金屬增材製造技術在航空領域的發展與應用
航空工業在上個世紀80年代就開始使用增材製造技術,之前增材製造在航空製造業只扮演了做快速原型的小角色。最近的發展趨勢是,這一技術將在整個航空航天產業鏈佔據戰略性的地位。 包括波音、空客、Lockheed Martin, 霍尼韋爾以及普惠都做出了表率行動。
新一代飛行器不斷向高性能、高可靠性、長壽命、低成本方向發展,越來越多地採用整體結構,零件趨向複雜化、大型化,從而推動了增材製造技術的發展與應用。增材製造技術從零件的三維CAD 模型出發,無需模具,直接製造零件,可以大大降低成本,縮短研製周期,是滿足現代飛行器快速低成本研製的重要手段,同時也是滿足航空航天超規格、複雜金屬結構製造的關鍵技術之一。
電子束熔絲沉積成形
電子束熔絲沉積技術又稱為電子束自由成形製造技術(Electron Beam Freeform Fabrication,EBF3)。在真空環境中,高能量密度的電子束轟擊金屬表面形成熔池,金屬絲材通過送絲裝置送入熔池並熔化,同時熔池按照預先規劃的路徑運動,金屬材料逐層凝固堆積,形成緻密的冶金結合,直至製造出金屬零件或毛坯。
電子束熔絲沉積快速成形技術具有一些獨特的優點,主要表現在以下幾個方面:
(1)沉積效率高。電子束可以很容易實現數10kW 大功率輸出,可以在較高功率下達到很高的沉積速率(15kg/h),對於大型金屬結構的成形,電子束熔絲沉積成形速度優勢十分明顯。
(2)真空環境有利於零件的保護。電子束熔絲沉積成形在10-3Pa真空壞境中進行,能有效避免空氣中有害雜質(氧、氮、氫等)在高溫狀態下混入金屬零件,非常適合鈦、鋁等活性金屬的加工。
(3)內部質量好。電子束是「體」熱源,熔池相對較深,能夠消除層間未熔合現象;同時,利用電子束掃描對熔池進行旋轉攪拌,可以明顯減少氣孔等缺陷。電子束熔絲沉積成形的鈦合金零件,其超聲波探傷內部質量可以達到AA 級。
(4)可實現多功能加工。電子束輸出功率可在較寬的範圍內調整,並可通過電磁場實現對束流運動方式及聚焦的靈活控制,可實現高頻率複雜掃描運動。利用面掃描技術,能夠實現大面積預熱及緩冷,利用多束流分束加工技術,可以實現多束流同時工作,在同一台設備上,既可以實現熔絲沉積成形,也可以實現深熔焊接。利用電子束的多功能加工技術,可以根據零件的結構形式以及使役性能要求,採取多種加工技術組合,實現多種工藝協同優化設計製造,以實現成本效益的最優化。
美國麻省理工學院的V.R.Dave等人最早提出該技術並試製了Inconel 718 合金渦輪盤。2002年,美國航空航天局(NASA)蘭利研究中心的K.M. Taminger 等人提出了EBF3 技術,重點開展了微重力條件下的成形技術研究。同一時期,在海軍、空軍、國防部等機構支持下,美國Sciaky 公司聯合Lockheed Martin、Boeing 公司等也在同時期合作開展了研究,主要致力於大型航空金屬零件的製造。成形鈦合金時,最大成形速度可達18kg/h,力學性能滿足AMS4999 標準要求。Lockheed Martin 公司選定了F-35 飛機的襟副翼梁準備用電子束熔絲沉積成形代替鍛造,預期零件成本降低30%~60%。據報道,裝有電子束熔絲沉積成形鈦合金零件的F-35 飛機已於2013 年初試飛。2007 年美國CTC公司領導了一個綜合小組,針對海軍無人戰鬥機計劃,制定了「無人戰機金屬製造技術提升計劃」(N-UCASMetallic Manufacturing Technology Transition Program),選定電子束熔絲沉積成形技術作為未來大型結構低成本高效製造的方案。目標是將無人機金屬結構的重量和成本降低35%。
