直齒錐齒輪的Hypoflex製造技術
在機械傳動系統中,直齒錐齒輪的應用十分廣泛。它們除了在汽車差速器上的用途外,其他應用的例子還在電動工具和各種各樣的農業機械和設備中有廣泛應用。
與弧齒錐齒輪相比,直齒錐齒輪承載能力較低,運行平穩。他們之所以應用廣泛,是因為與螺旋錐齒輪相比,具有較低的軸向力,且軸向力的方向和大小與旋轉方向無關,減少了對於軸承的設計任務量。這個特點與變速箱中無限制軸向安裝的附加優勢結合在一起,帶來了較大的設計優勢。
本文討論了採用先進的設計和優化軟體,以及與之相匹配的現代乾式切削技術對直齒錐齒輪加工的製造工藝。
研究現狀
直齒錐齒輪是通過預成形、成形或切削加工製造的。預成形的實例包括鑄造和燒結。鑄造被用來大規模生產直齒錐齒輪,當對齒輪要求精度和功率密度較高時,可以使用非金屬材料或有色金屬材料。燒結錐齒輪在手持電動工具中使用較多,例如,電動角磨機。與其它工藝方法比較,該工藝難以避免材料的不均勻性,由於不均勻的緻密化。另外模具的製造和齒輪參數的修改會有較高的成本。
鍛造和擺動擠壓都被證明是批量生產差速器錐齒輪的有效方法。但是該工藝方法存在的缺點在於其齒輪的周節誤差和齒的形貌誤差精度水平較低,採用擺動擠壓生產的齒輪精度等級一般大概為IT8。然而,切削加工工藝依然為認為是能夠穩定獲得大批量或者小批量高精度齒輪產品的重要加工工藝。
就軟齒面加工而言,可以採用諸如刨削、滾削和拉削等切削加工手段。直齒錐齒輪的熱後硬加工只能通過研齒或磨齒的方式在有限的範圍內進行。磨削工藝也在航空工業齒輪製造中有一些應用。Heidenreich-Harbeck制定的加工工藝依然應用在某些一次性和小批量的零部件製造中。
加工直傘齒輪的Revacycle的拉削工藝特別適用於差速器錐齒輪的生產。該工藝所利用的刀具是一種圓周拉刀,圓周上有大量不同齒廓的刀具。第一個圓周段由粗加工刀片組成,每個葉片之間有輕微的向外偏移,接著是帶有精加工葉片的段,接著是留出工件在一個周節處轉動的間隙,刀具的每一次旋轉都產生一個齒隙,如圖1所示。
圖1 Revacycle製造工藝
最後的葉片具有凹形,這個凹形將會被複制到工件,而刀具的中心點在一條直線上移動,就產生了直齒根。齒形沿端面寬度變化,縱向凸度是由單個切削刀片的形狀和拉刀的切向運動產生的。Revacycle加工直傘齒輪的特徵在於由其很高的生產效率,但僅僅可以用刀具來影響齒形。因此,這個工藝方法只適合大規模生產。
一種更為通用的切削方法是滾齒加工。在這裡有三種不同的切削系統,其差別僅僅在於刀具的輕區別。最常用的是Coniflex?, Konvoid和Sferoid Coniflex?。
這組刀具包括兩個圓周內嚙合側銑齒刀盤,它們代表了一個冠輪輪齒。這兩個側銑齒刀盤的軸線,一個在左側,一個在右側,被以一個相對確定的角度布置,因此這兩個刀盤存在一定的相互內部嚙合,這就引起它們產生一個梯形的輪廓。由於切削刃不在各自的旋轉平面內,但位於一個輕微的內錐面內(如圖2所示),齒廓就會存在一個固定的長度鼓形量,且齒根不是直線而是橢圓形,其最低點位於齒部中間。齒的長度鼓形變化量可以由刀具以及它的調整來決定。
圖2內嚙合側銑齒刀盤
齒的長度鼓形量是由兩個側銑刀互相傾斜的角度和刀具直徑決定的。這個角度的變化要求切削刃的側面角發生變化,因為齒的壓力角被改變了。
