10nm技術節點大戰:台積電vs.三星
智能手機的普及,大大地改變了現代人們的生活方式,言猶在耳的那句廣告詞——「科技始終來自於人性」依舊適用,人們對於智能手機的要求一直是朝向更好、更快以及更省電的目標。就像2015年發生的iPhone 6晶元門事件,每個蘋果(Apple)產品的消費者一拿到手機時,都迫不及待地想要知道自己的手機採用的是台積電(TSMC,16nm)或是三星(SAMSUNG,14nm)的晶元。
這場戰役兩家大廠互有消長,首先是三星的14nm較台積電的16nm搶先半年投入量產,因兩家大廠的鰭式晶體管(FinFET)設計也確有雷同之處,後續又衍生了競業禁止官司訴訟等故事,無論如何,最終台積電還是以些許性能優勢擊敗三星,並使其16nm工藝於來年獨拿了Apple的A10處理器(iPhone 7)訂單。
2017年,三星捲土重來,自主設計了10nm技術工藝的Exynos8895 (名稱源於希臘單詞Exypnos和Prasinos,分別意為智能和環保),搭載於自家旗艦機Galaxy S8上,宣稱與上一代14nm工藝相較性能提高了27%、功耗降低40%。另一方面,台積電的10nm產品A11 Bionic於今年iPhone 8發表會上亮相,Apple副總裁Phil Schiller對該晶元做了短短一句評價:「智能手機歷來最強大、最聰明的晶元」(The most powerful and smartest chip ever in a smartphone)。
於此人們又有新的議題可以討論,兩家世界級半導體廠究竟在新的10nm世代孰強孰弱呢?眾多的分析平台都針對兩家的產品進行了評比,例如,圖1是知名跑分評測網站Geekbench針對兩家晶元進行的比較,我們可以看到台積電的A11晶元效能分數,無論是單核心的4216分或多核心的10101分,分別都優於三星Exynos8895的1957與6433分,後續亦有許多文章或平台以各種數據說明兩家大廠產品的規格品項差異。
圖1:Geekbench網站提供的效能參考:i8 vs. S8
本文則從另一個角度出發,以材料分析的方式一探iPhone 8的Bionic (以下簡稱i8)以及Galaxy S8的Exynos8895 (以下簡稱S8)兩款晶元中靜態隨機存取內存(SRAM)區域與FinEFT工藝的差別,輔以高解析度的穿透式電子顯微鏡(TEM)影像分析技術,呈現納米級尺寸差異的影像,並以微區的能量散布光譜映像分析結果(EDS mapping),解釋兩家選用材料的差別,讓讀者得以連結形貌與成份二者間的關聯,從而了解兩家大廠的10nm工藝。
SRAM大小與密度
我們曾經在《電子工程專輯》期刊中發表《由材料分析觀點看英特爾14nm/14nm+演進》一文,比較英特爾(Intel)的14nm及14nm+6T SRAM差異。6T SRAM單元面積越小,顯示在同樣尺寸大小的組件可以植入更多的內存單元。圖2是2017年初英特爾指出14nm跨入10nm時,同樣大小的邏輯區域會增加2倍以上的內存單元,故6T SRAM單元面積通常被視為衡量工藝優劣的重要因素。
圖2:英特爾指出SRAM密度與線寬發展的關係
圖3a、3b分別指出iPhone 8 (i8)以及Galaxy S8 (S8)之晶元SRAM區域的STEM影像俯視圖,我們可以發現i8工藝中的鰭片間距(Fin pitch)較S8的小,進而影響了6T SRAM的單元面積,i8的面積為0.040um2,遠遠小於S8的0.049um2,然而圖3c、3d顯示兩者在工藝上並無材料選擇上的差異,所以相信i8整體效能勝出,與其邏輯區域搭載單元數量有相對之關係(若SRAM整體區域大小相同的狀況下,i8搭載的記憶單元數量將是S8的1.25倍)。
圖3:(a)i8 SRAM區域的STEM影像;(b)S8 SRAM區域的STEM影像;(c)i8 SRAM區域的EDS影像圖;以及(d)S8 SRAM區域的EDS影像圖
FinFET結構與特性
進一步看看兩者間鰭片結構的差異,透過TEM的影像以及EDS影像,我們可以解析其極細微的差異,圖4a、4b呈現的是i8以及S8中鰭式硅基板的形貌,包含了N型(N-Fins)以及P型(P-Fins)結構。
圖4:(a)i8 FinFET結構的TEM影像;(b)S8 FinFET結構的TEM影像;(c)i8 FinFET結構的EDS影像圖;以及(d)S8 FinFET結構的EDS影像圖
兩者的設計間存在著一些差異:首先,i8的N-Fins結構有二分之一的底部是相連的,這裡跟S8的每個鰭片彼此間有很大的不同;表1統整了一些N-Fins的指標性尺寸,在這裡我們可以發現兩家的工藝設計走向不一樣的路線,S8致力於增加與閘極接觸的鰭片高度(Fin High)與鰭片寬度(Fin Width),因此S8在這兩個數字上都是略勝i8的,這個設計完全符合FinFET增加通道面積的概念。雖然i8可能在通道面積上略小於S8,但其鰭片間距卻比S8小非常多,因此我們認為i8除了增加通道面積外,也兼顧縮小單元面積大小,因而能大幅增加SRAM單元數量。
