油田廢水常用處理技術匯總
我國大部分油田都是採用注水的方式(注水壓裂)開採的,每生產1噸原油約需注水2~3噸,因此,往往在原油開採上來,採油廢水也隨原油進入集輸系統中。特別油田生產後期,原油含水可高達90%以上。此外,在鑽井、洗井過程中,也有廢水產生,油田廢水就是原油開採全過程中所產生的廢水的統稱。油田廢水只有經過處理才可以回注到地層中,本文總結了油田廢水常用的處理方法。
油田廢水的來源及水質特點
油田廢水來源於油氣開採中鑽井、採油、洗井等過程,因此油田廢水成份複雜,為有機、無機混合物,還涉及到有機物在水相與油相的分配,經過蒸汽熱采、三次採油和其它處理工藝後,油中膠質瀝青質,脂肪酸類物質,硫醇、類物質等在一定條件下以一定的形態進入水相,使水中有機物與油中有機物相對組成發生較大的變化。油中脂肪酸類物質及膠質瀝青質是天然乳化劑,在熱采、三次採油和地層運移過程中與油形成乳化油,所以廢水中的油主要以乳化油和遊離態油的形式存在,在沉降站進行油水分離後仍有相當部分殘留在水相中。根據有關分析結果表明含油廢水中的主要成份有重質原油、脂肪酸類物質、破乳劑、硫醇類物質、膠質類物質、硫化物、碳酸鹽、硫酸鹽等。因為水中殘留的有機物和無機物組成複雜,給油田廢水處理帶來了一定的難度。儘管各油田水質各異,但總體看來具有以下特點:
l礦化度高,加速了腐蝕速度,同時也給廢水生化處理造成困難;
l含油量高,遠大於各種出路所要求的水質標準;
l含大量微生物,細菌大量繁殖不僅腐蝕管線而且還造成地層嚴重堵塞;
l含有大量生垢離子,采出水中含有SO42-、 CO32-、Ca2+、Mg2+、 Ba2+等易成垢離子;
l懸浮物(注聚區聚合物)含量高、顆粒細小、容易造成地層堵塞。
各廢水類型的具體來源及水質特點列於下表。
油田廢水含油量高,水體中油污染物的成分和存在狀態也不同,油在油田廢水水體中存在形式大致有以下5種:
油田廢水的危害
油田開採過程中會產生大量廢水,尤其是大規模油田開採,采出液中含水量相對更高。油田廢水是組成複雜的液態混合物,其主要成分有水、原油、可溶性氣體、固態懸浮物、電解質、細菌和各種油田化學添加劑等物質,直接排放,不僅會對環境造成嚴重危害,污染地表水和農田,導致動植物的死亡和人類潛在疾病,給當地人民的生活造成嚴重危害。而且,油田廢水中酸性氣體或鹽類會加速管線設備腐蝕;油田廢水中固體懸浮物會堵塞地層;油田廢水中工業細菌會腐蝕管線、堵塞管線,並使水質惡化。
油田廢水處理技術
油田廢水處理,主要是指將原油開採過程中產生的廢水回注地層前,將水中的原油、懸浮雜質、有害的化學離子分離開來,以免對地質結構和地表環境造成污染和破壞。油田廢水處理技術有物理法、化學法、生物法以及綜合性的物理化學方法。
物理法
物理法是通過物理作用分離和去除油田廢水中不溶於水的懸浮物的方法。物理處理法所用的設備大都比較簡單、操作方便,分離效果良好,使用極為廣泛,根據物理作用的不同廢水處理主要有重力分離法、離心分離、壓力沉降、粗粒化法以及過濾法等,都是利用不同的水處理設備將油田廢水中有害物質除去或降低其含量。
1、重力分離法
