揭秘鉗工師傅的那些秘訣
研合篇
(一)
一、精度保證能力
我有時候在想,為什麼會有研合這個動詞,他在模具製造過程中是必須的嗎?
為什麼工業世界發展到現在,各種高精尖數控設備都有,模具還需要手工去研合?
據說,號稱「消滅鉗工」的豐田汽車模具公司是可以做到不需要手工去打磨模具的,對於這個據說,我還是相信的。因為在我有限的模具生涯中接觸到的日本人,我都能感受到他們對於技術工作的專註與偏執,萬事就怕認真啊!
對於國內的汽車模具行業來說,消滅鉗工研合這個事情,應該到現在為止,絕大部分是做不到的。因為沒有數據統計,只能基於個人的認知程度來說,最少我是沒有看到或者聽聞國內號稱排名前幾十的模具廠現在可以做到,當然也有可能我孤陋寡聞。
要討論的鉗工研合,說白了就是模具製造過程中,為了保證模具製造精度的一種人工修正方法,他是工廠的精度保證能力中的一個工序。
怎麼樣去判斷一個模具工廠的精度保證能力好或者差?
1,左右件完全對稱的零件,在同樣調試環境下,出來的結果相差較大;
2,當客戶提出嚴格的公差的時候(例+-0.3),不能達到質量目標;
3,零件精度提升過程,從+-1.0至+-0.5的提升過程可能會反覆折騰;
4,模具重新加工、研合後,再調試零件精度波動大;等等,
我們都可以視為精度保證能力的判斷標準。
精度保證能力,是對一個工廠整個製程能力的體現,從模面設計、加工工藝、CNC編程、CNC加工、拼裝、研合全製造工序都需要專註於技術的提高才能做到一個高的程度,更多的是考驗我們的模具技術、設備加工能力、工藝方法、質量控制能力。
(二)
二、研合
1,首先我們聊一下研合的必要性吧
當我們從工藝方法、設備加工能力、質量控制能力幾個方面導致我們加工下來的模具做不到我們需要的精度要求的時候(即:我們通常要求的研合率85%以上),那我們怎麼辦?答案是我們只能靠手工去修正,即用一基準去修正非基準部分來保證模具的精度,以零件料厚為基準來保證模具上、下模間隙,以此才能達到我們所需求的模具與零件的貼合要求,以此來保證零件在衝壓過程的精度。
那有的人馬上又提出問題,為什麼會有研合率85%-90%等這些要求,我不達到研合率要求會怎樣?會有什麼問題?
如下圖:
零件料厚值為T
上下模間隙為T+間隙值C
例:T值為1mm,C值為0.8mm,則代表上下模閉合到底時,零件在衝壓過程中可以有0.8mm的間隙值可以來波動,再直接一些,同時衝出3個零件去測量,則可能會有3個完全不同的結果:1個可能是偏差,1個可能是-0.8偏差,1個可能是+0.8偏差,或者+-0.8中的一個任意數值。
那麼沒有研合來保證精度的
第一個問題是:不能控制零件在上下模間隙中的精度偏差值,和其製程穩定性。
第二個問題是:因為零件的波動,你不能依據唯一的基準對零件的精度進行改修,改修CAD數據也失去基準的再現性意義。
所以,到這裡研合的必要性應該不用重述了吧。
2,研合的標準
要做到什麼程度才可以?需要全型面貼合嗎?
標準如下:
拉伸模
修邊模
翻邊整形模
以上是研合的標準,每個公司根據實際情況會不一樣,此標準僅供參考。
你說看不懂?那我幫不到你了。。。。
3,關於研合的問題
基準
對於研合的作業規範的事情,我們不過多的聊,參考各工廠研合操作規範手冊
需要重點提出的是,手工修正模具是必須要有一個基準模的前提的。(碰到太多基準都不清楚的情況了)
要保證衝壓產品的品質與精度,高品質的基準型面是必要的前提
基準型面的使用情況為:
拉伸類的模具,壓料面基準使用凹模壓料面
型面基準使用凸模為基準
原因:成形的本質實際就是,在壓住部分材料的基礎上,用凸型面進行成型。
從工藝角度來講,凸模型面是決定材料的接觸狀態,凹模則是到底前的某一深度進行反成形、及與凸模的貼合,功能不一樣。
後工序的模具,均使用下模為基準
原因:零件成形完成後,往後工序傳遞時,所有工序都是下模為型面定位的基準,零件也是先在下模定位後,上模再壓料。
研合碰到的問題
當你知道以上所有研合操作程序,對模具進行正確的研合修正的時候,還有可能在壓機上趴上好多天之後,發現模具始終沒有研合率。
模具中空現象
中空現象,即上下模研合時,周圍一圈都有著色,但中間都是空的
中空,在型面範圍越大的時候,越明顯(如:門內板、地板、頂蓋)
在壓機設備檯面尺寸與模具尺寸相差越大的時候,越明顯;
原因:不考慮加工精度的前提,其實是研合過程中設備與模具的剛體變形造成的,
壓機變形:所有調試設備考慮模具通用性,都會選擇檯面偏大為好,而設備力源是幾根立柱在檯面的小的範圍傳遞,而模具都是不論大小的試,由此帶來的不平衡所以造成了檯面剛體的變形。
