汽車輕量化及使用材料多元化
關注我們,獲取更多汽車新材料資訊!
1前言
近年來,世界各汽車製造廠不斷推進汽車輕量化。在汽車用材方面,除了鋼鐵材料,鋁材和碳纖維強化樹脂(CFRP)的使用也在增加。車體採用多種材料的「材料多元化」有了很大進展。
歐盟2013年開始銷售的寶馬電動汽車「i3」的駕駛室和底盤分別採用CFRP和鋁材,使車體大幅度輕量化。i3的年銷售量超過1萬輛。大大超過此前CFRP車的銷售量。
之後,2015年開始生產的BMW7系插電混合動力車採用了超高強度鋼板、鋁材、CFRP鋁材補強材料等多種材料,進一步推進了車體的材料多元化。
戴姆勒從2014年開始銷售的新車型梅賽德斯-賓士「C級」、「E級」車的外板採用超高強度鋼板和鋁材,實現了數十公斤的輕量化,降低了燃油效率。
奧迪Q7正式將鋁材作為車體材料。
美國著名的福特皮卡車「F150」的2015年車型的駕駛室和後貨箱蓋板改變為鋁材結構,重量減輕320kg(減重15%)。
日本的本田技研工業公司第二代超級車「NSX」的車體骨架採用鑄造鋁材、擠壓鋁材和鋁板材,外板採用鋁材和CFRP。
豐田汽車2017年開始銷售的插電式混合動力車(PHV)「普銳斯」的後車門骨架採用CFRP。
本文首先對鋼鐵向鋁材、樹脂等輕型材料的轉化背景進行介紹,然後分別對鋼鐵、鋁材、樹脂等材料進行分析,最後提出在推進汽車用材多元化的進程中需要解決的問題。
2世界性汽車燃油效率法規的強化
全球各汽車製造廠努力推進汽車輕量化可以歸因於世界性的汽車燃油效率法規的強化。運輸領域的溫室氣體排放量佔世界溫室氣體排放量的比例很大。因此為抑制溫室氣體排放,對汽車燃油效率進行規定是必須實施的措施。實際上,世界主要國家對汽車燃油效率的規定不斷嚴格化。例如,美國規定2025年乘用車燃油效率是23.9km/L,比2013年燃油效率提高了61%。過去汽車製造廠在汽車動力系統改善方面進行投資研究,通過發動機混合動力化等方法提高燃油效率,今後除了進行這種投資,還要推進車體輕量化。一般來說,車體每減輕100kg,燃油效率可提高1km/L。
另一方面,必須認識到,車體輕量化並不是很容易實現的。這是因為,車體有向大型化方向發展的趨勢,並且為了達到安全規則的規定和實現電動化提高乘用的便利性,在汽車內增加安全氣囊和導航系統等裝置,使汽車重量增加。因此,為了使汽車的輕量化超過其重量增加量,不僅要採用比過去材料更輕的材料,而且要進行車體結構改革、改變部件形狀和部件數量。通過這兩方面的綜合措施實現汽車輕量化。
3各類材料輕量化動向
3.1鋼鐵材料:高強鋼比例增加
過去,汽車用鋼鐵材料是具有強度、成形性、環境性(循環利用)以及價格等多方面優勢的良好材料。隨著近年來汽車輕量化的推進,汽車用鋼材也發生了變化。強度高、加工性好的高強度鋼比例不斷增加。高強度鋼是添加C、Si、Mn等元素、進行組織控制提高強度的鋼材。其製造方法往往被鋼廠視為保密內容。高強鋼的強度高於普通鋼材,因此可薄型化,容易實現輕量化。一般來說,高強度鋼的強度升高,在進行複雜形狀部件衝壓成形時,容易產生裂紋。為此,對高強度鋼進行組織微細化,使高強度鋼在提高強度的同時,不易產生裂紋。並且生產成本沒有增加。現在已經開發出980MPa級以上的超高強度鋼材,並用於保險杠防撞梁和車門抗衝擊梁。