展成運動產生齒輪的齒高齒廓。這兩個刀盤沿著它們的頂端擺動,而工件沿著自身的軸旋轉。通過對機床的不同設定,可以利用相同刀具製造出不同的錐齒輪。
滾齒和拉齒工藝已經被創立好多年了,關於它們的歷史可以追溯到19世紀60年代。這兩種工藝均採用濕式切削,其工作效率和切削速度比較低。在生產率方面,它們已不能與現在所利用的乾式切削方法相比較。
與螺旋錐齒輪相比,關於刀具的計算沒有相應的軟體。沒有現代的尺寸計算和優化軟體可以使用,同時也沒有基於計算機的齒面形貌測量程序,同時缺乏3D名義數據。
理論基礎
弧齒錐齒輪通常採用單齒分度和連續分度加工。單分度加工時,機床單獨加工某一個齒面。刀具呈圓形排列,產生齒長方向鼓形。
當一個圓在另外一個圓上做滾動時,就產生了外擺線。滾動的圓通常稱為滾圓,半徑為EB,固定圓為基圓,半徑為EY。如果外擺線的生成點位於內部,所得的曲線稱為縮短外擺線;否則,它被稱為一個延伸外擺線(圖3)。
圖3擺線的形成方式
連續分度加工採用面銑刀刀頭,其刀刃口由內、外刀片組成。每組刀頭切削一個齒槽間隙。刀盤中刀齒的組數取決於刀盤的起始或者僅僅取決於其初始齒數Z0。在與工件相關時,一組刀齒沿著一個延伸外擺線運動。在連續切削的螺旋錐齒輪加工中,因此形成輪齒向的延伸外擺線部分。
當螺旋錐齒輪是在一個連續分度加工時,開始的數冠齒輪的齒數之比等於滾動圓半徑與基圓半徑的比值:
當滾動圓在基圓的做滾動時,所產生的即為內擺線(圖4)。這與切削外擺線時的刀具運動軌跡相同,但旋轉方向相反。
圖4內擺線以及縮短內擺線
在這個基礎上,怎樣才能產生直線,從而產生直齒呢?在滾圓半徑等於基圓半徑的一半的特殊情況下,滾動圓上某點產生的所有點都位於直線上。在這種情況下,縮短和延長的擺線就會變成橢圓。
Hypoflex製造工藝
Hypoflex製造工藝的動力學原理與上邊所述的基本一致,即,在理論精確地基礎上,開始的數與冠輪齒數的一半有關。
牙冠齒數通常不全是偶數,只有在極少數情況下才能完全滿足要求。一般情況下,選擇冠齒數的一半的整數作為起始數。齒長曲率(延長或縮短擺線)是由一個半徑幾米的曲率產生的在直線方向,存在2刀3μm的變化數值,這比在上面提到的滾削或滾削加工要小得多。
Hypoflex的連續分度加工工藝是一個精加工和半精加工的乾式切削加工工藝。在精加工工藝過程中,一組刀具包括內刀和外刀,它們分別切削齒輪的左齒面和右齒面,它們是在同一台機床上設置的。在半精切加工工藝中,需要進行兩台機床設置,其中分別加工齒輪的左齒面和右側齒面,但是刀盤上只有一組刀齒,外刀或者內刀。後一種加工方式的特點是,它只用了一組刀齒。Klingelnberg發明了一種具有兩個切削刃的刀具,稱為TWIN刀具。當僅用一組刀齒加工時,半精切加工的特點在於適合大批量生產和較高的靈活性設計。
Hypoflex齒輪的齒全高時隨著齒寬方向而變化的,其齒根和齒角可以在一個有意義的範圍內選取,這使得在用不同工藝生產的直齒錐齒輪進行改進時保留相同類型的毛坯成為可能。
由於根錐角和節錐角的不同,在°節錐平面上的螺旋角可以認為是由內刀刀齒和外刀刀齒的半徑差異引起的。這個差異的大小有一半取決於壓力角和齒根角。連續分度工藝中,同一類型的連續兩刀之間的組角的大小是:
