高效率高質量鑽孔的直線導軌鑽孔機設計
作者: 唐兵仿
單位: 江門銀特銀數控機床有限公司
來源:《金屬加工(冷加工)》雜誌
2017年以來,直線導軌副供不應求的狀況,吸引了大量資金進入這一資金和技術密集的小行業,可以預見2019年前後,低端直線導軌副將大量過剩,但由於核心技術的缺乏,中高端直線導軌副需求將在較長時間內保持供不應求的狀態。要實現國產直線導軌副達到中高端水平,絕大部分企業還有大量的技術問題需要解決,即使直線導軌安裝孔鑽削這一大家認為簡單的工序,合格率也不高。究其原因,一些生產者對產品技術要求沒有掌握,過度追求效率或節省成本,設備選型時就已經決定了產品質量合格率低。
直線導軌安裝孔不合格內容除了沉孔深度不一致、沉孔直徑尺寸超差和沉孔孔口倒角不均勻外,還有更為嚴重的直線導軌安裝孔距的累積誤差超差,直接影響直線導軌安裝精度,沉孔尺寸超差還影響螺母密封效果。
直線導軌安裝孔距的累積誤差是指1根直線導軌有多個孔(比如4m的25mm規格直線導軌有67個孔),機床一般通過鑽削頭與直線導軌進行多次相對移動完成鑽孔,這樣前面和後面的孔距會積累誤差,行業俗稱「累積誤差」。累積誤差產生的原因有導軌材質不均勻導致鑽孔時伸長或縮短沒有規律、機床自身定位精度不足、鑽孔速度超過主軸精度或剛性允許範圍及機床設計方案不合理的系統性誤差等。
直線導軌安裝孔的加工要求
如圖1所示,直線導軌安裝孔沉孔、孔口倒角、底孔的尺寸和中心距有一定精度要求,底孔倒角精度要求低。其中,中心距精度最為關鍵,相鄰孔距精度無須像有的企業要求的±0.05mm以內那麼高,但累積誤差必須要控制好。以25mm規格導軌為例,德國某品牌直線導軌安裝孔中心距公差圖樣要求只是±0.3mm,但包含了累積誤差。本文建議直線導軌任意兩孔的中心距公差標準按±0.2mm控制。
圖1 直線導軌安裝孔加工要求
一般的直線導軌鑽孔機方案分析
(1)採用導軌移動、鑽削頭固定的直線導軌鑽孔機。這種鑽孔機佔地面積很大,一般採用4個動力頭分別從導軌兩側鑽孔,導軌卧式,逐個孔依次移動完成所有孔的鑽削。
這種鑽孔機對導軌移動又有兩種驅動方案。一是伺服機構整體拖動直線導軌全長範圍連續移動(下稱「導軌全行程伺服驅動移動四主軸加工」方案),此方案鑽孔精度可達到要求,但換型號不方便;二是在行程很短的伺服滑台上安裝可以移動的液壓虎鉗、配合固定虎鉗交換夾緊和鬆開直線導軌,每次移動一個孔位,完成直線導軌全部孔的加工(下稱「導軌液壓夾緊交換驅動四主軸加工」方案),這種方案孔距累積誤差難以做到合格,比如,相鄰孔距偏差即使只有0.01mm,60多個孔,累計偏差就超過了0.6mm,由於導軌鑽孔時伸長或縮短重複性差,即使通過數控系統補償滑台誤差,累積誤差也難以穩定解決。
(2)單主軸移動、分工步加工方案。即採用1個傳統的單頭動柱鑽孔機,先鑽完所有底孔,再回去從第一個孔開始逐一鑽沉孔、沉孔孔口倒角,各工步分次鑽削,採用這一方案的國產機床成本比較低,但效率也很低。
(3)單主軸移動、成型複合刀加工方案。採用複合鑽頭1次鑽削底孔、沉孔和孔口倒角,刀具成本很高,對機床剛性要求非常高。
