追求品質與效率,看電腦中的「航空母艦」如何建成
如果將電腦中的配件看成各類武器,毫無疑問處理器、顯卡就是當今的殲20、殲31,集各類高技術於一身。而主板雖然在晶元技術含量上沒有處理器、顯卡那麼高,但卻是電腦中重要性非常高的一個—畢竟顯卡壞了直接換、內存壞了直接換,電腦甚至還可以通過集顯或單根內存繼續工作。而如果主板出現故障,那麼你必須拆下所有的配件,將主板發至維修點,電腦也必須停用。因此主板就像電腦中的「航空母艦」,承載著各個配件,為它們提供電力、數據傳輸通道,正常發揮出它們的設計功能。那麼這艘「航空母艦」是怎樣生產出來的?生產過程中又需要通過哪些步驟才能儘可能避免這艘「航空母艦」出現故障呢?
雖然電腦主板與航空母艦這樣的超級大型工程級產品完全不在一個層次,但從功能、作用,乃至外形上都有類似之處—都是一個方方正正的平台,承載著各類功能模塊,並必須確保它們發揮出正常作用,否則便是一損俱損的嚴重後果。因此這也就意味著,主板在電腦中具備很高的重要性,就像航空母艦一樣,它的生產、製造也是一個非常複雜、嚴謹的過程。接下來就讓我們像軍迷圍觀國產001A航母的建造過程一樣,走進技嘉南平工廠,來看看電腦中的這艘「航空母艦」是如何建造的。
產量可達40萬片
「航母」建設基地揭秘
雖然一塊主板的尺寸並不大,即便是E-ATX板型的主板也只有305mm×330mm大小。但要生產它們卻需要投入各類大型的設備與人力。設立於台北的技嘉南平工廠佔地4.5萬平方米,擁有多達1200名僱員,其中70%的員工的工作時間長達15年,可以說是一支經驗豐富、技術成熟的團隊。這為生產的高效進行、生產可靠的產品打下了基礎。生產力方面,現在技嘉南平工廠主要生產板卡產品、筆記本電腦、伺服器以及嵌入式產品。其中主板是最主要的產品,工廠專註生產技嘉AORUS系列、伺服器級主板,月產量可以達到40萬片,其次是顯卡產品,月產量為10萬片,伺服器主板的產量也有5萬片,加上台式機、筆記本、嵌入式產品,該工廠的總產量可以超過每月60.5萬片。
在技嘉南平工廠大堂,有一個用主板零件組成的工廠模型,簡明扼要地展現了技嘉主板工廠的結構。
10條流水線+多重檢測
開啟SMT貼片生產
嚴格意義上來說,主板的生產應該從PCB的生產、開料,主板晶元組的製造算起。不過一般在主板工廠的生產中,基本所有製造所需原材料都已準備完畢,主板剩下的生產主要有SMT貼片、DIP插件、TEST測試以及Packing包裝四步,技嘉南平工廠也主要是為了完成這四步建立的,每一個流程都需要眾多的設備、成員合力完成,任何一個環節都不容疏忽,包括進入生產線之前的個人除塵工作都必須強制性完成。
不管是員工還是訪客,任何人在進入生產線前,必須通過高壓除塵倉,並穿好鞋套。
當一切準備就緒後,主板的生產首先就從SMT(Surface mount technology,表面封裝技術的縮寫)貼片工作開始。這一步工作的主要目的是將貼片式的電阻、電容、電感、晶元組、音頻與網路晶元、M.2與CPU插槽等主板主要元器件通過機器高效地安裝在主板上。技嘉南坪工廠擁有多達10條SMT貼片生產線,其中6條由富士CP-742、QP-342貼片機組成,而另外4條採用了產能更高、更先進的富士NXT Ⅱ貼片機。
技嘉南平工廠生產線已經開始大量使用產能更大、更先進的富士NXT Ⅱ貼片機。
SMT貼片生產線中的上料系統,可以看到就像子彈帶樣,多顆主板晶元組這樣的「大號」元件整齊排列等待安裝,它們也將通過貼片機自動安裝在主板PCB上。
