讓人腦洞大開的新材料和新工藝!
材料作為航空業發展的基石,在航空百年的發展歷程中充當了重要角色。時至今日,隨著人類對於飛行速度、舒適度要求的日益提高以及運營商對於飛機效率要求的日益苛刻,製造商不斷嘗試使用新材料和新工藝來提高飛機性能,以更好地滿足各方的要求。
從竹纖維到蜘蛛絲
儘管與傳統金屬材料相比,複合材料具有明顯的優勢,但在「綠色航空」的大背景下,這種材料卻有其天生的弱點——在生產過程中,複合材料在經過固化後很難再次分解和回收利用。因此,碳纖維複合材料的廢料往往只能通過填埋的方式進行處理,對環境造成了一定的影響。
為了解決這一問題,法國多家企業正在聯合進行一項名為「BAMCO」的項目,該項目旨在研發一種由竹纖維製成的新型生物基複合材料。這種更加環保的複合材料未來可用於替代玻璃、酚醛類樹脂基複合材料,應用在飛機的機艙內部蓋板、機身包覆蓋板和機載廚房等部位。
多項試驗數據表明,竹纖維比傳統的玻璃纖維質量更輕,卻擁有旗鼓相當的應力水平,這使得它可以成為「客艙內部具有簡單幾何形狀的非承力或次承力結構」等部位的理想替代品。為了降低生產和使用成本,在BAMCO項目中,研製團隊將這種基於生物材料的複合材料與傳統製造工藝相結合,這將對材料的批量化生產起到關鍵作用。目前,已有一些歐洲的客艙和部件製造商對這種新材料表現出濃厚的興趣。根據公開資料,歐洲麗薩航空將成為全球首家使用由新型生物基複合材料生產的駕駛艙部件的客戶。
與此同時,空客正在與德國AMSilk公司合作,共同研發一種利用合成蛛絲纖維製成的新型複合材料,並計劃於今年發布由這種新材料製成的產品。
這種由合成蛛絲纖維製成的新型複合材料被稱為「生物鋼」,是由慕尼黑工業大學的一項科研成果衍生出的新材料。簡單來說,這種新材料是一種由蛛絲蛋白製成的生物高分子材料。科研人員利用植入了蜘蛛基因的細菌發酵來獲得這種蛋白質,並將其應用到商業領域。
目前,阿迪達斯的部分運動鞋中已經應用了這種材料,它具有更輕的質量和更好的避震性。受此啟發,空客正在與AMSilk公司一起加速推進這種新材料的研發工作。如果進展順利,空客將成為全球首家使用這種「生物鋼」的航空企業。
波音在新材料的研發上也不甘落後。目前,波音正與HRL實驗室、加州大學爾灣分校共同研發一種比泡沫塑料還要輕100倍的超輕金屬材料。
這種名為「微晶格」(micorlattice)的材料,99.99%是中空結構,也就是99.99%是空氣,其餘0.01%是相互連接的3D多孔聚合物中空管,中空管的厚度只有頭髮絲直徑的千分之一。
據波音公司介紹,如果將一隻雞蛋包在這種材料里,從25樓扔下地面,雞蛋也不會有任何損傷,中空多孔結構使其具備了超高吸能特性,即便本體被壓縮50%之後也能輕易還原。
此外,這種新材料比泡沫塑料要輕100倍,和骨骼的構造差不多。在波音公開的一段視頻中,研究人員可以輕易地將微晶格金屬吹起來,它就像羽毛一樣輕輕地飄到空中,然後緩慢落地,很難想像這是一種金屬材料。波音表示,這種材料如果能夠應用于飛機製造,將大大降低飛機的重量,實現更高的燃油效率。
除了新材料研發之外,NASA的研究團隊還「異想天開」地試圖利用複合材料自身的結構和分子的排列組合來提高機翼效率。
空氣動力學研究表明,機翼的形狀對飛行效率有巨大的影響。從理論上來說,機翼設計的好壞取決於多種因素,如飛機的重量、飛行速度、飛行姿態等。從這個角度來說,剛性機翼並不是效率最高的機翼。為此,NASA的自適應數字複合航空結構技術團隊利用碳纖維複合材料,設計了在飛行過程中可以改變形狀的機翼,以求降低飛行阻力。