另一方面,用於汽車的鋼鐵材料的比例逐漸下降。15年前鋼鐵材料占汽車用材的80%,現在已經下降到70%左右。但是,高強度鋼占汽車用鋼的比例升高,接近60%。今後,將鋼板加熱後進行衝壓成形,然後快速冷卻使部件強度有飛躍提高的熱衝壓技術、將不同厚度的部件進行拼焊的技術以及使部件具有不同強度的局部淬火技術將會得到擴大應用。
因此可認為,作為汽車用材的、具有綜合優良特性的鋼鐵材料(特別是高強度鋼)的需求,今後不會大幅度下降。鋼鐵材料將繼續保持在汽車用材方面的優勢地位。
3.2鋁材:輕量化的最佳材料
鋁材是汽車輕量化材料的強力候補材料。鋁材很輕,其重量是鋼材的1/3、並且耐蝕性、導熱率、鑄造性都好於鋼鐵。鋁材目前已經主要用於發動機、車輪、變速箱、懸架彈簧等鑄鍛部件和擠壓成形部件。最近,鋁材已經用於保險杠防撞梁、車門抗衝擊梁、發動機罩、車門、擋泥板、行李箱蓋、車頂等部位。此外,為提高強度的熱處理鋁合金材的用量也不斷增加。過去為了避免與鋼鐵材料的接合,鋁材僅限於用於與車體通過螺釘接合的部件。現在,為應對輕量化的要求,車頂等非螺釘接合部件也使用了鋁材。根據達科市場諮詢公司(Ducker Worl dwide)的預測,2025年小型車85%的發動機罩和46%的車門將實現鋁材化。
目前鋁材在汽車上使用的重量比例最高不超過10%左右,但隨著燃油效率的不斷嚴格化以及對汽車輕量化要求的提高,鋁材用量將會逐漸增加。美國主要推進鋁材在發動機罩的應用,歐盟還擴大鋁材在發動機罩以外部位的應用,日本也有若干鋁材應用的事例。
2015-2025年,北美一輛汽車的鋁材用量的年增長率為2.4%,到2025年達到每輛車500l b(227kg)。2016-2025年,歐盟一輛汽車的鋁材用量年增長率為1.9%-3.0%,到2025年達到178.2-196.2kg。根據這個預測,美國的美鋁公司等鋁材大企業將在生產汽車鋁材設備方面進行大額投資。日本大型鋁材生產商UACJ與荷蘭肯聯鋁業(Constellium)於2016年合作建成年產10萬噸的鋁材汽車面板生產廠。UACJ預測,2020年汽車用鋁板的市場需求量將達到150萬噸,是2012年(不到10萬噸)的15倍。
另一方面,在鋁材用作汽車材料時存在幾個需要解決的問題。首先是,鋁材生產消耗大量電力,因此生產成本大於鋼材。按重量計算,鋁材成本是鋼材的3倍;其次是成形困難,鋁材的伸長率小於鋼材,並且容易產生皺摺和裂紋,衝壓加工比較困難;第三,接合成本高於鋼材,由於鋁材的導熱率和導電率大於鋼鐵,所以,在進行點焊時,施加的壓力約為鋼鐵材料的2倍,使用的電流約為鋼鐵材料的2-3倍。
對於鋁材生產成本高的問題,如果使用循環利用材料,可以降低鋁材的生產成本。使用循環利用材料生產鋁材時,能耗只有利用新原料生產鋁材的2%。
對於成形和接合困難的問題,鋁材廠和汽車製造廠正在進行鋁材中添加Cu,提高成形性和接合性的研究。關於鋁材與鋼材等異種材料的接合技術,使用黏結劑的自沖鉚接(self-piercing riveting)等機械接合方法和利用摩擦能的攪拌摩擦焊接方法受到關注。目前馬自達和本田汽車已經將攪拌摩擦焊接技術用於鋁合金行李箱蓋與鋼板折葉的接合以及副車架用鋁材-鋼板的接合。
