煉油廢水的處理和回用進展
廢水是原油煉製、加工及油品水洗等過程中產生的一類廢水,污染物的種類多、濃度高,對環境的危害大。20世紀六七十年代以來,國內煉油廠大多採用「隔油→浮選→生化」工藝(即「老三套」工藝)處理廢水,且以二級處理為主,對含硫、含氨廢水預先汽提處理,外排水的COD , BOD等基本可以達標。近年來,水體污染加劇,生態環境惡化,許多煉油廠的用水矛盾十分突出。廢水深度處理和回用,一方面可以降低污染物的排放總量,減少對環境的危害;另一方面,可以提高水資源的重複利用率、節約大量的新鮮水和購水費用、降低生產成本,緩解地區缺水危機。本文總結了近年來煉油廢水處理與回用的研究進展和生產性應用的實例。
1 煉油廢水處理的研究進展
煉油廢水的污染物主要有油、硫化物、氰化物、揮發酚、NH3 -N以及其他有毒物質,其COD含量較高,難降解物質多,而且受鹼渣廢水和酸洗水的影響,廢水的pH變化較大。為提高外排水的水質,研究者開發了一些新的處理工藝和技術。
1.1除油技術的發展:廢水的除油效果對後續生物處理的影響很大,提高除油效率是近幾年研究的重點。除油方法很多,應用較廣的是重力隔油、混凝沉澱和氣浮除油等。許多煉油廠使用聚合氯化鋁(PAC)或聚合硫酸鐵(PFS)等單鹽聚合物作為混凝劑去除油和懸浮物,但存在一定的缺陷;目前,含多種離子的復鹽聚合物混凝劑、浮選劑的開發成功,使混凝除油的效果顯著增加,沉澱或氣浮的效率提高。夏暢斌等人以煤矸石和硫酸燒渣為原料合成聚硅酸鐵鋁(PSFA),在相同劑量和投加條件下,除油和除硫化物的效率比PAC和PFS高20 %以上。陳芳艷研究表明,聚合氯化鋁鐵對油和COD的去除率分別達到了92.5 %和78.1 %,明顯高於單鹽聚合物的效果。某煉油廠採用聚合鐵鋁作為混凝劑,不僅提高了油的去除率,而且對S2-也有50 %左右的去除效果,同時減輕了生物處理池的硫化物衝擊。Ogutveren將電解作用和絮凝機理有機結合,採用電絮凝方法除油取得了良好的效果,其除油效率與電極電位和支持電解質有關,油的去除率最高可達100 %。近年來,膜分離技術發展迅猛,尤其是通透率高且抗污能力強的複合膜材料的開發成功,使膜過濾技術在用於含油廢水除油和其它污染物等方面具備了更強的應用基礎和可操作性。研究表明,複合膜去除廢水中含量為幾十mg/L且粒徑小於100μm的油時,效率很高。
1.2生化處理技術的應用:生化處理是一般煉油廢水整個處理流程的核心。煉油廠的生化處理常採用好氧曝氣活性污泥法,對BOD和COD的去除有效,但無法除磷脫氮,且容易出現污泥膨脹或流失現象,導致外排水的水質不穩定。為達到更高的排放要求,一些新的處理工藝和技術被開發並用於生產中。
1.2.1厭氧處理+曝氣生物後處理工藝:煉油廢水採用「厭氧+好氧」處理工藝時常以好氧處理為主,厭氧段起水解和酸化的作用。GuanWei-sheng等人強化了厭氧處理的功能,採用上流式厭氧污泥床和好氧曝氣池中試處理含高濃度揮發酚和乳化油的煉油廢水,試驗結果見表1。
UASB在中溫和HRT為24 h的條件下, COD容積負荷達5.2 kg/(m3·d),BOD去除率超過85 %,沼氣產率達到1.34 m3/(m3·d)。通過投加適量的顆粒活性炭和FeSO4 ,促進了污泥的顆粒化, UASB的污泥濃度達到了60 g/L ,大部分易降解污染物都在UASB被去除(對難降解有機物如二甲基酚、乙基酚也有很好的去除效果)。這樣,後段曝氣生物處理池的HRT可以很短,且大大降低了曝氣量。該組合工藝比單獨好氧曝氣處理的去除效率高20 %~30 %。
1.2.2硝化-反硝化工藝:國內絕大多數煉油廠的廢水處理裝置不具備硝化和脫氮能力。提高好氧池的污泥濃度或延長污泥停留時間(SRT),在好氧池後單獨設置硝化構築物(即O1/O2工藝),均能起到較好的硝化效果。王培風等人兩級好氧生物接觸氧化法小試研究去除NH3 -N和有機物,進水的NH3 -N為58.4~92.8 mg/L ,出水降低到11.3~20.5 mg/L ,達到了國家排放標準。陳少華中試比較了O/O工藝和A/O工藝去除NH3 -N和NO-3 -N的差異,認為兩種工藝均能有效去除NH3 -N ,而且後者對NO-3-N有57.9 %~74.8 %的去除率。Hung Yuan-fang等人在活性污泥池和生物轉盤的進水中投加葡萄糖和5 mg/L的酵母粉,富集培養出大量硝化細菌,NH3 -N從20~80 mg/L徹底轉化為NO-3 -N。他們發現,一旦硝化細菌培養成功,就不必再加入這兩種營養物。該研究對廢水的生物硝化十分有利,但投加兩種物質促進硝化細菌生長的機理不詳。A/O2(即缺氧-好氧-好氧)工藝具有完整的除COD、NH3 -N和NO-3 -N流程,於得爽、凌雲等中試探討了處理煉油廢水的效果,並將其應用於生產,工藝流程見圖1。
