汽車零部件增材製造工藝鏈詳細探討
有內容 有深度 有態度 歡迎關注
當前,已經進入大工業生產的金屬列印工藝主要有兩種—電子束粉末床熔化技術(EBM)與激光粉末床熔化技術(SLM),兩種技術一直呈競爭態勢存在且各有優缺點。EBM技術可以提供很高的生產效率,但零件精度差、表面質量欠佳,需要繁瑣的後續加工;SLM技術正好相反,表面質量較好,零件精度高,後處理工序較少,但其生產效率一般。不過隨著四激光系統的出現,效率低下的問題正在得到極大改善。汽車領域作為金屬列印的主要應用領域之一,正在受到越來越多的重視,本期筆者詳細介紹粉末床熔化技術用於汽車零件製造的整個工藝鏈,全部內容包含12個部分。
1. 金屬列印工藝之間的競爭
粉床熔化技術是對傳統產業影響最大的增材製造技術,它可提供最高的設計自由度和靈活性,並且具有優秀的材料屬性。在分析粉末床熔化技術的成熟程度時,首先要研究的是設備的銷售情況。
粉末床熔化設備市場分析
2010至今粉末床熔化設備的銷量呈現快速增長,設備的銷量表明粉末床熔化技術在連續生產中的大量應用以及客戶對多機裝備的需求,基於其眾多的製造優點,該技術已經成為增材製造領域的主流生產技術。
相較激光列印技術來說,世界範圍內電子束印表機廠商數量極其有限,然而電子束設備的需求卻從未停止,這歸結於其在批量製造方面比激光列印技術更具優勢。
2. 金屬粉末床工藝汽車應用
由於汽車行業對成本、質量、效率的敏感要求,如何甄別哪些零件適合採用3D列印製造具有一定的挑戰性。也是基於金屬列印的高成本,目前幾乎只有高附加值、小批量的汽車採用了該工藝。而在大規模汽車生產中,單件零件的製造遵循成本最低原則,相對來說,汽車動力傳動系統以及懸架系統最可能用到金屬列印。
而金屬列印如何應用到零件的具體生產中呢?接下來以保時捷尾管製造為例,剖析SLM與EBM技術從設計到列印直至應用所融合的整個工藝鏈。
3. 優化設計
汽車尾管組件是發動機排氣系統的可見部分,由於該部位將發動機的性能直接反映給客戶,因此製作要求很高。
通常,該組件由不鏽鋼或鈦合金製成,採用焊接將兩片金屬連接起來,由於機械震動和腐蝕,焊接部位往往非常脆弱。在達到最終設計之前可能會產生大量迭代,同時也帶來高昂的加工成本,交貨時間也超過12個月。
此時3D列印的優勢即可體現,其個性化、自由製造的特點可將尾管組件集成為一個零件,通過優化管道內殼結構,提高性能,實現個性化製造。同時,其快速製造的特點可以在更短的時間內嘗試多種設計。
如若脫離優化設計,增材製造的優勢就很難顯現,但在優化設計時必須考慮零件主體與周圍部件的配合、整體功能以及裝配步驟。
4. 材料性能
4.1 粉末床熔化Ti6Al4V合金機械性能
金屬列印過程中,材料局部熔化形成微小熔池,快速冷卻凝固形成細小晶粒,在列印以及熱處理過程中,組織內部形成針狀馬氏體α』、α及α+β相,最終性能得以提升。結果表明,增材製造Ti6Al4V合金遠超鑄造標準,性能接近鍛件。
4.2 Ti6Al4V疲勞性能分析
汽車在行駛時不斷受到路面衝擊載荷、驅動力和制動力等的作用,而且汽車發動機本身也是一個振動源,因此汽車零部件都會受到隨時間變化的應力、應變作用。經過一定時間,一些零部件便會發生疲勞損壞,出現裂紋或斷裂。為使3D列印零部件具備良好的抗疲勞性能,在列印完成之後使用熱等靜壓對材料進行緻密化,提高整體力學性能,達到鍛件107個循環的疲勞極限。同時,為確保獲得這種優異的抗疲勞性能,如何拋光複雜自由表面也非常重要。
5. X射線斷層掃描
X射線斷層掃描可以檢測到材料內部尺寸小於100μm的缺陷。對於批量生產的零件,一般採用低至中等解析度的檢測才具有成本效益,多用於內部質量和尺寸精度檢測。
汽車尾管組件X射線掃描顯示電子束列印零件內部存在粉末未熔現象
EBM成型過程中,粉末會被預熱到幾百度,周圍粉末會相互粘附形成片狀,需要採用機械方法去除,中空結構則需要採用高速噴射方式去除。與此同時,SLM成型的零件表面質量要好得多。
6. 振動研磨和拋光
一般而言,具有功能性或光學表面的增材製造部件需要後處理才能滿足表面質量要求,對於汽車尾管部件,採用兩種表面處理手段。
