一文告訴你,腕錶機芯是如何生產出來的
腕錶之美,很大一部分是落實於機芯上(滑動查看)
【壹】
設計,這是整個機芯生產工藝的源頭,但有可能也是最耗時的一步。據卡地亞機芯研發總監所述,一枚全新的機芯從概念產生到批准生產,耗時少則三年多則五年。但有趣的是,這步的文字敘述不難,如今簡而言之就是通過3D max等軟體來實現對預期機芯的模擬。整個步驟與錶殼的設計有著異曲同工之妙,只是需要考慮的變數更多。工程師小組首先在專業鐘錶師的輔助下繪製草圖並標註各項數據指標,隨後通過繪圖軟體將其轉化為電腦中的3D模型,以此形成的模型小到輪齒大至整體布局都與最初設計的完全相同。隨後,該模型也成為了後續機芯零部件製作的「樣板」。
用軟體繪製機芯設計圖
在機芯設計確定之後,正式生產之前,還有兩步。一為相關專利的申請;二為製作手冊的撰寫,手冊中有著所有工序與元件的完整記錄,包括使用的潤滑油、螺絲的重量等,可謂鉅細靡遺。既然提到機芯設計,不妨額外提及一句,在Autodesk類軟體普及之前,機芯設計在正式生產之前還要經過一段長達數個月的樣機試驗。要知道,彼時所謂的樣機,並非如今的3D模型,而是真正地投入一次生產,製造實打實可以運行的「真實」機芯,整個過程可以理解為是在量產之前的小規模試產。其中涉及的財力與時間可想而知。好在, Autodesk類軟體的誕生幫助機芯生產省去了樣機的步驟,研發時間與成本也隨之得到了控制。舉個最簡單的例子,據雅典透露的信息來看,UN-150計時機芯的研發時間不過1.5年,這對於樣機模式來說是很難達到的一個效率,但在Autodesk的輔助下成為了現實。對此,只能感慨,「傳統有理,科技無罪」。
完成了機芯的設計後,就進入了最為重要的零部件生成環節。當然,有兩個前置工序,分別為材料的選擇以及模具的製造。材料選擇方面,黃銅依舊是夾板的主流,德國銀、K金、藍寶石、碳纖維等偶爾有之,但始終未成氣候;模具製造方面,如今但凡參觀過錶廠的人,對「自主製造模具」的論調想必不會感到陌生。
【貳】
完成準備工序後,就進入了正式生產的環節。但正如引言所述,因機芯零件的龐大數量,所以若一一列舉難免使全文顯得「零碎」,且篇幅的限制也不允許如此行事。要知道,曾經國內出版的一本講述機芯齒輪製造的圖書,16開,15印張。因此,相關內容顯然不是區區三千餘字就能總結的。故,只概述夾板、齒輪、遊絲的生產。這,也是整個機芯中較為重要的三大塊。
主夾板衝壓成型
夾板有很多種類,大致可分為主夾板、條夾板、中夾板、上夾板、叉夾板和擺夾板等。 這些不同大小、不同薄厚、不同位置的夾板,依照用途安裝在機芯上,各司其職。在生產工藝方面,除去主夾板,其餘夾板大抵相同,基本上都是通過車床切削成型。至於主夾板,生產過程敘述起來並不難,無非就是黃銅或其他金屬條衝壓成型後再以鑽孔機完成「打洞」。但,因其上布滿了凹槽與孔徑,所以對於製作精度的要求非常高,尤其是需要承載傳動輪部分的孔徑,加工精度甚至要求達到千分之一毫米。當然,對於凹槽的要求沒有這麼誇張,但同樣不容忽視,因為凹槽的深淺直接影響傳動零部件的軸向間隙。這也是為何在許多工程師的眼中,主夾板是機芯所有零部件中所需工時最長、加工設備最複雜的一個零件。
被高倍放大的機芯夾板,用以檢測機芯打磨的平整度和精度
無論是主夾板或者說其他夾板,在型後,自然就會進入打磨的步驟。主要有分為功能性打磨和裝飾性打磨。前者可以簡單地理解為消除毛刺,旨在盡量使孔徑及凹槽的邊緣光潔平整從而最大程度地減少摩擦力;後者則主要是起到裝飾作用,倒角裝飾、日內瓦波紋、魚鱗紋等均分屬其中。合適的打磨,會讓實為平面視覺效果的夾板表面有種明暗光影構成的高低起伏感;倒角而成的弧面更是賦予了現代機芯一種古典的韻味,Simpcy更是其中極致的代表。
