機械加工沒有一步登天的,這些技巧做到老學到老必須要會!
一.問:如何對加工工序進行劃分?
答:數控加工工序的劃分一般可按下列方法進行:
(1)刀具集中分序法 就是按所用刀具劃分工序,用同一把刀具加工完零件上所有可以完成的部位。在用第二把刀、第三把完成它們可以完成的其它部位。這樣可減少換刀次數,壓縮空程時間,減少不必要的定位誤差。
(2)以加工部位分序法 對於加工內容很多的零件,可按其結構特點將加工部分分成幾個部分,如內形、外形、曲面或平面等。一般先加工平面、定位面,後加工孔;先加工簡單的幾何形狀,再加工複雜的幾何形狀;先加工精度較低的部位,再加工精度要求較高的部位。
(3)以粗、精加工分序法 對於易發生加工變形的零件,由於粗加工後可能發生的變形而需要進行校形,故一般來說凡要進行粗、精加工的都要將工序分開。
綜上所述,在劃分工序時,一定要視零件的結構與工藝性,機床的功能,零件數控加工內容的多少,安裝次數及本單位生產組織狀況靈活掌握。另建議採用工序集中的原則還是採用工序分散的原則,要根據實際情況來確定,但一定力求合理。
二. 問:加工順序的安排應遵循什麼原則?
答:加工順序的安排應根據零件的結構和毛坯狀況,以及定位夾緊的需要來考慮,重點是工件的剛性不被破壞。順序一般應按下列原則進行:
(1)上道工序的加工不能影響下道工序的定位與夾緊,中間穿插有通用機床加工工序的也要綜合考慮。
(2)先進行內形內腔加工序,後進行外形加工工序。
(3)以相同定位、夾緊方式或同一把刀加工的工序最好連接進行,以減少重複定位次數,換刀次數與挪動壓板次數。
(4)在同一次安裝中進行的多道工序,應先安排對工件剛性破壞小的工序。
三.問:工件裝夾方式的確定應注意哪幾方面?
答:在確定定位基準與夾緊方案時應注意下列三點:
(1) 力求設計、工藝、與編程計算的基準統一。
(2) 盡量減少裝夾次數,儘可能做到在一次定位後就能加工出全部待加工表面。
(3) 避免採用占機人工調整方案。
(4) 夾具要開暢,其定位、夾緊機構不能影響加工中的走刀(如產生碰撞),碰到此類情況時,可採用用虎鉗或加底板抽螺絲的方式裝夾。
四.問:如何確定對刀點比較合理?工件坐標系與編程坐標系有什麼關係?
1.對刀點可以設在被加工零件的上,但注意對刀點必須是基準位或已精加工過的部位,有時在第一道工序後對刀點被加工毀壞,會導致第二道工序和之後的對刀點無從查找,因此在第一道工序對刀時注意要在與定位基準有相對固定尺寸關係的地方設立一個相對對刀位置,這樣可以根據它們之間的相對位置關係找回原對刀點。這個相對對對刀位置通常設在機床工作台或夾具上。其選擇原則如下:
1) 找正容易。
2) 編程方便。
3) 對刀誤差小。
4) 加工時檢查方便。
2. 工件坐標系的原點位置是由操作者自己設定的,它在工件裝夾完畢後,通過對刀確定,它反映的是工件與機床零點之間的距離位置關係。工件坐標系一旦固定,一般不作改變。工件坐標系與編程坐標系兩者必須統一,即在加工時,工件坐標系和編程坐標系是一致的。
五. 問:如何選擇走刀路線?
走刀路線是指數控加工過程中刀具相對於被加工件的運動軌跡和方向。加工路線的合理選擇是非常重要的,因為它與零件的加工精度和表面質量密卻相關。在確定走刀路線是主要考慮下列幾點:
1) 保證零件的加工精度要求。
2) 方便數值計算,減少編程工作量。
3) 尋求最短加工路線,減少空刀時間以提高加工效率。
4) 盡量減少程序段數。
5) 保證工件輪廓表面加工後的粗糙度的要求,最終輪廓應安排最後一走刀連續加工出來。
6) 刀具的進退刀(切入與切出)路線也要認真考慮,以盡量減少在輪廓處停刀(切削力突然變化造成彈性變形)而留下刀痕,也要避免在輪廓面上垂直下刀而劃傷工件。
六.問:如何在加工過程中監控與調整?