主板生產主要分為SMT貼片、DIP插件、TEST測試以及Packing包裝四大步。
SMT貼片工作的第一步是通過錫膏印刷機將錫膏印刷在PCB上,在這裡技嘉同樣採用了來自富士的GPX-HD高精度錫膏印刷機GPX-HD來完成這一任務。接下來就是機器置件工作—即SMT貼片機通過上料系統將前面提到的電阻、電容、晶元組、處理器插槽等元件貼到主板PCB上;再下一步技嘉主板則會進入來自美國的Heller 1913回焊爐,「享受」高達260℃的高溫使附著在PCB板上的錫膏融化變成液化狀態,充分結合貼片元器件的焊接腳,在進入較冷溫區後,焊錫膏就會變成固體狀態,令元件引腳和PCB牢牢焊接起來,實現安裝元器件與PCB穩定結合的目的。
SMT貼片生產線已經可以完成包括CPU插槽、M.2插槽在內的各類貼片式電阻、電容,主板晶元組的安裝。
來自美國的Heller 1913回焊爐可以通過高溫全自動地焊接各類貼片元器件。
當然僅僅安裝上元器件是遠遠不夠的,工作人員還必須確保各元件的安裝狀態是否正常。在這裡,技嘉南平工廠特別使用了型號為JUTZE LI-5000的AOI(Automatic Optical Inspection,自動光學檢驗)設備。AOI是集光學、計算機圖形識別、自動控制多學科於一身的高技術產品,它的內部存有多類缺陷圖樣特徵。工作時,AOI擁有高倍放大功能,並會用激光定位器精確定位CCD鏡頭,根據生產人員所設定的特定路徑,對主板上所安裝的各個零件、PCB板面進行檢查,掃描整塊PCB板,並將得到的圖樣與缺陷圖樣比對,以此對比元件的安裝、PCB線路的製作是否有問題,像常見的線路缺口、短斷路、蝕刻不全等缺陷都可以憑藉AOI找出來,如果有問題就會返工重做,或者廢棄。
JUTZE LI-5000 AOI檢測系統可以高效地找出貼片過程中的生產缺陷。
此時雖然主板還沒完成所有零件的安裝,但貼片工作已經安裝了包括主板晶元組、網卡、音頻晶元等主要晶元。因此生產人員還將對每一片主板進行斷短路測試(Open-Short Test),以確認測試時所有晶元的信號引腳都與測試系統相應的通道在電性能上完成了連接,並且沒有信號引腳與其他信號引腳、電源或地發生短路。至此SMT貼片生產線的工作才算全部完成,而值得一提的是從生產開始,每塊技嘉主板還會擁有一個特定的條碼,可以記載該主板使用了哪些零件,什麼時候生產的,可以追蹤生產時的所有信息,更方便後續的維修。
追求自動化、規範化
DIP插件生產線揭秘
主板的第二道生產工作就是進行DIP插件,將諸如內存插槽、PCIe插槽、固態電容之類的大型元器件安裝在主板上。一般談到這道工序,可能不少讀者首先想到的是一大群工作人員用手為主板插上各種零件。不過如今像技嘉南平工廠這樣的大型主板生產基地也通過引進Juki JM-10自動插件機器減少了人工工作量,使得工作完成得更加高效、精準。JM-10自動插件機器將主要為主板插上各類固態電容,同時該機器還有自動極性檢測功能,可以有效避免出現電容插反這類的常見錯誤。
現在DIP生產線早已不是人工生產的代名詞,電容安裝這類繁瑣的工作已經交由JM-10自動插件機來完成。
當然除了電容,還有很多零件需要安裝,而剩下的工作目前仍由人工來完成。在這一生產過程中,需要特別注意ESD(靜電放電)的防護,設備全部接地。因此工廠內的生產人員全部穿的是防靜電衣服和鞋子,然後還要佩帶導靜電的手環線。產品都是防靜電的包裝,以確保產品不會受到生產過程中的靜電損害。此外為了減少人力消耗,技嘉南平工廠還在DIP生產線部署了一個非常有趣的自動送料車,它會沿著固定的路徑,將料件送到工作人員的位置,同時響著音樂提醒大家注意避讓。
