PCD 的磨削特點與PCD刀具的刃磨技術
華紅艷1孫標1曹唯飛2
1鄭州航空工業管理學院2多美深圳有限公司
摘要:介紹了PCD切削刀具的製造工藝,分析了PCD材料的磨削加工特點及PCD刀具刃磨對工裝的要求,重點闡述了PCD切削刀具的刃磨工藝及其要點。
關鍵詞:PCD,刀具,刃磨
1 引言
隨著現代科學技術的高速發展,由聚晶金剛石(PCD)、聚晶立方氮化硼(PCBN)等超硬材料製成的刀具的品種越來越豐富、其性能也得到不斷發展和提高。刀片磨料粒徑從數十微米、幾微米到納米級;金剛石、立方氮化硼的含量分為低含量、中等含量和高含量;結合劑既有金屬、非金屬也有混合材料;PCD層厚度從毫米級到微米級;PCD層與硬質合金襯底的結合方式有平面、波紋面;PCD層有高耐磨、高韌性、高耐熱等不同特性。目前PCD、PCBN刀具的應用範圍擴大到汽車、航天航空、精密機械、家電、木材、電子電氣等行業,用於製作車刀、鏜刀、銑刀和鑽頭、鉸刀、鍃刀、鋸刀、鏤刀、剃刀等。
儘管PCD、PCBN刀具發展如此之快,但因其高硬度導致的刀具刃磨困難一直困擾著大多數用戶,刀片的重磨也主要由原刀具生產廠家來完成。不僅刀具價格高,交貨期長,而且佔用企事業流動資金。因此,很有必要認真研究PCD的磨削特點及PCD刀具的刃磨技術。
2 PCD刀具的製造工藝
PCD切削刀具的生產工藝流程一般包括拋光、切割、固接、刃磨、質檢等。PCD超硬材料毛坯直徑通常有1/2、1、2、3、4英吋,其表面一般較粗糙(Ra2~10μm)不能直接用於製作刀具,需經研磨拋光使其表面達到鏡面(Ra≤.01μm);然後通過激光切割或電火花線切割加工成一定幾何形狀和尺寸要求的刀片;再進一步對刀片和基體待固接面進行機械和化學處理,然後再採用銀基硬釺焊將刀片固接於基體上;最後經金剛石砂輪刃磨。
PCD切削刀具製造技術的關鍵之一是切削刃的刃磨質量。優質刀頭材料缺乏理想的刃磨工藝和技術將會造成資源浪費,採用好的刃磨工藝則會提升刀具的產品質量,降低刀具使用成本。
3 PCD材料的磨削加工特點
PCD是由特殊處理的金剛石與少量粘結劑在高溫超高壓下燒結而成的。無序排列的金剛石晶粒使PCD有均勻的、極高的硬度和耐磨性。PCD可用於切削刀具、砂輪修整、地質鑽探、量具測頭、拉絲摸具、噴砂摸具等。但是PCD的高硬度和高耐磨性也給其加工帶領了很大的困難。
國內外學者針對PCD材料的高硬度和高耐磨性所帶來的加工難題進行了大量的研究和試驗,其中包括電火花加工、超聲波加工、電化學加工、激光加工等,並取得了一定效果。但綜合分析發現,這些加工技術目前多適用於PCD材料的粗加工場合。要想獲得好的PCD切削刃口質量,最理想的加工方法仍是用金剛石砂輪磨削或研磨。
PCD的磨削加工主要是機械和熱化學兩方面混合作用的結果。機械作用是通過金剛石砂輪磨粒對PCD材料的不斷衝擊而形成的金剛石的微破碎、磨損、脫落或解理;熱化學作用則是金剛石砂輪磨削PCD形成的高溫使金剛石發生氧化或石墨化。二者混合作用的結果致使PCD材料被去除。其磨削加工特點主要為:
(1)磨削力很大
金剛石是已知礦物中硬度最高的物質,與各種金屬、非金屬材料配對摩擦的磨損量僅為硬質合金的1/50~1/800;PCD的硬度(HV)為80~120KN/mm2,僅次於單晶金剛石,遠高於硬質合金。採用金剛石砂輪磨削PCD時,起始切削強度很高,約為硬質合金(.4MPa)的10倍以上;比磨削能達1.2×104~1.4×105J/mm3;因此磨削力遠高於磨削硬質合金。
(2)磨削比很小
由於PCD的硬度和耐磨性(相對耐磨性為硬質合金的16~199倍)很高,磨削PCD時其磨削比僅為.005~0.033,約為硬質合金的1/1000~1/100000;磨削效率僅.4~4.8mm3/min。因此,為了保證切削刀具的刃口質量和去除量,磨削時間很長、加工效率很低。此外,當PCD的硬度、含量、粒度不同時,其磨削時間也相差懸殊。
(3)粒度影響很大
PCD材料用於切削刀具按粒度主要分為三類:即粗粒度(20~50μm)、中粒度(10μm左右)和細粒度(-5μm),其磨削力、磨削比相差幾倍至數十倍。粗粒度PCD磨削比最高,磨削也最困難,且磨削後刃口鋸齒狀最嚴重、質量最差,但耐磨性最強;細粒度PCD磨削比相對最低,磨削較易、磨削後刃口質量最好。