重力分離也叫重力沉降、自然除油,基本原理是利用油田廢水中油、水兩相的密度不同,使油水混合物在重力場中發生相對運動,最終實現油、水分離。重力分離的設備為重力隔油罐,適用於油田廢水的前期處理。含油廢水進入隔油罐後,大的油滴在浮力的作用下自由地上浮,乳化油通過破乳劑(混凝劑)的作用由小油滴變成大油滴。在一定的停留時間內,絕大部分原油浮升至隔油罐的上部而被除去。因其處理量大運行費用低,管理方便等優點而被廣泛應用,其缺點是佔地面積大,基建投資高,對乳化油的處理效果不好,廢水停留時間長。目前國內外在重力分離設備上已取得了一定的進展,已由自然沉降除油發展到斜板除油,加設斜板,增加分離設備的工作表面積,縮小分離高度,即利用「淺層沉澱」原理提高除油效率 。如美國Quontek公司研製的聚結板油水分離器(CPS)。最近,石油大學對CPS進行了改進,在其基礎上引進了斜板技術,發明了斜通道波紋波紋板油水分離器和翼斜板油水分離器,進一步提高了板式分離器的效果。
2、離心分離
離心分離也是利用油水密度差,在液流高速旋轉時,受到不等離心力的作用而實現油水分離。其特點是設備體積小、分離效率高。但其對原油相對密度大於0.9的含油廢水適應能力差。
3、壓力沉降
壓力沉降除油技術是在除油設備中裝填有使油珠聚結的材料,當含油廢水經過聚結材料層後,細小油珠變成較大油滴,加快了油的上升速度,從而縮短了廢水停留時間,減小了設備體積。其特點是設備綜合採用了聚結斜板技術,大大提高了除油效率,但其適用於來水水量變化、水質變化的能力要比隔油罐差。
4、粗粒化法
粗粒化是指油田廢水通過粗粒化除油罐時,粗粒化材料使油田廢水中的油珠粒徑由小變大的過程。粗粒化法主要在重力沉降除油工藝前使用。
聚結(粗粒化)除油器
5、過慮
過濾技術是根據濾後水質的要求不同分為粗過濾、細過濾和精細過濾。水質推薦標準,懸浮物固體含量為1.0~5.0 mg/L,顆粒直徑為2.0~5.0μm。過濾技術利用多孔介質從水中分離不溶解固體的技術,常用於廢水的末段處理,所用的過濾器有重力過濾器和加壓過濾器。過濾的核心技術是濾料的選擇與再生。採用粒狀材料為濾料(如石英砂、核桃殼和無煙煤等)通過潤濕聚結和碰撞聚結作用,除去廢水中的油和懸浮物。其優點是出水水質好,設備投資少,缺點是運行費用較高,適應負荷變化能力弱,易堵塞。而且,由於濾料粒徑受到限制無法進一步減小粒料粒徑來提高過慮精度和效率。近年來,隨著纖維材料的應用和發展,以纖維材料為濾料的纖維濾料過濾器,一般處理精度可達到出水水質含油小於1.5~2 mg/L,懸浮物粒徑小於5μm。
油田污水深度處理技術
化學法
化學處理法是指利用化學反應,通過向廢水中加入化學藥劑或採用電化學等方式除去有害物質的方法。
1、絮凝沉澱法
絮凝法主要是通過向廢水中加入絮凝藥劑,使廢水中的懸浮物形成絮凝物聚結下沉,該過程不僅可以除去廢水中的懸浮物和膠體粒子,降低COD值,而且,還可以除去細菌等。是指在絮凝劑的作用下,油田廢水中的膠體和細微懸浮物發生靜電中和、吸附或橋接,最終生成絮凝體被除去。化學絮凝法作為預處理技術在各大油田中被廣泛應用,常與氣浮法聯合使用。
絮凝法的技術核心在於研發新的化學藥劑,來提高去污效率,擴展去污範圍。油田水處理用的絮凝劑主要分為無機、有機和生物絮凝劑三類。
無機絮凝劑主要有無機化合物(如硫酸鋁、明礬、三氯化鐵、硫酸亞鐵等)和無機聚合物(聚合氯化鋁(PAC)、聚合硫酸鋁(PAS)、聚合硫酸鐵等高聚物),其中無機聚合物是60年代後發展起來的一類新型絮凝劑,由於其功效成倍提高,有逐步成為主流絮凝劑的趨勢。
