數控沖床及沖模技術在 鈑金製作行業中的應用與發展
鈑金加工工藝主要包括沖孔、淺拉伸和壓印,其加工的工件具有形狀複雜、零件精度較高等特點。採用傳統的普通沖床,加工效率低、質量不高。數控轉塔沖床與普通沖床相比,模具庫數量多,可自動換模,節省換模時間;具有高效率、高精度、自動化程度高的特點,在質量與效率上都有很大的優勢。本文將從數控轉塔沖床的發展、加工工藝應用、加工工藝存在的問題及對策、數控轉塔沖床模具的介紹及應用這四個方面進行簡單概述。
數控轉塔沖床的發展
數控沖床起源於美國WIEDEMANN公司,1932年該公司生產出了簡單型迴轉頭衝壓機床。經過多年的發展,數控技術、液壓技術、伺服電機技術不斷推陳出新,數控轉塔沖床也在更新換代。從其誕生到現在,主要經歷了以下三個發展階段。數控機械轉塔沖床數控機械轉塔沖床工作原理為:離合器控制沖頭衝壓動作,主電機帶動飛輪旋轉,利用飛輪旋轉產生的慣性力對工件進行沖孔或成形加工。優點有:機械結構相對簡單,機床佔地面積小、產品成本低、故障率低以及性能穩定等;缺點是衝壓效率低,衝壓行程不可調,衝壓速度低、雜訊大。代表產品有日本村田機械Muratec的 C系列沖床、日本天田AMADA的ARIES 系列等。
數控液壓轉塔沖床
數控液壓轉塔沖床通過電液伺服閥控制液壓缸上下動作,液壓缸與沖頭組件連接,從而控制沖頭的衝壓動作。優點有:衝壓速度較快,綜合效率較高;缺點是液壓系統對環境要求較高,溫度太高或者太低都會影響機床正常工作,液壓油需要定期更換,且更換的油對環境有影響。國外代表產品有芬蘭FINN-POWER的X5液壓沖床、日本村田機械Muratec的 V系列沖床、日本天田AMADA的VIPROS系列沖床;國內代表產品有亞威的 HPH/HPI/HPQ系列沖床、金方圓的VT 系列沖床等。
數控伺服轉塔沖床
數控伺服轉塔沖床是當代主流技術產品,代表了數控沖床的發展方向。主傳動結構形式主要有曲柄連桿結構、肘桿式結構、斜楔式結構、擺桿式結構等。伺服電機的高動態特性使沖頭衝壓頻次進一步得到了提高,產品的綜合效率更高,更加節能環保。國外代表產品有日本村田機械 Muratec的M系列沖床、日本天田AMADA的AE系列和EM系列沖床、義大利Prima Power 的E5X沖床;國內代表產品有亞威的HPE系列沖床、金方圓的 MT系列沖床等。
數控轉塔沖床的加工方式及加工工藝應用
數控轉塔沖床加工方式可分為單次沖孔、步沖、蠶食、單次成形、多次連續成形等幾種形式。從加工工藝角度,數控轉塔沖床可完成的加工工藝主要包括:沖孔、淺拉伸和壓印。沖孔主要是沖方孔、圓孔、腰形孔等;淺拉伸主要有凸包成形、翻邊、百葉窗、滾筋、滾台階等;壓印主要有衝壓商標、標記、字元等。數控轉塔沖床的加工工序主要分為先下料後衝壓和衝壓套裁加工兩種。兩種方式在效率上有所區別。對於單件形狀規整的工件可以先下料,後衝壓加工,省去裁邊的時間,效率會高一點;對於批量加工的工件來說,套裁加工方式的優勢顯得十分明顯。下面對其進行數據的分析及對比。
先下料,後衝壓
在進行下料時,首先要對板材進行剪裁,按照零件的外形尺寸要求,使用剪板機或者其他方式下料,然後用自動編程軟體進行模具匹配圖形處理,自動生成加工程序,用數控沖床進行自動加工。如圖1所示,板件加工尺寸為480mm×480mm,在一張長、寬尺寸為2500mm×1500mm的板材上可以加工出此種矩形板料15塊。如果單個零件下料時間為 30秒,則總下料耗時為7分鐘30秒。在此過程中,需要人工將下好料的板材放置在沖床上進行加工,單個工件加工需要 4種模具進行 166次衝壓,單件加工耗時41秒,則15件工件加工總耗時 10分鐘15秒,再加上裝卸工件的時間,1 件按15秒計算,15件裝卸總時間需要3分鐘 45秒。整個過程加起來,總耗時21分鐘30秒。
(a)圖紙 (b)CAD 圖
圖 1 單個零件加工
衝壓套裁加工
圖 2所示為衝壓套裁加工方式。排料在整個板材上進行,將15個零件整齊排布,利用沖床長方模具將各個零件單獨切斷分開。為了預防零件的脫落,需要增加微連接。零件與零件之間留有5mm間隙,這是切邊模具的尺寸寬度。此種加工工藝需要 5種模具,衝壓1850次,整個過程需要11分鐘10秒。加工完成後,需要對各個零件之間的微連接進行切斷打磨處理,耗時按 4分鐘計算。總共耗時約 15分鐘10秒。通過以上數據分析對比可知,批量生產的鈑金件可以用套裁的方式進行加工,既提高了生產效率,同時操作工又不需要頻繁更換板料,降低了勞動強度。
圖 2 衝壓套裁加工
加工工藝存在的問題及對策
數控轉塔沖床加工工藝存在的問題主要有板材表面壓傷、板材表面劃傷、加工後的板材發生變形、加工後的板材產生毛刺大等,下面分別進行描述。