操作人員必須注意靜電防護,佩戴防靜電手環,穿上防靜電衣物和鞋子。
生產過程中,就像所有高效的人工流水線樣,一個人不會負責完成主板上所有的插件工作,而是有所分工—比如一號工作人員只負責音頻電容的安裝,二號負責安裝BIOS晶元,三號負責安裝黑色內存插槽,四號負責安裝橙色內存插槽,直到主板插件工作全部安裝完成。
為了提高人工產線的效率,技嘉南平工廠還研發了自動送料車。
最後在波焊爐中,通過銀白色的液態錫將插接件牢牢固定。
同樣在DIP插件工作安裝完成後,生產人員仍必須檢查各元件的安裝是否正確無誤。這裡技嘉使用了他們與ITRI工業技術研究院聯合研發的AOI(Automatic Optical Inspection,自動光學檢驗)設備。該系統主要會檢查主板上的元件有沒有漏插、多插,以及用件型號不符等各類錯誤。同時即便產品通過AOI測試後,還會再進行一次人工檢測,確認所有零件安裝到位,並手動檢測各零件的安裝是否穩固。而如果產品沒有問題則會進入到DIP插件工作的關鍵一步—波焊爐。首先波焊爐會為插接件噴上助焊劑,並在前段對PCB加熱。而在波焊爐的後半段則是一個高溫的液態錫爐,它均勻平穩地流動。主板PCB傳過來後,就會利用高溫的液態錫和助焊劑的作用將插接件牢牢焊接在PCB上。
DIP插件工作仍然需通過AOI光學檢驗設備檢查元件安裝中是否存在問題。
在完成波焊後,技嘉南平工廠會再次安排人工檢查,檢查剛才的自動焊接是否存在問題,如是否有包焊現象,如存在的話,還需要人工使用烙鐵進行修復、處理。在通過這一階段後,最後主板將進入後組裝階段,裝配那些無需焊接的零件,如用螺絲固定的主板散熱片。至此一塊主板的生產基本就已完成。
保障品質
不可缺少的功能測試與烤機測試
技嘉南平工廠對主板的品質有非常高的要求,每塊主板在出廠之前,都必須完成100%的功能測試,而不是普通的抽檢測試。技嘉使用了一台名為「Function BOX」的自研測試平台—每塊主板將通過11次的插拔測試,5分鐘左右的測試時間,確保主板的每一個插槽、功能都能正常運行。最後主板還將進入BURN IN TEST即烤機環節—在恆溫箱設定的特定環境溫度下,通過運行各類烤機軟體使整機滿負載運行,以檢驗主板在高負載情況下是否能長時間穩定工作。
技嘉自行研發的「Function BOX」功能測試平台,檢查主板的插槽、每一項功能能否正常工作,主板在出廠前都必須通過此項測試。
追求效率
充滿技術含量的包裝環節
只有主板能通過以上所有測試,才可以確認這款主板的品質達到要求,接下來就需要執行主板生產的最後一步:包裝與發貨。這個環節看似技術含量不會太高,在早期這一階段也是純粹由人工來完成。不過為了提升工作效率,技嘉南平工廠現在在包裝階段也引入了自動化生產設備—首先是自動折盒系統。剛剛生產出來的主板包裝盒就像一片片的紙張一樣,並未成型。員工只要把盒子放入機器內,機器就會自動進行摺疊,將主板包裝盒摺疊成型,基本上5秒以內就可以折好一個盒子。
接下來還需要再次進入人工流水線,多名操作員分別為主板綁定身份證即貼上條形碼,放入如光碟、說明書、SATA線等附件。當單個主板的包裝完成後,操作員還會將數片主板放入一個大的運輸箱內,並進入最後一個環節—自動封箱即封裝運輸箱,也就是說連運輸箱的封箱工作都不需要人工操作了。這個自動封箱機的功能相當強大,首先為運輸箱的頂部、底部各貼上一條封口膠,再為包裝箱打上縱向打包帶,接著通過自動變向系統使運輸箱橫置,再為運輸箱打上兩條橫向打包帶。至此,一塊主板的生產過程才算全部完成,可以等待車輛運輸至機場、港口發往全球各地的經銷商。