有機絮凝劑有低分子量的陽離子聚合物(如聚胺等)和高分子量的聚合物(如聚炳烯醯胺及其衍生物)。與無機高分子絮凝劑相比,它的用量少,產生的絮體大、沉降速度快、受共存鹽、pH值和溫度的影響小,效果明顯、且種類繁多,在油田水處理中得到廣泛應用。在企業的日常油田廢水處理中,運用化學絮凝法時,大多以丙烯醯胺和丙烯酸的二元及三元共聚物作為有機高分子絮凝劑來吸附油污。但由於聚丙烯醯胺具有毒性、難生物降粘,目前天然改性高分子絮凝劑和兩性高聚物等環保型的無害水處理劑的研究倍受人們關注,如Doyle D.H.等人則研製出了新型的聚合物有機粘土來去除油污中的膠體和溶解性物質。國內新合成的以F691粉(主要成分水溶性多聚糖、纖維素、木質素單寧)為原料的新型高效陽離子絮凝劑FNQD,國外新推出的水處理劑(DTC),用於美國墨西哥灣和北海油田水處理中,輕易地將處理精度僅能達到60~70mg/L的水處理系統提高至1~2mg/L,效果十分明顯。
但也有很多因素限制了絮凝法的應用,主要的有:現場絮凝操作工序複雜;影響混凝效果的因素多;當懸浮物含量較高時,使絮凝劑的消耗量增大,產生的污泥量也隨之增大;壓裂余液殘存的粘度大大減緩了絮凝劑的擴散速度和絮凝產物的沉澱速度;對水溶性有機物的去除效果差等。
近年來,利用生物技術,通過微生物發酵、抽提、精緻而得到的一種新型生物絮凝劑,由於具有無毒、高效和可生物降粘等特點,對水資源的保護有十分重大的意義,是很有發展前途的綠色絮凝劑。
2、電化學法
運用電化學法處理廢水,不僅能降低成本,且不會造成污染。油田廢水處理的電化學法主要有兩種方法,分別是內電解法和電化學氧化還原法。
內電解法(又稱為「鐵-碳法」),一般以 Fe 作為原電池的陽極,以油污中的惰性導電物質作為陰極。通電後,陰極和陽極會發生一系列的化學反應,最後生成具有絮狀結構、吸附力極強的Fe(OH)2、Fe(OH)3。由於密度較大的油污會阻礙內電解法的化學反應速率,故此方法只適用於處理油污過程中較靠後的階段。內電解法在處理油污的過程中,化學反應所產生的電流還能使油污中的微生物的新陳代謝加快,提高微生物分解油污的效率。
電化學的氧化處理主要有直接氧化處理和間接氧化處理兩種。電化學的直接氧化法是通過電解作用產生的強氧化物質直接與被氧化物發生反應,從而分解油污中的酸性硫化物等無機物質。而間接氧化法則是不需要通過電解作用產生具有強氧化性的物質,只是把氯氣作為氧化物質注入油污中,間接氧化有助於去除油污中的苯、苯酚類物質。電化學氧化法起作用的主要是氧化物質,而電化學還原法是與氧化法相對的,直接電解油污中的有機物,這樣可以有效降低油污中的硫化物。電化學法以其低成本、污染少等優點得到油污處理企業的廣泛應用。
3、化學氧化法
化學氧化是轉化廢水中污染物的有效方法,能將廢水中呈溶解狀態的無機物和有機物轉化為微毒、無毒物質或轉化成容易與水分離的形態。化學氧化是利用氧化劑(如O2、O3、Cl2、ClO2、NaClO、H2O2、KMnO4、K2FeO4、漂白粉等)氧化分解廢水中油和COD等污染物質以達到凈化廢水。
秦芳玲等採用臭氧氧化法對油田作業廢水進行處理,當廢水的COD為1064mg/L,pH為3.0、每小時投加臭氧10g/L,廢水的COD去除率為69.1%。臭氧催化氧化技術的工藝過程簡單、反應周期短、設備佔地面積小、經濟性好,這些特點使得在壓裂廢水處理過程中研究催化氧化工藝具有很好的應用前景和經濟效益。但在應用過程中,臭氧的利用率及臭氧發生器的效率都亟待提高,催化劑不能能反覆使用及處理成本高的問題都是制約此方法廣泛應用的問題。
因次氯酸鈉具有強氧化性,在水處理中得到廣泛使用。彭鴻飛等人採用二氧化氯催化氧化的方法,廢水的COD去除率達到92%,達到國家工業水排放的二級標準。但二氧化氯法存在的問題主要是二氧化氯用量較大,費用較高,而且引入大量的氯離子。