在這項研究中,NASA與美國麻省理工學院、康奈爾大學、加州大學聖克魯斯分校、加州大學伯克利分校和加州大學戴維斯分校合作,使用新的複合材料來製造一種能夠主動改變形狀的超輕型機翼。
在NASA的這項研究中,機翼由碳纖維複合材料構件單元組合而成。這些構件單元被組裝成晶格結構或以重複結構排列,構件的排列方式決定了機翼的彎曲方式。藉助制動器和飛行控制系統,機翼能在不同的飛行狀態下變成最合適的形態。NASA表示,這種更加智能的機翼最顯著的特點是可以通過減少由諸如襟翼、方向舵和副翼等剛性控制表面所帶來的阻力,從而提高飛機的空氣動力學效率。
更高效、更經濟
根據IATA發布的市場預測報告,2018年,全球航空公司共運送旅客43億人次,到2037年,這一數字將增長至82億人次。為了滿足航空運輸快速發展的需求,未來20年,飛機製造商至少需要交付36700架新飛機。
為了滿足產能提升的需求,一些創新的生產工藝應運而生。其中,非熱壓罐工藝進入熱固性複合材料主承力結構製造領域引發了複合材料製造體系的一場變革。由於熱壓罐的使用成本昂貴,同時還會限制生產效率,因此,擺脫熱壓罐的掣肘是複合材料生產過程中降本增效的關鍵。
2015年,NASA開始了第一次嘗試。其對一種翼身混合體飛機的非圓柱形複合材料壓力艙驗證件進行了測試,該驗證件採用了波音的非熱壓罐製造工藝。同年4月,俄羅斯航空複合材料公司交付了MC-21幹線客機第一套非熱壓罐工藝製造的複合材料中央翼盒,該機的機翼蒙皮也由非熱壓罐製造,這是大型民用客機第一次採用這一技術。
在有了製造工藝的支撐後,熱塑性材料開始逐步替代熱固性材料,在航空器承力部件中被更多地採用。
空客表示,在A350項目之前,公司已經將熱塑性材料應用在超過1500種零部件上。此外,在歐盟的框架計划下,空客還在加快大型熱塑性複合材料主承力結構方面的研究。龐巴迪公司則公開了一項新型熱塑性複合材料托架技術,適用于飛機機翼、中央翼盒以及油箱的液壓和燃油托架,使用這種新材料生產的零部件可比金屬材料零部件減重至少40%。
隨著技術成熟、成本降低,更多複合材料結構件製造商將從經濟性和周期短的角度,選擇非熱壓罐材料與工藝,這在複合材料結構件設計、製造流程,以及原材料和製造裝備供應鏈中掀起了一場新的變革,越來越多的企業參與到這場技術變革中。
總部位於美國的Tri-Mack塑料製造公司提供了一種「混合」熱塑性複合材料部件,其中具有單向纖維增強的熱塑性複合材料(用於提供強度和剛度)與注塑成型工藝相結合,以實現設計靈活性。堅硬的單向碳纖維會阻礙部件生產成各種複雜的形狀,而注塑成型為該部件帶來了額外的功能,克服了堅硬的單向碳纖維帶來的工藝性差的挑戰。Tri-Mack公司表示,整個工藝過程完全實現了自動化,比製造性能相同的熱固性複合材料部件周期更短。
此外,還有一些製造商另闢蹊徑,通過開發複合材料纖維的3D「編織」技術來提高生產效率。
法國製造商Saint-Gobain開發了一種用於複合材料纖維的3D「編織」技術,可以將熱塑性樹脂纖維與增強碳纖維編織結合在一起。當部件固化時,熱塑性樹脂成為材料的基體,碳纖維也嵌入其中。目前,公務機製造商達索公司已經在一款「獵鷹」公務機上採用了由這種工藝生產的零部件。根據Saint-Gobain公司的規劃,未來這種工藝還將推廣到雷達天線罩、螺旋槳槳轂和排氣整流罩等部件的製造中。
圖|空客官網、視覺中國
編輯|李琰
校對|李欣陽
出品|中國商飛新聞中心

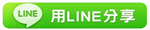
TAG:大飛機 |