金屬3D列印技術在液壓元件上的應用
點擊「iHydrostatics」,發現不一樣的靜液壓世界
i
欄目說明
#i前沿#欄目精選靜液壓傳動領域最前沿資訊,為你傳遞最有價值的行業動態。iHydrostatics致力於為你構建最具價值的靜液壓傳動領域內前沿資訊平台!
前沿
原文作者丨Ray I. Scroggins翻譯整理丨籍達
內容審校丨李春光排版編輯丨馬艷雙
與發動機、電動機和機械作動器相比,液壓泵、液壓缸及其他液壓作動器具有更高的功率密度,而液壓閥也可以輕而易舉的實現方向、速度、力和扭矩的控制。
然而雖然液壓的應用領域不斷擴大,但其加工製造方法卻沒有根本性的改進。金屬的3D列印技術,通過改進閥塊閥芯等部件的設計和生產工藝,為液壓技術的發展提供了新的機遇。
3D列印技術已經不僅僅局限於起初的塑料材料,在金屬材料的應用方面,3D列印也正在蓄勢待發。雖然對於大批量生產來說,3D列印在實用性和成本效益方面優勢不大,但與傳統的機加工藝相比,3D列印對於小批量及特殊設計的金屬液壓元件來說,卻有得天獨厚的優勢。
1、可實現效率和性能最優化的產品組合設計。
2、內部流道優化,實現更大的通流能力和更低的壓損。
3、可快速製作多個樣品,以便測試驗證最優方案。
4、3D列印可使用的耗材多樣,如不鏽鋼(鋁,鈦,以及其他正在開發中的新材料等。)
5、3D列印還可以規避工藝孔堵頭處潛在的漏油風險。
儘管液壓元件都可以通過傳統的加工製造工藝來製作,但傳統的製造是一種減材工藝,即對耗材進行減材製作,比如通過數控加工技術,將多餘的材料去除,最後得到需要的形狀,所以為了節省加工費用,很多多餘的材料並沒有被去除,最終導致零件重量的增加。
切削加工技術在產品設計方面同樣具有局限性。傳統閥塊中的內部流道必須精確定位以防止流道交叉,而且必須確保流道的壁厚以便具有足夠的強度承受高壓。加工流道所必須的工藝孔必須堵住,但這也增加了泄露的風險。
相比之下,3D列印是一種增材製作工藝,通過逐層列印的方式來構造零件形狀。通過3D列印技術,閥塊內部的流道可以得到精確的定位,並優化流道的形狀和尺寸。目前為止,諸如閥芯等元件的流道都是圓柱形的,這是因為他們是通過旋轉刀具加工而成的。但是通過逐層列印的方式,設計者可以設計出許多傳統製作方法所無法實現的方案。
例如流道截面可以做成正方形的,與圓形截面流道相比,方形截面的通流能力可以提高20%。通過優化流道設計,可以以更小的閥塊體積實現更大的流量方案。閥塊內部的交叉流道同樣也不再必須從閥塊外部鑽孔加工,額外的堵頭也就不再需要了。
這種工藝使用計算機控制,通過激光融化,層層的堆積金屬材料以形成想要的零件,義大利Aidro SrL公司總經理Alberto Tacconelli指出,目前最適合液壓元件的3D列印技術是粉末冶金法,通過直接金屬激光燒結(DMLS)或選擇性激光融化(SLM)。
DMLS通過高能激光將金屬粉末加熱,使其能夠在分子水平上發生融合。燒結金屬材料的孔隙率是可控的。而且DMLS可以應用於各種類型的合金材料,這使得樣件可以使用與正式的產品相同的材料製作。而使用SLM技術,金屬粉末不僅可以融合在一起,通過使用高功率密度的激光,金屬材料融合的更加均勻,同時由於孔隙率降低,SLM製成的部件擁有更好的強度,對晶體結構的控制也更加出色。但是這一工藝目前僅可應用於單一的金屬粉末材料。
何時使用金屬3D列印技術?