根據用途,在車體適用部位使用適宜的鋁材對於車體鋁材化十分重要。在進行鋁材用途開發的同時,改進加工等相關技術,將會擴大鋁材在車體的應用空間。可以預計,鋁材作為汽車外板的使用比例將會提高。
3.3 CFRP:作為結構材料實現輕量化
3.3.1 CFRP作為輕量化材料的優點
汽車輕量化的另一個良好的候補材料是CFRP。目前,CFRP已經用於汽車的內裝部件和外裝部件。其用量是汽車總重量的10%。最近,玻璃纖維強化樹脂也開始用作汽車結構材料。強化樹脂作為輕量化材料有如下優點。
1)比鋼材輕,但為了保持一定的剛性需要增加樹脂厚度。從保持剛性的要求考慮,鋁材替代鋼材可取得減重50%的輕量化效果,樹脂替代鋼材可取得減重70%的輕量化效果。
2)成形性良好,容易實現部件整體化。容易進行期望的設計。此外由於部件數量下降,可減少製造工作量。
3)可與高剛性材料構成複合材料。由於與高剛性材料複合,彌補了樹脂剛性低的缺點,可利用樹脂複合材料實現輕量化效果。特別是CFRP,由於具有很高的剛性,預期可獲得減重70%-80%的輕量化效果。因此可作為汽車結構材料得到正式應用。
3.3.2 CFRP及成形時間短的SMC工藝
CFRP是高強度、輕型材料,已經用作飛機材料。現在,波因公司的主力中型機B787所用材料的一半是CFRP。飛機用的CFRP中的碳纖維是用具有優良強度等性能的正規纖維束製造出來的。但根據材料特性和材料成本的要求,除了天然氣、氫燃料罐等部分部件材料CFRP的碳纖維,其他汽車材料CFRP的碳纖維是用性能較差但成本很低的粗纖維製造出來的。
CFRP的原材料和製造方法有許多種,大致可分為三類:1)使用高壓釜對片狀CFRP進行加熱硬化的聚酯膠片生產工藝;2)對液態樹脂滲入的碳纖維織物進行加熱硬化的樹脂傳遞模塑成型工藝(RTM);3)對短碳纖維樹脂複合薄片進行壓力成形和加熱硬化的片狀模壓成型工藝(SMC)。材料強度由高到低的順序以及成形時間由長到短的順序都是:聚酯膠片工藝、RTM、SMC。
CFRP的原材料和製造方法的多樣化,使CFRP在車輪部件有了廣泛的用途。例如,成形時間短的SMC,用壓力成形方法可以製作形狀複雜的部件。卡車車頂、後擋板、後車門骨架等形狀複雜的部件已經採用CFRP材料和SMC工藝製作。SMC工藝應用範圍的擴大,促進了CFRP市場的擴展,預計到2025年CFRP的市場需求量將達到8.5萬噸。
在技術方面,不僅SMC,各種CFRP成形工藝都有需要解決減少材料性能波動和縮短成形時間的問題。在經濟性方面,CFRP的製造成本是鋼材的10多倍,是鋁材的3倍左右,這成為CFRP應用的最大障礙。
3.3.3 CFRTP的真正應用尚需時日
目前的情況是,SMC工藝由於成形時間仍然較長,所以還不能做為量產汽車部件的方法。目前使用較多的CFRP是環氧樹脂等熱硬化樹脂。樹脂硬化製作部件的最短時間也需要5min以上。為達到汽車生產一個工序一分鐘作業時間的節奏,就必須增加CFRP的成形模具,導致投資增加。此外,CFRP部件製作的成材率很低,並且不能使用點焊等簡單的二次加工方法。另外,CFRP的循環利用技術尚未建立。所以目前CFRP僅用於一部分賽車和高級車。