(4)雙主軸單驅加工方案。此方案是在傳統動柱鑽孔機的Z軸滑板上固定安裝兩個主軸,配合完成底孔、沉孔和孔口倒角。方案與「單主軸移動、成型複合刀加工方案」相比,效率相當,但刀具費用有所降低,沉孔還是必須完全用成型刀鍃孔,刀具消耗成本仍然比較高。
(5)三主軸單驅加工方案。此方案是在傳統動柱鑽孔機的Z軸滑板上固定安裝3個主軸,配合完成底孔、沉孔和孔口倒角。方案與「雙主軸移動、主軸單驅加工方案」相比效率有所提升,刀具費用降低,但3個頭固定,鑽頭更換時調整麻煩,加工效率與沉孔深度和倒角均勻性質量難以兼顧,工人往往會犧牲加工質量。
(6)三主軸三驅加工方案。此方案是在動柱鑽孔機的立柱上安裝3個滑台,每個滑台上安裝一個鑽削頭,每個鑽削頭獨立通過伺服驅動鑽孔。3個主軸可以獨立控制深度,配合完成底孔、沉孔和孔口倒角。方案與「三主軸移動、主軸單驅加工方案」相比效率明顯提升,刀具費用降低。本機優點是效率較高,質量合格率高。缺點是機床成本較高。
(7)三主軸三驅加工方案加底面倒角。此方案是在「三主軸移動、主軸三驅加工方案」的基礎上,底面加1個倒角動力頭,1次裝夾完成導軌所有孔的加工。本機優點是效率高、質量合格率高。缺點是機床成本高。
本文研發的直線導軌鑽孔機
方案如圖2所示,方案說明:
圖2 本文直線導軌鑽孔機方案
1.鞍座 2.立柱 3.三組雙聯銑削主軸 4.工作台與夾具 5.床身
(1)本文方案是在主軸三驅加工方案的基礎上,將單排的三主軸更改為三組雙聯銑削主軸,研發設計出一種新型的「雙排三主軸三驅加工方案」的直線導軌鑽孔機,同時鑽削兩根導軌,成倍地提高了加工效率。
(2)本文直線導軌鑽孔機的三組雙聯銑削主軸。如圖3所示,為本文自主研發設計的雙聯精密銑削主軸,採用高剛性精密主軸軸承組合,控制主軸軸向圓跳動和徑向圓跳動精度都在0.01mm以內,這樣的主軸可以用於自銑直線導軌安裝定位面、保證兩條導軌定位基準面與兩排主軸的同步平行度,鑽孔時定位精度較高,無須中心鑽定位即可滿足鑽孔定位精度的要求。
圖3 三組雙聯銑削主軸安裝
(3)雙排三主軸三驅加工方案高質量高效率工作的原理。如圖4所示,每排的3個主軸配合對應1根直線導軌,1次成型加工兩根導軌的底孔、沉孔和孔口倒角。每排第一個主軸安裝略小於沉孔的標準鑽頭定位、鑽沉孔,留少量餘量;第二個主軸以第一個主軸所鑽孔自動定心鑽削餘下部分厚度,同心度控制好;第三個主軸安裝帶導柱的成型鍃孔刀,鍃沉孔少量的餘量和倒角,切削量小,表面質量好。由於沉孔的大部分切削工作量由成本更低、鑽孔效率更高的標準鑽頭代替、大幅度降低了昂貴的成型鍃孔刀的消耗。
圖4 雙排三主軸三驅加工方案高質量高效率工作的原理示意
本方案可快捷地優化3組鑽頭配合分擔鑽削量,讓3組鑽頭工作時間更加平均,節省鑽削時間。
另外,底孔倒角可在機床自動鑽孔時間範圍內,由工人用普通設備手動完成,或者用另行配套的、很低成本的全自動氣動倒角機完成,不影響整體鑽孔效率和質量水平。
(4)本文方案的機床主軸布局分析。本文方案鑽孔範圍包括了滾珠導軌和滾柱導軌從15mm到65mm的全部規格,相鄰孔距有30mm、40mm、52.5mm、60mm、80mm、105mm、120mm等尺寸,採用覆蓋上述孔距的最小公倍數方案,並考慮調整效率、機床成本及加工效率等因素,將上述3組主軸兩兩之間中心距分240mm(參考圖4)和315mm兩種距離布局,只需調整1次就可以滿足上述所有孔距的加工要求,本文設計了快速定位調整裝置,調整非常方便快捷。