Tacconelli列舉了以下幾個因素,來綜合考慮是否使用3D列印技術生產液壓元件。
1)數量。傳統的加工技術更適合大批量生產,然而3D列印技術對於小批量生產的專用液壓元件更加經濟實用。
2)生產周期。像CNC加工這種減材工藝在金屬毛坯的基礎上可能需要30到60天才能完成製作,如果需要鑄造的話,整個過程甚至可能需要6到12個月。採用3D列印技術,液壓元件在幾天內就可製作完成。
3)樣件。利用3D列印技術,可以同時製作不同的樣件,以便評估最優的設計方案。
4)材料。液壓元件必須具有足夠的強度和耐腐蝕性,以承受高壓,3D列印可以提供更廣泛的材料選擇,包括不鏽鋼(AlSl316L),鋁,鈦(Ti6Al4V),鉻鎳鐵合金(625或718)和馬氏體時效鋼等。
材料性能
由於液壓元件的3D列印相對來說是一個比較新的應用領域,這就產生了一個問題:與傳統工藝相比,3D列印的元件材料性能如何?儘管典型的機械性能如拉伸強度、屈服強度、彈性模量等我們有跡可循,但除此之外液壓系統中經常遇到的高壓及壓力衝擊我們也必須考慮在內。
通過適當的材料選擇和設計,液壓元件可以承受這些壓力,但液壓系統也會遇到衝擊和壓力脈動,這些脈動對元件的要求更高,例如閥塊通常由球墨鑄鐵或其他韌性材料製成以承受壓力脈動,但這些材料並不適用於增材製作工藝,鐵和碳鋼材料同樣如此,這是因為原材料必須以粉末的形式存在。
Tacconelli指出,並不是所有的金屬都適合3D列印,Aidro通常使用鋁或者不鏽鋼來3D列印液壓閥塊,這些材料的機械性能等同於甚至比鋼材更好。而且從結果來看,可以達到設計要求。
該公司使用有限元法(FEM)來模擬元件的受力情況,並對元件做功能性的模擬。Tacconelli解釋說,通過良好的設計方法,我們可以3D列印一個液壓閥塊,並足以承受液壓系統中的壓力衝擊,對於在有限元分析中顯示存在潛在風險的部位,我們還可以改變通道形狀,或者增加壁厚來規避風險。3D列印完成後,我們首先會做內部測試,然後在米蘭理工大學的支持下做進一步的測試。
特定的3D列印工藝及設備同樣會影響結果,Tacconelli指出,經過仔細評估,我們選擇了直接金屬激光燒結工藝,這可以保證液壓元件更高的精度要求和更好的表面光潔度。他補充說,可靠的設備以及金屬粉末可以確保工藝的可重複性和產品的質量。
我們可以有效的利用影響部件性能的各種因素。Tim Simpson是賓夕法尼亞大學機械及工業工程學教授,他同時還是材料直接數字成型工藝創新中心的聯合主任,他指出,每一種材料的受熱及冷卻過程都是不同的,這取決於金屬粉末相互作用時的速度和能量,這些因素會影響材料的微觀結構,進而影響其材料特性,如強度,剛度,和彈性等。
Simoson同樣擔任2015年ASME增材製造和3D列印展會主席,他指出,大多數3D列印的產品還需要進行熱處理,以消除由於激光的反覆加熱和冷卻而產生的應力。他解釋說:「傳統的減材工藝,是在所需材料的基礎上,製作出所需要的形狀,而3D列印則是先製作出零件形狀,然後進行熱處理或固溶退火,最後得到你所需要的零件。
之前不適用於增材製造的一些合金在3D列印領域的應用也取得了一些進展,比如高強度不可焊接的鋁合金(如Al 7075或Al6061),這些合金在3D列印過程中會發生嚴重的熱裂,為了解決這一問題,HRK實驗室開發了一種新技術,將這些金屬粉末與納米顆粒結合在一起,避免了熱裂的發生,從而形成具有全合金強度的3D列印零件。
如前所述,3D列印最適合小批量生產,但是其可以通過優化設計進而減輕零部件質量的優勢,使得他同樣適合要求高精度和低重量的應用,比如航空航天和醫療設備領域,另外農業機械是他的另一個重要的應用領域,比如可以利用3D列印製作各種樣件,模具,備件以及小批量生產的專用零部件。一般來說,3D列印也適用於那些依靠傳統製造技術難以製作的更緊湊的零件。
典型應用
3D列印技術目前已經應用到了許多類型的液壓元件的生產,例如,Aidro公司用不鏽鋼材料3D列印了一個控制單作用油缸的液壓閥塊(圖1)。與傳統零件相比,他們可以節省空間並通過優化內部流道來降低壓力損失,由於不需要額外的工藝孔,因此也就消除了油液泄露的風險。