漂白粉的有效成分是Ca(ClO)2,它在水中易放出氧和氯氣使其具有很強的氧化性,可氧化廢水中的有機物,進而降低COD。漂白粉還具有漂白作用,可以使水樣變得澄清透明。此外,漂白粉通常含有Ca(OH)2,CaCl2等雜質,它們可以作為助凝劑,提高混凝效果。高璽瑩等針對大慶油田壓裂施工過程中剩餘壓裂液的實際情況確定了NaClO氧化―漂白粉氧化―混凝―Fenton氧化―活性炭吸附―TiO2光催化氧化,六步處理工藝,處理後的廢水能達標排放。其中,漂白粉氧化條件為:氧化所需pH值為11,漂白粉投加量0.75g,氧化時間為80min,COD去除率達到26.51%。
4、高級氧化技術
光化學催化氧化法
光化學氧化法是近20多年來發展迅速的一種高級氧化技術,以半導體材料(如TiO2、Fe2O3、WO3等)利用太陽光能或人造光能(如紫外燈、日光燈等)使廢水中的油和 COD 等污染物質降解以達到凈化廢水的目的。
做為一種環境友好的催化新技術,它的反應條件溫和、氧化能力強、適用範圍廣,利用該法處理難降解毒性有機污染物已成為國內外研究的熱點。自然光中的部分近紫外光(290~400 nm)極易被有機污染物吸收,在有活性物質存在時即發生強烈的光化學反應,使有機物降解。由於反應條件所限,光化學氧化降解往往不夠徹底,易產生多種芳香族有機中間體,成為光催化氧化需要解決的問題。而光化學氧化和光催化氧化劑結合,可以大大提高氧化效率。根據使用的光催化氧化劑的不同,可以分為均相光催化氧化和非均相光催化氧化。目前在大慶油田等地已開展了非均相光催化氧化的可行性研究及應用。
利用光照射某些具有能帶結構的半導體光催化劑如TiO2、ZnO、CdS、WO3等,可誘發產生羥基自由基(?OH)。在水溶液中,水分子在半導體光催化劑的作用下產生氧化能力極強的?OH自由基,可以氧化分解各種有機物。在實際應用中,TiO2由於化學性質穩定、難溶無毒、價格低,在催化去除難生物降解污染物方面得到了廣泛應用。從含有表面活性劑的採油廢水中去除乳化油的難度大,處理的關鍵在於消除油水界面膜上的表面活性劑,使油滴發生重排、聚集而分離。處於油水界面層的半導體TiO2催化劑受到光照射時可以發生光催化氧化反應,使乳化油破乳,從而去除石油類等污染物。
Fenton 試劑催化氧化法
Fenton 試劑催化氧化法的應用最為廣泛,一般的生化和物化法難以處理的有機污染物,可以用此方法處理。Fenton 試劑的活性成分為氧化劑 H2O2和催化劑Fe2+。在酸性環境下,通過 Fe2+來激活、使 H2O2發生Fenton反應分解出水、氧氣和羥基自由基。通過產生活性極強的羥基自由基(?OH),?OH幾乎能將廢水中的有機污染物氧化降解成無毒或低毒的小分子物質,從而降低COD。
周國娟等採用Fenton氧化-絮凝處理方法對油田採油廢水進行處理研究,結果表明:在採油廢水pH值為3.0時,投加0.2%(質量分數)的 H2O2和20 mg/L的 FeSO4,處理後將廢水pH值調至7.5後,水中的懸浮物含量和含油量分別為2.5mg/L和5.22mg/L,平均腐蝕速率和細菌含量分別為0.011mm/a和10個/ml,達到油田回注水的水質標準。
