先進封裝挑戰愈發嚴峻|半導體行業觀察
來源:內容由 微信公眾號 半導體行業觀察 (ID:icbank) 翻譯自「Semiconductor Engineering」,謝謝。
使用現有的檢測工具來發現缺陷變得愈發困難,但升級到新技術的成本很高。
目前用於封裝的缺陷檢測系統已經無法應付最新的先進封裝,這促使市場需要新的工具。
作為回應,一些供應商正在推出新的缺陷檢測系統,用於各種先進封裝,例如2.5D / 3D技術和fan-out技術。新的缺陷檢測系統比以前的工具更強大,但也更昂貴。封裝廠可能需要購買不同類型的工具。
所有這一切都發生在業界試圖降低先進封裝的整體成本之際。多年來,業界一直使用各種檢測設備來定位IC封裝中的缺陷。現有的缺陷檢測系統適用於商用封裝,也適用於目前市場上的先進封裝類型,如2.5D / 3D技術、fan-out技術等。
但是最新的先進封裝正在向更精細的特徵遷移,擁有更多層和更多I/O。因此,缺陷變得越來越小,使用當前的檢測系統很難找到缺陷。無法檢測缺陷會直接影響器件的良率。
KLA-Tencor先進營銷主管Stephen Hiebert表示:「在許多情況下,適用於大尺寸的核心檢測技術,例如第一代嵌入式晶圓級球柵陣列(eWLB),現在已經失效,新的檢測技術正在部署。你曾經有(用於IC封裝)的宏觀檢測(macro inspection)。現在,這些用於先進封裝的工具必須能夠發現微米級和亞微米級的缺陷。」
例如,嵌入式晶圓級球柵陣列(eWLB)是市場上各種fan-out封裝之一。通常,fan-out是通過封裝內的再分布層(RDL)中的線和空間特徵來測量的。RDL由封裝中布置的銅金屬連線組成。線和空間是指金屬跡線的寬度和它們之間的空間。
圖1:再分布層(RDL)用於將連接重新布置到所需位置。 (來源:Lam Research)
隨著更複雜的晶元集成到fan-out封裝中,更多的具有更細連線和空間的RDL層可能會成為必須。例如,今天的fan-out的封裝範圍從5μm及以上連線和空間(5-5μm),到2-2μm及以下不等。
TechSearch International總裁Jan Vardaman表示:「隨著公司轉向下一個技術節點,凸點間距(bump pitch)變得更加精細,檢測能力必須提高。隨著特徵(連線和空間)縮小到2μm及以下,發現缺陷變得更加困難。此外,在一些應用中,發現通孔中的碎片成為了一個問題。」
總而言之,行業需要新的缺陷檢測系統,以應對最新的先進封裝。這些功能在汽車等多種應用中至關重要,因為這些應用需要零缺陷。其他市場也需要這些能力。
為了應對這些挑戰,KLA-Tencor、Rudolph和其他公司最近推出了用於先進封裝的新型光學缺陷檢測設備,它可處理5μm及以下的RDL。此外,供應商還為裸片分揀生產階段引入了新的紅外檢測工具。
封裝的趨勢
多年來,IC市場的重點一直圍繞著傳統的晶元微縮,在器件中加入更多功能,然後在每個工藝節點上縮小器件。封裝是事後才想到的,只是把器件裝起來而已。
然而最近,晶元在每個節點處的微縮都變得更加昂貴和複雜。如今,只有少數人能夠負擔得起在先進節點上設計晶元的費用。例如,根據IBS的數據,僅IC設計成本就從28nm平面器件的5130萬美元躍升至7nm晶元的2.978億美元。
這並不代表晶元製造商已經停止微縮。但模擬、射頻和其他晶元技術並不需要先進節點,這些技術正在快速發展。聯華電子市場營銷高級副總裁Steven Liu表示:「我們確實預計汽車和諸如電源管理、射頻和嵌入式非易失性存儲器等專業技術將穩步增長。」
先進封裝是其中的一部分。從世紀之交之後,行業開始尋找晶元微縮的替代方案,這便是先進封裝。先進封裝背後的思想是在垂直方向上集成裸片,而不是在單片裸片上微縮特徵。
