硬核航空 整體葉盤在國外發動機中的應用分析
1 概 述
通常,壓氣機及風扇的工作葉片(即轉子葉片)均用其葉身下的榫頭(多為燕尾形)裝於輪盤輪緣的榫槽中,再用鎖緊裝置將葉片鎖定於輪盤中。
20世紀80年代中期,在航空發動機結構設計方面,出現了一種稱之為「整體葉盤」或簡稱「葉盤」(Blisk)的結構。它是將工作葉片和輪盤做成一體,省去了連接用的榫頭、榫槽,使結構大為簡化。
整體葉盤的英文名詞 Blisk是由葉片blade的前兩個字母與輪盤disk後三個字母組合在一起形成的一個新詞,它較形象地表達了這種結構的特點,即它是一種合二(葉片、輪盤)為一(整體葉盤)的結構。
在壓氣機中,葉片與輪盤做成一體,並不是近期的設計,早在20世紀60~70年代研製的一些小型發動機的軸流 離心組合式壓氣機中,為了簡化軸流壓氣機轉子的結構,減輕重量,其葉片多做成小展弦比、片數少,這時常將葉片和輪盤做成一體。
例如美國特里達因CAE分公司(當年為大陸公司航空工程分部)於20世紀50年代按法國透博梅卡公司專利仿製瑪爾波2型渦輪噴氣發動機,並命名為J69T 25,其推力為450daN;隨後,在60年代初期發展了該發動機的推力增大型J69 T 29,推力增加到750daN。
為了提高推力所採用的主要措施是在離心式壓氣機前增加一級軸流式壓氣機以提高增壓比與空氣流量,如圖1所示。這個新增加的軸流壓氣機轉子直徑約為300mm,共有17片葉片,它的葉片、輪盤與軸即做成一體,既可用17 4PH沉澱硬化不鏽鋼精鑄後經拋光而成,也可用403合金鋼鍛制後經機械加工而成。
又如,法國透博梅卡公司於20世紀70年代初期開始研製並於1978年投入使用的阿赫耶發動機,如圖2所示。其壓氣機採用了1級軸流與1級離心式壓氣機組合的混合式壓氣機,軸流式壓氣機轉子的葉片與輪盤即做成一體,是用TA6VPQ鈦合金鍛制後在5坐標數控銑床上銑削加工而成。
圖1 J69 T 29發動機結構圖
對於這些小型發動機軸流壓氣機中採用的葉片與輪盤做成一體的結構,由於直徑小、葉片數少,當時均稱它們為「整體轉子」;後來,加拿大普惠公司則稱它們為「帶葉片的整體轉子」
圖2阿赫耶發動機結構圖
(IntegralyBladedRotor,IBR)。例如,該公司於1992 年開始研製的、推力為11.58~17.26 kN 的小型渦扇發動機PW500系列(如圖3 所示),其第1個型號PW530(推力為11.58kN)
已於1995年12月取得適航證,它的風扇轉子及高壓壓氣機中的2級軸流轉子(高壓壓氣機由2級軸流與1級離心壓氣機組成)均將葉片與輪盤做成一體;1996 年12 月取得適航證的PW500系列第2個型號PW545.(推力為17.26kN)在風扇後增加了一級增壓(低壓)壓氣機,
該型發動機除風扇轉子與2級高壓壓氣機外,增加的1級增壓壓氣機的轉子也做成整體的,該公司均稱這些轉子為IBR,而未稱它們為Blisk。由此可以看出整體葉盤是指那些直徑較大、葉片數多的將葉片與輪盤做成一體的結構。但實際上對於一些小型發動機的轉子,很難分出是屬於帶葉片的整體轉子IBR,還是屬於整體葉盤Blisk。
圖3 PW500系列發動機結構圖
但是,不論如何稱呼這種將葉片與輪盤做成一體的結構,它們的特點是相同的,為了敘述方便,在以下分析中,均用整體葉盤Blisk的名稱,且偏重於直徑較大、葉片數多的結構。
2 整體葉盤結構設計特點
將葉片與輪盤做成一體後,首先輪盤的輪緣處不需加工出安裝葉片的榫槽,因而輪緣的徑向厚度可以大大減小,從而使轉子重量減輕。
例如,F414發動機中的第2、3級風扇轉子採用整體葉盤後,使轉子重量減輕20.43kg,轉子重量減輕後,將會對整台發動機減重起到較大作用(F414發動機與其原型機F404相比,推重比由7.5提高到9.0);羅·羅公司的研究指出,採用整體葉盤結構與傳統的葉片輪盤結構相比,重量最多可減少50%,若採用金屬基複合材料(MMC)的整體葉環(Bling),則可減重70%,如圖4所示。
其次,使發動機零件數目大大減小,這不僅是由於葉片與輪盤做成一體而得到的,而且也是由於減少了每片葉片的鎖緊裝置而獲得的。前述的F414發動機,高壓壓氣機前3級也採用了整體葉盤,即它共用了5級整體葉盤,使發動機零件數減少了484件,這的確是一個不小的數目,零件數減少,不僅使成本降低,而且也可以提高發動機的可靠性。
另外,採用整體葉盤還可以消除在常規用榫頭連接葉片與輪盤的結構中,氣流在榫頭與榫槽縫隙中逸流所造成的損失,還可以避免由於裝配不當或榫頭的磨蝕,特別是微動磨蝕、裂紋及鎖片損壞等帶來的故障。