機械研磨可以顯著改善尾管部件的表面質量。然而,在LBM和EBM部件表面可能會出現大量的宏觀缺陷,對於批量生產,進一步審查設計和優化製造工藝非常重要,應當儘可能避免這種缺陷。
7. 表面粗糙度
激光熔化相較電子束熔化製作的零件來說具有更好的表面質量,前者表面粗糙度一般為10μm左右,而後者表面往往非常粗糙,即使經過振動研磨和拋光,兩者仍然存在差距,SLM列印的零件最終表面粗糙度可低至1μm。
粉末床熔化工藝粗糙度對比
SLM零件的表面粗糙度是由於粘附粉末顆粒及層疊紋路造成;而EBM零件的表面粗糙度除上述原因之外,還表現為由於電子束受到電磁場干擾容易形成表面宏觀缺陷,而且這種缺陷無法通過研磨和拋光去除。
表面輪廓曲線
仔細觀察表面輪廓可以發現研磨和拋光對錶面結構的影響,在EBM零件上仍然可以看到深槽和針孔,為了消除這些缺陷,材料必須留下0.1-0.2mm的加工餘量。
8. 尺寸精度
對於複雜的自由曲面,光學三維掃描和X射線斷層分析是精準測量零件結構的最合理手段。零件精度主要受模型失真和材料收縮的影響。
汽車尾管部件的尺寸誤差在1mm以下,尾管的圓形形狀有助於穩定成型,失真極小。
9. 熱等靜壓對尺寸精度的影響
熱等靜壓工藝是將製品放置到密閉的容器中,向製品施加各向同等的壓力,但如果工藝過程處置不當,會引起零件的變形,倘若將汽車尾管部件橫向擺放,會造成超過2.5mm的變形。
負載關鍵零部件要求必須經過熱等靜壓處理,而且絕不能忽視熱處理過程對零件尺寸及性能的影響,此處也強調了熱處理工藝的重要性。
10. 時間和成本
成本問題仍然是影響增材製造進入批量生產的主要障礙。相對來說,EBM比單激光SLM在批量生產方面更具優勢,不過SLM對於特定化的小批量製品成本要低一些。下圖以製作汽車尾管為例分析製造成本。
成本結構分析顯示超過60%的製造成本與增材製造工藝相關,從圖中也可以看出,EBM技術相對於SLM無論是原型製造還是批量製造成本都要高。但單憑此圖並不能說明EBM的生產效率低,這是因為汽車尾管屬薄壁結構,體積較小,EBM機器的高生產率並不能顯現。與此同時也可看出,四激光SLM系統可以達到很高的生產效率。
單件成本
汽車尾管部件在進行批量製造時每年的成本可減少50%,成本的降低主要源於後處理過程更加經濟。但同時應該注意的是,採用增材製造進行批量生產,需要考慮生產資質以及質量保證所產生的額外成本。
製造8個零件從提交訂單到交貨過程時間劃分
熱等靜壓和拋光往往需要外協處理,因此造成交貨時間很長。當然,根據合同內容要求實際的交貨時間可能沒有那麼長。該汽車尾管的製作總共用了25個工作日,與傳統的尾管加工方式相比,增材製造的整個工藝鏈還是快了幾個月。
11. 總結
3D列印用於汽車零件製造目前還處於起步階段,傳統的粉末床熔化工藝成本太高,使汽車領域的應用只能限定於小批量的高性能汽車零件製作,而EBM技術以及多激光熔化系統將大大拓展應用範圍。該項研究還表明,3D列印在製造具有較高機械性能和光學要求的零件方面可行並具有巨大的應用潛力,節約成本、提高生產效率,加速設計迭代。
此外,這項研究也揭示了粉末床熔化技術的優點和缺點。EBM技術的優勢在於批量製作大型零部件,並不適於單個零件的個性化製作,與此同時,EBM列印的零件需要較多的後處理工序。SLM技術適合列印單件或少量的零件,並且表面質量優異符合製作要求;多激光成型系統在批量製造方面存在巨大前景。總的來說,增材製造技術在汽車製造領域應用廣泛。
12. 展望
傳統的粉末床熔化工藝由於成本高昂限制了工業領域的應用,而多激光熔化系統尤其是粉末床粘接工藝的出現,將大幅降低成本、增加產量,同時將大大拓展應用領域。
然而3D列印製作零部件仍伴隨著其他諸多技術細節的挑戰,為成功應用,汽車製造商必須為其內外部的供應鏈提供更加寬泛的產品規格要求和認證方法。
當前國內外的汽車製造商幾乎都已經注意到了3D列印的重要性,並承諾投入大量資金予以進行應用研發,3D列印在汽車製造領域的應用才剛剛開始。
轉載請註明出處
長按添加訂閱
Share the World"s 3D Printing Technology

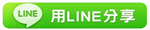
TAG:3D列印技術參考 |