幾十年來,先進封裝一直以有限的形式在小眾應用中使用。問題在於成本,因為這種技術對許多應用而言仍然過於昂貴。
隨著行業朝著所謂異構集成的概念發展,先進封裝仍在繼續取得進展。GlobalFoundries負責封裝研發和運營的副總裁David McCann表示:「在封裝和測試方面,我們需要做出貢獻的關鍵領域是異構集成。這樣,無論是一個節點還是多個節點,都可以封裝多個晶元,甚至可以將多個供應商導入集成封裝級別。」
舉一個這種趨勢的例子,行業推出了2.5D技術。在2.5D中,裸片堆疊在包含硅通孔(TSV)的中介層(Interposer)的頂部,中介層充當晶元和板之間的橋樑,提供更多的I / O和帶寬。
圖2:帶有中介層的2.5D封裝中的FPGA + HBM。(來源:Xilinx)
McCann表示:「2.5D使互連密度增加了一個數量級。你要解決的是內存帶寬和延遲。這就是擁有非常細的連線和空間的中介層的目的。」
例如,GlobalFoundries已經推出了2.5D / 3D技術,其TSV為5μm(直徑)×55μm(深度)。達標的TSV為2μm x 20μm。
其他封裝正在向更精細的特徵靠攏,即fan-out。在fan-out中,裸片在晶圓上就被封裝了。
圖3:Fan-Out WLP (來源:Lam Research)
十多年前引入的fan-out最初的RDL尺寸很大,I/O很少。相比之下,今天的高密度fan-out擁有超過500個I/O和小於8μm的線/空間。台積電的InFO技術是最著名的fan-out技術,應用在了最新的iPhone手機中。
KLA-Tencor的Hiebert表示:「今天,我們看到了一個數量級的微縮。我們看到了2μm的RDL用於生產,1μm及以下的RDL正在開發中。」
有些fan-out封裝有三到四層RDL。Hiebert表示:「業界正在努力轉向更多的RDL層,更精細間距的RDL層,以及更大的封裝。如果你有fan-out或多裸片fan-out,則佔用空間會更大。隨著封裝的擴大,層數的增加和RDL的縮減,所有這些都會帶來巨大的良率挑戰。發現和控制缺陷至關重要。」
這就是缺陷檢測所適用的地方。ASE的銷售和業務開發總監Eelco Bergman表示:「隨著連線和空間越來越細,挑戰變得越來越艱巨。」
Bergman表示:「隨著你轉向更精細的RDL,尤其是多層RDL,你該如何檢測質量?你需要一些監控內聯性能的機制,以推動流程優化,並儘可能提高良率。 而對於其他情況,你可能至少需要一些後製造(post-fabrication)驗證能力。」
這只是對於fan-out技術的挑戰。2.5D/3D封裝還有其他挑戰。還有其他類型的封裝正在開發中,例如chiplet,這可能會導致新的封裝方法。
chiplet更像是一種LEGO-block類型的方法,使用互連結構將各種預先開發的硬IP塊連接在一起。DARPA正率先朝這個方向努力,以降低成本和縮短上市時間,許多公司也在探索類似的選擇,包括英特爾、eSilicon和高通。
Kandou Bus首席執行官Amin Shokrollahi表示:「我們的目標是將晶元的所有功能都放在更小的裸片上並增加靈活性。你可以將神經網路的不同部分分配到chiplet上,但為了靈活性,裸片的布置非常重要,空間必須非常短。」
這些chiplet封裝最終的樣子還不清楚,檢測的挑戰也不清楚。儘管如此,總體趨勢與其他類型的封裝一樣,都是縮小距離和整體面積,以提高性能和減小功率和面積。
檢測的作用
為了發現缺陷,封裝公司使用缺陷檢測、計量工具和故障分析系統。檢測是發現產品缺陷的藝術,它在晶圓廠和封裝廠都有使用。這不能與計量混淆,計量是指測量和表徵器件的結構。
