Whelen案例,六西格瑪設計DMADV方法
Alex Stepinski
Greensource Fabrication 副總裁兼總經理
背景
2014年,應急報警行業OEM市場的領導者Whelen Engineering Company設計規划出了世界上第一家綠色智能PCB製造工廠,作為服務於內部需求的專屬工廠。由於該項目取得了巨大成功,2016年,公司決定建設一個更先進的工廠,為其他公司提供製造服務。本文概述了公司在設計這一新項目時所採用的方法,現在這個項目已經成為一個獨立的名為Greensource Fabrication的業務部門。這個新的業務部門預計於2018年投入生產。
方法概要
根據我們的經驗,對於PCB行業中複雜的工藝設計來說,整體六西格瑪設計DMADV方法並不常用。這種方法需要專門的研發資源、技術團隊長期出差、大量的實踐經驗以及巨大的資金投入。由於很少有PCB工廠具有研發能力,所以我們認為目前這種方法風險很低,並且具有很高的投資回報率,因為當其他人只會相互抄襲時,你能設計出一些不一樣的定製化的東西,就能獲得非常強大的競爭優勢。
DMADV方法高級大綱
階段1:定義
在設計工廠和工藝時,第一步是確定市場需求。在本案例中,由於我們是第一次進入這個市場,所以我們花了六個月的時間走遍全球,拜訪了20個不同國家的幾十家PCB廠和設備供應商。我們還研究了客戶的路線圖,並與重要的OEM技術人員進行了交流。我們很快發現,世界上絕大多數最好的設備和工藝北美都沒有。我們還發現,我們的潛在客戶不得不經常離岸採購PCB,以滿足他們對先進技術的需求。在由於知識產權出口限制或法律法規限制而不能採用離岸製造的情況下,設計往往會受到北美區域生產能力的限制。這應該並不意外,因為北美已經有近20年的時間不是製造PCB的主要區域了。
同時,我們發現,作為一個板廠,如果靠當地的銷售代表提供引導,則很有可能會極大地限制您的能力。如果您直接與海外負責人合作,就會發現他們能提供的解決方案遠比當地銷售代表的要好。北美市場尤其如此,由於其在全球PCB生產中所佔的份額很小,而且在印製電路板製造廠的投資資本支出中所佔的比例更小,因此不會成為主要設備供應商的重點市場。
在這個階段,我們得出的結論是,如果我們要採購世界級的工藝設備,並把它們集成到位於北美的一家工廠里,我們很有可能會具有巨大的競爭優勢,同時還有很高的投資回報率。隨後,我們決定,將工廠設計為專註於HDI技術,嚴格的對準公差(X軸、Y軸和Z軸),高縱橫比和薄電介質(包括撓性、ABF等),總厚度範圍為0.050 mm ~6.20 mm;同時我們要在製造這類PCB時不產生重大環境污染,並使用最高程度的自動化。
安美特薄芯撓性化學鍍和閃鍍生產線
階段2:衡量
在我們確定了關鍵設備供應商後,就開始舉行會議,對各個公司進行基準測試,以確定其作為潛在合作夥伴的技術和商業能力。然後,我們通過審核他們過去的多次設備安裝來確定項目效果,並聯繫我們的行業聯繫人來確定他們的營銷活動和口碑。收集到的參考數據越多,就越接近事實的真相。我們很快發現,這項研究的投資回報率很高,之前一些被認為是全球頂級的供應商無法通過篩選,而一些規模較小的區域供應商卻表現突出。
在完成衡量階段後,我們發現選擇的合作夥伴中有80%來自歐洲和日本,其餘的來自美國、中國台灣地區和大陸。由於我們採用高度自動化/低勞動力方法,這種區域分配主要是由我們對高可靠性工藝和低總質量成本的需求決定的。
AWP 集團在波蘭建設的零廢液排放、一件流DES 生產線
階段3:分析
在我們選定了主要的設備供應商合作夥伴後,我們就會跟他們坐下來,開始討論項目的具體細節。這時,我們才會在受控條件下討論細節,向他們介紹我們在項目中的知識產權。我們的知識產權來自於我們已經開發完成的世界上第一家專屬綠色智能工廠[1]。現在的挑戰是經濟有效地將這個模式複製到一家服務於商業市場的工廠中。與我們以前的專屬運營相比,這家工廠能夠採用更普遍的工藝(如干膜、化學鍍銅、OSP等)。
好消息是,我們選擇的供應商對我們項目所採用的方法都感到非常興奮,並且在實現自動化和讓世界上科技程度最高的加工工藝更加綠色環保兩方面都提出了大量好點子。
Ludy 公司在德國建設的零廢液排放SAP 和高縱橫比專用電鍍生產線
階段4:設計
設計階段是項目中最耗時的部分,需要我們的工程團隊與供應商的技術部門進行數百小時的面對面討論,討論環節大部分是在海外的供應商公司里進行。這是為了確定我們所採購的設備的設計細節,以確保我們的設計中沒有任何風險,並最大限度地提高設計性能。
這個階段產生了太多驚喜,由於我們與合作夥伴們一起度過了非常多的時間,所以能夠整合全世界這個行業中最有才華的工程師們的經驗。例如,我們現在的自動化水平更高,相比我們最初的估算,需要的勞動力減少了一半;在濕法生產線的工藝設備中,廢水平衡能夠達到完全不需要排出任何沖洗廢水,同時,通過工程開發出的集成完全廢酸洗液回收的平衡系統,減少了50%以上的化學品成本。
我們還設計出了世界上第一套具有完全可追溯性的PCB生產系統,它使用了嵌入式二維碼和RFID來追蹤每一塊單獨的覆銅板,從而實現真正的單件追溯流程,並消除了紙面記錄和手動記錄輸入,以及使用了一些 AGV運輸。這些還只是剛開始的時候我們與合作夥伴實現的設計創新中的一小部分。
階段5:驗證
目前,我們正處在啟動和驗證50%的已經安裝和合格設備的過程中。到目前為止,我們達到了所有的里程碑目標,公司對我們的進度也非常滿意。我們獲得如此好的成績,跟我們竭力選擇好的供應商以及我們和供應商合作夥伴之間大量辛勤工作和出差是分不開的,這也讓我們相信選擇DMADV方法是正確的。
我們希望市場能夠在不遠的將來認識到:零排放、高度自動化、高一致性的綠色智能工廠將會成為行業標準。根據我們的經驗,我們覺得在這個行業中,這種轉變早就應該發生了,現在才是真正邁進21世紀,特別是考慮到這個轉變有如此高的投資回報率時。

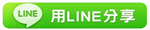
TAG:電子時代 |