Fenton法在處理難降解有機物的同時也要解決其帶來的問題,如:產生的 H2O2即有極強的腐蝕性,容易腐蝕設備,氧化過程中產生的二價鐵離子使水的顏色變深,Fe(OH)3沉澱帶來的污泥,反應產生的過量H2O2殘留在水中會抑制羥基自由基的產生,不利於Fenton 反應的進行等。
超聲化學氧化法
超聲化學氧化法利用超聲空化效應產生的高溫、高壓降解水中的有機污染物。在超聲波作用下氣泡與水界面處可產生高達2000K的高溫,但持續幾微秒後該熱點隨之冷卻,溫度變化率達109K/s,並伴有強烈的衝擊波和時速高達400km/h的射流,這樣的環境可以使高能化學鍵發生斷裂,引起「水相燃燒」。在超聲空化過程中,進入空化泡中的水蒸氣在高溫和高壓下發生分裂及鏈式反應,產生 ?OH和H2O2,而空化泡崩潰後 ?OH和H2O2進入本體溶液,易揮發的有機物可進入空化泡內進行類似燃燒化學反應的熱解反應,不易或難揮發的有機物在空化泡氣液界面或本體溶液中同 ?OH和H2O2發生氧化反應。
目前超聲化學氧化法已成為一種極具前景的深度氧化技術。當前的主要問題是如何提高聲能的利用效率,避免有毒中間體或產物的產生。另外,超聲降解與其他降解技術相結合的技術,也具有很大的發展潛力。如將超聲降解與化學氧化、電化學氧化、光催化降解或吸附等技術有機結合,可充分利用超聲波的化學效應和機械效應。
夏福軍等在不改變目前油田現場「沉降-過濾」傳統廢水處理工藝的條件下,在沉降前增加超聲波處理,發現超聲波對大慶汕田聚合物驅含油廢水中的油珠有聚結作用,可加速油珠聚並。當超聲波功率為1000W時,除油率可達到85.8%,功率為600W、沉降時間為18min時,除油率比空白平均提高17.9%,超聲波可明顯改善聚合物驅含油廢水的處理效果。胡松青發現,單純的超聲波處理對油田含油廢水中CODCr的去除效果有限,但若與納米TiO2光催化聯合處理,可明顯提高廢水中CODCr,的去除率,一般超聲/TiO2聯合處理的效率可比單獨光催化處理提高15%,處理65min的CODCr,去除率大於46.8%。
超臨界水氧化法
超臨界水氧化法(SCWO)是一種新型高效、快速的廢水處理技術,它利用超臨界水(T≥374.2℃、P≥22.064MPa)作為氧化有機物的介質,使氣體、有機物完全溶於水相中,氣液相界面消失,形成均相氧化體系。該體系的黏度低、擴散性高、流體傳輸能力得到改善。非極性有機物質可溶解在超臨界水中,與添加的氧化劑發生單相反應並轉化為 CO2和 H2O,其他取代原子如Cl、S、P等會相應轉化為HCl、H2SO4和H3PO4等。該方法具有反應速度快、處理效率高、對難降解有機物的處理具有獨特的效果併兼有不產生二次污染等優點。
超臨界水氧化裝置
王亮、趙朝成等利用間歇式超臨界水氧化反應裝置進行了含油廢水的超臨界水氧化工藝的研究,結果表明反應壓力對COD的去除率影響較小,溫度、時間是影響有機污染物降解率的主要因素;隨著反應時間的延長和溫度的升高,除臨界點附近外,有機物的XDD 去除率可明顯增加,在反應時間為90 s時含油廢水中COD 的去除率達90%以上,由280.8 mg/L降低到150 mg/L左右。勝利油田東辛採油廠的間歇式超臨界水氧化反應裝置設計容積500 ml,設計最高溫度525℃,最高壓力30.399 MPa,其核心部分是一個由不鏽鋼製作的帶電磁攪拌的高壓反應器,採用智能型控制器控制溫度、攪拌強度、加熱功率,攪拌速度在0~1000 r/min範圍。現場的運行實踐表明,超臨界水氧化反應壓力在240~280 MPa較為合適。超臨界水氧化技術可有效地深度處理含油廢水,符合石油工業對含油廢水處理的環保和工業應用要求。當前主要問題是高壓反應器的腐蝕比較嚴重,這是超臨界水氧化技術工業化急需解決的主要障礙之一。