晶圓廠和封裝廠使用不同的檢測系統,儘管二者都在努力實現類似的目標——他們希望找到並消除器件中的致命缺陷,從而提高良率。
在晶圓廠中,晶元以納米級測量,缺陷有時是在埃級。為此,晶元製造商不得不使用昂貴的電子束和光學晶片檢測系統。
在封裝中,缺陷尺寸更大,在微米或亞微米級別進行測量。封裝廠使用基於光學、紅外和其他技術的工具。
通常,晶圓廠和封裝廠的檢測要求不同。Rudolph technologies公司企業營銷高級總監Tim Kryman表示:「儘管先進封裝工藝的發展可能只是前端技術向後端操作的遷移,但包裝過程創造出的結構和使用的材料通常不會出現在前端。因此,它們有獨特的檢測和測量要求,現有前端工具無法滿足這些要求。」
在很大程度上,檢測對於封裝而言相對便宜,但在某些環節正在發生改變。Kryman表示:「這些供應商面臨的挑戰是不斷變化的經濟模式。傳統上,封裝被認為是低技術和低成本的。低價格和低利潤率給企業帶來了持續的壓力,迫使他們將運營成本和資本成本降至最低水平。先進的封裝工藝現在需要對傳統上在前端工廠中發現的設備和技術進行投資。」
發現缺陷
在傳統的內聯封裝流程中,封裝廠使用基於光學的高速缺陷檢測系統。Camtek,、KLA-Tencor、Rudolph等公司在此市場銷售系統。
較舊的檢測工具適用於大多數封裝類型,並將繼續使用多年,但對於最新的2.5D/3D和fan-out技術而言,情況就不同了。
通常,檢測工具可以發現臨界尺寸三分之一到二分之一大小的缺陷。例如,有一段時間,封裝廠正在開發一種10μm RDL的封裝。為此,他們要使用能夠檢測出3μm及以上缺陷的檢測系統。
但這對於最新的封裝而言還不夠好,這些封裝的RDL在5μm及以下。因此,供應商需要可以發現2.5μm及以下,甚至亞微米級缺陷的檢測工具。
KLA-Tencor公司的Hiebert表示:「這些工藝變得越來越複雜。因此,使用檢測和計量數據有更多的內聯監測。而且你利用它來把良率從研發提高到大批量生產的水平。許多能夠在10μm或20μm RDL運行的檢測技術確實面臨著達到1μm或更低水平的挑戰。」
這包括最新的fan-out封裝。在fan-out封裝工藝中,晶元首先在晶圓廠的晶圓上加工。然後將晶元切割,並放置在一個類似晶圓的基於環氧樹脂塑封料的結構上。
然後在頂部創建多層RDL堆疊。為了製造RDL,先在表面沉積一層銅種子層。然後對所需的RDL結構進行圖案化和顯影。
此時,結構需要進行缺陷檢測步驟。如果存在缺陷問題,封裝公司可以通過重新加工晶圓來解決問題。
然後,完成該步驟後,就進行剩餘的RDL步驟。對每個RDL層重複這個過程。
封裝生產完成後,要進行最後的缺陷檢測步驟。總的來說,三到四個RDL層的fan-out封裝可能需要10到15個內聯檢測步驟。
但是,即使進行了所有這些步驟,仍然很難發現所有的缺陷。Yole development的分析師Amandine Pizzagalli表示:「對於先進封裝應用而言,存在許多缺陷挑戰。」
JETET集團技術戰略總監Seung Wook Yoon指出,目前的先進封裝至少存在三個主要的缺陷挑戰。「首先,微小或纖薄的異物/殘留物可能存在於介電層中的小通孔的底部。第二,當空間狹窄且金屬線高(大高寬比)時,金屬線和空間(溝槽結構)處會有纖薄的金屬橋接。第三,多層RDL檢測對於檢測更細的線寬和線間距中的異物具有挑戰性。」
