3D混合製造技術改變射頻接插件工藝
原標題:3D混合製造技術改變射頻接插件工藝
來源:微波模擬論壇
微波器件指天線/功分器/PA功放/波導等等,安裝在衛星/飛機上的部件需要輕質化,一般採用鋁合金製造,但器件一些部分之間需要絕緣處理。
能否一體化3D製造,節省製造成本且降低組裝調試費用?
大幅度的減輕產品重量呢?
採用新型的塑料成型技術:3D混合製造可以到達要求,3D混合製造步驟是3D列印成型/激光LDS選擇性沉積金屬。
採用這種工藝的好處是節省了製造時間和實現了複雜的饋源/波導等器件的一體化免安裝調試,且帶來的另外好處是大幅度減輕了產品重量。下面舉例說明:
波導器件
傳統的波導式金屬材料製造,見下圖
美國從事製造衛星微波器件設計的工程師,希望採用3D混合製造技術來替換以上軍用金屬波導器件:先3D列印成型,再在內部牆壁金屬化,這個部件重量只有金屬工藝的15%,即節省了85%重量!這對衛星和飛機中微波通訊系統減重意義非凡!
射頻接插件
射頻接插件,是在無線通訊設備中廣泛使用的一種元件,傳統的都是金屬件車削加工後電鍍。困擾著這行業之技術難點是3G以上頻段的接插件難以控制品質:光潔度、電鍍層質量關乎射頻阻抗。另一個困難就是降低製造成本。
「3G以上的射頻線和接插件真能合格的不多」撰寫{實用無線電}一書的作者,曾開發出國產射頻網路分析儀的我國知名的射頻專家胡樹豪先生曾對我說。因此,我比較留意這個領域的技術進步。 全塑射頻接插件在LDS技術起來前,不能實現,是基於:
第一:塑料電鍍層抗剝離指標差;
第二:電鍍層厚度不便於精確控制;
第三:電鍍層剛性太強,彈性不足;
第四:不能精確實現選擇鍍,不需要金屬的部分不好遮蔽。
然而,LDS是一種在塑膠上選擇性沉積金屬方法。其在塑膠上是存在根,並據此化學生長的金屬層,克服了以上所有缺陷。並且可以通過手機和汽車行業嚴格的高溫高濕後抗剝離測試。因此,開始發揮注塑件製造便宜、產能大優勢,導入到射頻接插件領域,下圖是採用注塑工藝製造的射頻接插件,再選擇性金屬化
下圖是注塑模具及其注塑件:
3D構型天線
大型的軍艦上面天線,需要考慮減輕重量,美國隱形軍艦採用了一種塑料技術製造的3D分形天線,其組件是3D列印成型的,見下圖:
事實上,很多3D構型且要選擇性金屬化的天線,且可以採用本文提到的混合製造技術:
否則採用傳統的FPC和電路板技術,安裝誤差大,調試難度高,重量重。當然製造成本也高。
3D混合製造技術是剛出現的新工藝,還不為行業所知,需要廣大微波工程師/工藝師多推廣。

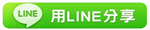
※韓自研反坦克導彈實現「發射後不管」
※美陸軍研發過渡防空系統
TAG:裝備參考 |