朗格和Simpcy夾板的打磨效果絕對令人嘆為觀止(滑動查看)
額外提一句的是,機芯夾板,尤其是橋板的視覺效果,並不僅取決於打磨紋路,與整個機芯的板路設計、形狀、其他裝飾等均息息相關。若處理得好,縱使是3/4夾板這樣的「大臉」也能極具美感。反之,某些機芯夾板的視覺效果在高倍放大鏡下,簡直不堪入目……
黃銅夾板電鍍
完成打磨工藝後,若夾板是黃銅材質,自然少不了電鍍的工序。該工序存在的意義很簡單,一為防止氧化,二為視覺美觀。整個步驟簡單來說就是將掛滿夾板的托架浸入電鍍液,常見的為黃銅鍍銠,但金、銀、鎳等亦有人為之。
【叄】
齒輪生產方面,有一個和之前所述的盤面製造相似的場景,那就是同樣為鐘錶中非常重要的部件,但在錶廠的參觀流程中卻很難見其身影。究其原因,有二,一為部分齒輪確實是外購;二為迎合「機芯手工製造」的論調,因此事實上基本依託於車床的齒輪製作自然不能在參觀中展示。然而有一個觀點需要再次強調,也是全文通篇持有的一個觀點,車床的生產模式意味著工序的由難至易,但並不代表著加工精度或者說加工難度的降低。只不過,難度從手工時期的體力勞動轉變為自動化時期的代碼編寫及刀具選擇等;精度要求,更是毋庸置疑,相比手工時期,有著非常顯著的增加。
齒輪製造的流程(滑動查看)
回顧齒輪的生產步驟,在純手工時代,鐘錶技師必須為每個嚙合齒輪加以鍍層並挫削處理,十分辛苦不說,輪齒的側面輪廓也難以得到保證。到了18世紀,隨著第一台齒輪切削機的發明,齒輪的生產精度得到了提升,根據固定在水平軸上的刻度盤可以銑切出齒間距相等的輪齒環。如今,隨著高精度數控自動車床和自動制齒機器的普及,齒輪的生產方實現了真正的高精度。齒輪整個生產工序的起始步驟名為Décolletage,文字形容非常簡單,就是一個自動車刀從自動填入的金屬棒料中切削出齒輪毛坯。其中,有三點需要注意,一為金屬棒的材質基本為黃銅,硅齒輪的生產工藝是DRIE而非此;二為這道工序也可製造鋼材質的齒軸或螺絲;三為此時齒輪毛坯的厚度會故意超標以為後續的打磨環節留有餘地。此外,採用中心孔或者其他管套從黃銅板帶或者鋼板帶中衝壓出齒輪的圓片坯料,是一道簡單快速的工序,不過這道工序不可能進行精密制齒的製造,因此還需要進行另一個步驟——精密銑切輪齒。經過清理、去毛刺和高拋光處理後,由裝備了自動裝料機和硬金屬銑切裝置的制齒機器進行下一步工序,讓齒輪重疊在一起如同板疊一樣嚙合,銑切出符合預先設計的輪齒。經過銑切的齒輪將通過加熱和淬火進行部件的硬化及退火處理——這是齒輪傳動裝置精準運行的重要條件。接著通過滾壓處理來確定其確切的尺寸:將部件夾緊在轉軸上,急速旋轉,讓部件達到額定尺寸,與此同時完成拋光程序,讓整個部件光可鑒人。這道工序以前稱為「輥軸旋轉」,和打磨工序相比,不會磨蝕原料,而且大大增加了密合性。在齒輪製造廠Affolter Pignons,部分定價較高的齒輪將進行多次滾壓處理,包括用木塊打磨拋光輪齒,以及其他保密的加工處理工序;極其昂貴的齒輪甚至會在側面鑲嵌鑽石裝飾。最後一道工序是將齒輪和齒軸安裝在一起,通過鉚接將黃銅齒輪連接在鋼製的齒軸上,大批量產品採用自動鉚接設備,小批量產品則采手工鉚接。由於關係到整個機芯的質量問題,製造一個齒輪的過程中會進行12—15 次檢查,一再確認其尺寸,在顯微鏡下將部件放大50至100倍,和樣機進行對比,沒有達到最佳,就必須報廢。且隨著科技的進步,齒形的檢測變得更為便捷,通過齒形加工儀器,可依據設計圖分辨每個齒形的錯誤值,並通過激光顯微鏡照射出每個細節,從而提升了齒輪的製造精度。