圖片:Sciaky製造的零件
中航工業北京航空製造工程研究所於2006年開始電子束熔絲沉積成形技術研究工作,開發了電子束熔絲沉積成形設備。開發的最大的電子束成形設備真空室46m3,有效加工範圍1.5m×0.8m×3m,5 軸聯動,雙通道送絲。在此基礎上,研究了TC4、TA15、TC11、TC18、TC21 等鈦合金以及A100超高強度鋼的力學性能,研製了大量鈦合金零件和試驗件。2012 年,採用電子束熔絲成形製造的鈦合金零件在國內飛機結構上率先實現了裝機應用。
圖片:中航工業北京航空製造工程研究的電子束熔絲沉積成形設備
激光直接沉積增材成形
激光直接沉積技術是在快速原型技術和激光熔覆技術的基礎上發展起來的一種先進位造技術。該技術是基於離散/ 堆積原理,通過對零件的三維CAD 模型進行分層處理,獲得各層截面的二維輪廓信息並生成加工路徑,在惰性氣體保護環境中,以高能量密度的激光作為熱源,按照預定的加工路徑,將同步送進的粉末或絲材逐層熔化堆積,從而實現金屬零件的直接製造與修復。
由激光在沉積區域產生熔池並高速移動,材料以粉末或絲狀直接送入高溫熔區,熔化後逐層沉積,稱之為激光直接沉積增材成形技術。該技術只能成形出毛坯,然後依靠數控加工達到其凈尺寸,由於適合加工大型零件,送粉式的LENS技術在航空航天零件修復領域有著不可替代的作用。
激光直接沉積技術的特點如下:(1)無需模具;(2)適於難加工金屬材料製備;(3)精度較高,可實現複雜零件近凈成形;(4)內部組織細小均勻,力學性能優異;(5)可製備梯度材料;(6)可實現損傷零件的快速修復;(7)加工柔性高,能夠實現多品種、變批量零件製造的快速轉換。
在我國,西安鉑力特的LSF設備就是這類技術的代表。除此之外,典型企業還有美國的OPTOMEC公司,法國BeAM公司,德國通快以及專為CNC機床公司提供增材製造包的HYBRID公司。
激光直接沉積技術是20世紀90 年代首先從美國發展起來的。1995 年,美國Sandia 國家實驗室開發出了直接由激光束逐層熔化金屬粉末來製造緻密金屬零件的快速近凈成形技術。此後,Sandia 國家實驗室利用LENS 技術針對鎳基高溫合金、鈦合金、奧氏體不鏽鋼、工具鋼、鎢等多種金屬材料開展了大量的成形工藝研究。1997 年,Optomec Design 公司獲得了LENS 技術的商用化許可,推出了激光直接沉積成套裝備。1995 年,美國國防部高級研究計劃署和海軍研究所聯合出資,由約翰霍普金斯大學、賓州州立大學和MTS 公司共同開發一項名為「鈦合金的柔性製造技術」的項目,目標是利用大功率CO2 激光器實現大尺寸鈦合金零件的製造。基於這一項目的研究成果,1997 年MTS 公司出資與約翰霍普金斯大學、賓州州立大學合作成立了AeroMet 公司。為了提高沉積效率並生產大型鈦合金零件,AeroMet 公司採用14~18kW 大功率CO2 激光器和3.0m×3.0m×1.2m大型加工艙室,Ti-6Al-4V合金的沉積速率達1~2kg/h。AeroMet 公司獲得了美國軍方及三大美國軍機製造商波音、洛克希德·馬丁、格魯曼公司的資助,開展了飛機機身鈦合金結構件的激光直接沉積技術研究,先後完成了激光直接沉積鈦合金結構件的性能考核和技術標準制定,並於2002 年在世界上率先實現激光直接沉積Ti-6Al-4V 鈦合金次承力構件在F/A-18 等飛機上的裝機應用。
自「十五」開始,在國家自然科學基金委員會、國家863 計劃、國家973 計劃、總裝預研計劃等國家主要科技研究計劃資助下,北京航空航天大學、西北工業大學、中航工業北京航空製造工程研究所等國內多個研究機構開展了激光直接沉積工藝研究、力學性能控制、成套裝備研發及工程應用關鍵技術攻關,並取得了較大進展。
