提升沖模零件模具表面強化處理技術質量控制的方法
本文摘選自《模具工業》2018年第3期
作者:葉立淵,趙樹林
(御捷汽車質量和製造工程中心)
通過對TD處理工藝各階段的控制,提高了衝壓件的品質,降低了企業經營成本。目前開發的新車型高強度鋼板模具的壓邊圈、凹模鑲件(左/右縱梁後部、左/右A柱下加強板、左/右B柱上部橫樑)已全面普及TD處理工藝,以後計劃在高端車型的高強度鋼板模具開發方面,嘗試使用更高級別的ASS?AB88材料,並同步開展TD處理工藝與ASSAB88母材適應性的研究。
隨著我國汽車工業的高速發展,各大主機廠對汽車安全性的關注度也越來越高。通過在車身安全結構件中使用高強度鋼板替代普通鋼板,以提高車身的安全性,勢必對模具零件強度、耐磨性提出更高的要求。高強度鋼板在R角及複雜成形面處極易出現毛刺缺陷,該缺陷已成為阻礙衝壓件成形質量提升的難題,通過引入模具TD表面強化技術,可以提升衝壓件成形質量和延長模具鑲件的使用壽命,具有製造成本低、整改周期短的特點。
TD工藝簡介和工藝流程
TD工藝簡介
TD模具表面強化處理技術是熱擴散法碳化物覆層處理(thermal diffusion carbide coating process),在一定的處理溫度下將零件置於硼砂熔鹽及特種介質中,特種熔鹽中的金屬原子與模具零件中的碳、氮原子發生化學反應,擴散到模具零件表面而形成膜厚幾微米至幾十微米的釩、鈮、鉻、鈦的金屬碳化層。實踐證明,這種覆層厚度為10~15μm,硬度達到2800~3200HV,具有很高的耐磨性、抗崩刃性、耐蝕性,可以重複TD處理3~5次。
高強度鋼板模具材料的選用逐步使用高耐磨、抗崩刃的SKD11替代Cr12MoV,合資品牌在嘗試使用更高級別的模具材料ASSAB88(材料成本是SKD11的2倍以上),高強度鋼板材料對比數據如表1所示。
TD工藝流程
① 來料檢查:鑲件數量、質量、外觀(碰傷、裂紋等)、母材牌號、母材硬度檢測和確認;
② TD處理前尺寸和硬度確認(零件長寬尺寸不能大於620mm×850mm);
③ TD處理前打磨和拋光(粗糙度小於Ra0.8mm);
④ TD處理:預熱(520℃左右)、TD處理(900~1030℃硼砂熔鹽8~12h)、鹽浴淬火(500℃左右鹽浴10~20min)、回火2次(低溫回火180~200℃,高溫回火500℃,回火時間在3~5h);
⑤ 清洗及孔中鹽類物質去除;
⑥ TD處理後尺寸和硬度確認;
⑦ 尺寸調整確認;
⑧ TD處理後的拋光;
⑨ 出貨檢測(碰傷、裂紋、雜質、硬度、皮膜厚度);
⑩ 包裝出貨。
TD處理前要進行預熱的目的是防止鑲件產生劇烈變形和開裂,預熱溫度設定為520℃左右,以保證鑲件表面不產生氧化物為前提。需要注意的是鑲件從硼砂熔鹽到鹽浴中的速度要快,以防止TD層氧化。
TD處理使用範圍和優點
TD處理的使用範圍
TD處理適用於汽車衝壓成形類模具的鑲件、各種擠壓模、滾壓模、彎管模、成形模、彎曲模、擴口及縮口模、變薄拉深模等。
TD處理的優點
模具鑲件通過TD處理後,可以提高其表面的耐磨性和母材的韌性,通常情況下進行TD表面處理後,其使用壽命至少提高8倍以上、衝壓單件合格率能提升到98%以上、停線時間縮短、維護成本降低。
TD處理模具零件選擇
1
Cr12鋼材不適合做TD處理,因為TD處理後,相關技術參數不達標:①模具零件硬度不達標,一般只能達到45HRC左右,耐磨性較差;②零件尺寸變形大,Cr12在TD處理過程中沒有二次硬化,由材料自身的特性決定的。
2
油鋼(DF2)、碳鋼類不適合做TD處理,因為其熱處理工藝不適合TD處理工藝要求,油鋼、碳鋼的淬火溫度在780~850℃,而TD的淬火溫度在900~1030℃。
3
高速鋼不適合做TD處理,高速鋼TD處理屬於二次淬火過程,開裂風險大,而且熱處理工藝與TD工藝不適應,高速鋼淬火溫度為1200℃左右,而TD的淬火溫度在900~1030℃。
4
不鏽鋼系列鋼材不適合做TD處理,因為含碳量低,在0.1%~0.3%,TD處理後無法成膜(要求母材含碳量在0.3%以上)。
TD處理常見問題及應對措施
1
模具零件在TD處理過程中,會出現母材硬度不足,尺寸無法調整的問題,主要原因是模具母材牌號錯誤或質量達不到相關標準和要求;應對措施是選擇適合TD處理的優質模具鋼,例如:SKD11、Cr12MoV。
2