物化法
物化法是運用物理和化學的綜合作用使廢水得到凈化的方法。物理化學法在油田廢水處理中主要有氣浮法和吸附法。
1、氣浮法
氣浮法(又稱浮選法)是較常用的物化法除去油污的方法之一。氣浮法是藉助於浮力,通過很多微氣泡包裹在油污的周圍,把油污帶出水面,最終使油污與水達到分離的目的。由於組成空氣中的微小氣泡大多是非極性分子,易與油污中的油粘合在一起,油污隨著微氣泡的上浮力而被快速帶出水面,這樣,加快油水分離的效率。氣浮法較為常用的有三種方法,分別為:電解氣浮法、機械碎細氣浮法和溶氣氣浮法。由於電解氣浮法存在耗電量大、管理複雜、電極易結垢等問題,故電解氣浮法一般不適用於大型生產。機械碎細氣浮法則是通過機械混合的方式將氣泡分散分布於水中。溶氣氣浮法主要是通過加壓或常壓下將空氣注入水中,並在負壓或常壓的狀態下析出,溶氣氣浮法以其方便、快捷、高效的優勢得到廣泛應用。
Casaday等人研製出一種新型的IGF設計,將機器的撇油裝置和氣體擴散裝置結合起來,能夠去除顆粒較小的油污,極大的改善了出水的水質。新型的IGF設計不僅提高IGF處理油污的工作效率,而且也改進了操作方式,使得管理更加方便、安全,能耗也更低。
2、吸附法
吸附法是利用多孔吸附劑對廢水中的溶解油進行或是物理吸附(范德華力)或是化學吸附(化學鍵力)或是交換吸附(靜電力)來實現油水分離。
油田廢水處理中採用的吸附主要是利用親油材料來吸附水中的油。常用的吸附劑有活性炭、活性白土、纖維素、高分子聚合物及吸附樹脂等。活性炭,由於其吸附容量有限,且成本高,再生困難,使用受到一定的限制,無法得到廣泛應用,一般只用於含油廢水的深度處理。因此,近年來開展了尋求新的吸油劑方面的研究,研究主要集中在兩點:一是把具有吸油性的無機填充劑與交聯聚合物相結合,提高吸附容量:二是提高吸油材料的親水性,改善其對油的吸附性能。Darlington等人就研製出了水不溶性油污和水溶性油污去除法,主要分為兩步,先是用酸活性膨潤土組成的疏水粘土除去水不溶性油污,再用聚乙烯吡啶組成的大孔網路吸附樹脂過濾除去水溶性油污,經過這兩步處理過的油污的水可直接重新利用。該方法不僅經濟,而且吸附量大,在日常的油田廢水處理中得到了廣泛的應用。
3、膜分離技術
膜分離技術被認為是「21世紀的水處理技術」,是一大類技術的總稱。主要包括微濾、超濾、納濾和反滲透等幾類。這些膜分離產品均是利用特殊製造的多孔材料的攔截能力,以物理截留的方式去除水中一定顆粒大小的雜質。特別是超濾,己經在除油的相關研究中取得了—定的進展,逐漸從實驗室走向實際應用階段。
Humphery等人採用Membralox陶瓷膜進行了陸上和海上採油平台的采出水處理研究,經過適當的預處理後取得了較好的效果,懸浮物含量由73~290mg/L降低到1mg/L以下,油含量由8~583mg/L降低到5mg/L以下。Simms等人採用高分子膜和Membralox陶瓷膜對加拿大西部的重油采出水進行了處理,懸浮物含量由150~2290mg/L降低到1mg/L以下,油含量由125~1640mg/L降低到20mg/L以下。美國在1991前後研究了一種陶瓷超濾膜處理采出水用於油田回注,在美國路易斯安那、墨西哥灣的海上和陸上油田進行了小規模生產實驗。采出水先進行投加化學藥劑和沉降分離常規處理後,出水含油為27~583mg/L,經過超濾處理後降為10mg/L以下。