工件在找正及程序調試完成之後,就可進入自動加工階段。在自動加工過程中,操作者要對切削的過程進行監控,防止出現非正常切削造成工件質量問題及其它事故。
對切削過程進行監控主要考慮以下幾個方面:
1.加工過程監控粗加工主要考慮的是工件表面的多餘餘量的快速切除。在機床自動加工過程中,根據設定的切削用量,刀具按預定的切削軌跡自動切削。此時操作
者應注意通過切削負荷表觀察自動加工過程中的切削負荷變化情況,根據刀具的承受力狀況,調整切削用量,發揮機床的最大效率。
2.切削過程中切削聲音的監控在自動切削過程中,一般開始切削時,刀具切削工件的聲音是穩定的、連續的、輕快的,此時機床的運動是平穩的。隨著切削過程的進行,當工件上有硬質點或刀具磨損或刀具送夾等原因後,切削過程出現不穩定,不穩定的表現是切削聲音發生變化,刀具與工件之間會出現相互撞擊聲,機床會出現震動。此時應及時調整切削用量及切削條件,當調整效果不明顯時,應暫停機床,檢查刀具及工件狀況。
3.精加工過程監控精加工,主要是保證工件的加工尺寸和加工表面質量,切削速度較高,進給量較大。此時應著重注意積屑瘤對加工表面的影響,對於型腔加工,還應注意拐角處加工過切與讓刀。對於上述問題的解決,一是要注意調整切削液的噴淋位置,讓加工表面時刻處於最佳]的冷卻條件;二是要注意觀察工件的已加工面質量,通過調整切削用量,儘可能避免質量的變化。如調整仍無明顯效果,則應停機檢察原程序編得是否合理。
特別注意的是,在暫停檢查或停機檢查時,要注意刀具的位置。如刀具在切削過程中停機,突然的主軸停轉,會使工件表面產生刀痕。一般應在刀具離開切削狀態時,考慮停機。
4.刀具監控刀具的質量很大程度決定了工件的加工質量。在自動加工切削過程中,要通過聲音監控、切削時間控制、切削過程中暫停檢查、工件表面分析等方法判斷刀具的正常磨損狀況及非正常破損狀況。要根據加工要求,對刀具及時處理,防止發生由刀具未及時處理而產生的加工質量問題。
最後插播一則小知識
我們來談談加工中心中,機台刀庫出現異常如何處理呢?
白天的話我們還能找機修,尤其是夜晚的話機台只能停著放到第二天來解決,那麼我們今天就先來說說機台出現刀庫異常,導致刀庫偏位了怎麼解決呢?
我們首先來說說三菱機台的處理辦法:
三菱系統普通刀庫初始化操作:
1.打開PLC開關的#3、#4,這兩個是開啟刀庫維修模式;
2.手輪模式下把Z軸搖到最高點,(機台提示到達Z軸最高點,就往下搖一點);
3.點擊面板上面的「刀盤正轉」,「刀盤反轉」(這個按了以後刀庫會旋轉);
4.回到住畫面執行M74,刀盤會自動旋轉至一號刀位;
5.執行M77開啟ATC維修模式,再執行M79,(這兩個代碼執行了,機台是沒有任何反應的。);
6.Z軸往下搖致第一參考點,關閉PLC裡面的#3,#4、然後關機重啟,
以上六點完成後,機台即可恢復正常運轉
法拉克(FANCU)系統普通刀庫初始化操作
1、打開K參數(K18.0 ,K18.1)開啟刀庫維修模式;
2、手輪模式下把Z軸搖到最高點;
3、打開K19.0=1,模式切換到回零模式,刀盤會自動旋轉至1號刀位;
4、修改K參數(K18.0=0 、K18.1=0 、K19.0=0);
5、Z軸往下搖至第一參考點,重新啟動機床,機床即可恢復;
以上五點即使法拉克機床刀庫出現異常處理辦法,你們學會了嗎?

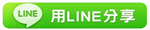
※資深玩表總結超詳細的機械錶保養硬知識!愛表如愛車!
※anrot改裝各種越野豪車!hks機械增壓
TAG:機械 |