遊絲的設計、製造與盤繞(滑動查看)
遊絲,尤其是合金遊絲,這個在生產工藝上一度蒙著神秘面紗的機芯零件,如今隨著越來越多的鐘錶品牌提出的「自產遊絲」概念而逐漸展露於世人面前。回顧整個工藝,除去硅等特殊材質,相比錶殼錶盤的生產工藝,合金遊絲因產品的特殊性而有些「獨一無二」的工序。最為顯著的就是需要自己製造生產原料。不同於錶殼錶盤生產中原料的外購,遊絲的生產工藝中,作為原料的合金棍是需要自己生產的。簡言之就是熔煉、制坯、鍛造、熱軋的工序。之所以合金棍需要自制,主要原因在於合金材料的保密性,或者說獨一性。縱覽鐘錶行業,除去Nivarox,但凡宣稱能自產遊絲的鐘錶品牌,所產的合金遊絲的合金配方均為獨一份且保密。
在獲得了作為原料的合金棍之後,就是具體的生產環節。第一步需要做的就是將棍變為絲,通過電機的拉扯不斷縮小合金棍的直徑以提升其長度,常規情況下直徑達0.05mm即可,但也會有一些將直徑縮小至0.014mm。此處需要指出的是,合金棍的拉扯與錶殼的衝壓其實有著異曲同工之妙,即並非一次成型,而是需要不斷重複步驟,那麼酸洗清潔表面,回火去除應力自然是題中之意。當合金棍的直徑達到上述數據時,遊絲粗坯就算製作完成。隨後就是盤絲的過程。取三或四根特定長度的遊絲粗坯,通過盤絲器構成阿基米德螺線,取下後進行熱處理使其定型。之後,再通過儀器將遊絲盤分解成三或四根獨立的遊絲。將這些遊絲經過檢測後,整個製作工序就算完成。
【肆】
自此,整個機芯的零部件生產工藝大抵完成。當然,上述的夾板、齒輪、遊絲只是機芯的「通用零件」,此外還有一些諸如音簧、腎形輪等複雜功能專屬的零部件,這些部件的生產工藝無外乎也就是衝壓車削打磨等工序,在前文所述的夾板及齒輪生產工藝中都可找到身影,所以此處限於篇幅便不再贅述。
從左至右(滑動查看):螺母擺輪製造,由機械手臂將紅寶石點入機芯夾板,機芯金屬零部件的製作
整個零部件生產完成後,便進入了機芯的組裝環節。這個環節形象點來說類似拼積木的過程,將零部件根據設計圖按序嵌入主夾板後壓上夾板旋緊螺絲即可。且有趣的是,相比機芯設計或零件生產,對於鐘錶編輯來說,機芯組裝可能是最熟悉也最陌生的一步。之所以熟悉,是因為得益於如今許多鐘錶品牌熱衷於舉辦的「機芯拆解與組裝」課堂;說其陌生,原因更簡單了,那就是真實的組裝,除非是大複雜機芯,不然根本不可能一人一芯。
只有大複雜機芯的組裝,才有可能是一人一芯
機芯的組裝,尤其是非大複雜款的組裝,如今各大錶廠採用的是流水線的方式。即將機芯底板固定在一個安裝有晶片的底座上,隨後所有的組裝工序都由電腦精準設定,包括擰螺絲的力道和滴潤滑油的量。而每個工作人員會分配到一個工作盒,裡面有所從事工序的完整配備,工具、螺絲、零件、指導手冊、壓力模具等一應俱全以保證工序的運作無誤,且便於發生問題後的追溯。當然,對於高複雜機芯,錶廠通常採用的是一個人重頭到尾組裝的方式,這樣每枚機芯都可通過序號追蹤到負責組裝的人員。自此,整個機芯的生產工藝落下帷幕。當然,組裝完成之後還有檢測環節,尤其是高複雜機芯的檢測環節更是耗時不少。但,這是另一篇章的故事了……
線性時間

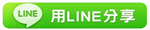
TAG:線性時間 |