美國加利福尼亞的德克薩斯砂道油田位於薩里納斯谷,氣候乾旱,特別是近幾年來地下水位降到臨界點,因此研究決定向地下水注入高質量的水以補充水源的不足,實驗以砂道油田采出水作為水源,用膜法處理使其滿足飲用或灌溉要求。Chen等對0.2~0.8μm陶瓷膜處理油田采出水進行了研究,發現經過Fe(OH)2預處理,可使油質量分數由27×10-6~583×10-6降低到5×10-6以下,懸浮固體由73×10-6~350×10-6降低到1×10-6以下,通過反衝和快速沖洗,膜通量能在較長時間內達到3000L/(m2·h)。
在國內,李永發等用超濾膜處理勝利油田東辛採油廠預處理過的廢水,處理後油截留率為97.7%,能達到低滲透油田回注水標準。梁立軍等用中空纖維超濾器對大慶油田的注水站的回注水進行了試驗,開發的膜組件在通量上比常規的中空纖維組件大3~4倍,在0.08MPa的壓差下,其通量最大。溫建志等採用中空纖維超濾膜對油田含油廢水進行了處理,研究表明,總懸浮固體質量濃度由6.69mg/L下降為0.56mg/L,油質量濃度由127.09mg/L下降為0.5mg/L,達到滿意的效果。王懷林等採用南京化工大學膜科學技術研究所生產的0.2μm和0.8μm陶瓷微濾膜對江蘇真武油田的采出水進行處理,效果很好。
生物法
生物法是利用微生物的生化作用,將複雜的有機物分解為簡單的物質,將有毒的物質轉化為無毒物質,從而使廢水得以凈化。生物處理技術是目前世界上應用最廣泛的廢水處理技術,該技術較物理或化學方法成本低,投資少,效率高,無二次污染,廣泛為各國化工行業採用。我國城市廢水採用生物處理法的佔85%以上,油田採用生物處理法的相對較少,大港油田的氧化塘處理技術就是生物法處理技術。
生物法處理技術的機理就是採用一定的人工措施,創造有利於微生物生長、繁殖的環境,使微生物大量繁殖,在繁殖的過程中,這些以廢水中的有機物作為營養源的微生物通過氧化作用吸收分解有機物,從而使廢水得以凈化。生物法從微生物對氧的需求上可分為好氧生物法和厭氧生物法,好氧生物處理是在水中有充分溶解氧的情況下,利用好氧微生物的活動,將廢水中的有機物分解為CO2、H2O、NH3和NO3-等。
一般好氧反應器分為活性污泥法、生物膜法(生物濾池、生物轉盤、生物氧化塔)、接觸氧化池、好氧塘等。厭氧生物處理的主要特點是可以在厭氧反應器中穩定的保持足夠的厭氧生物菌體,使廢水中的有機物降解為CH4、H2O和CO2等。厭氧反應器主要有厭氧活性污泥法、厭氧濾池、升流式厭氧污泥床(UASB)、內循環反應器(IC)和膨脹顆粒污泥床(EGSB)等。雖然油田廢水COD大多在300~500mg/L,但由於其可生化性差,且含有難降解的有機物,因此,目前國內普遍採用A/O法,即先厭氧後好氧的方法進行處理。序批間歇式活性污泥法(SBR)是融厭氧、好氧為一體的處理方法,因此在研究中用的較普遍。
生物膜法、活性污泥法和氧化塘是運用的比較多的油田廢水處理的方法。
1、生物膜法
經過物化法去除油田廢水中的不溶性有機物質之後,油田廢水的污染物主要為溶解性有機質,而生物膜法可以去除油田廢水中的溶解性有機物質。通過油田廢水與生物膜的直接接觸,生物膜中的固體物質與油田廢水中的液體物質相互進行交換,進入生物膜內的有機物被微生物氧化,同時膜內的微生物數量不斷增加,這樣就促進吸收油污的良性循環,最終凈化了油田廢水。
2、活性污泥