C919大客翼身組合體大部段中的關鍵零部件鈦合金上、下翼緣條是由西安鉑力特激光成形技術有限公司使用金屬增材製造技術(3D列印)所製造,上、下翼緣條中最大尺寸3070mm,最大重量196kg的左上緣條,僅用25天即完成交付,大大縮短了航空關鍵零部件的研發周期,實現了航空核心製造技術上一次新的突破。
電子束選區熔化成形
電子束選區熔化技術是指電子束在偏轉線圈驅動下按預先規劃的路徑掃描,熔化預先鋪放的金屬粉末;完成一個層面的掃描後,工作艙下降一層高度,鋪粉器重新鋪放一層粉末,如此反覆進行,層層堆積,直到製造出需要的金屬零件,整個加工過程均處於10-2Pa 以上的真空環境中,能有效避免空氣中有害雜質的影響。
電子束選區熔化技術特點如下:
(1)真空工作環境,能避免空氣中雜質混入材料。
(2)電子束掃描控制依靠電磁場,無機械運動,可靠性高,控制靈活,反應速度快。
(3)成形速度快,是激光選區熔化的數倍。
(4)可利用電子束掃描、束流參數實時調節控制零件表面溫度,減少缺陷與變形。
(5)良好的控溫性能使其能夠加工TiAl 等金屬間化合物材料。
(6)尺寸精度可達±0.1mm,表面粗糙度約在R a15~50 之間,基本近凈成形。
(7)真空環境下成形,無需消耗保護氣體,僅消耗電能及不多的陰極材料,且未熔化的金屬粉末可循環使用,因此可降低生產成本。
(8)可加工鈦合金、銅合金、鈷基合金、鎳基合金、鋼等材料。
電子束選區熔化技術源於20世紀90 年代初期的瑞典,瑞典Chalmers 工業大學與Arcam 公司合作開發了電子束選區熔化快速成形(Electron BeamMelting,EBM)技術,並以CAD-to-Metal 申請了專利。2003 年,Arcam 公司獨立開發了EBM設備。目前以製造EBM 設備為主,產品已成系列,兼顧成形技術開發。美國、日本、英國、德國、義大利等許多研究機構、工廠、大學從該公司購置了EBM 設備,在航空、航天、醫療、汽車、藝術造型等不同領域開展研究,其中,生物醫學植入物方面的研究較為成熟。近年來,在航空航天領域的應用也迅速興起,美國波音公司、Synergeering group 公司、CalRAM 公司、義大利Avio 公司等針對火箭發動機噴管、承力支座、起落架零件、發動機葉片等開展了大量研究,有的已批量應用,材料主要銅合金、Ti6Al4V、TiAl 合金等。由於材料對電子束能量的吸收率高且穩定,因此,電子束選區熔化技術可以加工一些特殊合金材料。
電子束選區熔化技術可用於航空發動機或導彈用小型發動機多聯葉片、整體葉盤、機匣、增壓渦輪、散熱器、飛行器筋板結構、支座、吊耳、框梁、起落架結構的製造,其共同特點是結構複雜,用傳統方法加工困難,甚至無法加工。其局限在於只能加工小型零件。目前世界上最大的電子束選區熔化設備是Arcam 公司的A2XX 型設備有效加工範圍為φ 350mm×380mm。
清華大學在國內較早開展了相關研究,並開發了裝備。近年來,西北有色金屬研究總院、中科院金屬研究所、北京航空航天大學、北京艾康儀誠等單位利用Arcam 公司生產的設備開展了研究,涉及多孔材料、醫學應用等領域。自2007 年以來,在航空支撐及國防預研基金等項目支持下,中航工業北京航空製造工程研究所針對航空應用開展了鈦合金、TiAl 合金的研究。開發了電子束精確掃描技術、精密鋪粉技術、數據處理軟體等裝備核心技術。針對飛行器結構輕量化需求,重點研究了鈦合金的力學性能及空間點陣結構的承載性能和變形失效行為,目前正進行飛機複雜鈦合金接頭及TiAl 葉片的電子束選區熔化製造技術研究。
激光選區熔化增材成形技術
