度要求高達0.1mm(相對G-H_A),要達到符合要求的平面,則對該平面的平面度、平行度以及面到基準的距離三者之和有很高的要求,實際加工中主要存在的形式是因為距離的偏移過大,導致面輪廓度超出工藝要求。針對該問題,進行原因分析如下:
(1)測頭精度不足
為保證缸體頂面到曲軸孔中心的距離保持在一個穩定的值,精銑頂面時需跟隨曲軸孔中心連線的變化而變化,所以精銑頂面前會採用marposs測頭對曲軸孔中心進行100%測量,實時監控曲軸孔加工情況,並補償到精銑頂面的坐標值中,補償的準確度直接影響頂面的加工精度。對於測頭精度,可通過type1 重複50次測量標準塊來確認,對於重複精度不足的測頭進行更換或維修即可。
(2)測頭或曲軸孔有雜質
當曲軸孔或者測頭粘帶有鐵屑等雜質時,會導致測量結果錯誤,致使補償結果出錯。對於鐵屑等雜質,可以在設備內部增加噴嘴,對曲軸孔、測頭分別吹氣或者噴切削液進行沖洗,以確保無雜質。同時,還可以在程序中對測量結果進行判斷,根據工藝分析,當補償量超過0.01mm時,機床報警不補償加工,由生產人員清潔工件及測頭後重新測量加工。以此監控來區別是設備補償測量錯誤問題還是來料變化問題,避免加工超差。
(3)加工偏移後人員未及時調整補償
面銑刀磨損速度較快,當刀具磨損後若不及時調整刀補量,則會形成逐漸攀升的距離差,從而導致輪廓度變差。此外,當整個加工系統運行一段時間後(如定位面等設備磨損),也會出現整體偏移中值的情況,也需要現場人員根據運行情況,對加工坐標系統進行整體補償。
圖3 缸體頂面平面度監測數據(刀具壽命短)
2. 精銑頂面平面度達不到要求
圖3所示為某工位缸體頂面平面度的測量監測數據,從數據監測可以看出,平面度波動特別大,很多點處於接近超差的邊緣,個別點已失控超出工藝要求。缸體頂面是一個大面,整個大面上分布有水套孔、缸孔和缸蓋螺紋安裝孔等,使頂面被分割成多個小區域平面。在精銑過程中,由於各個區域面積不一致,導致切削過程中受力不一致,對刀具調整、刀片質量和刀具防振等提出了更高的要求,分析原因如下:
(1)精銑刃高差控制
精銑刀片刃高差決定了修光去除量,修光太少,不利於修正平面度及保證表面粗糙度;修光量太多,容易造成刀具壽命短,刀片磨損加劇,甚至出現崩刃的情況。根據實際驗證,當修光刃高差控制在40~60μm的時候,加工質量及壽命都比較好。
圖4 CBN刀片壽命長平面度控制好
(2)刀片材料選用不當
刀片材料很大程度上影響了刀具使用壽命,較好的刀具壽命可以保證刀具短期內磨損量小,切削穩定,從而保證平面度的加工穩定性(見圖4)。新刀片到磨損後期舊刀片平面度差異大,選用壽命長的刀片不僅利於質量控制,還可以減少現場因為換刀而增加的工作量(見圖5)。
圖5 改變切削刃材質,提升刀具切削質量
(3)刀片幾何尺寸設計不合理
刀片的前角后角、刀夾設計以及刀片安裝緊固方式等,也會影響刀片加工過程的切削穩定性,鑄鐵加工切削力大,適當的刀片尺寸設計和安裝方式,對加工過程的穩定起著關鍵作用。
(4)調刀尺寸控制
實際調刀高度與理論高度的差異是否控制在符合要求內,各個刃之間高度差是否在要求範圍內,因為,刀刃之間的高度差過大會導致切削受力不穩定,導致刀盤整體振動。一般對於切削力大的半精銑刀片採用固定式硬限位安裝刀片,修光刃刀片為高度可調式。
(5)其他原因
設備主軸抓刀力、刀盤整體動平衡、主軸遠端跳動以及刀夾與刀體貼合情況等都會影響到頂面切削時的穩定性,出現異常情況時需要對以上相關參數逐一排查確認。
3.精銑頂面粗糙度達不到要求
精銑頂面粗糙度達不到要求的主要表現為頂面粗糙度Rmax不合格,超出工藝要求,相關原因分析如下:
(1)鑄鐵材料組織異常
對於這類問題,可從金相組織中明確判定材料是否存在異常,對於異常材料,則推動毛坯供應商改善澆築工藝及進行過程式控制制。
(2)銑削速度過快,表面組織被撕裂出小凹坑
對於這類缺陷導致的粗糙度不合格,可以通過降低切削速度來改善切削情況,計算合理的轉速和進給,防止刀具撕裂組織表面,形成凹坑。
(3 )其他問題
此外,刀具磨損嚴重、刀具不平衡量大、工件夾不緊加工時退讓和系統剛性差導致加工振動等也會導致表面粗糙度差。

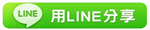
TAG:AI汽車製造業 |