生產運行效果見表2。
Joel H A在處理漢堡煉油廠的廢水時開發出一種能有效去除硫化物、COD和脫氮的工藝,其原理是在缺氧環境中,某些硫氧化細菌能在氧化硫化物的過程中,以NO-3 -N作為電子受體,將硫氧化成硫酸鹽、NO-3 -N還原成N2 ,達到了同時去除COD , S2-和NO-3 -N的目的,克服了常規生物處理S2 -過高造成的衝擊影響。
1.2.3序批式生物反應器和膜生物反應器工藝:序批式生物反應器(SBR)集污染物的高去除效率和自動控制於一體,能在同一處理構築物內完成去除有機物、脫氮和除磷的功能,具有污泥濃度高、抗衝擊能力強、適應範圍廣等優點。煉油廠的鹼渣、酸洗廢水由於含多種有毒、有害物質,常規生化處理難度很大。林濤等人建立了工業性SBR試驗裝置處理鹼渣廢水、汽提凈化水等高濃度廢水。總HRT為12 h ,處理程序採用以下方式:
進水COD為4 000~8 000 mg/L ,出水低於250 mg/ L ;進水NH3 -N為120~140 mg/L ,去除率達90 %以上, TN的去除率也可保持在60 %左右,而且運行非常穩定。膜生物反應器(MBR)工藝是生物處理技術和膜分離技術的有機結合,一方面,該工藝簡化了處理流程,另一方面由於固液分離的效果顯著提高,使生物處理池的污泥濃度可以保持在30 g/L以上,大大強化了生物處理的功能,因而污染物的去除效率很高,同時良好的出水水質可以滿足回用要求。M DKnoblock採用膜生物反應器(MBR)工藝中試處理含油廢水,預處理只有簡單的沉砂和隔油,經過11個月的運行,取得了滿意的效果(見表3)。
MBR的COD容積負荷達6.3 kg/(m3·d),膜通量可保持63.6 L/(m2·d);與另一套採用傳統工藝的對比試驗表明,出水水質優於後者。MBR非常適用於煉油廠的鹼渣廢水、酸洗廢水等高濃度廢水的處理。
此外,有研究者利用好氧固定床反應器結合活性炭過濾處理潤滑油煉廠的廢水,出水COD降低到22 mg/L ,GC/MS檢測表明,該工藝對微量大分子有機物如烴類和非烴類物質的去除效果良好。
2煉油廢水回用處理的研究與應用
國外的一些煉油企業噸油耗水量和產生的廢水量均很少,為達到嚴格的排放標準,廢水一般採用三級處理,雖流程較長,但外排水的污染物濃度低,基本上可以直接回用。我國煉油廠廢水回用的探索早在20世紀70年代就開始了,如長嶺煉油廠、紅星化工廠等將外排水回用於循環冷卻水系統,後由於水質等原因,先後停止了回用。90年代以後,我國的缺水矛盾突出,節水和廢水回用成為人們的共識,廢水回用的研究和應用日益廣泛。
2.1我國煉油廢水回用處理的現狀:達標外排的煉油廢水還有少量NH3 -N ,COD ,BOD , SS , TN , TP ,大分子有機物等,其濃度根據各廠的運行狀況而變化。回用的領域有循環冷卻水系統、生產、生活的雜用或用於綠化、景觀等。綠化對回用水的水質要求較低,很多煉油廠已經應用,但回用於生產過程的水質要求較高。國內某些煉油廠的廢水生化處理採用了A/O ,A/O2或O1/O2工藝,具有除磷脫氮的功能, COD , BOD , NH3 -N , TN去除較徹底,在二沉池後設石英砂或活性炭過濾,出水COD為30~50 mg/L , BOD , SS和油含量很低,進一步殺滅細菌後就可以補充到循環冷卻水系統或生產過程中去。如濟南煉油廠和湛江煉油廠已開始將廢水回用。但大多數煉油廠的廢水仍採用「老三套」處理技術,雖外排水的主要指標能達到排放標準,但離回用的水質要求差距較大,只在進行深度處理後才能回用。
2.2煉油廢水回用處理進展:為進一步降低外排水的COD , NH3 -N , BOD ,SS ,濁度,油,色度,金屬離子等,必須採用有效的方法將其去除。目前,廢水深度處理的常用方法有物理、化學和生物深度處理等。