生物法中的活性污泥是一種人工培養的生物絮凝體,主要通過微生物來吸收油田廢水中的溶解性有機物,活性污泥法主要就是用這種生物絮凝體來處理油田廢水。油田廢水一旦進入生物絮凝體中,其中的微生物就開始分解油污中的溶解性有機物質,不僅凈化水質,也為自己的生長、繁殖提供能量。同時,油田廢水中的膠體或不溶性物質雖不能被微生物分解,卻會被生物絮凝體吸附,並與胞外酶起水解反應,最後成為微生物能夠吸收的物質。
3、氧化塘法
氧化塘法是能夠提供有機物分解的大型淺池,塘內有大量好氧微生物和藻類。氧化塘的特點是投資少,管理簡單,但佔地面積較大。氧化塘除暴氣塘需要機械薄氣外,其他各種氧化塘皆不依賴動力來充氧,而是充分發揮天然生物凈化功能。氧化塘一般採用水面自然復氧和藻類光合作用復氧,其運行情況隨溫度和季節的變化而變化。該技術要求廢水停留幾天或幾個月,因此,處理措施的耗時較長。目前,大港油田的廢水處理採用了氧化塘法。
4、其他生物法的組合運用案例
華中理工大學的杜衛東等利用厭氧酸化+接觸氧化的方法對某油田廢水進行試驗研究。該油田廢水BOD5與CODCr的比值小於0.15,可生化性差,在厭氧酸化單元,廢水中的一些複雜有機物在厭氧菌作用下進行水解酸化,轉化為較易生物降解的簡單有機物,改善了其可生化性,為後續的好氧處理提供條件。在生物接觸氧化單元,廢水中的有機物在好氧菌的作用下被無機化,從而使廢水中的COD值降低到排放標準。試驗結果表明,經過一段時間的馴化,當停留時間(HRT)為16h時,厭氧單元能把原水COD從406mg/L降到272mg/L,去除率在33%;BOD5提高一倍,大大改善了可生化性。在好氧單元,先用自來水配以營養鹽進行好氧菌種的培養,再用廢水對微生物馴化。經過馴化後,當HRT為20h時,COD去除率可達70%。把厭氧段和好氧段串聯運行,經16h厭氧及20h好氧後,COD的最終去除率在63%~78%。
清華大學的竺建榮等採用厭氧-好氧交替(AAA,它是SBR工藝的變型)工藝對遼河油田廢水進行處理試驗,試驗流程:油田廢水氣浮除油UASBAAA接觸氧化出水。遼河油田廢水COD一般為1100~1200mg/L,進水油含量100~150mg/L。經氣浮預處理後,廢水COD約950mg/L,油降到40~50mg/L。試驗表明,進水COD360~950mg/L,UASB反應器的COD去除率均保持在60%左右。經過厭氧UASB反應器處理後的廢水,再經AAA工藝處理,在HRT8~12h的條件下,其COD含量能夠從350mg/L降到160~240mg/L,COD去除率在31%~48.5%。對於質量濃度為160~240mg/L的廢水,採用好氧接觸氧化法作為好氧二級處理,其出水COD去除率在50%~60%,出水COD質量濃度一般接近80mg/L左右。
天津大學的李哲等採用SBR方法來處理某油田廢水。該油田廢水可生化性好,COD為400mg/L,BOD5為250mg/L,油為30mg/L。通過不同周期的考察,發現使用8h為1周期,1h進水,5h曝氣,2h沉澱和出水,出水COD始終低於100mg/L,去除率為80%~90%。
綜上所述,油田廢水處理方法較多,各有優缺點。總結於下表:
含油廢水處理方法比較
不同的油田廢水處理技術,都有各自的優勢和不足。在實際應用的過程中,應綜合運用不同技術的優勢以期在低成本、高效率的前提下,達到最好的凈化效果。

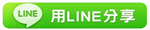
TAG:北極星節能環保網 |