板材表面壓傷
產生壓傷的原因主要有以下幾點:板材表面有雜物;刀具上下模刃口處有廢料;轉盤中間有雜物;加工過程中產生廢料反彈導致壓傷。相應的解決措施有:加工前對板材表面進行清理,去除雜物;根據不同板厚、不同材質的板材合理的選擇下模間隙,並及時檢查模具刃口,對模具做好保養工作;定期對轉盤中間及周邊進行清理,去除廢料等雜物;合理選擇模具,例如加工不鏽鋼板材時,選擇加塗層的模具(塗層的作用:1)降低板材的粘連;2)提高耐磨性能;3)增強模具的表面硬度;4)延長模具的使用壽命);選擇防廢料下模及防廢料反彈模具;模具研磨後需要進行退磁處理等。
板材表面劃傷
產生劃傷的原因主要有這幾點:衝壓時預壓點過低,板材移動過程中模具與板材發生摩擦,產生劃痕;人工在上料、下料過程中產生劃傷;人工對板材表面拋光打磨時產生劃痕;模具自身上下模表面有劃傷。相應的解決措施有:簡化電氣程序,避免板材運動時與模具干涉;人工上料、下料過程中最好兩個人進行,避免板材與其他硬物摩擦;拋光打磨時盡量避免產生過多的劃痕,也可以使用去毛刺模具;檢查模具表面是否有劃傷,如有可用油石對其進行打磨處理。
加工後的板材發生變形
如果在一張板材上沖很多的孔,板材不可能保持平直,很容易發生變形,這是由於沖切應力的累積造成的。每次沖一個孔時,孔周邊的材料會被向下拉伸,使得板材表面產生張力。沖切時向下運動也會造成板材下表面的壓力增大。對於少量的沖孔,這樣的影響不明顯。但當孔的數量成倍增加時,張力和壓力作用會成倍增加,直至板材變形。相應的解決措施有:可以使用多孔模來加工,減少衝壓次數,減少變形;抵消這一效應的方法是首先每隔一個孔沖切,然後返回沖切剩餘的孔。這種方法雖然兩種情況下加在板材上壓力相同,但是在衝壓剩餘孔時產生的內應力可以抵消在衝壓首次沖孔時累積產生的內應力和材料壓縮。同時,第一序列的孔也能夠吸收第二序列孔的一些扭曲變形。
加工後的板材毛刺大
產生的原因較多,主要有這幾點:模具間隙選擇不合理;模具自身問題;機床模位上下同軸度跑偏;模具上表面與打擊頭接觸時受力不均勻。相應的解決措施有:依據模具手冊,針對不同加工板材時選擇合理的模具間隙;將模具返修或更換新的模具;調整機床模位上下同軸度至出廠要求;重點檢查打擊頭及轉盤部件,找出原因並維護,保證模具上表面在衝壓時的受力均勻。
數控轉塔沖床模具的介紹及應用
模具分類
數控轉塔沖床模具主要分為厚轉塔模具、薄轉塔模具和專用模具等。厚轉塔與薄轉塔的主要區別在於模具的長度不同,厚轉塔的總長及導向長度比薄轉塔的長。本文主要介紹厚轉塔模具。厚轉塔模具市場上,主要使用有兩種模具:標準模具和90系列模具,由於各個廠商的叫法不一樣,其主要結構原理大致相同,相應的結構示意圖如圖 3所示。兩者主要區別在於以下幾點:價格不同。標準系列比 90系列價格低,性價比較高;研磨量不同。標準模具沖芯的研磨量正常在 2mm~3mm,90系列的達5mm~8mm,單從這一點來說,90 系列的使用壽命較標準的長;模具調節方式不同。標準系列需要工具調整模具頂端的螺釘來調整模具高度,而90系列不需要工具即可調節,每次旋轉一格,模具高度調整一定數值。
標準系列 90 系列
圖 3 模具結構示意圖
模具種類
衝壓模具主要分為標準沖孔模具和成形模具。標準沖孔模具主要有:長方模、正方模、腰形模、三角模、圓模、正多邊形模等。成形模具(圖4)主要有:滾筋模、滾台階模、百葉窗模、凸包模、翻孔模、沖切成形模、雙橋模等。另外,模具廠商也推出了高檔的特殊模具(圖5),如攻絲模、去毛刺模、多子模等,這些模具豐富了沖床的加工工藝,不足的是性價比不高。
圖 4 成形模具
(a)多子模 (b)多孔模
(c)去毛刺模 (d)攻絲模
圖 5 特殊模具
模具保養
具需要及時刃磨,刃磨的時間點如下。1) 刃口圓角半徑達到0.25mm時;2) 有較大毛刺產生;3) 衝壓雜訊異常。刃磨的注意事項如下。1) 沖頭和下模都要磨;2)對使用的46目白剛玉砂輪,保持其砂輪鋒利;3) 吃刀量小於0.013mm;4) 對模具保持足夠的冷卻;5) 工裝夾持模具穩定可靠;6) 刃磨後清洗、去磁、潤滑。定期對模具進行塗油防鏽處理。定期檢查模具高度、緊固件有無鬆動。
結束語
數控沖床及沖模技術在鈑金加工行業的應用,解決了鈑金加工中存在批量大、形狀複雜、零件精度高等問題,大大提高了鈑金加工能力,使鈑金件在質量和產量上得到了保證,同時也降低了工人的勞動強度。隨著機床智能化、自動化的快速發展,鈑金加工行業也呈現出加工方式多樣化、機床操作智能化、自動化的發展趨勢。
——節選自《鈑金與製作》 2018年第3期

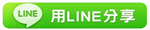
TAG:鈑金與製作 |