追求自動化是技嘉南平工廠的一個特點,不論是主板包裝盒的製作,還是運輸箱的封箱,全部由機器自動完成。
自動化、多重測試、規範化
讓主板品質更加可靠
從技嘉南平工廠主板的生產流程可以看到,當前主板的生產已經加入了多個自動化生產設備與流程—SMT貼片生產幾乎全由機器完成;傳統的DIP插件工作也由自動插件機進行繁瑣的電容安裝,焊接階段更是由全自動的波焊爐來完成;甚至在包裝、封箱階段,大部分工作也全交給了機器。這在很大程度上可以提高工作效率,同時更因為機器、電腦天生的程序化、模式化,以及「不知疲勞」的優勢,使得工作的準確度要遠遠優於人工操作。
當然不管是人工操作,還是自動化生產,錯誤率、故障率仍然存在於全球任何一個產品的生產線上。因此加強產品測試成為技嘉南平工廠提高品質的又一法寶—SMT貼片生產中的AOI檢測、斷短路測試,DIP插件產線中的電容極性檢測、AOI測試、焊接人工檢測,專業的Function BOX功能測試、烤機測試,一塊主板在出廠前就必須要經歷至少七大類檢測,這也使得主板的品質能得以充分保證。
同時規範化的生產流程也加強了對生產人員的管理,提高了效率,不管是進廠前必須的除塵工作,還是防靜電的手環與著裝,以及非常貼心的自動送料車、各部門的品管比武大賽等細節都凸顯出技嘉工廠在提升人員生產規範化、高效化的努力。而努力的成果就是技嘉主板長期以來在市場上都擁有很大的銷售份額,成為當今位列一線的重量級主板廠商。同時「電腦用的久,就選技嘉超耐久」的評價也在用戶中口口相傳。所以加強自動化生產、執行多重測試、生產規範化,就是造好主板這艘「航空母艦」的秘訣。

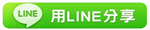
※小米拿下諾基亞專利授權;華米科技發布米動手錶青春版!
※高性價比炫彩側透機箱,大水牛潘多拉·晶Plus
※1080p高畫質網遊隨便玩!三款GT 1030顯卡鑒賞體驗
※【簡訊】AMD Vega專業卡曝光;最新三星Note 8渲染圖曝光
※【評測】雙攝手機360N5s的進化之路,堪稱完美的偏執狂!
TAG:微型計算機 |
※按照目前的進度,我國什麼時候能夠建成核動力航空母艦?
※點燃空中的綠色革命,電動飛機是航空業的未來嗎?
※船塢中的「遼寧」航空母艦拆除重要裝備 或升級性能更強
※航空母艦究竟能否成為海上作戰艦艇科技樹的盡頭?其實不一定
※如果殲6改裝成無人機,能打沉美國航空母艦嗎?
※波音帝國是如何建成的 中國航空業能複製嗎?
※直升機航空電子技術的現在與未來
※航空母艦與鋼鐵俠助陣,這麼硬核的智能鎖你見過么
※國產航母還沒下水,又要建造電磁彈射航空母艦?確定不是在搞笑?
※航空母艦的「超級奶爸」,沒有了它,航空母艦談不上任何戰鬥力
※航空母艦是如何在戰場中生存下來,如何對空、對海警戒與防範的
※中美貿易爭端如升級航空製造業或成重要砝碼
※航空母艦能潛到水下航行嗎,從技術上能實現嗎?
※航空工業長風:讓大師工作室真正成為提質增效的主力軍
※法國賣的最火的導彈,差點擊沉航空母艦,如今成為中國現役裝備
※航空工業成飛集成劉鏡茗:與你相遇 好幸運
※航空母艦為什麼叫「海上充電寶」?原來歷史上真的有航母發電
※中國的航空母艦事業如火如荼 關鍵技術已攻破 建造速度全面升級
※二戰後美兩重型航母遭到航空火箭彈重創,該彈成最強反航母武器
※我國已經擁有製造航空母艦的能力,能否採用核動力?技術還未成熟