由於整體葉盤有這些特點,因而自EJ200發動機採用後,已被一些現代的軍民用發動機採用,特別是最近幾年推廣及使用更為迅速。
為什麼在小發動機中,早在20世紀60年代就推廣整體轉子,而整體葉盤卻遲遲不能出現,這主要有兩個問題,其一是加工問題,對於小尺寸、葉片數目少的轉子,既可以用精密鑄造加工,也可以用鍛件在5坐標數控銑床上加工,但對於大尺寸、多葉片的整體轉子卻較難用上述方法來加工;其次是如何保證損壞1片或幾片葉片後,不會帶來過大損失的問題。
工作葉片常常會在工作中被外來物打傷,造成卷邊、開裂、掉塊,或由於振動而造成的裂紋等。在用榫頭連接的結構中,可以更換單個損壞的或有缺陷的葉片,而整體轉子卻不能更換葉片,因此,有可能因1片葉片損壞而使整個整體葉盤報廢。
綜上所述,如果不解決這兩個問題,整體葉盤這一具有特殊意義的結構,很難得到廣泛應用的。
圖4、整體葉盤、葉環減重效果簡圖
在驗證機上,高壓壓氣機採用了兩排可調靜子葉片,即0級與1級。0級即進口可調葉片內環處不帶內緣板,僅有軸銷,在原型機上可調靜子葉片改為一排(進口導流葉片),這是由於在驗證機試驗中發現壓氣機僅用一排可調靜子葉片就能滿足在各種轉速下壓氣機有較好的穩定工作能力;另外進口導流葉片在原型機上改為內環處帶內緣板,這是為了增加抗擊外物打擊的能力。試驗中改型的進口導流葉片承受了吸入兩隻鳥的打擊而未損壞的考驗。
============================================
3.2 懸臂靜子葉片改為內環處帶內緣板
驗證機中,高壓壓氣機各排靜子葉片均採用懸臂結構,即內徑處不帶內緣板,在原型機階段,將靜子葉片改為帶內緣板的,且4片焊在一起形成靜子葉片扇形段,其內徑處釺焊上蜂窩封嚴環帶。採用這種結構可以避免在大的過載下轉子有較大彎曲變形時,或者發動機由於軸
承損壞造成嚴重故障時,靜子葉片與轉子鼓筒間發生摩擦,甚至導致靜子葉片切入鼓筒事故的發生。
為降低靜子葉片生產成本,在原型機階段對靜子葉片做了大的改進。在原型機初始設計中,帶內外緣板的靜子葉片是單個地用電化學加工出來的,然後4個葉片釺焊成一扇形段。
圖10、釺焊再切成扇形段的靜子組件
這種加工方法既費工又昂貴。在改進中,將不帶外內緣板的葉片插入開有葉型槽的內外兩個環形件中,環上的葉型槽是用激光加工出來的,在所有葉片插入環形件後再送入真空爐中加溫釺焊,然後將焊好的組件切割成一段一段的4個葉片組的扇形段,如圖10所示。
3.3 雙層機匣
EJ200發動機中,高壓壓氣機4~5級機匣做成雙層的,這是現代高總壓比發動機中慣用的設計。因為沿發動機軸線看,高壓壓氣機後幾級機匣是內涵機匣中直徑最小處,俗稱之為「縮腰」。
發動機出現縮腰後使縱向剛性變弱,在飛機作機動飛行時,機匣會變形造成後幾級處葉尖間隙沿圓周不均勻,甚至出現葉尖碰磨機匣。為此,絕大多數發動機均在縮腰處做成雙層機匣,內機匣僅作為氣流的包容環及固定靜子葉片的環形件,承受氣動負荷;外機匣則作為承力結構,一般均將直徑加大很多以增加發動機的縱向剛性。
在驗證機中,1~3級機匣做成單層的;但在驗證機、生產型發動機中採用了雙層結構。這是為了減少發動機在承受過大的機動載荷時不會對葉尖間隙產生不良的影響。為了保持每一級沿圓周有較均勻的葉尖間隙,內機匣做成整環形的,沿軸線則做成一段一段的,各段間用短螺柱連接。
4~5級內機匣做成三角形的結構,以加大縮腰處的縱向剛性。為了便於裝配,靜子葉片做成帶安裝邊的扇形段(如圖10所示),掛在內機匣內的固定環上,即渦輪中常用的「掛鉤式」安裝方式。
圖11、鈦合金機匣結構圖
3.4 防鈦火設計
高壓壓氣機外機匣採用鈦合金製成,內機匣中,除第5級採用Incoly合金外,其餘4級機匣均由鈦合金製成,由於這4級的葉片也採用了鈦合金,這就容易引起鈦著火的嚴重問題。
為避免鈦火的發生,在鈦機匣內徑對應工作葉片的環形帶上,設有防鈦火的氧化鋯陶瓷塗層作為保護裝置;其內還塗有易磨塗層,其結構如圖11所示。
高壓壓氣機中採用鈦合金機匣時,須處理好防鈦火問題及提高包容性問題,機匣做成雙層結構,自然解決了壓氣機的包容性問題。

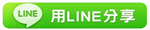
※膠布堵塞皮託管闖大禍 導致70人遇難的秘魯航空603號航班
※膠布堵塞皮託管闖大禍 墜毀的波音757和70人遇難的秘魯航空603號航班
TAG:航空之家 |