激光選區熔化成形技術原理與電子束選區熔化技術類似,通過把零件3D 模型沿一定方向離散成一系列有序的微米量級薄層,以激光為熱源,逐層熔化金屬粉末,直接製造零件。利用該技術可以製造出傳統方法無法加工的任意形狀的複雜結構,如輕質點陣夾芯結構、空間曲面多孔結構、複雜型腔流道結構等。在航空、航天領域,可用於製造火箭發動機燃料噴嘴、航空發動機超冷葉片、小型發動機整體葉輪、輕質接頭等,同時還可用於船舶、兵器、核能、電子器件、醫學植入等各個領域,具有廣泛的應用前景。相較於電子束選區熔化技術,激光選區熔化由於所使用的粉末尺寸小,因此具有很高的尺寸精度和表面質量。
激光選區熔化增材成形技術由激光選區燒結技術發展而來。20 世紀80 年代以來,經歷了低熔點非金屬粉末燒結、低熔點包覆高熔點金屬粉末燒結、高熔點金屬粉末直接熔化成形等階段。激光選區燒結成形主要用於蠟模、砂模等製造,為精密鑄造提供模型。這種原型表面粗糙,疏鬆多孔,還需要經過高溫重熔或滲金屬填補孔隙等以後才能使用。隨著激光技術的發展以及高亮度光纖激光器出現,國內外金屬激光選區熔化增材成形技術發展突飛猛進。近幾年來,英國、德國、法國、美國、瑞典等國外發達國家先後開GH4169、AlSi10Mg、CoCr、TC4 等合金金屬複雜結構的激光選區熔化增成形設備,並開展應用基礎研究。國外著名R-R、GE、P&W、MTU、Boeing、EADS、Airbus 等航空航天武器裝備已利用此技術開發商業化的金屬零部件。
需要關注的方面
增材製造技術以其與傳統去除成形和受迫成形完全不同的理念迅速發展成了製造技術領域新的戰略方向。金屬零件的高能束流增材製造在航空航天領域的研究和應用也越來越廣泛,在先進位造技術發展的同時,也促進了結構設計思想的解放和提升,兩者的相互促進必將對未來飛行器製造技術領域造成深刻影響。隨著我國綜合國力的發展,包括航空在內的國防武器裝備的開發逐漸加速,增材製造技術迎來了高速發展的階段,未來的應用前景十分廣闊。但目前實際應用還比較少,尚處於技術成長期,為了推進技術的應用和發展,需要關注以下幾個方面。
(1)內部質量和力學性能的均勻性、穩定性和可靠性。由於高能束流增材製造過程集材料製備和零件成形於一體,零件的尺寸、形狀、擺放位置、熱參數、加工路徑等對內部缺陷和組織的形成具有重要影響,每個零件的形成過程都具有一定的特殊性,因此,需要經過多批次、大量的試驗考核,確定並固化從材料、成形到後處理的各個技術環節,以實現零件性能的穩定性。
(2)與用戶的充分溝通,形成獨立的標準。增材製造技術實現過程不同於傳統的製造技術,其製備的零件性能也與傳統的鍛件、鑄件有明顯差異,不能完全用傳統技術的評價方法對增材製造技術進行評定。通過溝通讓用戶充分了解增材製造技術的優缺點,獲得用戶對產品性能的具體要求並有針對性的進行滿足,形成針對增材製造的零件質量評價標準,對於促進增材製造技術的應用十分重要。
(3)成本、效益的兼顧。並非所有的零件都適於採用增材製造方法,在進行應用技術開發時,需要選擇合適的應用對象。綜合考慮成本、效益與周期等因素,在航空領域,適宜採用高能束流增材製造技術加工的零件種類主要有複雜形狀結構、超規格結構、需要快速研製的結構以及可明顯降低成本的結構等。
國內外關於上述金屬增材製造技術具有典型性的設備供應商,請登陸3D科學谷網站,搜索3D科學谷發布的:
一張圖看懂世界範圍內金屬3D列印-2017版本
一張圖看懂世界範圍內金屬3D列印-2016版本
作為本文補充,根據3D科學谷的市場研究,近幾年國內在以金屬絲為原材料的加工工藝上出現了更多的設備製造廠商,包括武漢天昱、西安智熔。另外,西安智熔除了EBAM設備,還開發了EBM電子束選區融化設備。