反過來,這也推動了對更好的檢測的需求。Rudolph公司的Kryman表示:「與前端一樣,不斷縮小的特徵尺寸正在推動檢測要求,以提高精度、靈敏度和吞吐量。RDL線的幾何形狀已經小於10μm,並且在缺陷靈敏度大約為印刷線和空間尺寸的50%的情況下繼續縮小。凸起(Bump)尺寸、間距(pitch)和高度也在持續下降。製造商還面臨著封裝工藝多樣性和需求快速變化的挑戰。」
其中一些需求是封裝本身的結果,這是目前正在開發的各種新方法背後的推動力,以限制諸如翹曲之類的問題,翹曲本身可能導致缺陷。實際上,在實際封裝之前的幾步就要解決這個問題。
Brewer Science高級技術研發執行總監Rama Puligadda表示:「一種選擇是使用薄膜預粘合(thin film pre-bond),在塑封料(mold compound)的模板內放置晶元。結果就是沒有翹曲,這是EMC(環氧樹脂模塑塑封料)日益嚴重的問題。你也可以採取更模塊化的方法來減少翹曲。」
無論如何,檢測都需要識別新的和複雜的模式。「像fan-out這樣的應用的金屬圖案往往非常複雜。與前端應用相比,我們看到了更多不規則的形狀。我們看到了對角線。我們看到了本質上不是電氣的其他結構。我們看到由於熱或結構原因插入到金屬層的結構。」
同時,為應對這些挑戰和其他挑戰,KLA-Tencor、Rudolph等公司推出了新的光學缺陷檢測工具,適用於5μm及以上的RDL。
供應商的最新系統使用明場(brightfield)和暗場(darkfield)技術。在明場成像中,光點直接位於樣品上方。光照射到樣品上,系統收集來自物體的散射光。在暗場成像中,光從一個角度照射到樣品上。這兩種情況都對數據進行了缺陷分析。
每個供應商還在其系統上提供不同的功能。KLA-Tencor的新型Kronos 1080系統旨在檢測先進的晶圓級封裝工藝步驟。它提供了靈活的基板處理,支持粘合、減薄、翹曲和切割的基板。該工具使用一種稱為FlexPoint的技術,該技術將系統集中在裸片的關鍵區域。這是缺陷產生最大影響的地方。
與此同時,與之前的版本一樣,Rudolph公司的新型Dragonfly G2平台將2D和3D檢測和計量功能整合在一個平台中。但它具有更高的吞吐量和靈敏度。它可以檢測小至1μm的缺陷。此外,它還增加了一種檢測非視覺缺陷的技術。
更多檢測
在這個過程之後,封裝移至最終的測試和組裝,有時稱為晶元電特性揀選(die sort)。這個過程對封裝進行切割和檢測。
這裡可能會出現幾個問題。今天的器件中使用的低k材料是脆弱的。在切割或其他步驟,裂縫可能出現在fan-out封裝的側面,以及存儲器封裝和裸片上。
KLA-Tencor 公司ICOS部門總經理Pieter Vandewalle表示:「這些材料在切割過程中更容易破損和斷裂。一些新的缺陷出現了,比如這些切割裂縫,這需要新的檢測方法。」
針對這一應用,KLA-Tencor公司已經通過一種基於紅外技術的系統進軍晶元電特性揀選市場。KLA-Tencor新推出的ICOS F160系統可進行檢測和模具分揀。該工具還支持六面光學檢測功能。
與此同時,Mühlbauer和其他供應商也在晶元電特性揀選領域展開競爭。
前進的道路
隨著行業正在加速下一代封裝,新的檢測工具隨之而來。這些系統希望可以解決良率/缺陷問題。
不過,行業必須解決成本問題。一般而言,先進封裝對於許多OEM仍然太昂貴。蘋果和其他一些公司例外。
這必須改變。傳統的晶元微縮變得非常昂貴,許多OEM正在更加嚴格地看待先進封裝,問題是,封裝公司能否應對下一波技術的成本和良率挑戰。

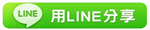
※蘋果iPhone Xs Max拋棄了這兩家晶元供應商?|半導體行業觀察
※蘋果高通英特爾三方混戰,基帶晶元難在哪裡?|半導體行業觀察
TAG:半導體行業觀察 |