4 PCD切削刀具刃磨對工裝的要求
基於PCD的上述磨削特點,用金剛石砂輪磨削加工PCD時對刃磨設備的要求比一般工具磨床高得多。主要有:
(1)機床具有良好的工藝系統剛性
由於PCD材料硬度很高,因此磨床必須有較高的抗變形能力,特別是主軸系統和刀具裝夾系統。PCD切削刀具刃磨時磨削力一般達100~500N。因此要求機床的軸徑大、軸承的軸向剛性和強度要高。
(2)機床具有行程可調和速度可調的短程擺動機構
PCD磨削比極低,PCD的磨削加工機理主要是通過金剛石砂輪對PCD材料的不斷衝擊而形成的微破碎、磨損、脫落、解理等機械作用和氧化、石墨化熱化學作用混合的結果。因此採用短程擺動機構有利於提高磨削效率,改善刀具刃口質量。一般擺動距離0~50mm,擺動速度20~60次/分。
(3)機床的刀夾具有高精度迴轉功能和在線檢測裝置
由於PCD材料硬、脆而耐磨,通常將其刀尖設計為圓弧狀,以有助於減小刀具和工件相對振動的幅值。為了實現刀尖圓弧的加工,機床的刀夾應具有高精度迴轉功能和刀尖圓弧半徑尺寸與質量在線檢測裝置。這樣可避免多次裝夾帶來的定位誤差,同時可成倍提高加工效率。
5 PCD、PCBN刀具的刃磨工藝
5.1 刃磨工藝的選擇
切削刀具刃磨的目的之一是獲取性價比高的切削刃口質量,而質量好壞的關鍵在於刃磨砂輪粒度的選擇。砂輪粒度越細,切削刃崩口越小,而磨削效率越低。為此可根據刀具切削刃的精度、用途(見表1)或其失效程度(見表2)將PCD切削刀具刃磨工藝分為粗、精、細三個加工階段。根據具體情況制訂合理刃磨工藝可大幅度提高加工效率。
粗加工對刃口要求不高,可選電加工或磨削加工。電加工效率高,宜用於加工複雜刀具,如印刷電路板用鑽頭、切削強化木地板用成型銑刀等。磨削加工時可選粗粒度砂輪,刃磨時接觸面積大、磨削力高(300~400N),可快速去除多餘的加工餘量;細加工時選用細粒度砂輪,刃磨時接觸面積小、磨削力低(100~200N)、磨削髮熱量少,但材料去除率低。此階段主要是通過研磨和拋光,進一步改善切削刃口質量。精加工居於二者之中。
5.2 刃磨工藝要點
(1)主軸精度要好, 一般砂輪端面跳動應≤0.02mm 。砂輪端面跳動過大,磨削時砂輪斷續衝擊切削刃,容易使切削刃發生崩口,難以獲得高精度切削刃;
(2)砂輪應具有良好的動平衡。砂輪的不平衡將導致機床的振動,進而影響被加工刀具的刃口質量和加工精度;
(3)刃磨砂輪應優先選用陶瓷結合劑金剛石砂輪。因為在磨削過程中陶瓷結合劑易發生微裂使磨粒得到更新自銳,使磨削過程平穩,有利於提高加工表面的精度和效率;次之可選耐熱性較高的樹脂結合劑金剛石砂輪;
(4)適時注意砂輪開刃、且開刃油石粒度要合適。用金剛石砂輪加工PCD刀具時,砂輪會發生堵塞、鈍化、高溫和快速磨損,導致加工速度降低和振紋、噪音、燒傷的產生。通常選擇比所用砂輪粒度細1~2號的軟碳化硅油石作為開刃油石;
(5)因金剛石易與鐵系合金髮生化學擴散, 加速砂輪磨損,因此應儘可能避免同時磨削金屬與PCD;
(6)砂輪迴轉方向務必從刀具前刀面向後刀面迴轉。從磨削時PCD刀具切削刃的受力可知,當砂輪從刀具前刀面向後刀面迴轉時,其磨削力(切向與法向力之和)作用於切削刃向內,即刀具受壓應力,不易崩刀;反之則為拉應力,切削刃易崩口。若因刀具結構原因必須反轉刃磨時,則選樹脂結合劑砂輪優於金屬和陶瓷結合劑砂輪;
(7)為了保證切削刃質量同時提高刃磨效率,可將刀具的后角分為大后角和小后角。用粗粒度砂輪先磨大后角,因接觸面大磨削力大,刃磨效率高;然後用細粒度砂輪刃磨小后角,將小后角的刃帶寬度控制在.1~0.3mm左右,接觸面小刃磨質量好;
(8)儘可能在一次裝夾中完成對刀具切削刃的加工;
(9)PCD刃磨冷卻液應優選水基磨削液。由於PCD材料硬度高且耐熱性差,水基磨削液冷卻效果優於油基磨削液,可提高加工效率和刃口質量。另外磨削過程中冷卻要充分,不能斷流,避免因磨削液量小或斷續供給造成金剛石(砂輪、刀具)的大量消耗(氧化、石墨化)和刀具的刃口破損。
技術交流
已成立研習社,為大家提供產品製造解決方案。
如需進群,請加小編好友:

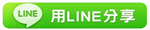
※磨具用樹脂結合劑的研究現狀與展望
※幾種磨料微粉的顆粒整形技術對比與分析
TAG:磨料磨具研習社 |