圖(1)用不鏽鋼材料3D列印的液壓閥塊,不僅尺寸更小,而且提高了閥塊流道的通流能力。(由Aidro ArL提供)
此外,3D列印還改進了疊加式液壓閥的設計和生產(圖2)。直動式減壓閥由鋼製成,並通過鍍鋅來提高耐腐蝕性,如果客戶僅僅需要少量的閥,若採用CNC加工,則交貨周期太長,成本太高。相反,利用3D列印技術,零件重量不僅可以減輕60%,而強度也可以媲美機加工零件,3D列印生產的零件與機加工零件在250bar壓力下的測試結果相差無幾。
圖(2)左邊的閥塊是由機加工製作,並經過了鍍鋅處理來提高耐腐蝕性,右邊的閥塊由3D列印而成,重量減輕了60%,但強度相當。實際上,傳統的機加工藝也可以將重量做的更輕,但成本卻要高得多。(由Aidro ArL提供)
多年以來,英國布里斯托爾的Domin Fluid Power公司一直在開發專門通過增材製造設計生產的液壓閥、泵以及更複雜的子系統。該公司今年上半年將推出其主導產品:直驅式液壓伺服閥( 圖3)。
圖(3)不久將推出的這款直驅式液壓伺服閥,價格具有更強的競爭力。(由Domin Fluid Power Ltd.提供)
Domin公司總經理Marcus Pont表示,相比於目前最先進的伺服閥,新型伺服閥在尺寸,效率,重量和流量等方面都有所改進,並且價格也更具競爭力。
Pont表示,與一個重要的競爭產品相比,Domin伺服閥流量增加了25%,泄露減少了20%,體積減小了25%,重量減輕了15%,同時零件的數量減少了40%,這些都大大簡化了生產製造工藝。
圖(4)這個為農機製作的3D列印閥塊相比於傳統工藝的零件,尺寸減小了一半,重量減輕了75%。(由Aidro ArL提供)
另一個來自Aidro公司的例子是用一個在農機上的液壓閥塊,圖(4)。這個閥塊用兩個電磁閥和兩個先導單向閥來控制一個雙作用油缸,3D列印的閥塊可以節省一半的尺寸和75%的重量。該閥塊由AlSi10Mg,6000鋁合金製作,具有良好的強度和熱性能,重量輕並可進行靈活的後處理。3D列印通常可用來製作這種具有薄壁且形狀複雜的零件。
Aidro公司的Tacconelli報告說,壓力測試顯示,3D列印液壓閥塊在拉伸強度,伸長率,衝擊韌性和硬度等機械性能方面的表現甚至比傳統閥塊更加出色,同時因為內部通道的交叉點處沒有90°的折彎,所以它的通流能力更強。
圖(5)這種3D列印閥塊做成一個整體,用來替代由17個零件組成的裝配體,重量減少了70%,卻仍可以承受相同的壓力和疲勞測試。(由Penn State CIMP-3D提供)
在賓州州立大學的CIMP-3D上,一個液壓閥塊被3D列印成一個整體,用來替代由17個零件組成的裝配體(圖5),重量減少了70%,卻仍可以承受相同的壓力和疲勞測試。
Aidro設計了一個全新的閥芯,通過3D列印,用方孔代替圓孔(圖6),這增加了閥芯內的通道面積並減少了壓降。
圖(6)原閥芯(左)有圓孔,需要CNC加工,3D列印閥芯具有較大面積的方孔以減少壓降。(由Aidro SrL提供)
這些只是3D列印技術在液壓領域應用的冰山一角,來自Infinium Global Research的報告顯示,全球金屬3D列印市場2017至2023年間預計年增長率可達33%,液壓領域的應用有望成為金屬3D列印市場重要的組成部分。
新技術的出現,總是那麼的讓人心潮澎湃!對此,朋友們怎麼看?有什麼見解?歡迎留言說說!
參考資料
【1】http://www.hydraulicspneumatics.com/hydraulic-valves/produce-better-hydraulic-components-metal-3d-printing
液界聯盟會員註冊
與液界精英一起玩轉液壓界
聯盟在召喚,期待專註液界的你加入!
關於iHydrostatics
工程化解讀最前沿的液壓技術

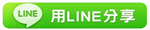
TAG:iHydrostatics |