物理方法:沉澱和過濾主要用於去除水中的SS ;空氣吹脫對外排水的易揮發性物質如NH3 -N和有機物有較好的處理效果,但存在二次污染等問題;膜分離技術用於廢水的深度處理時,根據膜材料和孔徑的不同,能夠有選擇性地去除SS和一價或二價離子,出水可以達到多種工業用水要求。化學深度處理:絮凝常和沉澱、過濾結合使用以降低水的濁度和SS ;離子交換、電滲析可有效降低水的鹽濃度;電化學、光化學和聲化學氧化技術主要用於去除水中的大分子物質,與氧化劑如O3 ,H2O2的協同作用使污染物的去除效率遠大於兩者單獨處理的效果。
生物深度處理:主要是好氧生物處理,而且以生物膜法為主,能夠將多種污染物較徹底去除,從而避免回用水的微生物孳生及生物粘泥等問題。
從上可知,單獨一種處理技術只能去除某一類污染物,污水回用需要幾種技術的組合處理才能滿足要求。
當前,膜分離、氧化技術和生物深度處理是煉油廢水回用研究的熱點。Elmaleh S , Ghaffo r N等人利用一種新的超濾膜材料過濾煉油廠的外排水,油和SS分別為20 mg/L和30 mg/L ,處理後小於5 mg/ L和10 mg/L ,完全可以回用。近年來,O3氧化技術在煉油廢水回用中的應用日益廣泛;電化學技術、光化學技術用於廢水深度處理的研究增多:電解氧化、電解絮凝和電催化氧化用於除COD和金屬離子等效果顯著;紫外光氧化、光催化氧化、射線輻照法用於水中大分子物質的去除有良好的作用。需要指出的是,電化學和光化學法由於能耗和處理費用較高,尚處於試驗階段。生物深度處理具有去除污染物的種類多、效率高、抗衝擊能力強且運行費用低等優點,再經過絮凝、過濾等後處理,能夠獲得良好的回用水,這是COD ,油, NH3 -N ,BOD等濃度較高的外排水深度處理優先考慮的技術。本課題組採用懸浮載體生物接觸氧化、微絮凝過濾和臭氧生物活性炭技術中試深度處理煉油廠外排水。研究表明,外排水的COD可從70~140 mg/L降低到30~40 mg/L ,NH3 -N從15~30 mg/ L降到小於5 mg/L ,出水的油低於1.0 mg/L ,濁度低於3.0 NTU ,色度, UV254等也有良好的去除效果。該研究成果正用於生產中。有研究者採用生物處理和過濾結合的人工土層快速滲濾工藝深度處理石化廢水,小試表明, COD , BOD , SS和油的去除率分別達到67.8 %~72.4 %, 80.0 %~84.5 %, 90 %和85.7 %~89.0 %,出水能作為循環冷卻水的補水。此外,有研究者達標外排水進行簡單處理後回用於循環水系統,利用藥劑達到緩蝕、阻垢、殺生的目的。這種方法的基建費用相對較低,但對藥劑的依賴性大,而且長期使用後微生物的耐藥性增強,結垢和粘泥的問題仍將十分突出。
2.3煉油廢水回用處理的工業應用:煉油廢水進入生產性回用的實例很少。韓春來等人開發了一種以膜分離為主的外排水深度處理工藝,哈爾濱煉油廠採用該技術深度處理外排水,規模為4 000m3/d ,工藝流程見圖2。
該系統已運行2年多,活性炭出水約70 %回用到循環水系統,超濾出水回用於動力裝置。由於外排水只經過二級處理,水質變化大,對深度處理系統常造成一定的衝擊影響,而且總出水的NH3 -N濃度較高,不利於長期回用,為此,增加了除氨裝置。
撫順煉油一廠的廢水在「老三套」處理基礎上設置了氧化溝,深度處理後的COD很低,僅SS和油濃度偏高。工業試驗裝置處理水量為30 m3/h ,採用「氣浮-三級纖維束過濾」的流程除濁度、SS和油等,出水直接回用到循環水系統。天津石化公司將煉油廢水和其它化工廢水深度處理(一、二期的處理規模共為10 000 m3/d)後回用到基建、沖廁、綠化、洗車以及空分廠的循環冷卻水,經過2年的實踐,趙秀雲等人認為回用廢水的COD最好控制在40 mg/L以下,而且回用水應有效殺滅細菌和藻類。
3結束語
隨著煉油廢水外排標準日趨嚴格和廢水回用的呼聲逐漸高漲,二級處理無法滿足這一要求,新的處理工藝、技術和藥劑的研發力度正在加大,符合我國國情的簡單實用、高效可靠、運行費用低的回用水深度處理工藝和技術仍將是今後一段時間的發展趨勢。污水回用是一項長期的工作,目前許多煉油廠已進入實質性操作階段,只有根據本廠外排水的實際狀況,研究合理可行的技術路線,全面提高回用水的質量,才能達到污水的可持續回用。

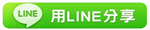
TAG:乾來環保 |