目前,用熱可塑性樹脂替代熱硬化樹脂的碳纖維增強熱塑性複合材料(CFRTP)受到人們的關注。CFRTP熔融後僅需冷卻,在一分鐘內即可完成成形,並容易進行點焊和表面裝飾加工。現在已經開發出的CFRTP產品有,含有細碳纖維的粉末注塑成形品和短碳纖維、長碳纖維與熱可塑樹脂的壓力成形品。這些CFRTP成形品的材料特性雖然不如CFRP,但根據其強度等特性可用於製作汽車外板和電裝品等部件。日本正在推進採用CFRP和CFRTP製作車體結構和外板,可使部件重量減輕30%(400kg)。
目前,CFRTP還存在量產化技術和降低生產成本等必須解決的問題。並且,與其他材料不同,CFRTP具有材料特性的各向異性,因此在進行材料設計時,必須考慮到材料特性的各向異性。此外,熱可塑性樹脂黏度大,所以存在是否完全浸透到碳纖維中的問題。即使熱可塑性樹脂完全浸透到碳纖維中,還存在樹脂是否完全包敷住碳纖維的問題。關於碳纖維的長度,碳纖維越長,越能發揮碳纖維的特性,但碳纖維越長越難使碳纖維均勻分布在樹脂中,並且使成形加工變得困難。
關於CFRTP低成本化的問題,目前德國和日本的研究機構正在進行長纖維增強熱塑性複合材料(LFT-D)工藝研究。LFT-D工藝是從粗纖維和樹脂粉末的材料供給到利用CFRTP製作成最終產品的系列化生產工藝,實現了短時間成形和低成本化生產的目標,但該工藝的實用化尚需一些時間。
4異種材料接合技術是汽車用材多元化不可或缺的技術
汽車製造廠為了進行新一代汽車開發,現在已經對汽車不同部位新材料的應用問題進行研究。汽車製造廠的用材方針是最大限度地發揮材料特性,將「把現有材料特性用盡」作為汽車輕量化的方針。當「把現有材料特性用盡」仍不能獲得滿意的輕量化效果時,再研究新材料的正式應用。
另一方面,隨著燃油效率法規的強化,對汽車輕量化的要求不斷提高,將不斷推進對鋁材和CFRP的應用研究。鋁材和CFRP的應用,形成汽車材料的多元化,雖然要經過一定時間,但這是不可逆轉的發展趨勢。
汽車材料多元化的推進過程中,異種材料接合技術是不可或缺的技術。通過異種材料接合在抑製成本升高的同時,還可以利用異種材料的特性。但是,由於不同材料的熔點、熱膨脹率、氧化性的不同,異種材料接合部件的材料界面上容易產生裂紋、鏽蝕,導致強度下降。因此要研發出基於各種材料優缺點的異種材料接合技術。
特別是,異種結構材料接合技術十分重要。僅用鉚釘對鋁材和鋼板、金屬和CFRP進行機械接合不能保證足夠的強度,所以一般多用鉚接與黏結劑並用的方法進行接合。但目前尚未建立對粘結接合的檢查和評價方法。此外,異種材料接合後,接合材料界面的劣化過程也不是十分清楚。另外,接合材料的循環利用問題也是今後需要研究的方向。由於CFRTP不是熱硬化材料,所以對CFRTP與金屬等異種材料的粘結接合還處於研發階段。
異種材料接合技術的進步及其可靠性的提高,將是汽車材料多元化、實現汽車輕量化的關鍵。
來源:世界金屬導報
- END -

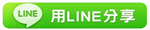
※Hackrod利用眾籌研發汽車設計軟體 旨在提供3D列印定製版車輛
※助力下一代電池材料設計 韓國研究組發現汽車充電電池效率低的原因
TAG:蓋世汽車新材料 |