封裝面臨的挑戰!
過去幾年,半導體行業的關注點一直在於縮小特徵尺寸來提高晶元性能,而現在的關注焦點已經轉移到封裝工藝上來。有數據表明,目前約有35%的晶元採用WLP技術封裝,而市場的晶圓級封裝(WLP)需求已經從引線鍵合轉向倒裝晶元封裝。
來源:長電科技官網
2017年,封裝廠商為推出更低成本的倒裝晶元解決方案而延緩了扇出晶圓級封裝(FOWLP)技術的使用,所以先進封裝市場在2017年有所放緩。目前主流的先進封裝技術以倒裝晶元技術為核心,但FOWLP和3D IC封裝技術也在不斷發展。
市場上對高性能和小特徵尺寸半導體的需求促進了先進封裝技術的不斷發展。未來外觀更小的智能手機和高端伺服器等終端設備將擁有更快的處理速度和更高I/O密度,這也意味著對封裝工藝的技術要求將會越來越高。
IC製造中基本的互連和凸點工藝流程如下:阻擋/種子層沉積,圖案化,電鍍,光阻膠剝離和蝕刻。工程師們在設計倒裝晶元時正逐步使用薄膜再分布技術(RDL),這項技術允許在無需更改I/O焊盤布局的條件下,將I/O焊盤重新分布到凸點焊盤。凸點底層金屬(UBM)技術,能夠在晶元上的(Cu或Al跡線)金屬焊盤與焊料(或金)凸點之間形成一層金屬化層,使得晶元與基板互連工藝更容易實現、互連可靠性更高。
封裝互連可靠性和半導體性能的提升能帶來I/O密度的提高,但這最終會導致線/間距幾何形狀、凸點直徑和間距縮小。線/間距尺寸正在從10μm縮小到2μm,不久後凸點直徑可能會縮減到10μm,光刻、光阻膠剝離和UBM/RDL蝕刻工藝步驟也會隨之面臨相關技術難題。
光阻膠剝離:一旦特徵尺寸縮減,I/O密度增加,剝離光刻膠就會變得越來越難。光阻膠剝離工藝中,剝離劑擴散到光阻膠中發生溶脹得以去除光阻膠。而隨著特徵尺寸縮減,剝離劑能滲透光阻膠的能力受限,需要更長時間的噴塗才能達到較好的光刻膠剝離效果,勢必會帶來光阻膠剝離效率的降低從而影響產出。
能夠保證光阻膠剝離效率的一種工藝方法是,在精準控制的加熱和氮氣環境下,將單張晶圓浸入到再循環溶劑蒸發槽中。考慮到下游的測序工序,需要確保每張晶圓浸入時間相同。在恰當化學成分的剝離劑和干膜厚度條件下,浸入過程可使高度交聯的光阻劑發生溶脹和溶解。
浸入工序完成後,晶片表面在轉移到單晶片旋轉處理台期間需要保持剝離劑濕潤;然後再使用高壓化學風扇噴霧強力清除殘留物,可確保晶圓表面完全沒有光阻膠;最後再將晶片轉移到旋轉清洗乾燥台完全清潔表面。
凸點底層金屬/薄膜再分布技術(UBM/RDL):縮小的線和間距尺寸也帶來了UBM/RDL蝕刻工藝的挑戰。種子層蝕刻步驟的關鍵在於去除阻擋層和種子層的同時也要盡量減少底切。較高的底切會影響到器件的機械完整性,而不徹底的光阻膠剝離則會導致器件良率降低。而對於較大的特徵尺寸,由於底切包含特徵直徑的一小部分,對器件的影響則會相對較小。相應地,如果特徵尺寸從10μm縮小到1μm,相同的底切卻會產生十倍的影響。為了盡量減少這過度蝕刻的問題,需要有更好的工藝控制來精確監測蝕刻步驟完成的時間,從而減少底切並保證臨界特徵(線或凸點)尺寸。
濕法蝕刻是各向同性工藝,橫向蝕刻速率等於縱向蝕刻速率。蝕刻工藝中,只要達到了最小化的底切金屬厚度,工藝需要立即停止。與濕式工作台中的批量處理相比,單晶片濕法處理(即一次刻蝕一個晶片)能更好地控制蝕刻工藝。與此同時,使用終點檢測(EPD)也能為精準的金屬蝕刻工藝終點提供原位自適應工藝流程式控制制,通過精準控制化學品供應時段分布來保證晶圓蝕刻的均勻性。
先進封裝是未來封裝的必然趨勢。汽車電子產品包括自動駕駛輔助系統(ADAS),數據處理,5G基礎設施部署對增強移動性和連通性有更多要求,智能手機和其他移動設備也在增加設備的功能性,這意味著終端產品的性能需求會持續影響封裝市場。雖然FOWLP和3D集成等先進技術在當前市場上佔比不到10%,但預計未來幾年複合年增長率將超過15%。許多封裝廠商正在以改進工藝流程和設備等方法和轉變策略來解決技術難題,晶元製造廠商也需做好充分準備才能積極應對市場變化。
編譯:Sharon
文章來源:3dincites
圖片聲明:如果我們使用了您的圖片,請作者與本站聯繫索取稿酬。如您不希望作品出現在本站,可聯繫我們要求撤下您的作品。

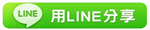
※2025年前硅晶圓都將缺貨 擴充產能關鍵看大陸新晶圓廠
※晶元的今生前世③
TAG:全球半導體觀察 |