模具變形:1,鑄造變形;2,熱處理變形;3,設計造成強度弱
如圖:
解決方法:
在說解決中空問題前,有必要提一下機差問題。
機差問題
壓機的變形問題,會有一個差異性問題需要解決,即通常所說的機差問題
例:假如模具工廠設備與客戶端設備一模一樣,或者說客戶方衝壓生產直接在模具工廠設備上完成,那則在模具工廠調試好模具和零件後直接轉入衝壓生產。
反之,模具工廠與客戶方設備不一致,則就會存在機差問題。就會出現在模具工廠確認好研合和模具精度後,轉入客戶方又會發生變化。
研合的問題,不能因為機差原因而去放棄達到目標,因研合問題是直接影響到零件精度問題,對於機差問題,只能盡最大可能去符合實際量產機、物,在此基礎上再把研合做到目標。
研合中空問題
a,永久性措施,做的好的公司,接合實際工廠設備實際情況,統計鑄件變形數據,在編程前加工數據處理階段已做型面間隙處理,熱處理變形靠加工工藝解決。
所以,最好的解決方案是,根據本工廠設備、工藝精度保證能力,在前期做預間隙補償處理以達到減少鉗工研修的工作量。
b,臨時措施,當碰到這類情況不多的時候,可以通過臨時手段進行補償。
(可以回顧揭秘鉗工師傅的那些秘訣第一篇講的墊片功能)用個人實例來講一下吧
(當故事看)
某年某月,一模具工廠承接了幾個相對於他們來說比較大的零件,已快到交貨節點,但還有很多零件、模具問題沒有解決,我正巧過去喝茶,然後老闆就提出是不是可以幫忙。以此為前提,他們鉗工師傅就提出了這個問題,說某一零件研合總打不上顏色,周圍一圈都有,但中間空的,空測了間隙沒有問題,但帶料厚去貼合就是沒有顏色,研合不到50%。
然後現場上壓機調試,我一起參加,調試過程大概是:我在零件各個區域開了孔洞,放上鉛絲測了間隙,然後確認了模具R避讓、排氣孔、硬點、壓傷之後,基本確定是壓機變形造成。隨後找了0.5mm的矽鋼片,直接墊在上模中空位置,再刷上紅丹,研合率90%。
壓力不足問題
當料厚較厚與材質強度較高的時候,出現研合不良問題
例:料厚3.0,材質抗拉強度780,外形尺寸800*600,零件有較大多形狀的某一零件,在設計分析時成型力800T足夠,但實際在1000T的壓力機上打不出紅丹。
此類問題確實在實際製作過程有出現,實際調試時壓力不夠,導致打不出紅丹。
建議方案如下:
1,首先確認是否模具已去除不必要的貼合部分,如:R、局部硬點、廢料部分;
2,在1的基礎上,再確認不成型的條件下研合,只確認模具料厚間隙是否達到研合的間隙要求(比如說成型完的板件上挖孔測間隙,或者同料厚低強度的材質確認模具料厚間隙);
3,在確認料厚間隙OK的前提,還不能達到研合要求,這種情況我們試壓一批次零件,確認零件無質量缺陷,工序件測量3個零件以上確認尺寸精度偏差波動範圍在正常範圍(比如產品公差要求+-0.5零件波動範圍小於0.2)。理論上就已經可以保證零件尺寸精度的穩定性,個人意見,這個時候不能達到研合要求,應是可以接受的情況。
4,如客戶一定要確認研合的情況,只能在以上基礎上,找同料厚低強度的板材進行研合確認,或者將零件分成多小塊分別進行研合確認(當然這個過程要注意模具的平衡,用同料厚小板料調整模具平衡);
以上的問題應是模具製造過程中,研合可能會碰到的問題
特別提醒的是:不論是中空問題,機差問題,設備壓力能力問題,在此之前我們都要先確認模具的狀態已符合要求,硬點已去除、R角已避讓、不必要的研合去避讓、排氣足夠、上下模料厚間隙空合OK,再去排查其他的問題。
於如何去判斷研合是否OK,提醒以下:
1,紅丹油、藍丹油它只是檢測研合率的一種工具,不能嚴格代表製程能力的表現,差別只是藍丹油會更薄一點而已,當然你紅丹也可以刷到很薄;
2,確認零件的研合率,必須是同一個區域雙面確認的,單面著色不代表間隙OK,因為零件都是凸成型的,儘管模具間隙偏大,在凸的區域也是會先著色的;
3,你需要防止投機取巧的操作人,對於紅丹刷的過厚,以及設備壓力調的遠遠超過你的成型力,或者重複壓多次後來壓出紅丹給你看;
最後,研合不能算高技能的操作,他只是對加工能力、設備能力的一種修正,是作為汽車模具鉗工工作職責的基本必項;
對於那些從事普通板材,零件直線折彎,平面成型沖孔的操作者,說他從來都不需要研合的,我只能說不在此文討論範疇了;
對於那些說做了10來年鉗工的,研合的時候上、下模一起打的操作者,我只能感嘆行業從業人員是真勝差不齊,水太渾啊!!

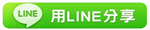
TAG:白濕傅衝壓鐵匠鋪 |