模具零件TD處理後會出現焊接部位不成膜或存在裂紋的問題,主要原因是:TD處理前模具鑲件R角和成形面存在較明顯的裂紋和砂眼缺陷、焊條材質與母材不相融(熱膨脹係數和收縮率相差較大)、焊接工藝不合理等。針對鑲件R角和成形面缺陷(裂紋和砂眼)的應對措施是首先使用砂輪機和磨頭將缺陷部位表面深度0.5mm以下去除,然後選擇與母材相融的焊條實施焊接、修磨、拋光。對於已實施過TD處理的模具鑲件,需在200℃左右的加熱爐中保溫1~2h後再實施焊接,這樣可以減少開裂風險,提高焊接質量。
為了篩選出最適合母材的優質焊條,通過試驗數據驗證不同型號的焊條在SKD11上焊接後,實施TD處理的效果(膜厚和硬度指標)。
試驗材料
①母材:材質為SKD11;②焊條:包括CMC-EMagic6、TM2000在內的6種不同型號焊條。
試驗步驟
①由具有豐富經驗的模具高級技師,依次使用6種不同型號的焊材在母材上試焊3cm長的焊接面,並做好1~6的編號(見圖1);②將焊接面表面打磨光滑,實施TD處理;③TD處理完畢檢測膜厚、硬度參數,觀察其外觀,並做好記錄,檢測數據如表2所示;④依據評價標準,對6種不同型號的焊條焊接後的TD效果實施綜合評價。
圖1 TD處理圖示
試驗結果
使用型號3(SUPER7)和型號4(WeD-6a)焊條在SKD11母材上焊接,TD處理後效果(皮膜厚度、硬度、外觀質量缺陷參數等)最優;上述試驗數據是通過試驗得來,不同的施焊人員、焊接設備、焊接方法、不同批次的焊接母材和焊條、焊接環境、檢測設備等,得到的檢測數據可能有偏差。
3
模具鑲件經過多次TD處理後,會引起模具零件表面成膜不好、耐磨性差或開裂的問題,主要原因是模具零件經過多次TD處理後母材表面的碳原子含量會逐漸減少,皮膜厚度不斷下降,同時母材表面脫碳層越來越深;如果母材表面脫碳層深度達到0.50mm以上,TD處理後模具鑲件表面成膜效果較差,嚴重時會引起鑲件開裂,當出現以上缺陷時,則不再適合做TD處理。
TD處理變形量控制
1
沖模鑲件實施TD處理過程,實際是二次淬火的過程,其組織變化與真空淬火後的組織變化基本相同;不同的是TD淬火的介質和真空淬火的介質。
真空淬火的介質是油和氮氣,在常溫下這2種介質在零件淬火時冷卻速度較快、熱應力釋放也較大。在這種情況下如果保護不當,會引起零件的變形和開裂;通常情況下,真空熱處理的變形量比TD處理的大,且開裂風險增大。
TD淬火的介質是等溫鹽浴,鹽浴淬火溫度控制在500℃左右,淬火時間10~20min,零件在此過程中冷卻速度較慢,釋放出的熱應力較小,一般TD處理後的模具鑲件整體變形量和開裂風險都較小。
2
變形量的控制要求:平面和側面的變形量可以控制在±0.05mm左右。當前行業內對於零件變形量的控制參數,參照日本行業相關標準,沖模鑲件尺寸長、寬、高均在300mm以內的控制在±0.10mm左右,在100mm以內的控制在±0.05mm,在50mm以內的控制在±0.03mm,特殊要求除外。
TD處理後使用維護相關注意事項
1
新的模具鑲件調試穩定後才能實施TD處理,TD處理後的模具鑲件在運輸前,必須使用獨立防磕碰的包裝,運輸時使用專用器具裝車,運輸過程中避免急剎車等情況出現。
2
TD處理後的模具鑲件會有微量的變形,在進行裝配前,需對鑲件安裝型面進行細緻研磨,裝配面的研合率達到80%以上,使鑲件之間、鑲件與安裝面之間達到較好的匹配效果。
3
TD處理後的模具在生產前,必須對模具零件表面進行清擦,在板料上塗適量拉深油,有助於延長TD層使用壽命。
4
每生產5000沖次,需將模具吊入全封閉模具清洗間實施整體清洗、吹乾,保證模具整體的清潔。
5
在進行必要的焊接作業時,必須對TD處理面實施必要的防護措施,否則會造成TD處理層的氧化脫落,縮短模具使用壽命,模具鑲件的TD處理層抗氧化溫度為500℃左右,而焊接電弧溫度達到6000℃以上。
6
模具鑲件在TD處理後其表面硬度能達到2800~3200HV,具有較高的硬度和耐磨性,但是尖錐物的敲擊和砂輪機的打磨會導致TD處理層的損傷,應避免以上不當行為。
7
異物擠壓會導致TD處理層的變形凹陷,需要及時實施鈍化和研磨處理,處理不及時會導致TD層損壞面積不斷增大,造成衝壓件局部產生嚴重毛刺,縮短模具使用壽命。
微信編輯:野牛
《模具工業》創刊於1975年,是我國最早出版的模具專業期刊,系中國模具工業協會會刊,在我國模具行業具有較高的知名度和影響力,主要報道各類模具先進技術及行業動態等,是交流模具技術、傳播模具信息、宣傳行業廣告的理想平台。
《模具工業》雜誌唯一官網為中國模聚網(www.moulds.com.cn),雜誌投稿系統的鏈接為http://www.moulds.com.cn/magazine/

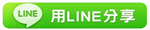
TAG:模具工業 |