面向未來
由於增材製造所具有的極大靈活性,未來的飛機設計可以實現極大的優化,更加仿生力學的結構。市場研究機構SmarTECH曾經從4個角度來探索3D列印技術如何推動航空航天製造技術的發展。包括縮短交貨期、減輕零件重量、降低生產和運營成本、有利於環境保護。
- 增材製造在新的零件和備品備件製造方面對於縮短交貨期有著顯著的優點。航空專家認為比傳統方式縮短80%的製造時間,同時還可以顯著提高零部件的性能。
-將來增材製造方式可以顯著改變目前航空零部件的庫存狀態。把設計圖紙輸入到印表機就可以快速製造出零部件將大大降低航空零部件的庫存。
-商用飛機的使用壽命在30年,而維護和保養飛機的原製造設備是非常昂貴的。根據空客,通過增材製造技術,測試和替換零部件可以在2周內完成,這些零件可以被快速運到需要維修的飛機所在地,省時省力的幫助飛機重新起飛。
-另外,不再需要保有大量的零部件以防飛機有維修需求,這些大量的零部件的生產也是十分昂貴和浪費資源的。當然,對於舊的機型,尤其是數據丟失的型號,保有原來的零部件還是需要的。
其他挑戰
另外,除了技術層面,增材製造在未來十年航空航天的需求與挑戰還很多,包括:
-當前的飛機製造商並不了解增材製造設備,也很難提出對設備如何升級的要求,下一步飛機製造商需要更多的參與到增材製造設備的開發中來。
-增材製造設備廠商必須提高做工程的能力和提升材料專業度。當前增材製造設備廠商缺乏開發高端航空航天零部件的能力,缺乏開發質量跟蹤和控制設備的能力。增材製造設備廠商不能局限於做設備製造,而應該發展圍繞著增材製造、增材製造材料一系列的系統服務商的能力。
-增材製造設備廠商需要開源設備材料,雖然接受其他的材料會帶來競爭,但靈活性提高了才能使得航空航天製造商開發更多的應用。開源設備材料也會使得設備本身更容易受市場歡迎。
-軟體之間需要更好的銜接。目前脫節的地方很多,使得做出一個完整的零件過程變得磕磕絆絆,這不利於行業的績效。
-需要集成控制系統到增材製造設備里。目前市場上很少有系統的工具來監測和跟蹤增材製造的過程,這導致需要大量的測試件,而且需要昂貴的後處理。
(主體內容來自作者鞏水利,中航工業北京航空製造工程研究所)
歡迎轉載,如需加入白名單請將微信公眾號回復至3D科學谷微信公眾號

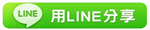
※看美國增材製造標準化路線圖所揭示的設計方面的26個當前短板
※盤點3DP技術在建築方面各種腦洞大開的應用
※迪肯大學推進氮化硼納米管材料量產和3D列印應用,航空與國防領域將受益
※飛機高性能結構件,3D列印碳纖維複合材料的下一個目標
※國內對高鐵制動閘片的3D列印研究
TAG:3D科學谷 |
※混合現實技術在醫學領域的應用
※區塊鏈技術在物流領域風控的應用
※激光技術在汽車製造領域的幾大應用
※區塊鏈技術在通信領域的應用
※切削模擬技術在生物醫學領域的應用
※VR虛擬現實技術對建築領域的應用
※閃展VR全景虛擬現實在工業製造領域的應用
※激光焊接技術在車燈領域的應用
※區塊鏈技術——金融領域的去中心化應用
※我國將加快區塊鏈技術在商務領域的應用
※發展太空領域科技對人類生活與軍事的影響
※3D列印技術在製鞋領域的應用
※漢莎航空技術公司建立增材製造中心,將推進航空航天領域3D列印應用
※國產商用密碼在工控領域的應用建設
※人工智慧輔助診斷技術在醫療領域的作用與挑戰
※智能交通領域 AI技術應用領域更加廣泛
※微軟在人工智慧領域的投資和發展邏輯
※中歐在納米功能複合材料方面進行合作,將應用於航空製造領域
※石墨烯關鍵製備技術及在軍民領域的應用
※4G產業市場規模成熟發展 技術行業應用領域廣闊