表1:鰭片的高度、寬度與間距差異:i8 vs. S8
另一方面是材料的選擇,從圖4c、4d的EDS影像顯示,兩種10nm的FinFET成份組成是大同小異的,而且也沒有出現跟以往不同的新材料,但是,i8在P-Fins的設計上有一個較獨特的地方,我們發現了明顯的鍺(Ge)信號出現在鰭片上,而且整整涵蓋了三分之一的鰭片,意即i8直接將鍺元素添加於P-Fins結構中;而對照S8的設計,在P-Fins結構的頂端也可觀察到鍺信號,但是非常微弱,而且只佔整體十分之一的鰭片長。
在2016年IEEE國際電子組件會議(International Electron Device Meeting,IEDM)的一篇文章『Setting the Stage for 7/5 nm』中提及,在鰭片中添加鍺確實能夠有效地提升電洞的遷移率,而且三星、GLOBALFOUNDRIES、IBM皆已計劃在7nm工藝中使用,目前各廠尚未量產或大量添加,原因可能是尚未完全克服添加鍺後形成的錯位跟缺陷,但我們的確看到台積電已經在10nm量產中使用此技術領先群雄。
SiGe組成與應變
在目前的工藝中,磊晶所生長的硅鍺(SiGe)結構系利用硅鍺與硅之間晶格常數差異產生應變,從而提高載子的遷移率,這使得邏輯組件在相同尺寸下,性能可以得到很大的提升。為了讓讀者一窺SiGe全貌,我們準備一個極薄(依照圖5中閘極下緣high-k材料的邊界及其下方的鬼影判斷,我們製備的樣品寬度為一個鰭片左右,約5~10nm)的樣品來觀察鰭片上方磊晶的SiGe結構。 圖5:(a)i8與(b)S8平行鰭片方向閘極與SiGe結構;(c)i8與(d)S8 SiGe結構處的EDS元素分布圖
圖5即是在i8與S8平行P-Fins方向上觀察到閘極與SiGe部位的高角度環形暗場(HAADF)影像及其EDS mapping影像。我們可以因此推敲一些設計細節:i8所使用接觸SiGe的金屬觸點W為多段設計,但S8卻是一整塊的W材料;另一方面,比較SiGe的大小面積,即可看到S8的SiGe相對面積較小,可能在工藝的過程中有較大的SiGe損耗,這一點在i8中可以看到其SiGe整體結構優於S8的表現。最後,在HAADF影像及EDS成份分析,則可觀察到兩者的SiGe皆呈現兩個不同濃度的成份分布,中心與外層的鍺濃度不相同,而這個設計最早在英特爾的14nm+時已經觀察到了,相信濃度變化的SiGe應可導致更大的應變,使得載子的遷移率能夠有效地提升。
金屬聯機與尺寸微縮
最後使用SEM觀察整體SRAM金屬聯機的狀況(圖6),在此可以清楚地看到i8在這個部份遠遠勝過S8,粗估M1至M11,i8的尺寸就比S8將近少了300nm,在這個金屬聯機迅速降低的情況下,相對而言即是帶來寄生電容及信號延遲(RC-delay)的現象。RC-delay的影響因子如下: ?ρ= 互連導線電阻值
?ε= 圍繞導線的介電材料之介電常數
?L= 金屬互連的長度
?W= 寬度或互連的間隔
在導線距離W迅速減少的情況下,為了降低RC-delay的方法有二,第一為更換更低電阻的導線材料,這一點在日前於舊金山舉行的IEDM 2017上,英特爾透露其10nm的工藝節點細節,他們將為最底部的兩互連層更換新材料——鈷(cobalt),這個部份的細節將在日後進一步揭露;第二即是使用更低介電常數的材料做為low-k層。本文在i8與S8的討論中,並沒有發現到金屬導線材料的更新,所以我們推斷i8所使用的low-k材料可能也優於S8,才能在尺寸優化300nm的情況下,依然保持高效能。
圖6:10nm工藝金屬內鏈接的SEM影像:(a) i8與(b)S8
結語
根據i8與S8的FinFET比較,以筆者的角度觀察,S8規規矩矩地走向尺寸微縮,以及增加通道面積的方向,但是i8在這個架構概念下增加了更多的巧思,提升了整體邏輯區的密度,同時也在工藝中添進了一些極微小的差異來改善效能。
透過進一步的材料分析,就能幫助工藝端以及讀者發現並了解這些極小的差異。正所謂「見微知著」,小小的一個SRAM區域就已經藏在許多設計上的小細節,而且最後的勝負就來自於這些每一個小細節的累積。
因應10nm以下的工藝即將開打,工藝端在微縮尺寸將會面臨更多的挑戰,此時工藝的驗證能力,如何精準地提供在幾個納米間的差距,絕對是致勝的關鍵。藉由材料分析帶來的強大驗證武器,將成為工藝端以及讀者的眼睛,並一起投入接下來的每一個戰場。
本文授權編譯自EE Times Taiwan,版權所有,謝絕轉載

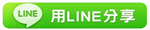
※過春節帶什麼電子產品給家人作禮物?
※不僅服務硬體工程師,2018年賽靈思如何布局AI?
TAG:EET電子工程專輯 |