(5)X軸動柱驅動方案分析。本文採用自身已經成熟應用到型材加工中心的齒輪齒條驅動方案,並選用高精度磁柵尺作閉環控制,以保證精度的穩定性。本文在床身設計上也預留了動螺母滾珠絲杠驅動方案,供更加信任滾珠絲杠傳動方案的用戶選擇。
(6)夾具設計與夾緊方案分析。集中控制的壓緊機構,保證定位夾緊可靠。可調整壓緊頭,能適應不同型號導軌快速換型調整。由於導軌形狀差異很大,有的側面上下等寬,有的不等寬,因此,除15mm型號採用兩邊抱住夾緊外,其餘型號都只壓緊導軌下側面,而在頂面的另一側設置防止導軌翻轉的限位蓋(見圖5)。
圖5 夾具示意
排屑排水方便:機床設計成多個型號共用1套夾具,在夾具上設計有導軌鑽孔避空孔位,這些孔位具有排水功能,同時,在夾具支撐強度允許範圍內,在每兩個壓緊頭之間設計了排屑槽,鑽屑可直接掉入下面的自動卷屑槽,清掃非常方便。
本文設計的直線導軌鑽孔機鑽孔能力解析
本文設計採用1個主軸電動機,通過3∶1減速比的減速機構帶動1組兩個主軸轉動,設計了主軸強製冷卻系統,允許主軸不間斷地長時間工作。
(1)最小鑽孔能力評估。制約最小鑽孔能力的是主軸轉速,如果採用硬質合金鑽頭,需要的最高轉速約3 000r/min,本文採用10 000~12 000r/min的伺服主軸電動機,可以滿足用戶要求。
(2)最大鑽孔能力評估。制約最大鑽孔能力的是主軸輸出轉矩,45mm規格直線導軌沉孔直徑為20mm,65mm規格直線導軌沉孔直徑為26mm,選用7.5kW/47.7N·m主軸電動機,主軸輸出最大轉矩超過170N·m,可以滿足所有孔的加工。如果用戶僅僅加工35mm以下導軌,可以選5.5kW/34.7N·m的主軸電動機。
(3)影響機床鑽孔能力的其他因素。機床各軸驅動力、機床各軸導軌的剛性、各軸滾珠絲杠及絲杠支撐軸承的承載能力等因素都會影響到機床的鑽孔能力,本文設計統一以鑽直徑26mm孔的要求進行設計匹配,以滿足各型號直線導軌的鑽孔要求。
(4)各種數控直線導軌鑽孔機方案對比分析(其中,A鑽孔時間為1根4m25mm規格導軌用時)如附表所示。
各種數控直線導軌鑽孔機方案對比分析表
結語
本文研發的新型直線導軌鑽孔機,設計了由三個獨立伺服軸驅動的三組雙聯減速精密主軸,已經生產的樣機加工100根4m25mm規格的直線導軌樣品經過檢測,任意兩孔孔距誤差全部在±0.2mm以內,絕大部分孔距誤差實測在±0.1mm以內、孔徑在設計公差範圍內、倒角均勻,加工質量合格。每兩根導軌加工時間可控制在10min之內(平均每根5min),加工效率是其他直線導軌鑽孔機的2~12倍,達到了高質量高效率的研發設計目標。
近期鼓勵投稿內容:工業機器人相關、維修與改造相關
《金屬加工》出品(其他投稿地址均為虛假信息)
熱門圖書排行

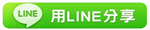
※非完全機加工面直徑測量工具
※卧式加工中心高精度同軸孔調頭加工找正
TAG:機工機床世界 |