作為專家應當承認的是,當採用內刀齒和其它刀齒的排列角度與刀組數的一半相等時,就會發生齒槽的寬度與期望的數值相差太大的情況。因此有必要去調整刀齒序列角度。這意味著與採用連續分度法加工螺旋錐齒輪相比,刀齒之間距離會靠近。刀齒序列角度的數值取決於起始數量,齒根角、壓力角以及滾動圓和基圓半徑。一標準在設計齒輪和選擇一個真正的刀盤時必須考慮到。
通常情況下,鼓形量是由各種修正方法來實現的。與切削其它錐齒輪工藝相,齒長鼓形是可以通過刀盤傾斜和特定的壓力角來實現的。如果在長度鼓形方向採用空心錐的方法去實現,就會出現齒面接觸區位於齒高方向的變化。另外一種生成齒廓鼓形的方法是採用修緣的刀具。更進一步的修正(接觸區和失配)可以採用與螺旋錐齒輪的相同的方法來實現。
對於螺旋錐齒輪的接觸應力和齒面承載能力計算的相應最新計算方法,同時能夠適用於Hypoflex製造工藝。第一次,採用計算機和享用計算程序,可以測量齒面數據,建立3D齒面模型,在這基礎上進行機床參數的修正。這使得使用者能夠採用閉環製造系統,作為Hypoflex的製造工藝,提高產品的質量水平。
採用這一個工藝過程,直齒錐齒輪副可以採用Oerlikon的錐齒輪切削機床進行加工,所需要做的僅僅是選取不同的計算軟體。同樣,刀具調整和磨削傻唄也可以通用,只需要在現有的ARCON刀具上匹配所需要的刀條以及起始數量即可。
Hypoflex製造工藝的優點
Hypoflex製造工藝是一種直齒錐齒輪的製造工藝方法,它採用的連續分度切削方法,採用帶有條形刀條的銑齒刀盤。除了在直齒錐齒輪領域率先採用最新的干切削技術外,它還有更大的靈活性。採用硬質合金刀具,切削速度高,可獲得較高的生產率。
Hypoflex製造工藝可以在現有的CNC螺旋錐齒輪製造機床上實現。,所需要做的唯一調整就是設計軟體的升級。直齒錐齒輪的設計可以在現有的KIMOS軟體上實現,KIMOS軟體在螺旋錐齒輪製造領域已經成熟應用多年,它可以就按機床設置參數,刀具參數以及EASE OFF的優化,還可以做載入齒面分析和齒面輪廓數據設計。所有需要的數據均以名義數據的格式保存在KIMOS資料庫中。
由於採用了較高的生產效率,Hypoflex製造工藝使得使用者能夠利用現有的閉環製造系統來控制整個過程中的質量水平。這個閉環系統包括了製造過程中的檢測以及與之相關的刀具和機床參數修正的KOMET和3D形貌輪廓掃描等,該系統已經在螺旋錐齒輪中得到了廣泛應用。
應用實例
圖5顯示的是如表1所列的齒輪參數的齒輪實例,該齒輪為Hypoflex工藝製造而成。
圖5採用Hypoflex工藝製造的錐齒輪
相關的齒面接觸區分析結果如圖6所示。齒面接觸區位置和載入分析結果符合客戶要求。
圖7 KIMOS對hypoflex的計算
該齒輪是在C29銑齒機上採用半精切工藝所加工的,所用的是代用條形刀具的ARCON刀盤,14組刀條,且代用刀具塗層。主動輪加工時間為4.25分鐘,被動輪加工時間為4.5分鐘。齒輪副測量結果顯示,主動輪周節誤差精度達到DIN3965標準的3級,被動輪周節誤差精度達到標準的2級。齒面形貌測量結果以及齒面粗糙度等級均滿足生產質量要求。這意味著與以前的傳統製造工藝相比,有了一個巨大的質量和效率的提升。

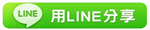
TAG:燕青談齒輪 |